The developer of Catia, a design tool in aerospace and automotive, has long held aspirations for the AEC sector. The move to offsite digital construction presents its best market opportunity, with Lendlease, Vinci and Bouygues now customers
If you have ridden in a car or flown in a plane, the chances are it was designed in Catia, the flagship CAD system of French software firm Dassault Systèmes (DS). Many of the consumer goods you also buy are designed in another market dominating CAD brand of DS, Solidworks.
DS is an undisputed giant in engineering and manufacturing, but when it comes to buildings and infrastructure, its tools have really only been used in niche projects, probably most famously championed by Zaha Hadid Architects (ZHA). In these processes, Catia was selected because of its ability to model at 1:1 scale, connect geometry to downstream fabrication, and provide a common tool that allows architect and manufacturer to talk the same language.
DS has long been watching the emergence of BIM. It was actually one of the investors in Revit before it was sold to Autodesk. At the time, 2002, it was one of the reasons Autodesk paid so much for Revit ($133 million), which had no user-base, as it didn’t want DS to own a potential threat in the AEC space – having already lost out to acquiring Solidworks, which DS bought in 1997 and then went on to dominate the mid-range mechanical CAD (MCAD) market.
In the mid 2000s, DS CEO Bernard Charlès certainly had aspirations to compete in the volume modelling market within AEC but little transpired from this initiative. In the last five years, DS’s interest and activity in the space has slowly and steadily increased, although it has failed to gain any significant penetration into the volume market with the portfolio of Catia-based tools it has developed.
It’s pretty clear to anyone in architecture that the development of BIM has stagnated and the original aims of moving to a model-centric process are still stuck in the ancient constraint of drawings-based contracts and deliverables.
The vast majority of architects are still modelling with the sole purpose of creating drawings. The future of the industry is to model to fabricate and save an incredible amount of wasted time and effort in generating resource hogging 2D drawings.
BIM is also responsible for negatively impacting design time, as buildings do not require the level of detail or certainty that the ‘Lego-based’ systems of BIM impose. Here Rhino is king and it’s all about the geometry.
The bad news for architects is that the malaise of development in their toolsets comes with the fact that these products, such as Revit, are mature and from a sales perspective are highly penetrated and quite saturated. The software industry is now looking for new gold seams to mine, where they can add value and generate additional revenue.
Construction is where the action is at, whether that be connecting up supply chains, managing data or having models which are more aligned to fabrication than showing design intent. It’s here that DS appears to be focusing, because it has a manufacturing-ready ecosystem of products that could be shaped to better fit the needs of large construction firms.
Aeroplanes, ships and cars are just large assemblies of geometry and manufacturing information. A building, a bridge or a road is not that different, and the increasing use of digital fabrication in AEC means products like Catia and SolidWorks are being used with the industry.
Vinci and Lendlease have been working with DS for a few years to create expert systems to create highly detailed, construction-ready models and codify their internal processes. The latest firm to join the group is Bouygues Construction which has just signed a new three-year deal to accelerate the research and development of new cloudbased, mobile enabled approaches to building construction ‘virtual twins’.
It’s worth mentioning at this point that Digital Twins, which is currently all the rage in our industry, is woefully behind the use of Digital Twins in manufacturing. In short, DS is developing a tailored construction system for Bouygues to increase its productivity, ensure compliance of designs and produce predictable output. By using DS’ cloud-based design products, the aim is to connect developers, architects, subcontractors, suppliers and operating companies within the same ecosystem, which DS terms its ‘3D Experience Platform’. While construction is a horribly federated process, Bouygues aims to use a single environment to streamline the flow of data within projects.
This is the typical DS ‘playbook’ in aerospace and automotive, to get all the players to work in the same system. This is far easier to pull off in something like aerospace where the owner is Boeing and can drive this level of software consistency through its suppliers. In the AEC space, finding a significant owner that can drive that through disparate supply chains is frequently less straightforward.
