George Broadbent and Dr. Xifan Jeff Chen of global AECO technology consultancy Microdesk explore the potential for connected operations in asset management, harnessing the power of BIM, digital twins, IoT and deep learning
Asset Management essentially is a cost-effective, systematic process of managing assets. It is however, this promise of cost management that is creating market pressure for owners and facility operators to implement an Internet of Things (IoT)- based solution. Connected Operations, which is designed to improve the operational efficiency of physical assets, serves as a critical component to complete the root definition of Asset Management.
Connected Operations is developing from a compelling concept used in manufacturing to an AECO industry-wide process. The benefits of Connected Operations implementation include enhanced interoperability efficiency, faster implementation speed, and optimised operation safety. It is triggering the development of several up and downstream sectors, like risk management, supply chain management, and manufacturing services. Connected Operations is stimulating the development and integration of state-of-art technologies such as IoT, Artificial Intelligence, cloud computing, Machine/Deep Learning, big data, and Augmented Reality into the Asset Management process.
Connected operations advances
The rapid growth of Connected Operations is a result of both internal and external factors. The AECO industry has been craving new technologies and solutions to increase operational efficiency and enhance asset performance. IoT-led data-driven technologies have sprung up to enable real-time visibility for organisations to overcome these challenges. Cost reduction is another critical motivator that is pushing Connected Operations forward.
The introduction of IoT plays a significant role in redefining the term “connected” in this process. More controllable operational reliability ranks at the top of the capabilities of IoT-enabled Connected Asset Management. Although it is still mission impossible to fully predict operational reliability due to any number of uncertainties, industry as a whole is getting one step closer to utilising the power of IoT-driven data analysis.
Sensor-equipped connected assets automatically log machine performance and operation status. This data is recorded and analysed via a Computerised Maintenance Management System (CMMS) in combination with cloud-based AI systems to make predictions on system performance. When this is compared to the traditional fixed maintenance schedule (i.e. calendar based), IoT-enabled preventive maintenance can lower operations and maintenance (O&M) costs significantly, while taking maximum advantages of human resources. IoT “weaponises” the existing Connected Operations with a state-of-art data-driven core, to diminish the boundary between tangible assets and their intangible digital constructs. In addition to scheduling preventive maintenance, data collected from connected assets can be used to perform a failure analysis targeting the root cause of unplanned downtime to improve performance in the future. Big data, the idea that the world is replete with more information than ever, is now gradually reshaping existing asset management from passive to a proactive and more sustainable mode.
Data leads to major changes
The world is converging due to the trends of merging of technologies withinand between-industries that have been changing the way people work, communicate, and interact with the physical world. Data-driven Connected Operations reveals enormous possibilities to collaborate with other state-of-art technologies. The Artificial Neural Network (ANN) based deterioration model has been widely used in failure analysis, while emergent Artificial Intelligence (AI) became a stronger challenger because it offers more accurate schedule predictive and proactive maintenance of assets. With the availability of big data from connected assets, machine learning can be utilised to detect patterns hidden in collected data to produce actionable insights to increase the accuracy of prediction and benefit decision making.
Looking into the upstream industry, Building Information Modelling (BIM), instead of being described as a threedimensional model, is a pure data presentation of built assets. The nature of datadriven decisions makes BIM and Connected Operations highly compatible and complementary. While owners and operators were struggling to find a solution to reduce interoperability inefficiency, the BIM and CMMS integrated process emerged from obscurity as an organic workflow. They carry data over through planning, design, construction, commissioning, and into the operations and maintenance stages.
The National Institute of Standards and Technology (NIST) examined US capital facilities and determined that organisations spend $0.23 per square foot annually due to interoperability inefficiency. A well-established as-built BIM model or digital twin that captures as asset information post construction and maintains data consistency and integrity could fundamentally reduce this cost. A BIM and CMMS integrated implementation could follow up to minimise the remaining expenses of interoperability inefficiency.
