Croatia’s Mate Rimac is often described as ‘Europe’s Elon Musk’. In just ten years, he has quickly risen to the forefront of electric hypercar design and battery production, even acquiring Bugatti. 3LHD architects was engaged to design Rimac Automobili’s futuristic new production and R&D facility not far from Zagreb
American and European auto motive firms have been caught out by the rapid rise in start- ups producing commercial – electric vehicles. While Elon Musk has led the charge (no pun intended) in making Tesla one of the most desired vehicle brands worldwide, you might not be so aware of a Croatia-based firm called Rimac Automobili, which has trailblazed the development of electric hypercars. Capable of a staggering 258 mph they are the fastest in the world.
Rimac Automobili is owned by 34-yearold entrepreneur Mate Rimac, who has a passion for electronics and inventing. In 2007, while trying to get into car racing, the engine of his 1984 BMW Series 3 blew up. Despite not having any automotive engineering experience, he converted the car to electric and then proceeded to break several world records for electric car performance.
By 2011 Rimac had created his first supercar from the ground up, called the Concept One. Those of you who are keen watchers of Amazon’s The Grand Tour may remember Richard Hammond’s test drive of the Rimac Concept One, which ended with him rolling and destroying the oneof-a-kind prototype, valued at £1 million.
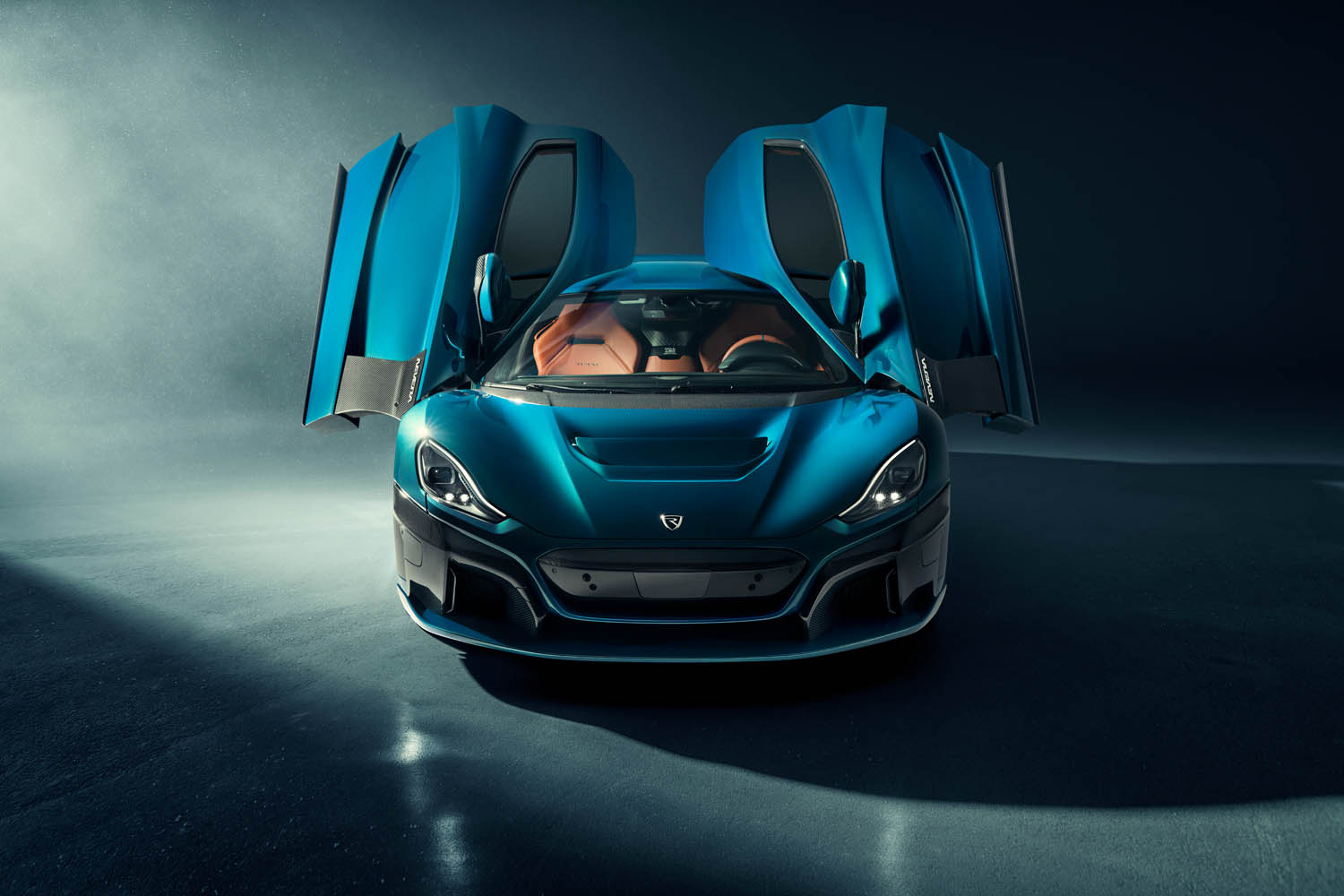
While making amazingly fast electric vehicles, the company that Rimac built became widely respected for its battery R&D and powertrain designs, attracting major investment from Porsche, Hyundai and Camel Group. Rimac currently provides electric drive and battery technology to Renault, Jaguar, Aston Martin, SEAT, Koenigsegg and Pininfarina.