As the industry moves to more design-build projects, the owners of projects become clearer and have much more say in the discrete processes of suppliers. While DS can be proud of getting Catia into ZHA and even Foster + Partners, the attraction is primarily on the geometry capabilities of the modelling kernel. By working with Lendlease, Vinci and Bouygues, the whole DS ecosystem of products – modelling, simulation, PLM (Product Lifecycle Management), collaboration, model management, production management, CNC etc. – can all be exploited.
Centred around the virtual twin (Digital Twin) Bouygues will use Catia from design to operation by ‘industrialising’ its project management, anticipating the various phases of a project and planning their on-site implementation in fine detail. Bouygues expects to see energy savings, reduction in errors, greater predictability, materials tracing and better waste management.
The knowledge that DS gains from its interaction with Bouygues and others feeds into the development of three configurations of its Catia-based 3DExperience platform, these will be “Integrated Built Environment,” “Inclusive Urban Future” and “Building Design for Fabrication.”
As DS continues with these high-level interactions with construction firms, it’s building up a knowledge-base and best practice approach which it can then productise. This will make subsequent engagements with construction firms successively easier and quicker. All this fits in with DS’ approach to other markets: sell to the top players and drive sales through the supply channel ecosystem. And, by avoiding the architecture part of the puzzle, it avoids the necessity to try and take on Revit, the 800lb gorilla in the volume architectural design market.
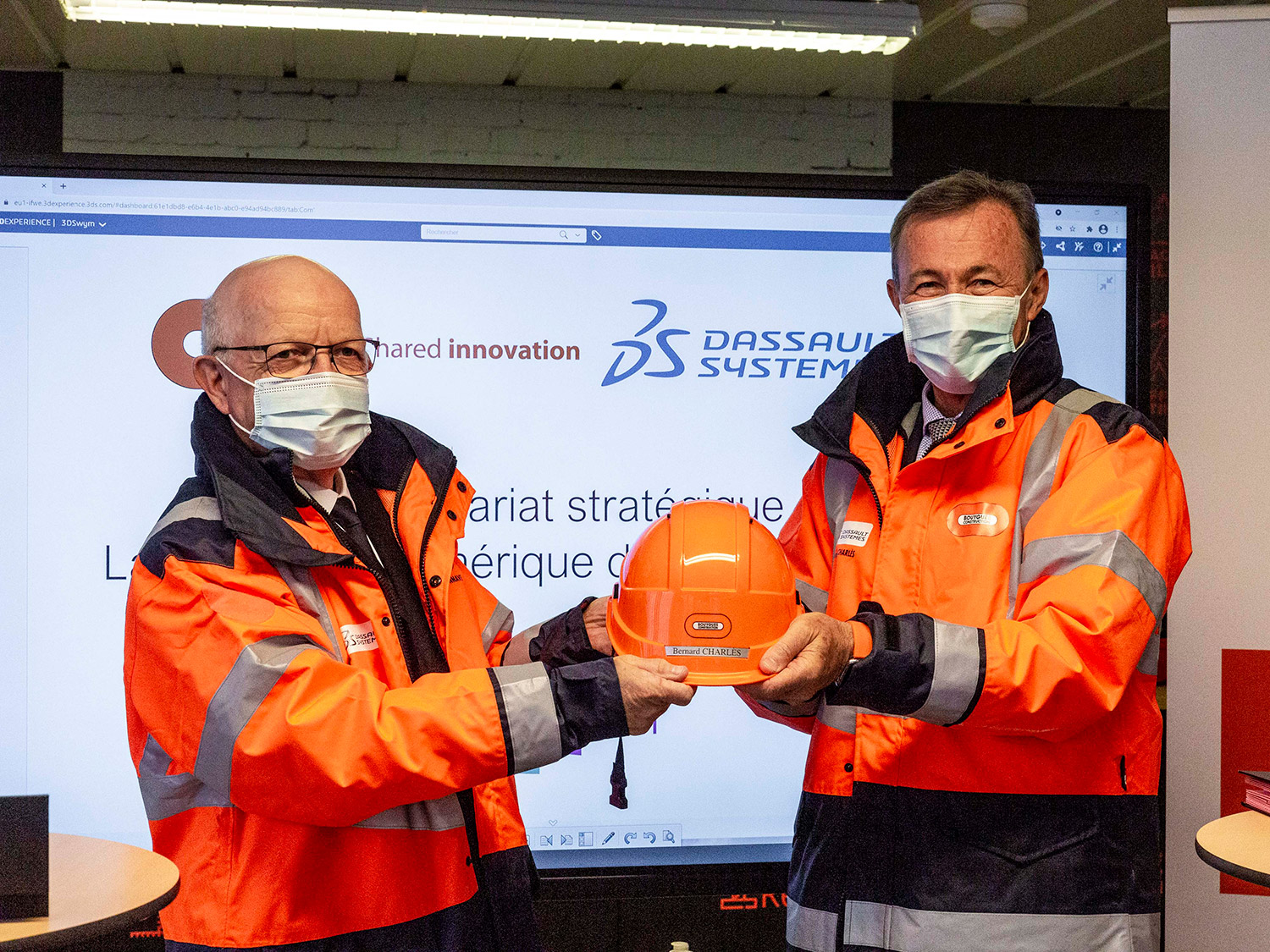
One cannot ignore that its main construction clients are also French. Vinci, Bouygues and DS are perhaps more inclined to work together due to proximity, language and culture. However, construction is global and these firms are global players which adapt to the language, culture and codes of where they’re needed. Should the deployment of the 3D Experience platform bear fruit, it may not be too long before established AEC software players find themselves competing against an extremely capable modelling solution, with a proven track record in industry digital transformation.
Beyond BIM
While DS may not be particularly vocal about what it is doing in the AEC space, UK VAR Desktop Engineering (DTE), has taken the initiative to promote and engage with the design and construction market, running an annual event showcasing, called ‘Beyond BIM’ , which highlights customers and signature architects who have gone beyond the capabilities of today’s BIM systems and are typically looking to go straight to digital fabrication.
