As the industry moves to adopt 3D workflows, the ability to capture as-built conditions in 3D is finding many new application area beyond surveying. We evaluate the latest scanning innovations
Every time I write about Scan to BIM, I start off by stating that there is no such thing. The phrase that so easily slips off the tongue, leads people to think that there is a quick, autonomous and instant way to bring the real world inside a BIM application and have an intelligent model ready to go. I am sorry to disappoint but this just is not the case.
In many respects the hype that follows BIM around also leads owners to perceive that in some way less work is done in the process of design and by using a BIM they can magically expect savings of anything up to 30% on design development. Myths are easily started but oh so difficult to squash.
Building Information Models are much richer than their predecessor’s 2D symbolic representations, the density of knowledge captured and layered with BIM provides even more benefits from the fact that building elements are modelled in 3D.
The ‘Scan to BIM’ process only caters for the physical 3D representation and will only ever generate dumb XYZ points or meshed surfaces. These ‘dumb’ points act as a guide for those who model BIM components to replicate the ghostly as-built point clouds in BIM components, such as walls doors and windows. This process is, in itself, a skill set requiring training, experience and additional software tools.
Many surveys will not need to be done by laser scan. The old and proven ways will be quicker and more economic. Simply asking for a laser scan survey will add to the cost to get the same result and the 30GB point cloud model delivered will be handed to a design team who will have no idea what to do with the data format.
Like BIM, owners and management are asking for work to be done in a certain way because they have heard it is the latest thing, often with no comprehension of the benefits or what they can do with it once they get what they have asked for.
As the reality capture world develops, I feel this situation is only going to get worse as the technology involved in scanning just gets ‘cooler’ every year, now featuring UAV (Unmanned Aerial Vehicles) aka drones, robots and hand scanners.
The act of effortlessly capturing reality for manipulation in a computer just seems so wonderfully Sci-fi, no wonder everyone wants to do it. Until real-world captured data becomes ubiquitous, 3D manipulation skills will still remain a specialised area. For this to happen the price for the scanners still needs to drop to pro-sumer levels.
SPAR Europe
The latest advances in real world data capture were demonstrated recently at SPAR Europe, held in Amsterdam in December 2014. The event features a diverse exhibition area along with a conference programme, which included a Scan to BIM track. Speakers on the Scan to BIM track included; Fred Mills, Managing Director, The B1M, James Kavanagh, Director of Land, Professional Groups and Forums, The Royal Institution of Chartered Surveyors (RICS) and John McCreadie, Business Development Director at IIC Technologies.
The Scan to BIM session started with Mr Mills of B1M, a video resource on BIM, explaining the movement of the building industry to BIM. He concentrated on the need to up-skill the industry — the ‘1M’ being the million people required to instigate widespread adoption of Building Information Modelling.
Mr Kavanagh explored the link between BIM and wide area geographic information systems, asset management projects, smart cities the expansion from 3D into 4 and 5D BIM (X,Y,Z, Time, Cost) and the advent of automated cost estimation software. As part of the process, RICS laser scanned and surveyed its own headquarters in London to get a better understanding of the scan to BIM process its members are being often asked to complete.
Mr McCreadie pondered if Scan to BIM was an opportunity or a threat to surveyors, as BIM changes clients’ data requirements, surveyors risk becoming increasingly irrelevant if they fail to adapt to the challenges of BIM.
He recognised that the delivery of 3D data for an existing building in a BIM ready model is a challenge, especially when BIM is new to many clients.
IIC Technologies worked with Heriot Watt University and Simpson and Brown (Architects) to specify and create a BIM for existing heritage buildings in Edinburgh. During the project Mr McCreadie recognised that recording the fabric of the building for digital documentation purposes versus creating a model for the maintenance of the re-developed building were two different things and required different approaches to creating the 3D model.
Overall it was a well-attended and engaging session, given mainly from the surveying perspective as opposed to the consumer of the surveyed 3D data. It was clear that, as an industry, surveyors and the architects are both still wrestling with the changes brought about by moving to a 3D design process.
The conclusion being that surveyors are well-placed to seize the opportunity to provide scanning services, but need to work with their clients to educate them over its conversion to meaningful BIM.
