Sustainability meets industrialised construction in this new Autodesk-led collaboration to deliver affordable housing to West Oakland, California
Project Phoenix is a collaborative effort between MBH Architects, Factory_OS, and Autodesk Research designed to make housing that is less expensive, faster to design / build and more sustainable. According to Autodesk, the project is about 50% less in terms of time, cost and carbon footprint than traditional housing in the San Francisco Bay area.
Like many western regions, California has a shortfall of homes – estimated to be 3 million, in fact. Project Phoenix is a 316-unit modular housing development in West Oakland on a site that is heavily impacted, both from congestion and noise pollution.
Targeting carbon neutral, the housing units feature innovative materials, including facade panels made from a core of mycelium, the rootlike structure of mushrooms. The panels themselves are carbon-negative, as the process of making them involves more carbon absorbed than emitted, due to the large volume of plant-based material that drew carbon out of the air as it grew.
Design to site time is claimed to have been crushed from two years to one year and all the modules are constructed offsite, including the external cladding panels.
Factory_OS, a Californian off-site firm (in which Autodesk has made multiple investments) is making studio apartments, one bedroom, two-bedroom interlocks with housing modules that can be assembled onsite ‘like Lego’.
This is not a one size fits all approach to factory-based industrialised construction. MBH and Factory_OS have developed about 25 different modules, which can be stacked in different ways to create different building types.
“Our goal is to really address collectively, a housing crisis and environmental stewardship, and at the same time, not have it be a race to the bottom so that your dwelling units are awful, ‘but we did it modularly”. The idea is to raise the bar,” said Andrew Meagher, vice president of design and engineering, Factory_OS.
“We don’t want to have a McDonald’s type approach. where it’s ‘oh, I recognise that building, no matter where you are in the world.’