Now in its third year, the range of speakers has broadened, demonstrating that the industry is looking at alternatives when seeking to innovate the current workflows. This year’s speakers included a keynote from Dale Sinclair, director of innovation, EMEA at AECOM.
Change is certainly coming and there’s much to learn from manufacturing for some areas of AEC
Dale’s talk succinctly highlighted future trends and problems the AEC industry needed to address. While we have been obsessed with BIM, the process of design to operation is not all about one aspect, one technology because, Dale blatantly said, the thing many in the industry have been thinking, but not saying out loud is – ‘the industry really needs to stop this notion of using drawings.’
Looking at the challenges, he identified Net Zero goals as being a key driver, with additive manufacturing, Digital Twins, the rise of volumetric fabrication and how all these things will mean the industry’s workflow has to change.
Dale sees the rise of robots in construction, and for that we need to reinvent brick and plasterboard to better suit robots, as most of the sizes and shapes are defined by human limitations, not what our robots could do.
The industry needs to start looking at ‘whole life outcomes, IoT, Big Data, Artificial Intelligence, Digital Twin and better asset management to drive down energy costs’. Dale identified it’s possible to save up to 24% of the cost of building in operating throughout the whole lifecycle – which he described as ’like getting the building phase for free’.
AECOM is internally researching design automation, exploring intuition and iteration using AI and machine learning. It is working smarter with data and working with connected data but he could not go into great detail. He concluded, “We have to control the whole process, almost become like a car manufacturer, with end-to-end processes, design, manufacture, even the sales process.”
Other speakers this year included:
- James Brown, Digital Manufacturing Engineer at Prodtex
- Ben Haldin, MD of Fulcro
- Hector Camps, Phi Cubed
- Mattia Santi, Co-founder and director of Sasi Studio
- Abdulmajid Karanouh, International director of Interdisciplinary Design & Innovation, Drees and Sommer
- Chun Qing Li, MD, founder and principal of Kreod.
Registration is required to watch the talks but it’s all free and well worth it. Click here to register.
These industry talks were supplemented by presentations from Dassault Systèmes executives – Jonathan Asher, Catia construction portfolio director, Patrick Mays, vice president strategy and Marty Rozmanith, construction cities & territories industry sales director.
