Construction practice is changing. Old workflows, methodologies and practices are being challenged, as offsite, modular and design for manufacture concepts are under development. Could 3D printing technology be part of that change? Martyn Day investigates
As a species, we certainly have our flaws, but we are eminently resourceful at making things. We are natural engineers. When it comes to providing shelters, we have always used the resources around us to construct structures; wood, soil, clay, stone, straw. Our tools evolved, we made axes and chisels from metals, and we further refined and processed our raw building material, carved joints, planed surfaces, and baked bricks. We experimented with geometry, built towering pyramids with 2.5 tonne blocks, invented plumbing, heating, glass, built Great Walls visible from space. Humankind, ‘masters of construction’ since 9,000 BC. Not bad for a bunch of jumped up monkeys. We are always innovating.
In the 21st Century, it looks like we might well move ‘beyond the brick’. Concrete actually dates back to around 700BC when lime mortar was first used in Jordan and Syria. The Nabataeans even had concrete floors and waterproof concrete cisterns, which still survive. Obviously, the Romans turbo-charged the whole concrete thing and made domes, arches, aqueducts, amphitheatres etc. but they never figured out reinforcement.
We had to make it through the middle ages and into the Industrial Revolution for Portland cement. An unhappy French gardener, Joseph Monier, miffed at his easy to break concrete pots, embedded an iron mesh in his next generation flowerpots. He went on to patent the process and made, reinforced tanks, beams and bridges. Now we produce over 10 billion tonnes of concrete a year for the building industry, and the steel rebar market is worth $121.1 billion alone. Concrete is now the most commonly used man-made material on Earth.
As always, while our materials have evolved, so have our tools. Look out spades and shovels, the robotic revolution is upon us. And with precision motors, computer modelling / analysis and automation driving the next industrial revolution, construction is also at the forefront.
In manufacturing, 3D printers have survived the hype curve and are now moving from prototyping plastic parts to making real plastic and carbon within the traditional mix of processes. However, despite becoming faster, more reliable and production- capable, 3D print is a long way from replacing traditional methods of mass production such as plastic injection moulding. It’s still carving its own niche.
With 3D modelling now standard within construction, in the late 1990s there were a number of research projects examining how 3D printers could be used to speed up the process of fabricating buildings and components, both onsite and offsite. Behrohk Khoshnevis, director of the Center for Rapid Automated Fabrication Technologies (CRAFT) at the University of Southern California (USC) looked at the then formative 3D print process and realised that while manufacturing parts in 3D layers was a novel approach, making buildings in layers was actually a continuation of the traditional construction process. He went on to develop a layered, 3D print fabrication technology he named Contour Crafting
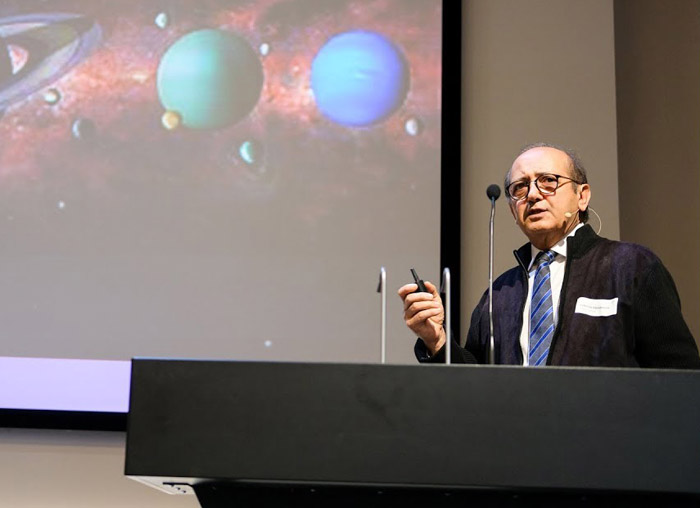
Today there are over 20 firms selling 3D print manufacturing services, cement 3D printers or 3D printed buildings, from fixed gantry-based systems to portable robot arms. That said, it’s still very early experimental days, with the most common use of 3D printing being the production of wax moulds for items like panels, an example being Laing O’Rourke’s FreeFab wax 3D print methodology which was used recently in some stations for London’s Crossrail.