In 2021, Rimac took the majority share in a partnership; Bugatti Rimac (Bugatti, of course, previously owned by Volkswagen and makers of the incredible Bugatti Veyron.)
The rise of the Rimac brand has been meteoric, despite coming from a country that has no real history of car production. (Although it has to be said that Nikola Tesla grew up in a village (Smiljan), that lies in modern day Croatia).
With rapid expansion and a filling order book, space had become a constraint, both for production and R&D. Rimac Automobili needed a big new home.
Rimac campus
The story goes that Mate Rimac was out on his bicycle in the countryside, about 20 minutes’ drive from the centre of Zagreb, when he came across an abandoned castle. He thought that one day it would make a great HQ for his company.
Roll forward a few years and Rimac acquired the land around the castle. While refurbishing the castle itself was not practical, in 2019 he planned to build a headquarters for his company there. The idea was that the facility would combine car production, high-capacity battery production (hundreds of thousands of units per year), power train production for other automotive firms, R&D, a museum and, of course, a professional-level racetrack for test-driving sports cars.
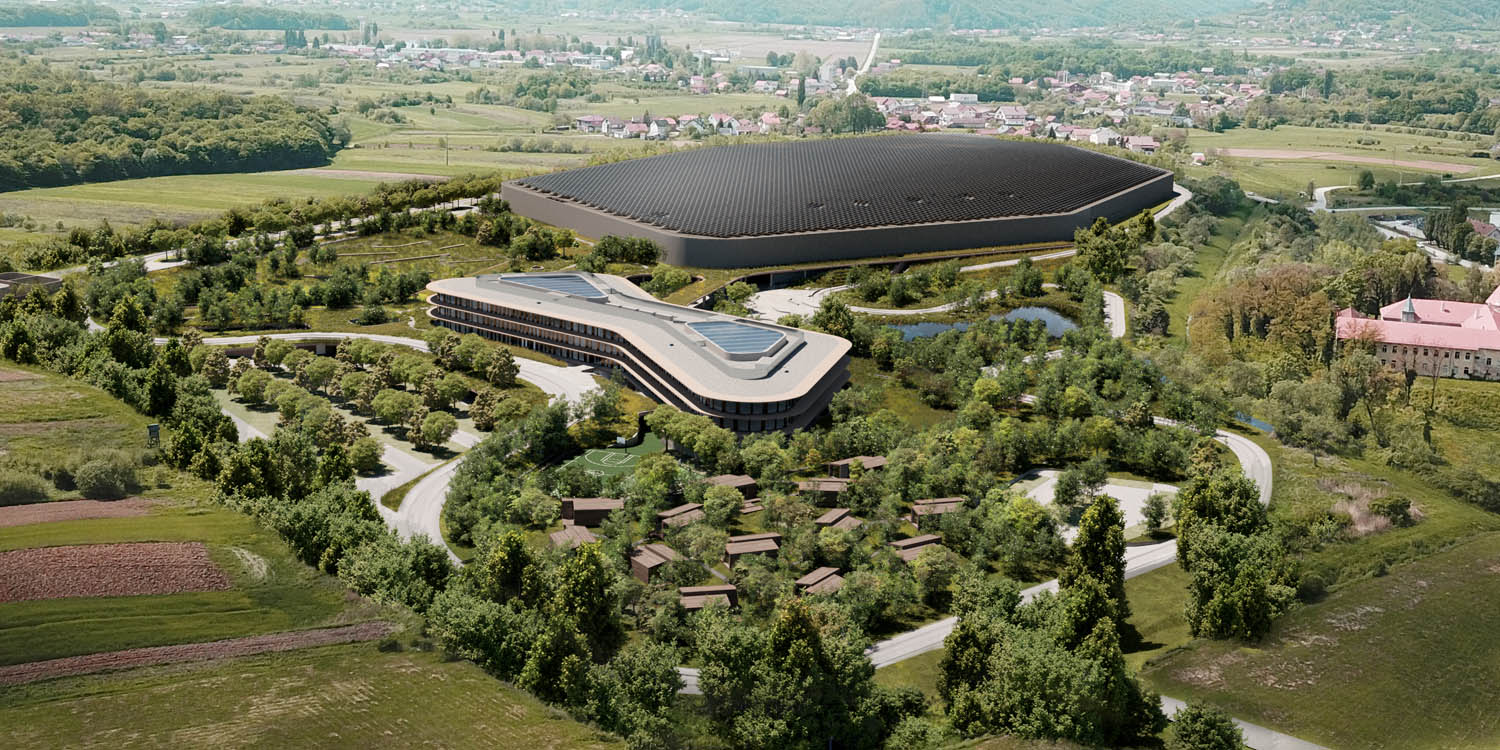
Rimac started an international competition for architects to design the whole campus, to accommodate a potential 1,000 employees. With a detailed brief, firms were given one month to submit their ideas. Local architecture firm, 3LHD Studio won the competition and came up with a futuristic campus, which covers over 95,000 square metres, of which 35% will be covered in vegetation.