Recent advances
As the data capture market grows, the technology expands under the skin of today’s BIM systems. At the end of last year both Autodesk and Bentley made announcements that they were working with the major scanning vendors. This has been driven predominantly by the new focus on construction in the BIM market, where on-site needs require more measurement and spatial data. Bentley was first to announce a deepening of its relationship with Trimble, where the two companies are developing a mutual schema for construction BIM.
Bentley has included support for Trimble measurement and layout devices at a platform level. Trimble, meanwhile, has adopted Bentley’s iModel technology for data mobility within the collaborative process.
Autodesk has a historic relationship with Faro and supports its file formats as native, but this year is adding support for Topcon devices at a platform level (see tinyurl.com/topconapp). This may be a coincidence but it is clear that the leading AEC developers realise that BIM needs to be taken onsite, and with the latest devices can directly feed layout and placement throughout the construction process.
This has also driven mobile development and so now BIM models are accessible ‘live’ over wifi and cellular on iPads and Android tablets, which in turn can drive laser pointers and scanners.
Conclusion
The scanning and reality capture market is undoubtedly growing fast. While there are many software firms that are innovating, the key thing holding back wider adoption is the cost of the scanners. Starting at £20,000-plus, it’s just not something that many firms would use in-house. The take-up of hand held scanners is growing, which is bringing down price and accessibility, but these still cost £3,000-£10,000 and are limited in the size of object that can be captured.
Photogrammetry and video to mesh looks to be the cheapest entry point to the market and Autodesk’s Recap and Memento are enabling new possibilities from every day imaging devices. When you add drones and video into the mix, both the small and large scale are covered. The accuracy of photogrammetry is not the same as a laser scan but on the scale of a building site this could be unnecessary, while a manufactured object for fabrication would have issues.
Scan to BIM is a work in progress and, over time, will become more automated and easier to do.
But perhaps we should also consider that not everything has to be modelled to achieve a desired outcome. By accepting that ‘dumb’ spatial data has its place in the BIM workflow, we can stop worrying about converting everything we see to data rich models.
Laser scanning and point cloud technology
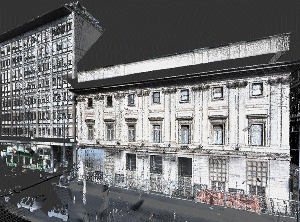
Autodesk
Autodesk released Recap, Recap Pro and Recap 360 last year for the collation and registration of laser scan data and conversion of photographs to a 3D meshed model. The service provides access to the cloud to publish and stream huge point cloud models. Autodesk Memento can take point clouds, video and photographs and create incredibly dense and accurate 3D meshes. It handles huge datasets and has a minimalistic interface. Advanced sub-division surfacing, intelligent hole filling and the ability to compare meshes and drive 3D printers gives Memento a unique feature set and will be expanded to offer advanced T-spline editing.
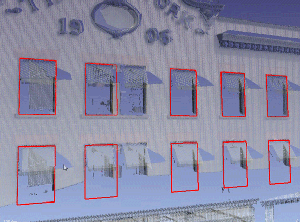
ClearEdge
ClearEdge offers the most enhanced laser scan to Revit model process, using advanced shape recognition algorithms. The EdgeWise BIM Suite for Building, MEP and Structures offers ‘structure’ extraction, ‘cylinder’ extraction and ‘planar’ extraction and integrates with Revit so structure, walls, windows, doors, pipes, conduits, and round ducting can be automatically extracted into Revit as vanilla Revit Family components. You can even teach the software to find repeated objects by highlighting the part of the point cloud and the software attempts to learn the pattern. It will then search through the point cloud and identify the objects.
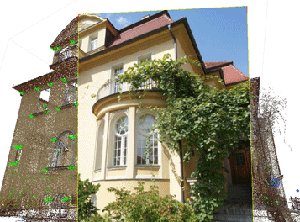
Kubit
Kubit is a German-based developer of standalone and Autodesk-integrated surveying tools. Its products include TachyCAD for online surveying, PhoToPlan for image rectification in AutoCAD, PointSense for 3D scanning post processing, VirtiSurv for viewing laser scan data, MonuMap for structured mapping of building conditions, DistoPlan for surveying as-built and hylasFM for facilities management. In the March / April edition of AEC Magazine we will have a guide from Kubit on the principles behind generating a BIM model from point clouds.