In the confines of this article I will concentrate on what Rozmanith had to say as it ties in to what Dale Sinclair talked about at length and to the previously mentioned agreement between Bouygues Construction and DS.
Rozmanith was an early employee at Revit, prior to the Autodesk acquisition and has spent a number of years at DS driving development and engagement with the industry. His presentation was on the ‘Productisation of Buildings’, applying a systematic industrial process to standardise large chunks of buildings in advance of them arriving on site, more commonly called Design for Manufacturing and Assembly (DfMA).
Rozmanith first identified the core pain points in construction – the unpredictability, timeline problems, diversity, lack of skilled labour, geography and the huge variation in construction partners and contracts. These were compared to typical manufacturing processes, such as engineer to order and configure to order, to show where improvements in efficiency and margin can be identified. The ironic thing is this is already happening in components of buildings that are engineered, such a Schindler lifts, which has a rulesbased design system, using modules and variants, saving time because bespoke lifts can be configured and automated.
Bouygues Construction is one of the key clients that Rozmanith highlighted as looking at this approach to deploy in its productisation to get the benefits of configure to order. Taking the General Arrangement as the geometric inputs, using in-house predefined assemblies and subassemblies as custom IP, to automatically generate the LOD 400 models and documents, what Rozmanith terms ‘150%’ Bill of Materials = highly detailed output for fabrication and assembly. The more projects Bouygues does in this way, the more information it can put into its productised assemblies, enabling the automation of highly detailed configurations.
Bouygues wants to move from being a company that is drowning in documents to having a data-led process, driven by these ‘engineering master’ configurators, so it drastically reduces its design and documentation phase and has fewer components shipped to site, requiring less on-site assembly. The main downside of this is larger and heavier assemblies will arrive on site, requiring more cranes and more work preparing the site for lifting and placement.
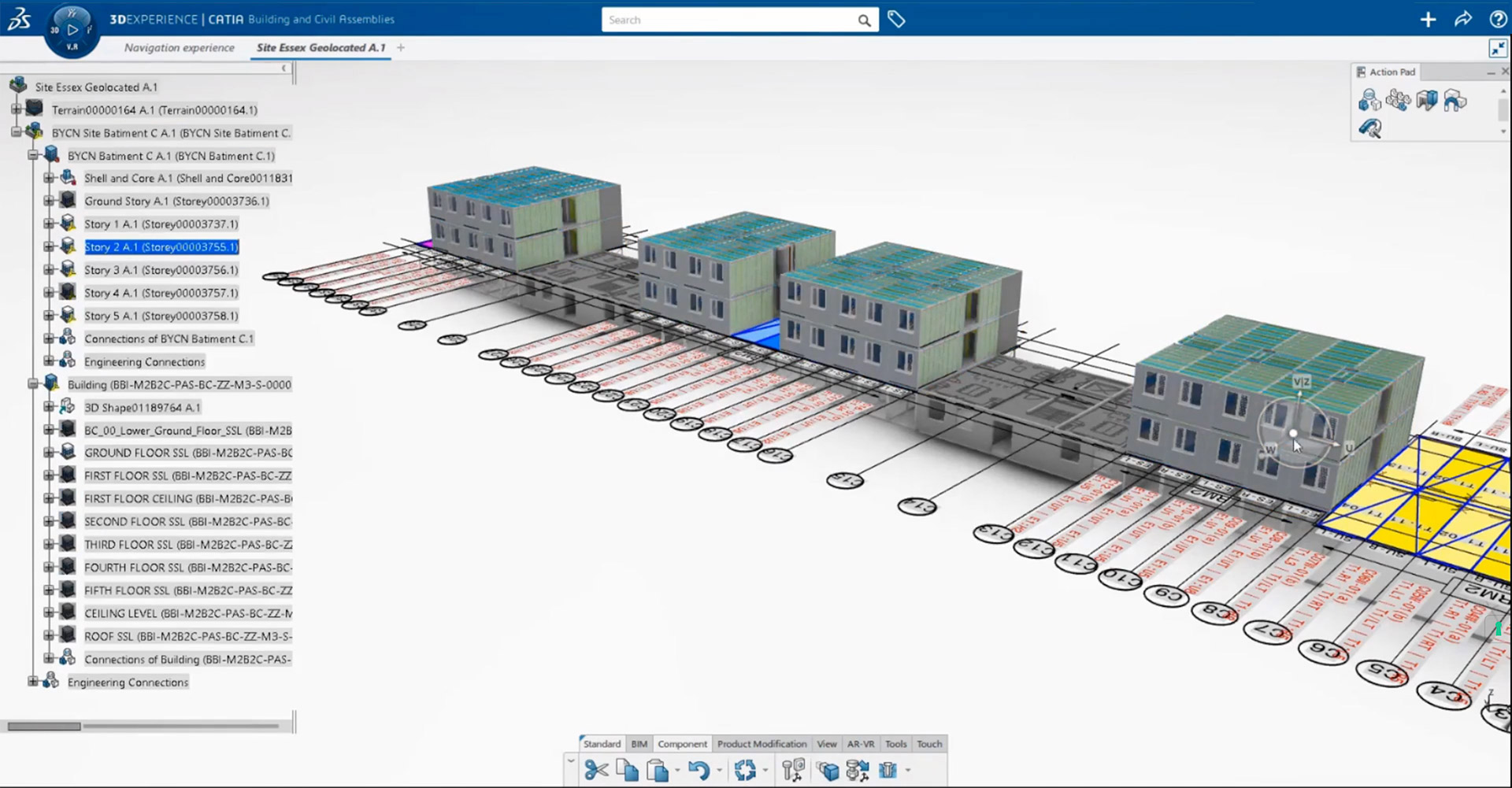
An example given was how Bouygues use DS tools to conceptualise hospital rooms, although this could be done and brought in from Revit. The results of that conceptual general arrangement are fed into DS’ generative platform leveraging Catia, which then generates the 100% configured 3D model automatically.