As the scheme developed, the company grew, despite COVID, and is now being built to accommodate up to 2,500 employees, over double the company’s current headcount.
Marko Dabrović, one of the founders of 3LHD explained the rationale of the winning design, “To better understand the company we are working for, we always find out what their key values are. For Rimac, these were: speed, balance, growth, family and openness. With that in mind, we analysed the site and the topography.
“The castle was, of course, the most prominent building, set on the high ground – the roof of which gave us the maximum height.
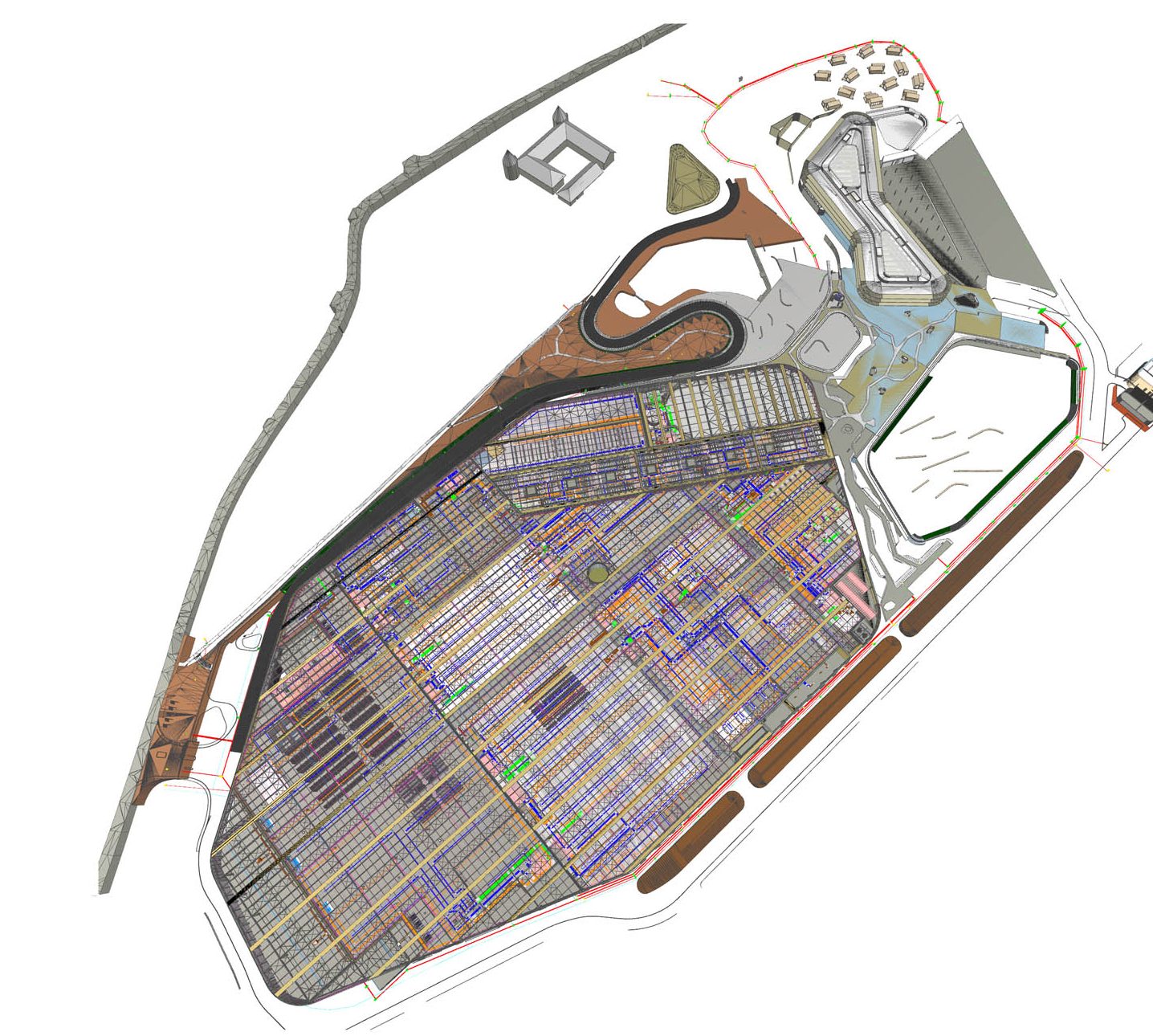
“We took the largest flat surface for the production facility, and we wanted to somehow create the relationship between the production facility, the R&D facility, and the castle – the three largest volumes on the site.
“In between, we placed a lake, which reflects all three buildings and keeps them in balance and connects them all with a ‘topographically ‘invisible’ building, the campus restaurant.
“The production facility is the largest building, being 400 metres long and 200 metres wide. Unlike most automotive firms, Rimac makes all the parts for the car on site. They don’t buy parts from the other companies, but they produce and assemble everything on site.”
For 3LHD, it was very important to make the campus as high quality as possible for working and for living. Dabrović explains that his team spent considerable time working out how to minimise noise, toxins, humidity and maximise efficiency, hiring a consultancy from Stuttgart to help design the climate needs, both indoors and outdoors.
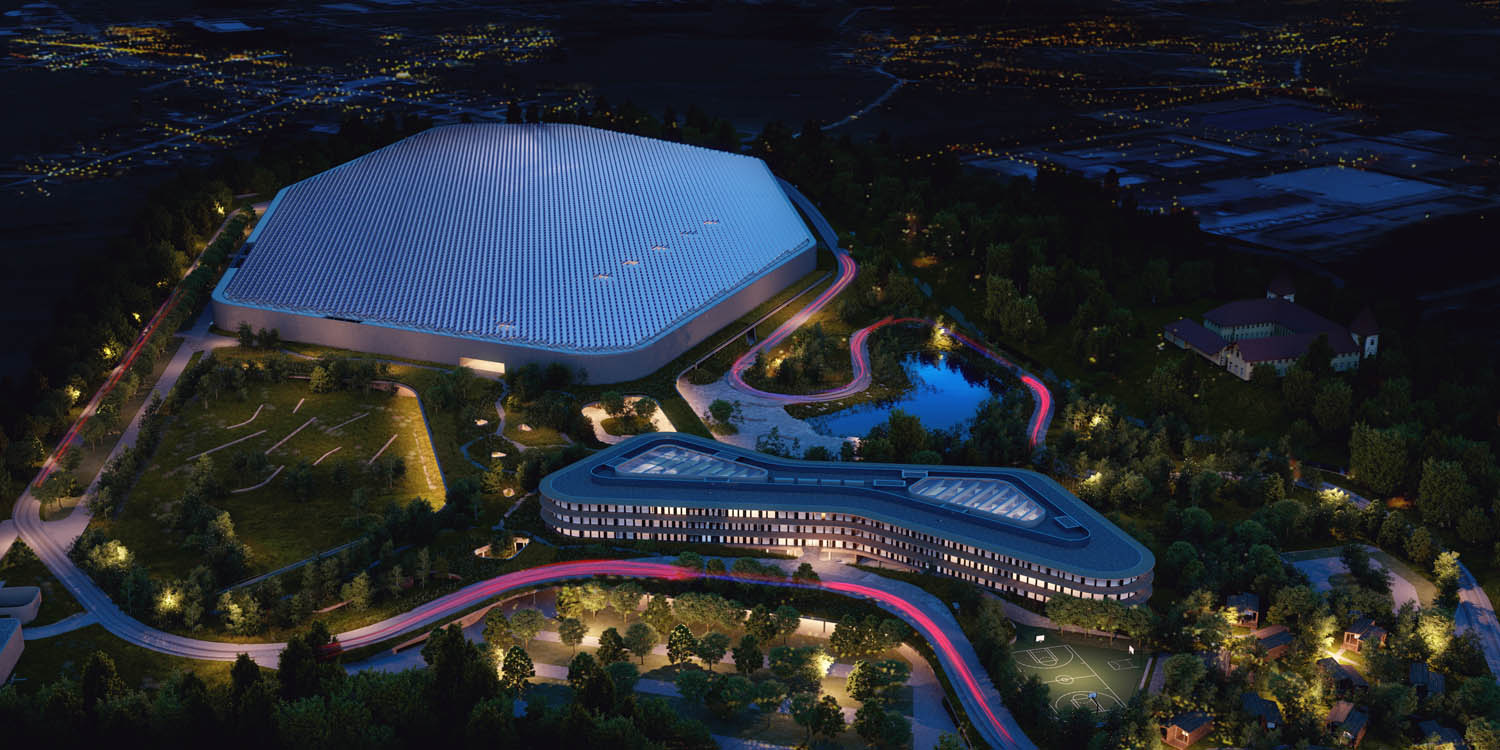