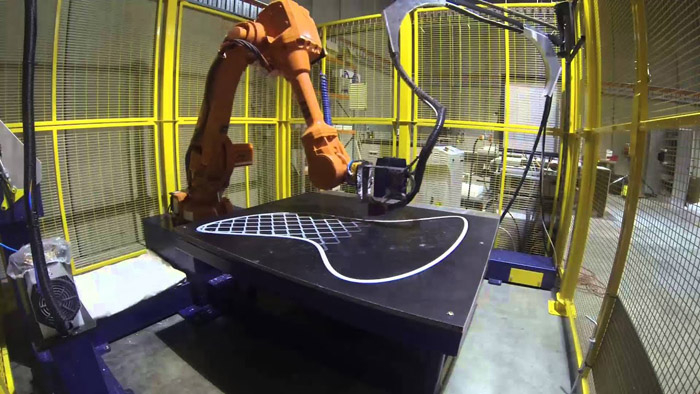
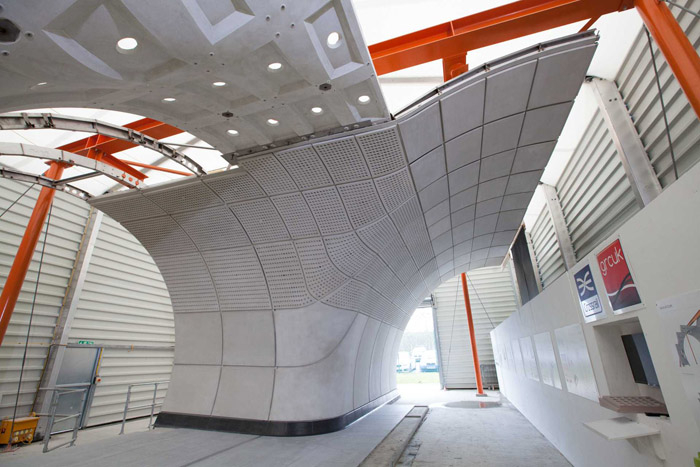
3D printed buildings
The ‘dream’ solution is that one day buildings would be printed in concrete, onsite, with robots and gantry systems laying down fast drying cement, working 24/7 to deliver at great speed, affordable structures for housing, offices, barracks, hotels and more. The reality of the limitations of the technology has meant there is more development in the deployment of 3D printing offsite, in a controlled environment, where the temperature and moisture levels can be maintained. This comes with build-size limitations for 3D printed components, as they have to fit on a trailer to be shipped to site.
The real hype for 3D printed buildings took off when China’s WinSun demonstrated in 2013 that it could make 10 single storey buildings in 24 hours, using prefabricated 3D printed components. This indeed was an impressive feat, however the design component of the ‘architecture’ (four walls with a roof) left a lot to be desired.
WinSun carried on its rapid development and created a 3D concrete printer which measured 20 feet tall, 33 feet wide, and 132 feet long and had created its own special liquid concrete from recycled building material, which was given the name CMS (Crazy Magic Stone). WinSun won over the Dubai royalty with the idea of having the first 3D printed office and so WinSun teamed up with Gensler to design a 250m2 concrete C-shaped cassette structure, with metal reinforcement between the layers, costing $120,000. This was eventually shipped and assembled in Dubai.
To hear a first-hand testimony on the project, Jorge Barrero (formerly at Gensler, now at HKS) talked at DEVELOP3D Live in Boston and I highly recommend 30 mins of your time, it’s both informative and hilarious. WinSun has gone on to build massive buildings which have drastically improved on its initial forays and continues to champion 3D printed buildings.
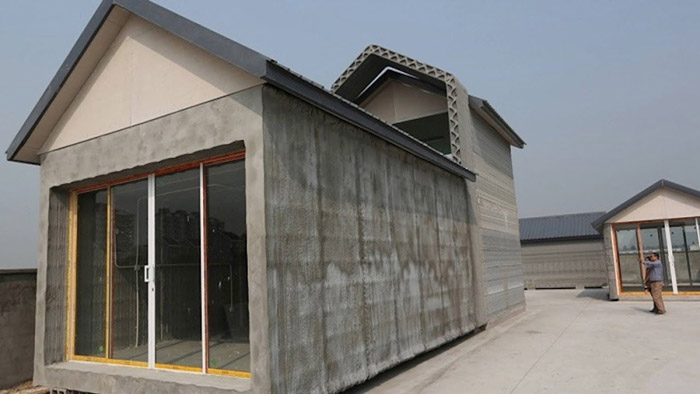
AI Space Factory is one of those Teslakind- of-firms. Set up in 2017 with the main purpose of competing in an ‘X Prize like’ NASA competition to design 3D printed habitats for Mars, which the company won in 2019 with a very interesting conical design, material and print process. It is now moving on to design habitats for Earth.
