Given the digitisation of the AEC industry, and the effort that firms put into designing and documenting projects ahead of construction, there is a general feeling that not enough is being done to verify and document what actually gets built. A new initiative aims to promote better work practices
As a magazine we are always wary of the fact that our excitement for new technology can often lead to selling the utopias promised by our friends in software and hardware development. BIM has undoubtedly delivered benefits over drawings, but it has also created its own problems. Many of these technologies also fail to get out to the construction site. So, while architects may get lost in detail modelling, Design for Manufacture and Assembly (DfMA) and digital twins, in the real world what gets delivered does not match the original design intent. Buildings are not currently delivered by robots.
Despite digitisation, errors on site still occur, undocumented changes happen in the white heat of compressed delivery schedules, and nobody really wants to own them or the associated liabilities. As digital deliverables increase and, perhaps, digital twins become more relevant, capturing the as-built for documentation and use downstream needs to become part of the standard practice of construction work. But this currently comes at a cost.
This becomes easier, however, as technologies develop and evolve. While we might not all be able to afford a Spot robot to roam a building with a scanner, iPhone solutions, as we have covered widely this month, mean that anyone can capture and document building elements, or rooms, using a device that everyone has easy access to.
The Construction Verification Initiative is a LinkedIn group set up by professionals working across all construction disciplines, to promote the functional benefits of construction verification and establish good practice for its use. The aim is to educate clients and practitioners to understand the full value of verification and to support the industry in its adoption, align standards and evolve the landscape of legislation around improving construction quality. This month we highlight the opinions of four active members of the Construction Verification Initiative (CVI), coming at the issue from different directions, relative to their roles in the market.
Adam Box
Business Development Manager, Topcon
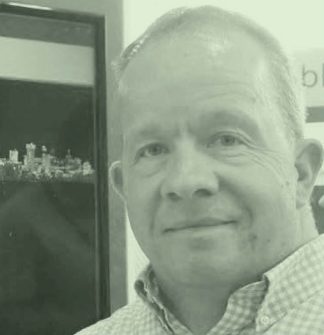
Technology and the construction sector are very uneasy bedfellows. You have a ‘traditional’ industry that has had centuries of doing things in a certain way, supported by tried and tested standards, contractual protocols and good old-fashioned experience. When you align this with new technology, which often doesn’t care about the way things used to be, rewrites the delivery process and drops a grenade into traditional processes, then it is always going to be difficult.
Despite this latency, change is happening. Having been fortunate (if that is the right word) to see electronic drawings, 3D models and cloud-based information distribution become accepted, I am still a believer in the increasing value that technology can bring to the construction process. And I do mean increasing value, when I see the transition of focus from the design and planning stages to handling the on-site delivery side, then this is where the real gains are to be had.
I certainly am not discounting the advantages provided through having a well costed, clash-free 3D model in place prior to the construction phase. However, most people would agree that when the large, unexpected costs appear it is nearly always during the delivery phase.
Technology is working hard to try and manage the risks and mitigate the errors. On-site data is more freely available than ever before and automation continues to arrive on the job site. Despite all the changes going on, one question has always remained the same, “Have you built it right?” It is here that we at the Construction Verification Initiative believe lies one of the biggest challenges to overcome. Just answering basic questions like “Is it in the right place?” or “If not, then what else has been affected?” can often reveal huge potential future costs implications through rework, redesign or, in the worst cases, demolition. All of which are not healthy to remaining on program and within cost.
Digital capture devices have become ever more affordable, smaller, more mobile. Data processing and model verification is much more accessible than ever before
The good news is that the right tools to do just that are readily available and getting easier to utilise every day. Digital capture devices have become ever more affordable, smaller, more mobile. Data processing and model verification is much more accessible than ever before, with tools such as Verity allowing for clear informed decisions on identified deviations. Implementing the right tools and baking them into the project process as ‘business as usual’ is one of the primary goals that the CVI wants to help achieve. We are under no illusions that this will take some time, but for help with your journey we are a passionate group who want to support and facilitate this change.
Ben Raybould
Associate Director, Technology, Turner and Townsend
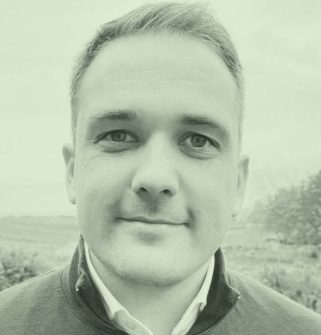
For many, construction verification is associated with main contractors and their respective surveying teams. However, we’re seeing an increase in the opportunity to specify construction verification at a much earlier project stage, at the hands of the client.
Better information management driven by industry standards such as ISO 19650 means clients are becoming more aware of the opportunities to design and construct their assets in a smarter, more organised way. Whilst construction verification in its true form is highly technical and requires specialists at each end of the data, the outputs are becoming more presentable and user friendly for clients and their project delivery teams in assessing many aspects of the construction process.