“In such a large production facility (having the area of almost seven football pitches), people need access to outside places to have comfort. So, we designed an atrium in the centre or building and smaller atriums near the offices,” says Dabrović.
The restaurant, which connects the production facility with the R&D facility, is central to the campus design, as Dabrović explains, “It represents the family and openness because in Croatia, everybody’s invited to the table! This green-roofed restaurant caters to all the employees from production offices, R&D and visitors. It’s where the whole campus can meet.
“The Rimac R&D and office building is an envelope built around two large unique atriums. One is planted with trees and the other one is a big assembly hall, for all-hands meetings. The atriums are directly linked to the restaurant. This building is really open with beautiful views to the forest, to the lake, to the castle and to the south.
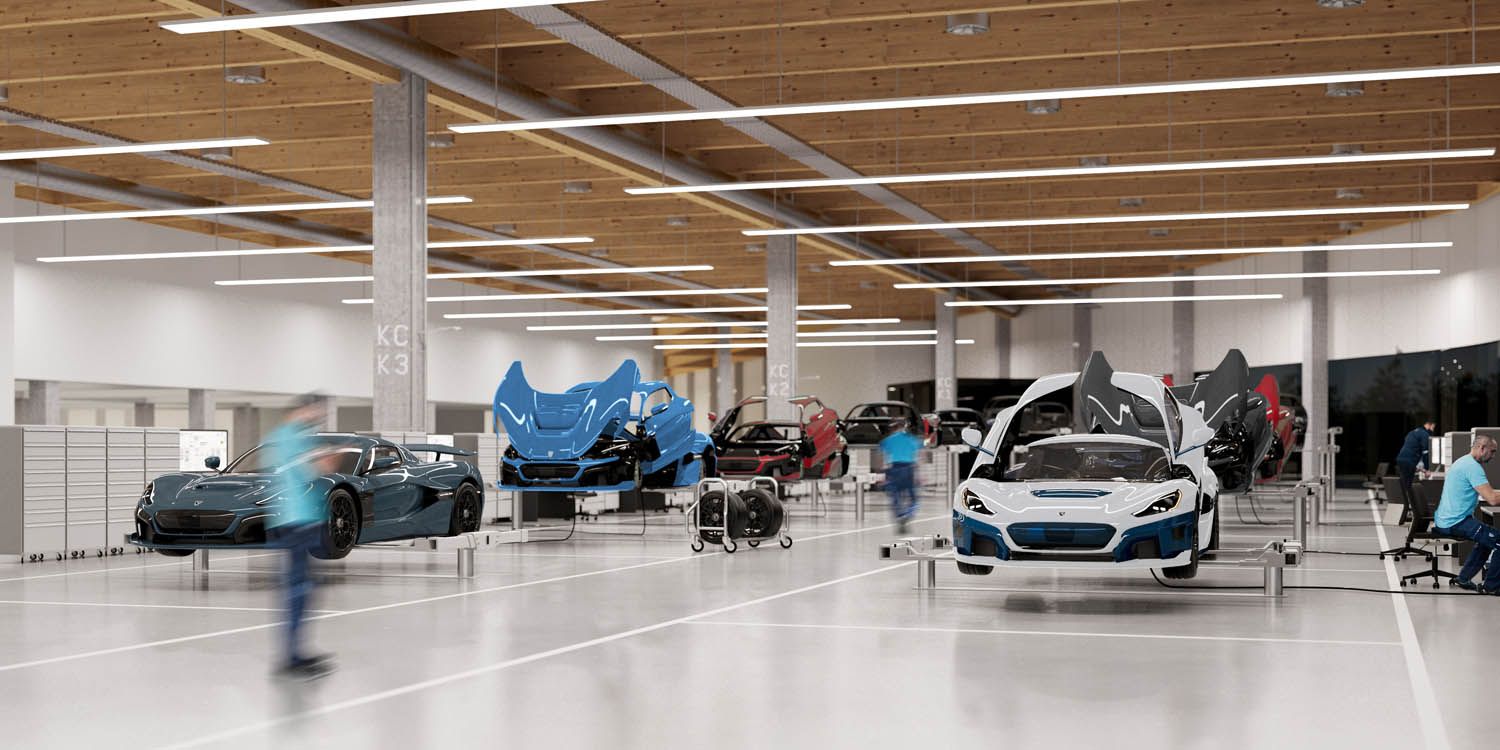
“The design of the park is inspired by the flow of the air over race cars. Seamless flow was important to the design, as to how people move around the campus, between buildings. Mate Rimac didn’t want to have any fences so the whole campus was to be accessible.”
No boundaries
One of the complications, or should we say idiosyncrasies, with the design brief relates to the restaurant. Mate Rimac is a vegan and wanted to have livestock on the campus, especially in front of the restaurant, to remind people of the animals they were eating, in case they wanted to change their minds!
However, combining the design objectives of sportscar racetrack and livestock with the other constraint of ‘no fences’, 3LHD had to research to find inventive solutions.