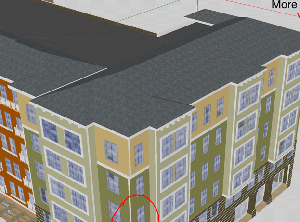
LFM Software
LFM software, part of Aveva, is heavily involved in the factory and facility management side of laser scanning and is about to introduce the concept of a ‘living point cloud’. Recognising that the modelling of complete facilities is often an expensive process, LFM is advocating a point cloud that provides a framework for doing partial edits when changes are made and then resubmitting those back to the cloud.
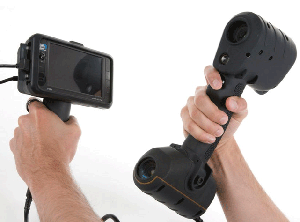
MV4D
Mantis Vision(MV4D) is an Israeli company with some seriously clever hand held scanner technology. The devices project a structured light/ laser pattern on an object which, as you swipe over them, reads the deformation of the pattern to build the model. The smallest of its devices fits neatly in the palm of your hand. This is probably one of the best mobile scanning technologies currently on the market.
■ mv4d.com
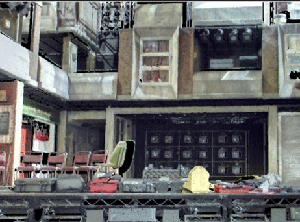
NCtech
NCtech is based in Scotland and produces a very clever 360 degree imaging device that sits on top of a tripod. Using four fish eye cameras the iStar rapid imaging unit can capture an environment in high-resolution 50MB panorama in a single shot. It also is capable of doing HDR (High Definition Range) imaging of three exposures. The iStar offers video capture and streaming of full 360 degree environments and works in low light. The company is also working on higher resolution devices.
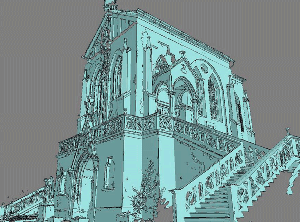
Pointfuse
Arithmetica’s Pointfuse converts point clouds to vector models. The software is fully automatic, fast and accurate and is directly aimed at scan-to-CAD workflows. Pointfuse enables the simultaneous cropping of multiple point clouds into a single point cloud, which can be converted to a single vector model for 2D elevations, plan views and sections. Batch conversion is also possible with export to DXF or IFC, and has been tested with ArchiCAD, Autodesk Revit, Blender, Rhino and SketchUp. Pointfuse Free, Lite, Pro and Pro Trial are available.
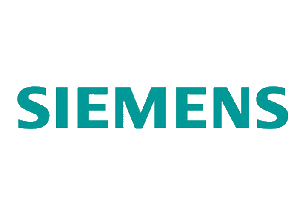
Siemens
Siemens is not a major player in the BIM world but through Siemens PLM it does have a business in factory design. It recently licensed the Pointools engine from Bentley Systems and has included it in its Tecnomatix and Teamcenter products, as manufacturing firms look for a way to document and manage their facilities. Increasingly firms are opting to laser scan their factories and use this spatial information for planning new machine placement and possible clashes.
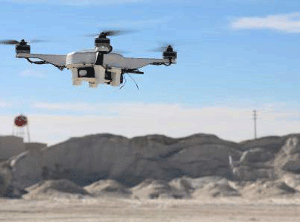
SkyCatch
SkyCatch is an autonomous drone that can follow a regular flight path over a site. Carrying a payload of high resolution stills or video camera, the service can provide accurate snapshots of construction projects, or survey for as-built. With companies like Autodesk working on video conversion it would be possible to use this data to build a 3D model of a construction site. This mesh could be compared against the BIM model to check for errors, issues with construction sequencing, checking volumes of raw materials or identify potential problems.
If you enjoyed this article, subscribe to AEC Magazine for FREE