The firm is eschewing traditional forms and has devised TERA, TERAmini, ASTRA and EVO habitats, ranging between 500 and 1,000 sq ft, ranging from 1.5 – 3 floors and up to 24 ft high. The company is claiming green credentials using reclaimed and local materials (basalt and biopolymers) and looking towards a carbon negative model.
In November 2019, the firm started to print a TERA habitat in-situ at Garrison, New York, on the Hudson River. The birch plywood interior is being made in a factory and will be inserted when the outer shell is complete. It will operate as a short-term rental as they test the insulation materials and longevity. I think these designs are gorgeous, but have no clue as to how liveable they would be.
US-based 3D print specialist Apis Cor is one of the leading firms in delivering on the 3D print utopia. i.e. actually printing all walls and floors onsite. It has completed a number of buildings which go way beyond many of the 50m2 demonstration projects you will find on the web. It has developed its own print technology, software and gypsum-based material. It recently completed a twostorey, 640m2 curve-laden administrative building for the Dubai Municipality. The 3D printing arm was moved around the site by crane to build the concrete walls. The company has even worked out a process as to how to print floors and roofs. i.e. horizontal printing over voids. The company estimates a 250 sq ft space takes eight hours to print and would cost $5,100 in print material.
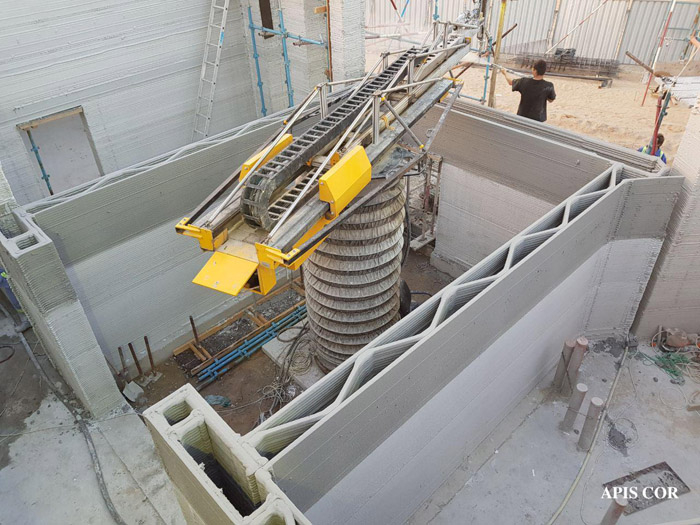
In all the case studies I have mentioned, you will have hopefully picked up that if it wasn’t for super-rich Middle- East royalty or mind-blowing space competitions, 3D printed buildings, while capturing the imagination, have yet to gain any real industry acceptance. And there is rarely a repeat order. Someone could easily argue that 3D printing in construction is a solution looking for a problem. But many people thought that about 3D printing in manufacturing and after the hype curve, it is now starting to make the impossible, possible.
Royal BAM
Outside of the University research labs, 3D printing in construction has seen development and limited use in big firms such as Skanska and Laing O’Rourke. But a lot of the development is coming out of the Netherlands.
TU Delft University, Eindhoven University of Technology, DUS Architects, MX3D, Houben / Van Mierlo Architects and Aectual have all been experimenting and building at 1:1 scale, refining their processes. The Netherlands is amongst the global leaders in 3D print research and certainly a leader in the commercialisation of the process.
Royal BAM has been working with TU Eindhoven and Weber Beamix since 2015 to develop an onsite and offsite 3D print capability, which uses ABB robot arms. In 2017 the company printed the world’s first fully structurally pre-stressed concrete cycle bridge (8 x 3.5 metres) in six sections, in two days. By 2019, BAM had opened a dedicated 3D print facility in The Netherlands, which can build elements up to 3.5m in height, but theoretically could go up to 25m. However, the limitation is the weight and size to fit on a lorry.
The key point with BAM is that while most others see the prize as building cheap houses, the company is primarily focussed on solving the hard problems, like performance, weight and reinforcement because it wants to apply the technique to civils projects which operate under higher loads. Figuring out the strength issue will open up all the existing areas where concrete is used. BAM’s 3D print technology can simultaneously lay metal wire within each layer of a 3D print. Primarily this is to stop cracking, but it does act as a kind of reinforcement as it is added layer upon layer.