They ended up deploying a technique which originated in 18th Century France, an idea which was then taken up by the landed gentry in the UK at the time. The unusually named ‘Ha-Ha’ fences, are optical illusions, as they are sunken fences, which consist of a deep dry vertical ditch and wall on the inner side, with a steep grass slope opposite. From afar, they give an illusion of continuous rolling lawn, but livestock can’t cross the hidden ditch boundary.
This solution is used to keep the animals away from the extremely fast electric hypercars. 3LHD also had to investigate with veterinary experts, as to which animals could be put together and would not destroy the plants. This turned out to be Geese and Sheep. The lack of any barriers will make the Rimac campus probably the only advanced Automotive Research Facility which does not have a fence.
The road around the interior of the campus also doubles as a racetrack. Never having designed a racetrack, 3LHD hired traffic and race consultants, the net result is a track which has a series of corners inspired by parts of famous racetracks around the world. In the original brief, there had to be at least one corner where they could drift their cars.
Since Rimac employs a lot of young people, they wanted to have a kindergarten, so this was also added to the plan, and further relates to the firm’s key value of family. This means the kids grow up next to the parents, who just so happen to be creating one of the craziest supercars in the world!
The Rimac campus prides itself on having numerous amenities, and a few quirky elements. Apart from having a racetrack, a kindergarten, a restaurant, sheep, geese and no fences, it will also house a car museum. Visitors are also welcome to take a tour of the factory. This will not just feature Rimac cars, but there will be a tribute to car development. It will include Mate Rimac’s original green BMW conversion, together with all the new concepts, car parts developed for the other companies, as well as their new Bugatti cars.
Embracing sustainability on the Rimac campus
Long term sustainability is of paramount importance for the Rimac Campus. This is being addressed in many different aspects of the design, as Dabrović explains, “We are trying to make the buildings as compact as possible to minimise energy losses through the facade and to keep it cool by overshadowing windows.
“We are using energy from the solar panels on the roof, heat energy from the ground water as well as air source heat pumps. So, all this energy should be renewable. The function of the lake is to reflect, but also to collect the rainwater to cool and reduce the heat, attract wildlife to the site and to produce a calm working environment.”
Dabrović explains that long term sustainability is not only linked to the architecture and materials, but also to those that inhabit the campus. In addition to employees, this includes animals and visitors as well.
Part of the brief was to provide temporary accommodation to allow visitors, foreign employees, and customers to stay overnight. Instead of building a traditional hotel on campus, 3LHD took a more stripped back approach, as Dabrović explains. “We felt we already had this perfect balance between the three buildings. We went to the trouble of hiding the restaurant and all the amenities, so they should not stand out.