The opportunity to identify how the programme is proceeding, or the accuracy of the build, has long been an interest of the client but is often managed using traditional methods. Replace this with an accessible dashboard that is able to draw from near-time site data, 3D models and construction programmes, and you’ve got an incredibly useful tool and process to manage a project effectively.
However, whilst we see lots of opportunities and positives in construction verification, we find ourselves in the debate of “Who should pay for this service?” and “Just get it correct in the design and build it properly”. These are fair questions, but often cause verification to be omitted from the construction process entirely.
If we think about these questions, as an industry, we’d like to assume the design is coordinated. It’s designed against the background of a validated model, and it gets installed exactly how it’s designed! Even with the greatest efforts this really isn’t possible, mainly due to the varying nature in which construction moves! However, to give ourselves a chance, which includes accepting that things change, we can apply the progressive verification logic to all of our projects, and we will gift greater awareness of the true reality.
Opportunities for clients:
- Reduce the traditional risks associated with visiting a construction site, by reducing stakeholder site visits, inductions, and the associated environmental impact.
- Support commercial management, digitally, for the valuations and final account.
- Support operational readiness activities by capturing a record of equipment at the point of installation, archive information in one location, and increase construction and asbuilt awareness.
- Support avoidance of disputes, rather than dispute resolution by keeping accurate recordings throughout the construction and handover programmes, enabling early warning and effective issue management.
- Support progress validation and assurance by connecting directly to the digital design process, enabling users to understand near time site conditions from anywhere, anytime.
- Validate and assure progress against the programme (using advanced 4D programming).
- Control quality of construction by enabling virtual site tours, effective and informed change control, organised and navigable progress photography, and a platform for completion reviews and sign off.
Robert Klaschka
Founder and Principal Consultant @evrbilt
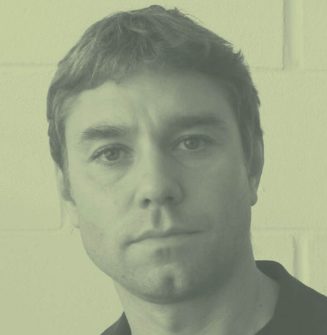
While the product options for software construction verification continue to grow, the process itself remains poorly defined, and so, like many digital support processes in the built environment, references to it are starting to appear in contracts without clarity of what the author is expecting.
To successfully deploy verification, we first need to understand what we are trying to achieve. At its heart, the construction verification process involves comparison of laser scan or photographic record data collected on site to a 3D design BIM. Within this there are three functional use cases that we generally seek to support:
Progress monitoring: This process uses photography or laser scan data to track the progress of site work against a digital model.
It has a lower requirement of accuracy because it is primarily about establishing the presence of objects. This approach does require frequent collection of data to ensure a meaningful record.
Using this approach could allow a site to track the progress of planned work against real activity on site and anticipate emerging programme or logistical problems that otherwise remain unnoticed until they cause delays or disputes.
Accuracy of as-built conditions: Comparing laser scan data with models at or near the end of a project can serve to assist in the production of more accurate asbuilt information. This process can involve a series of scans throughout a site as a project reaches completion to capture what has been built and to make a comparison. The site may need to be scanned and re-scanned as works are concealed, for example, when a suspended ceiling goes up.
Accuracy in as-built models should be defined by the reason for the as-built information. This could be to help an operative find and maintain a system concealed above a ceiling which arguably could mean opening the correct ceiling tiles. Or to allow a client to know that the designed lettable area has been achieved in the completed project, in which case the expectations could be dependent on the square footage value.
Using this approach can support contractors or subcontractors when they are documenting the changes that have occurred during an installation to ensure the as-built record reflects what has been built.
Accuracy during construction: Like accuracy of as-built conditions, this process involves comparing models with laser scan data. However, to verify during construction many more increments of data collection are required throughout the project because this follows the construction as it occurs.
To be meaningful, data collected for this approach requires a high level of positional accuracy.
Using this approach can check the position of installations during construction and identify differences from the design. Establishing the impact of these differences can reveal future clashes with following work much earlier and prevent delay from re-work that would be required without this insight. This process also provides the information required for progress monitoring.
At this point it is worth observing that generally contractual references to verification focus on improving the poor quality of as-built records. This could be viewed as a by-product of the general direction of travel towards better more accurate digital handover of buildings. The other use cases are more relevant to supporting the management of the site, both in monitoring progress and that construction tolerances are being met.
To understand the challenges of the process we need to consider the relationship between the physical site and the documentation from which it was derived. Whether in a 3D model, or 2D documentation, every construction element has an absolute positional relationship with every other element. Columns and walls are snapped to grid lines and line-through perfectly vertically up the model, floors are perfectly flat. The resulting real buildings, whether well-built or not, will differ in ways that we hope deviate within acceptable construction tolerances.
So why does this go wrong? While arguably there are many human factors that cause problems on site, including poor positioning of installations and undocumented changes during construction, we should ask, ‘are we setting up our sites to enable the quality of installation that a perfectly coordinated model or drawings have led us to expect?’ Arguably, establishing accurate position anywhere on a site relative to the originating model would mean that there was no excuse not to build in the right place. Yet, as with many of the dysfunctional consequences of pushing risk down to specialist subcontractor and installers, this results in shortcuts, such as using parts of the construction that have already been built to set out relative to.