“The building envelope is determined by the designers, the site designers, and hopefully if you’re using this facade panel, this is just one version. So over time, you’ll be able to have any kind of configuration and articulation of this facade panel – bay windows, decks, recesses, notched – but the core dwelling unit stays the same.”
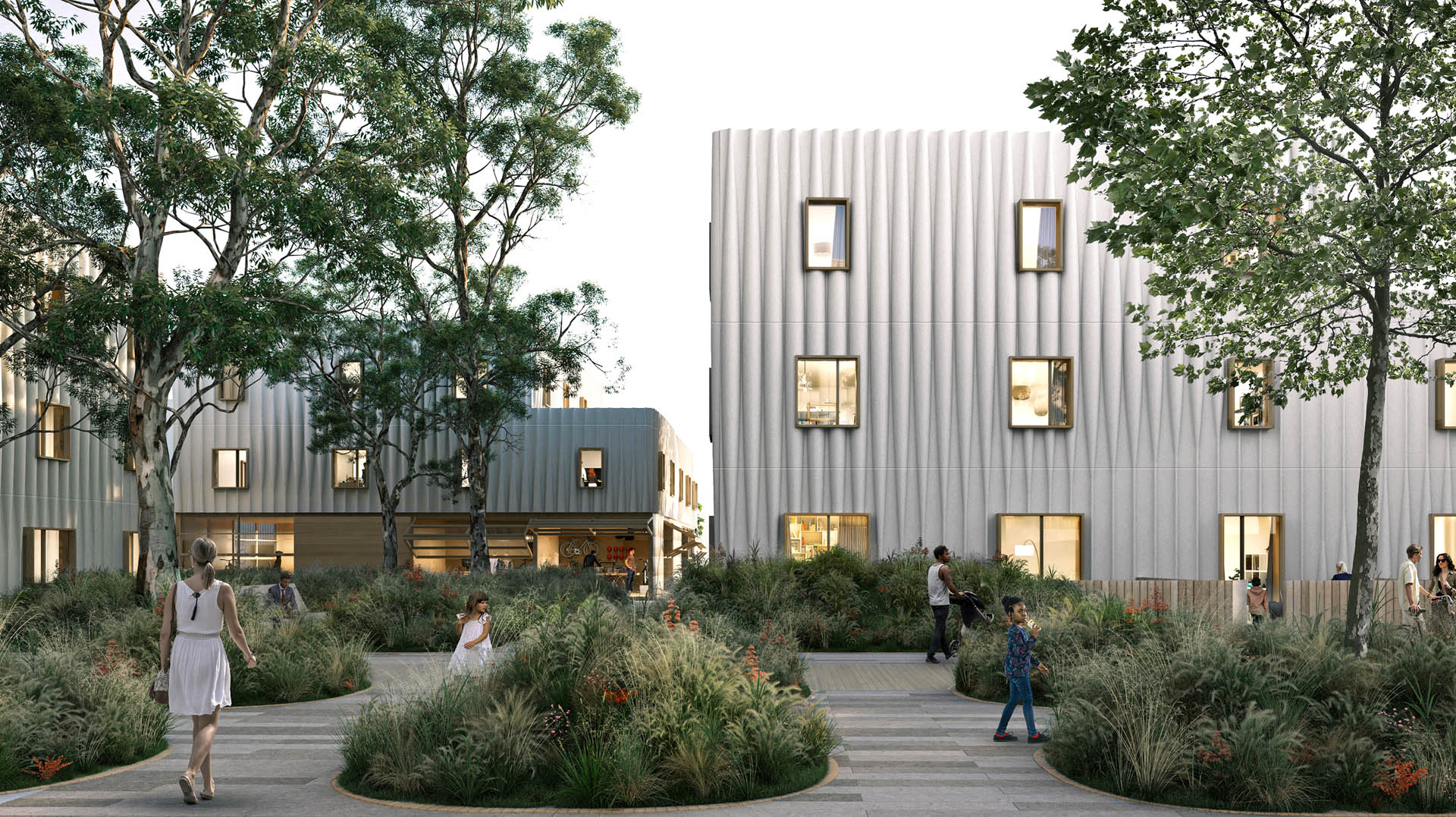
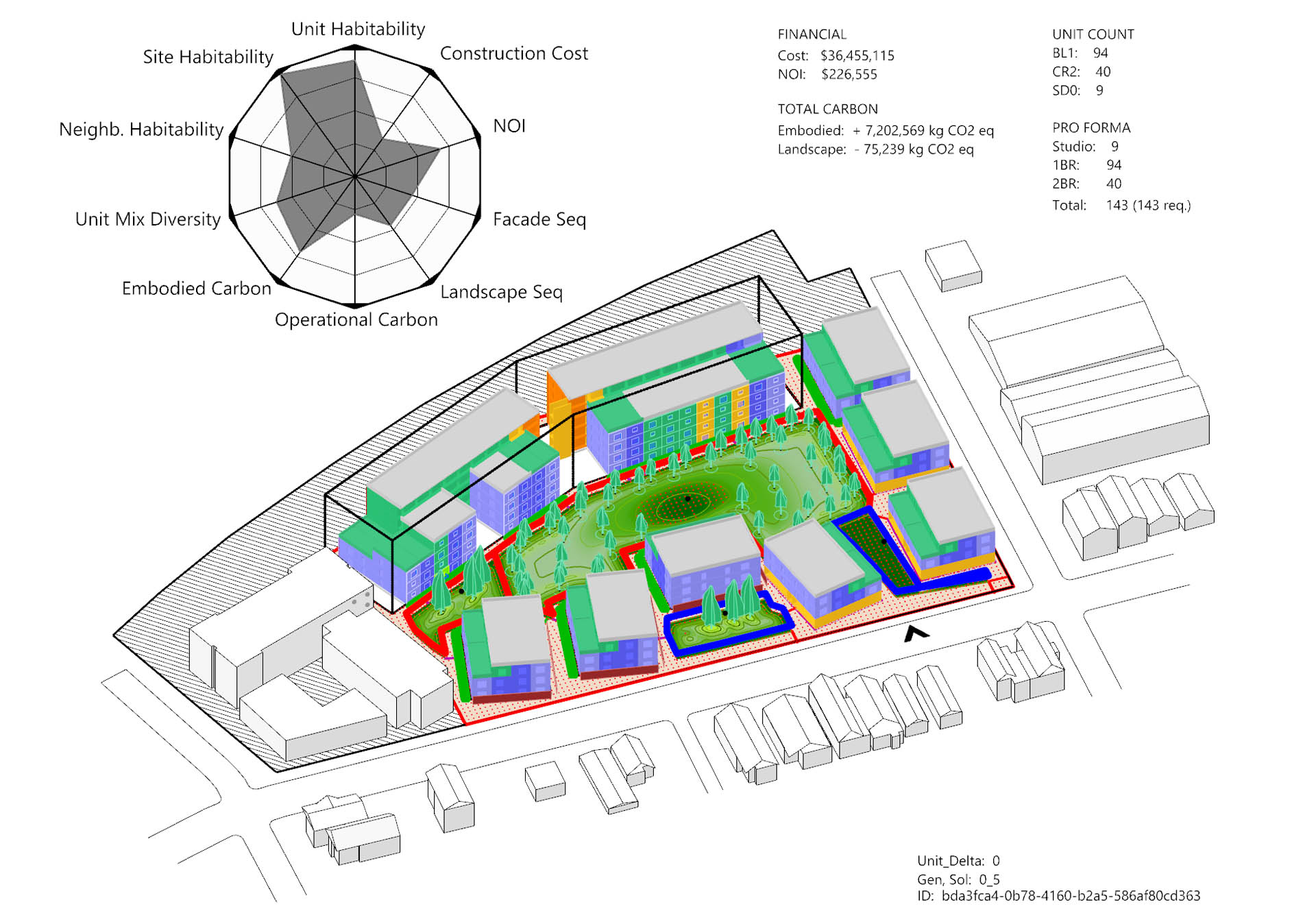
From a software perspective, MBH Architects used Forma for early-stage design and Revit for detailed design, with data shared with Factory_OS via Autodesk Construction Cloud.
Forma is used to navigate trade-offs between things like operational carbon, embodied carbon cost and liveability.
MBH Architects can rapidly explore a huge range of options such as adding a floor to a building, nudging the structure’s position north or south, shifting a playground or greenspace from the edge of the development to the middle.
Find this article plus many more in the November / December 2023 Edition of AEC Magazine
👉 Subscribe FREE here 👈
Tim Haley, director, technical; architect, at MBH Architects was effusive in his praise for Forma. He told AEC Magazine it saves an incredible amount of time at the very beginning of any project, “We can figure out the parking, we can figure out some of the energy used. The best time to make a decision about sustainability is the very beginning. If you have to reorient your building five months into the construction schedule [it’s too late].”
‘Project Phoenix’ is only just the beginning, as David Benjamin, who leads applied research on net-zero buildings at Autodesk Research explains, “We’re trying to address the one-off nature of (generally) construction and allow software to play a role in helping to do those things quicker.
“What we’re experimenting with here will allow other projects in the future to be designed more quickly with more intelligence and more data, including the carbon in numbers.
“We’ve been working as a team to basically figure out what are the rules of stacking the modules and can we put that in algorithms so that you can do that on the next project?
“What is the carbon footprint of both the existing materials in the factory but also the new innovative materials and can we make that available to other designers on other projects in the future?”