BAM and TU/e are currently printing and assembling a ‘freeform’ 29 metre pedestrian and cyclist bridge by Michiel van der Kley, for the city of Nijmegen. A Rhino and Grasshopper model had to be created, to allow analysis and optimisation of the expressive form. It required a lot of experimentation and structural analysis to develop the best componentisation and sectioning for assembly and transport.
For now, printing offsite, in a factory, is the preferred method, as the environment is completely controlled, but BAM foresees a time when printing onsite will also be common practice.
At a recent demonstration, it was pretty clear that BAM believes this technology is now ready for commercial use. It’s currently in talks with Heathrow to use it on the next phase of expansion and London Underground and Thames Tideway have visited to see the ‘portable’ version in action. Over time, BAM expects the process to become more economical than the traditional concrete methods, perhaps as low as 50% in a few years’ time. And as usage grows, BAM has said it would open factories in the UK and Ireland.
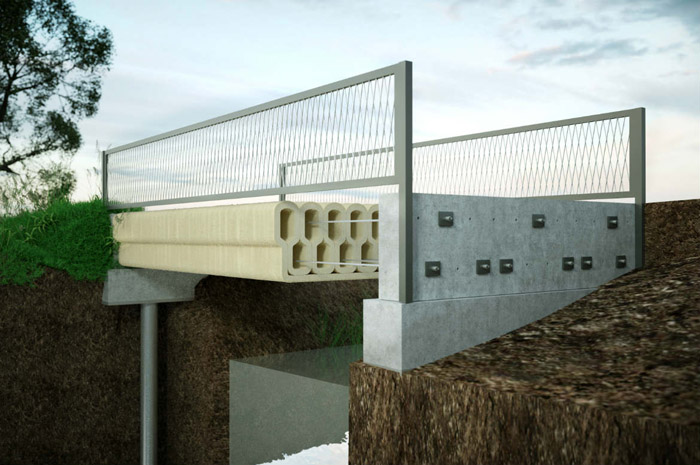
Print pros and cons
3D printed structures offer a range of potential benefits. The primary ones are cost and speed. Should this be making components offsite or printing onsite, there is no doubt that a whole lot of time could be saved in replacing brick and block work.
It’s pretty basic, but as there is no need for formwork or shuttering, a whole load of time, effort and on-site wastage can be avoided. According to TU Eindhoven, this could lead to a financial saving of 35% to 60% compared to traditional methods.
With the construction industry facing labour and skills shortages, a technology that reduces head count and delivers more with consistent quality, with less, deserves further investigation.
For eons we have been slaves to the right angle and those that have gone curved have paid an additional price, 3D printed forms can bring in interesting geometry at no extra cost and produce unique facades.
With the greenhouse gas issue, traditional concrete is not our friend. New green materials are in the pipeline which will make 3D printing a better alternative to using today’s cement. Using algorithms, it will also be possible to ‘lightweight’ structures and optimise material usage.
In the negative camp, there are some key problems which need a solution: reinforcement and tensile loads have limited the number of floors 3D printed buildings typically can have, as well as the loads structural elements can bear. There have been some advances in doing this, but performance is still a critical concern.
Related to performance, certification and testing of concrete is baked into the way we build. It is challenging to monitor the material to check for stability and strength, even in the manufacturing world, where printing in metal has become an affordable reality. With 3D printed metal voids can form within the unfused material, altering the strength characteristics and potentially resulting in a future stress failure in service.
In the half-a-job-bob category: 3D printed buildings can’t really finish a complete building – at best you get a shell. Work still needs to be done for structural placement, rebar placement, electrics, plumbing etc. A 3D printed house in France took just 54 hours to print – but it took four months for contractors to add windows, doors and the roof. One only has to look at offsite construction methodologies from firms like Katerra, where wood walls arrive on-site and everything is inside ready to go.
There are limitations to what geometry can be printed. In the manufacturing space, 3D prints regularly have to be printed with support structures to hold a 3D print together and are removed afterwards. This is not so easy with cement. Most print jobs will need a strategy of which way round it should be and how to optimise the print to get the required shape.
When printing, you have about ten minutes to put down the next layer before the underlying layer cures to the point that the two won’t properly fuse. I’m not sure what happens if there is a power cut or a nozzle jam and your print is compromised halfway through.