Where components interface with structure, these are all generated automatically as they are predefined / automated. These modules can be stacked and Catia has modelled, defined and created drawings for 80% of the finished design. These are structural steel, panels, fire, hot and cold MEP, ductwork, electrical routing.
DS is fortunate that the AEC market is falling ‘‘ into its way of thinking – the workflows it has perfected in the engineering space are becoming increasingly relevant
This model is the ‘virtual twin’, which drives the field execution, producing the instructions for how they are assembled in the field, using DS’ 3D Lean platform. The example also included panelised systems, which lend themselves to digital fabrication, where all the individual panel drawings were automated, untouched by hand. Rozmanith defined this as ‘Generative Configure to Order’ and the productisation of buildings. Obviously in a presentation it all looks like a miracle but the hard work has been put in in defining the productised elements and building the configurator. It’s interesting that the system allows adaptability to custom designs and also operates in the constraint of what can be manufactured. Bouygues’ aspirations are pretty impressive and it will get a tailor-made system at the end of this.
Conclusion
DS is undoubtedly gaining some traction in the AEC space and, in doing that, is getting knowledge to provide more turn-key Catia packages for its next customers in construction. But this isn’t really a case of DS chasing new customers. There is a general recognition that today’s tools and construction and architectural design are the evolutionary products of workflows which need to change because they are not connected. And the change that is coming is to become more like product design workflows in aerospace and automotive.
DS is fortunate in that the AEC market is falling into its way of thinking; the workflows it has perfected in the engineering space are becoming increasingly relevant.
In Rozmanith’s presentation, he simply took Schindler’s Lifts engineering / configure to order process and mapped that to Bouygues. It was a clear example of how productisation is going to become a key concept for many firms in the AEC space.
However, this is not a homogeneous market and different building types have different workflows. Building a server centre is not the same as building a hotel or one-off villa. DS is a long way from impacting the current status quo but it has been quietly establishing a beachhead. Also, the AEC industry has some very big silos that will take a long time to knock down.
We will have to wait and see where Bouygues and DS push their co-development and also what direction the general construction industry takes, given its move to off-site fabrication. Change is certainly coming and there’s much to learn from manufacturing for some areas of AEC.