So instead of designing a hotel, we proposed to create a small village of wooden buildings which people could use, a bit like ’glamping’.
“Visitors and guests can acclimatise, find some friends, and get to know the place. We made a community house which had a fireplace where they could meet each other during the nights, when the factory is not working.”
Design technology
3LHD started off using AutoCAD running a traditional 2D architectural workflow. Early on it migrated to Archicad and totally bought into adopting a BIM process, which it uses from initial concept design through to completion.
Dabrović’s first company was an architectural visualisation company and so, as one might expect, the practice has a great reputation for strong in-house rendering quality. The firm is currently using Epic Games’ Twinmotion, which Graphisoft added support for recently.
While being heavy users of BIM, 3LHD has also, somewhat accidentally, gone into software development, having created its own collaboration and management tool, called volum3 (see below).
Dabrović explained that 3LHD started developing software in house in 2004, as the company needed a solution to track the working hours. Using Javascript, the team created a simple browser-based time logging system, which then led to developing an expenses system, handling all the supplies and payments to subcontractors. As the firm started to design ever bigger hotels, 3LHD realised that it was getting very complicated to produce the bill of quantities and the specification of materials in Excel, which is not a structured database.
In 2011, 3LHD created an in-house system to capture specifications, materials, furniture, lamps, walls, frames – anything that can be felt or touched. Dabrović explained that this is especially important in hotels, where you have to be very specific about what the designers want, the type of veneer and then how that veneer is laid down and how it is treated. By 2013 Dabrović realised that it was not sustainable to write software just for 3LHD. It was not only challenging to create, but also expensive to maintain. He decided to develop something that other firms can use too and applied for a European Union grant.
“By the time we started to work on projects in China, Canada and Switzerland, we added another layer of complexity to our coordination issues, working on multilingual projects meant two or three languages”, explained Dabrović. “We think and work in Croatian, but then have to translate everything into English, and then it has to be translated into German or Chinese. This meant we needed to create each data set with three languages – meeting minutes, task lists etc – so we designed a task management tool with connectors for meeting minutes, that can work in any language you want. We got a grant from the European Union for €300,000 and set up a software company.”
Conclusion
Designing the Rimac Campus would have been daunting for any architectural practice. Not only considering the scale, but also meeting the highly detailed brief, together with some unique quirks from the client.
Mate Rimac appears to have been a very hands-on client, involved in nearly every aspect of the process and the design rationale. 3LHD had also never designed a factory, racetrack or catered to sheep before. Similarly, Rimac had never defined a brief for a building before!
3LHD’s holistic approach to design and open communication with the client has successfully got the project to the construction phase. We look forward to visiting and driving the circuit when it’s complete.
Construction on the Rimac Campus started in 2021. Rimac plans to move the first parts of its production into the factory building by the end of 2022 and hopes the whole campus will be finished by the end of 2023. The cost of the first phase of the campus, without any production equipment or infrastructure, is about €110-120 million. Adding equipment for testing, machining, as well as IT, furniture etc. will cost more than another €100 million.
Pump up the Volum3 (volume)
Volum3 is a collaboration platform for architects, managers, engineers, project managers, construction firms, facilities management and owners. It provides a single environment to upload all the drawings and for easy dissemination.
Data is stored per project, stages are defined, as well as teams. Then drawings can be easily shared, together with related task management and meeting notes. It also allows specification of materials and product specifications.
Drawings are turned into PDF, are rasterised to save file size, and can be viewed and marked up. As the software is cloud-based, volum3 can be accessed from anywhere and used on mobile devices.
The system is tried and tested on a daily basis with 3LHD utilising it on its projects. What’s even more interesting is that volum3 is completely free. It’s funded by the manufacturers to have their data in the specification database, as well as by the owners when it comes to large projects.
3LHD Architects
3LHD Architects started in 1994 with four founding partners – Marko Dabrović (pictured), Saša Begović, Tanja Grozdanić Begović and Silvije Novak – who have since been joined by Paula Kukuljica. The company now employs 60 people from its offices, a converted cinema, in the capital city, Zagreb.