Finally, the finish. To me, it looks like dry elephant skin. The waffled edges of layers are incredibly rough. While all might be homogeneous within the printed concrete, the outside really needs extra work to smooth out the finish. Even if you didn’t like the 1950s grey Brutalist buildings, the surfaces were at least clean and had an aesthetic.
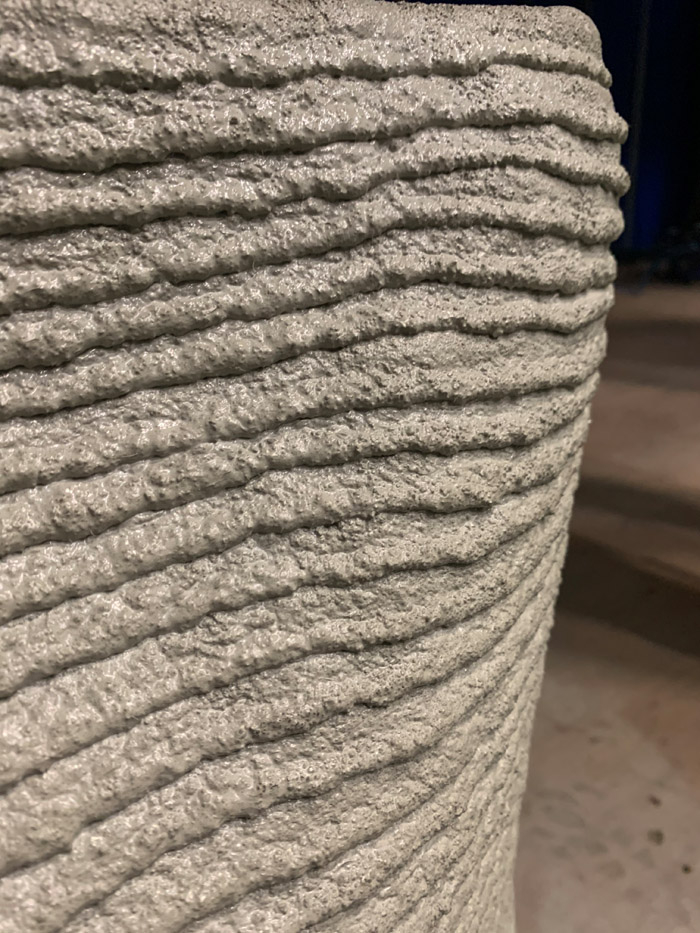
Conclusion
As the construction industry modernises, it is fantastic that major firms are literally rethinking every step of the process to improve delivery time, quality and price.
Without moving to 3D, whether that was SketchUp, Rhino or Revit, I don’t think the industry would be considering connecting its design systems directly to fabrication machines. 3D printing is perhaps the most esoteric of these, as it’s been happening in the more traditional steel and wood components for a decade or more.
It has to be said that it took humans a while to realise that moving nine metre-tall, 25 tonne granite rocks, 25 miles to the Stonehenge construction site was probably not the best way of delivering material to site. Bricks and blocks have been our ‘go-to’ solution for over 2,000 years and, guess what? They are optimised for the size of our hands! It’s only right that we should keep looking for alternatives and despite the current drawbacks I am convinced that 3D printing has a role in the new mix of technologies that will be adopted, especially offsite.
With major construction firms such as BAM working with Weber Saint Gobain, as well as other building innovators in construction like Skanska and Laing O’Rourke, the technology is set to go mainstream as these firms add 3D printing to their list of available processes. There will be projects where it fits well and others where it doesn’t. As architects continue to push the complexity of form with generative architecture, construction firms are going to be looking at all options to bring them to life.
3D printing in manufacturing
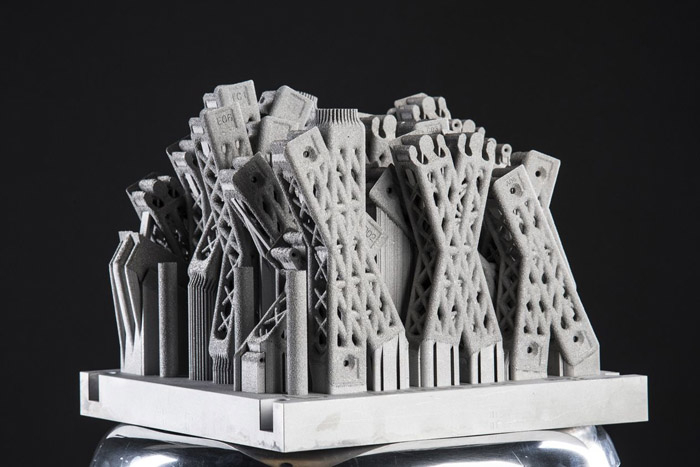
Manufacturing is decades ahead of construction in its use of 3D and factory-based assembly. It still has a long way to go, but 3D printing has evolved steadily over the last decade from an over-hyped novelty making plastic parts into a more commonplace manufacturing technology, printing in metal.