Real world examples of this could be measuring a relative height from an as built slab that might have a tolerance of +/-25mm, or setting out a wall from a structural column that might have a similar tolerance. In each case the result is that one is setting out an element that anticipates high accuracy from another element with an acceptable low accuracy. If you work this way, the low accuracy becomes baked into everything that is positioned relative to it.
There is some irony that the same problems affect attempts to verify site work when something is identified as going wrong. Reestablishing accurate reference points on site to carry out positional verification locally is costly and so often the poor practice of best fitting site data to as-built columns and levelling from as-built floor is substituted. Ask yourself, what you are measuring from at this point? It’s entirely arbitrary and, more importantly, isn’t going to stand up in a dispute.
So how can we move beyond this piecemeal approach to position, and can we identify the points where the risk is greatest during a construction project? As is so often the case, when responsibility is passed from one party to another, the information flow breaks down. This is true for positioning, whether at the point that a design is being passed to a contractor or a package is being passed from a contractor to the subcontractor who will install the work.
An example of this is where a survey is commissioned by the designer, but the reference points are not preserved for the main contractor to set out from who commissions their own. Two surveys, both separately georeferenced, could quite possibly misalign by 50mm. It is self-evident that this minor cost of planning and installing permanent stations, documenting them in a witness statement and providing them as digital coordinates as part of the contract documentation to be taken on by the main contractor, will very quickly pay dividends to any project.
When the build progresses, extending these reference points inside the building and, again, documenting them and providing them in digital form to subcontractors both to set out from and to be used to verify work, will result in smoother installation, and enable meaningful tracking of progress and accuracy.
Unlike many of the more esoteric wants that we have from digital construction, all the technology required to do this now is available, we simply choose not to do it. More importantly, if we start to plan for all parties working on site to have easy access to accurate position, there is every chance that the verifications we perform will be focused on high value activities such as digital progress monitoring and digitalising technical sign-offs and handover, instead of trying to correct poorly built work.
Andrew Evans
Senior Product Manager Digital Construction Works (DCW)
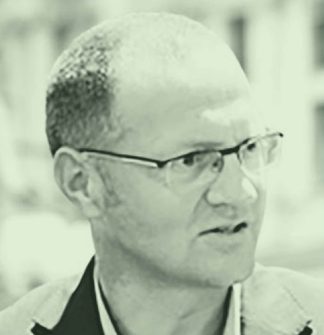
Where does construction verification fit with the other project stakeholders, such as the planning teams and the clients – those paying for the job?
Any form of digital documentation is going to support increased confidence in the project schedule. If that documentation is geospatially enabled and capable of quantifying build quality to high tolerance, then that can only be a good thing.
Mistakes and design issues caught early can be planned out of the build entirely. Snagging becomes an almost non-event. If that feedback cycle between site and office can be implemented in real time, with high quality measured data or deeply informative geo-located visuals, then construction automation is getting closer to being Business As Usual.
Back in 2014 I wrote about tools and technology to enable quick and easy construction as-built .
Construction verification was then (and is now) a reality, but what if I told you we had also managed to use the output from the verification routine to automatically update the project plan so that all project stakeholders could be informed of construction progress in their familiar planning environment?
If the feedback cycle between site and office can be implemented in real time, with high quality measured data or deeply informative geo-located visuals, then construction automation is getting closer to being Business As Usual
Not only is there the capability to do detailed planning and digital rehearsals, but there is also a proven method to enable a fast-feedback of in-field as constructed status.
Not only that, but the input doesn’t have to be from a static scanner. We’ve proved it out for mobile and for drone derived data as well.
Kirsten Lamb of the Centre for Digital Built Britain presents the following statement about the Built Environment usage as part of a broader overview of the development of Digital Twins (DT) over time.
In the built environment, the use of digital twins is just beginning to take off. Fully realised examples are rare, even at the level of individual assets. A great deal more technological and organisational maturity is needed for a National Digital Twin of built assets and services.
She notes in her recently published Scoping Review of Principle-based Digital Twins that the concept is far from new.
First used by NASA, and commonly in place for manufacturing, she highlights that the majority of publications discussing the motivations and uses for DT do not really focus on their use in the Built Environment, except in the realm of Smart Cities.
As you would imagine the ideas of how a DT would work in Smart Cities is well-aligned to the Gemini Principles, serving the public with secure data that is enabling sustainability and collaboration.
It would appear that, at this early stage, the focus is really on the ‘how’ of DT rather than focusing on the ‘why’.
This is great news for digital construction, as it seems that we are still early on in the implementation of these concepts for what could be termed the construction digital twin, and, as a group, we’ve got a very good handle on the how, and that is considerably more than just creating a pretty visualisation.
What I’m hinting at here is that we also have a pretty good picture of the ‘why’.
Image credit: Construction verification in Verity. Image courtesy of Jacob Down