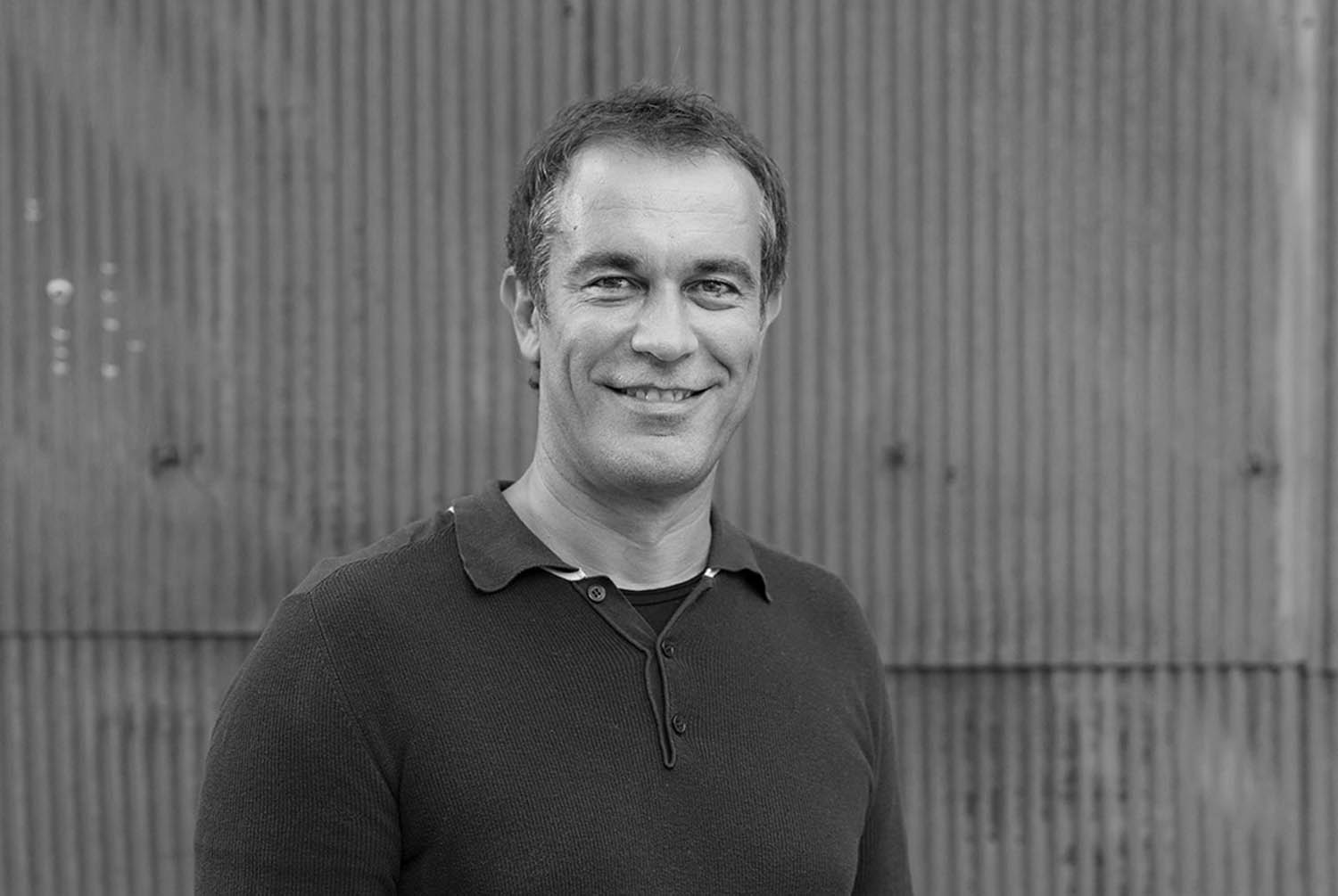
The firm has carried out work on many different private and public projects. These include bridges, the Croatian Pavilions for EXPO exhibitions in Japan and Spain, Hotel Belvedere in Dubrovnik, Croatia, Hotel LN Garden in Guangzhou, China, and Port Lands Sport Centre in Toronto, Canada.
The largest project 3LHD has completed so far is the redesign of a substantial part of the beautiful Venetian seaport of Rovinj. The project included the design of two large hotels: Hotel Lone and Hotel Grand Park, together with outer pools, public beach, waterfront and marina.
Rovinj is located on the western part of the Istrian peninsular. The old town, built on a hill, has been kept as a heritage site, with the old waterfront merging with a collection of modern hotels and marina.
Hotel Lone is an exceptional modern hotel, with swooping curves and balconies. 3LHD pooled together many young Croatian artistic talents, such as furniture designers, graphic designers and artists for the interiors.