Low-volume, high-value parts have risen in popularity among automotive and aerospace manufacturers, with material properties, finishes, testing and quality control hurdles gradually being overcome.
The 3D printing hardware itself is developing faster, now that may of the leading names in the technology, such as HP and GE, are also their own biggest customers.
HP 3D prints parts for its own 3D printers, because the volume/cost ratio makes sense. GE, meanwhile, has placed almost 300 3D printed parts into each of its new GE9x plane engines, helping push the entire industry forward in accreditations for aerospace.
Trials by companies like Volkswagen, which enlisted HP and GKN Additive, are acting as a learning curve for mass manufacture – churning out over 10,000 metal AM model cars for an exercise in part management and quality control.
Footwear designers are also using production grade 3D printing materials for manufacturing sneakers. Carbon has been working with Adidas to develop an elastomeric polyurethane material used for midsoles and New Balance has partnered with Formlabs to develop ‘Rebound Resin’ from springy lattices. But mass production is still far away.
With 3D printing comes the ability to ‘print in’ performance, should that be light-weighting or strength. Design tools for this topology optimisation and generative design are now incorporated into the major CAD software for product design as standard.
The next big step is happening now, with new software utilising AI to add speed, automation and intelligence to the actual print process – promising to make even existing machinery work faster with more efficiency.
Stephen Holmes
The 3D printed metal car
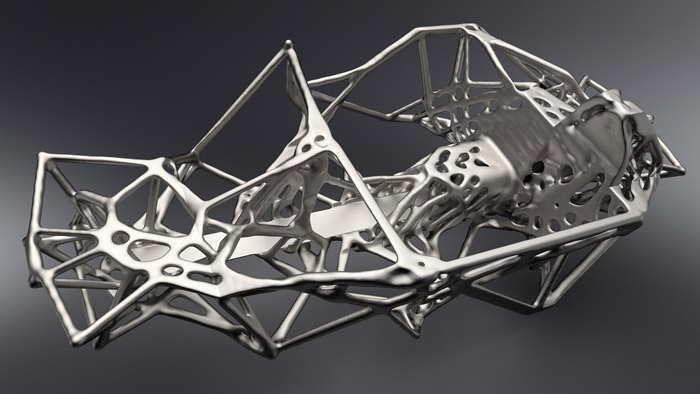
Hackrod is a California-based company on a mission to 3D print in metal a car chassis. The firm has built a massive 3D print bed, with a combined metal deposition print head and CNC milling arm. As the metal is deposited it is simultaneously machined to produce a refined finish.
Using computer simulation, derived from forces when driving a real race car, the chassis geometry was actually ‘grown’ by generative design. As the aim was always to 3D print the chassis, the design was unencumbered by the limitations of traditional manufacturing processes, which typically comprises metal tubing.
The company’s technology is still in development and a presentation on the vision can be seen in this DEVELOP3D Live video by Hackrod founder Mouse McCoy.
Construction 3D printing firms
XtreeE ■ xtreee.eu
Apis Cor ■ apis-cor.com
Cybe Construction ■ cybe.eu
WASP Crane ■ 3dwasp.com
Contour Crafting ■ contourcrafting.com
MX3D ■ mx3d.com
Vertico / University of Ghent ■ vertico.xyz
AECtual ■ aectual.com
AI Space Factory ■ aispacefactory.com
COBOD ■ cobod.com
BetaBram ■ betabram.com
SPECAVIA ■ specavia.pro
D-Shape ■ d-shape.com
WinSun ■ winsun3d.com
Branch Technologies ■ branch.technology
Ai Build ■ ai-build.com
Icon Build ■ iconbuild.com/technology
Mudbots ■ mudbots.com
Totalkustom ■ totalkustom.com
SQ4D ■ sq4d.com
Twente Additive Manufacturing ■ twente-am.com
Constructions-3D ■ constructions-3d.com
3D printing timeline

If you enjoyed this article, subscribe to our email newsletter or print / PDF magazine for FREE