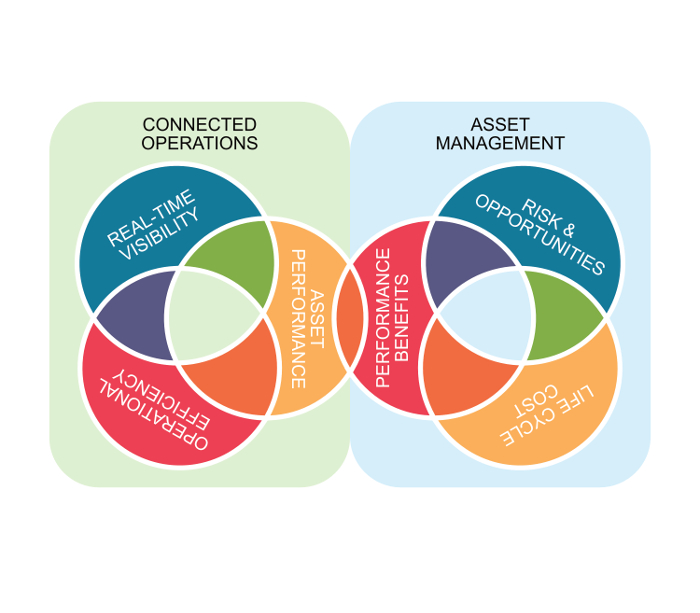
Aligning technical challenges
Although IoT and other Connected Operations related strategies and technologies carry tremendous potential to reshape how asset management is utilised for facilities, it is not free from challenges. All stakeholders involved in the Connected Operations process must work together to understand the methodology to maximise the efficacy of the solution. This requires coordination between facility operations, IT and business leaders. The relatively steep learning curve determines the degree of implementation and further affects the system performance.
From another point of view, this emerging topic draws attention to the complexity of maintaining the consistency, integrity, and interoperability of data collected from all sources. It became even more complicated when dealing with roll-in and rollout of new data formats and old data formats, as well as several different data formats. Potential scenarios include having the ability to merge BIM data with existing two-dimensional records in CMMS or trying to relate data inputs from an upstream BIM as-constructed model with collected IoT data in a bidirectional way.
From a financial perspective, Connected Operations may lead to relatively high capital costs for system implementation, sensor and monitor installation, as-built model and data collection, and labour training. Despite the Life Cycle Benefit/Cost Analysis of Connected Operations exhibits promising a productive Benefit/Cost Ratio (BCR), ROI and Payback Period, it is still a key factor keeping clients from understanding the system at the very beginning. Besides, policy, execution, adaptability, and other external influences that also indirectly positively or negatively impact system implementation, it is becoming an accepted method to implement Connected Operations from the Enterprise Level. Once applied, IoT-enabled Connected Enterprise Asset Management (EAM) provides a robust environment for achieving exceptional value from assets.
Technology of the Future
Connected Operations is paving a highway to the future with the data of today as the roadbed. The advent of IoTenabled Connected Operations is driven by the industry pressures for operational efficiency enhancement, and the graduation of IoT technology from academia to the industry.
IoT-enabled Connected Operations does everything that traditional solutions do while adding intelligence to make existing workflows adaptive and proactive through real-time alerts, short response times, and predictive maintenance. It also dramatically expands the scope of traditional asset management to embrace state-of-art technologies inside and outside the AECO field.
Looking ahead, the future development of AI-based cognitive computing and Machine/Deep Learning offers the real promise of more accurate schedule predictive and proactive maintenance of assets. The scope of Connected Operations has been expanded to embrace the data flow from design stage to supply chain. As the rapid deployment of BIM in the AECO industry continues, the integration of BIM and CMMS will be better connected by a unified code and standardised constructionasset data flow. This will further accelerate data exposure and benefit data usage in the asset management stage.
The Enterprise Asset Management sector has been described as “the single, biggest controllable expenditure on the planet.” IoT-enabled, data-driven Connected Operations is fundamentally changing the way that traditional asset management has been utilised for generations. With this new vision, Asset Management, the systematic process of developing, operating, maintaining, upgrading, and disposing of assets costeffectively, has been pushed to the forefront of the trend, and will most likely hold that position for a very long time.
If you enjoyed this article, subscribe to our email newsletter or print / PDF magazine for FREE