UK start-up Correvate offers cloud-based registration for laser-scanned point clouds. With a growing trend to mix and match scanning technologies, the service recently added support for SLAM, terrestrial LiDAR and UAV captured data
Laser scanning is rapidly becom ing a commonly used technology within AEC. While it has traditionally been the realm of surveyors, smaller and lower cost devices have started to drive wider adoption.
Innovations such as SLAM technology (Simultaneous Location and Mapping) liberate scanning devices from tripods, to enable real-time data capture on the move. This rapidly speeds up capture, lowering the cost, but sacrifices some degree of accuracy.
With portable scanning becoming a common practice, users are starting to mix-and-match scanning technology on the same projects. SLAM is also set to benefit from the huge amounts spent by automotive firms, developing automated driving systems and in aerospace for unmanned UAVs, where it provides mission critical ‘vision’.
Last year London-based Correvate launched its Vercator service, a cloud platform that automatically registers static-captured, scanned data from a series of overlapping scans.
The registration engine, which uses technology developed by University College London’s Department of Electronic and Electrical Engineering, finds multiple features within each scan and auto-aligns the huge data assets.
Correvate estimates its cloud service is 60-80% faster than manual alignment and has a simple token-based system for processing data. You can read more about it in this AEC article from April 2020.
SLAM dunk
Correvate has now incorporated SLAM into its service, so AEC Magazine caught up with Correvate’s Charlie Cropp, a laser scan industry veteran, to find out more. “The first thing to say is that we’re not solving the SLAM algorithm. We’re leaving that to the likes of GeoSLAM, Paracosm and NavVis,” explains Cropp. “We’re just taking their processed point cloud, once it’s been captured and solved, and uploading the point cloud into our system to then align with other scanned data.
“We’ve seen a couple of big shift changes. The first is that people are deploying different arsenal. Firms who’ve traditionally always had a Leica or a Faro static scanner, are starting to run with GeoSLAM or Paracosm scanners and doing data capture to capture different levels of detail, different accuracy, tolerances, to match different project requirements.
“There is a realisation that they don’t need to be sending £50/60/70k pieces of kit to site when they could do so with a £15,000 to £20,000 solution. So that’s been a shift change in how the industry is working with SLAM data.
“Secondly, we are also seeing people actually use these devices in the same way they would a traditional scanner. So instead of having long, large linear scans that potentially have drift, they are truncating their capture and keeping that data section quite small.
“The challenge with doing that is they end up with lots of small sections — chunks of scan data which their hardware provider’s software can’t actually manage. They then have to look for an alternative software programme for processing, such as CloudCompare, which is less than ideal.
“We’re seeing firms producing ‘hybrid’ datasets; capturing core areas with a higher accuracy scanners and filling in other areas with a GeoSLAM (or equivalent SLAM) scanner.
“We get a lot of people coming to us with mobile data or the SLAM data captured from drones, handheld scanners, and they’re wanting to align them all together. Our core algorithm initially came out of the static scan world where the centre point, the zero point, was in the centre of the scan. With SLAM that centre point can be outside of the scan data and we would typically see that data fail. We’ve been able to enhance our algorithm and go from a 0% success rate to 100% success rate, enabling automated registration for SLAM data as well as static data.”
SLAM – Data trade-offs
SLAM has always been seen as ‘dirty’ or ‘noisy’ data as it’s far from clean and usually not colourised. Cropp shared her thoughts, “Laser scanning has always been a compromise. There’s always been trade-offs. Do you want data quality? Do you want speed of capture? How much data do you want? How much can you work with? And those three key elements are still relevant today.
“Looking at a GeoSLAM scanner, what actually are you trying to do with it? I get asked quite a lot ‘which scanner should I be buying?’ And I always say ‘ignore the hardware for the moment, start with the workflow’. Start by thinking, ‘what am I trying to do? What’s the purpose of scanning? What’s going to be 90% of what I do and capture, and why and what’s the deliverable I need?’ If you need to deliver to Autodesk Recap, work back from the deliverable and that will then dictate your hardware.”
It’s clear Correvate is seeing a change of attitude in scanning. While SLAM might not be as accurate as it would like, firms are weighing that up. Do they need to be as accurate as a Leica or as clean as a Z+F scanner and spend the £70/80k on each scanner? Or can they actually increase productivity using SLAM to do more work, while still achieving what they need from a deliverable perspective. If you can be four times more efficient or productive because you are able to capture or generate four times the number of projects, many firms are easily making that call.
5G potential
While scan registration in the cloud means firms get the benefit of large processing power, the other advantage would be having real-time registration fed live from the survey site.
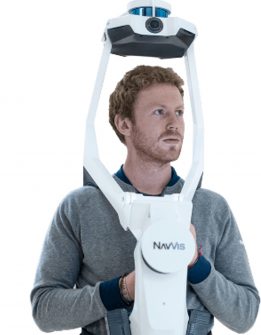
When we first met Correvate, 5G had yet to be rolled out and it was somewhat of an unknown. Now that 5G is starting to become available and phones are capable of submitting large amounts of data quickly, the reality of feeding Vercator from site is a possibility.
AEC Magazine asked Cropp if there had been any uptake of 5G. Cropp explained, “Not as yet. I think we will start to see a difference when there is actually a hardware shift. With something like the Z+F scanner, they have a tablet which can synchronise to the scanner. It essentially pushes out the scans complete from the hardware to the tablet.
“What we anticipate, and what we’d like to see a bit more adoption from the hardware vendors, is actually making that push out from the scanner to the tablet, and from the tablet to the cloud. If that starts to become commonplace, that will drive 5G use.
“There’s two things here. The first is getting data into the cloud in the first place, and the second is connecting the cloud to your downstream production.
If we can get data into the cloud more readily, and here there will be the naysayers saying ‘laser scans in the clouds, they’re too big’ but actually if we can send the data up in truncated chunks, almost without their knowledge, the data is in the cloud ready to work with. “If we can then connect that data to our algorithm, which actually knows the order of the scans, from the timestamps, you can plot that route and resolve the registration.
“The other thing that will be key for us will be the downstream connectors. If we can securely connect to Autodesk’s or Bentley’s cloud via APIs, we can start processing point cloud data that’s held there. That will also be another huge turning point in the market.”
Scan-to-BIM
At the moment Scan-to-BIM, where point clouds are automatically turned into building information models, is still a pipe dream. However, there are a number of companies working on trying to bring this to reality.
Correvate has declared that it intends to compete in that market. This is data alchemy, turning the dumbest data possible — 3D points — into intelligent walls, doors and windows.
Cropp told AEC Magazine that the company is aiming for its first beta in March, as in-house development resources scale up. To improve the quality of scan-to-BIM, it’s important to get as much data out of the scanner as possible. This requires access to APIs, colourised registrations etc. and some scanner companies are reluctant to give potential competitors deep access.
Correvate is vendor neutral but will work best with firms who are open with their developer communities. Some scanning firms are very defensive of their high-cost point cloud software. Registration is the start point, but the company intends to offer additional segmented offerings from deep analysis of identified components within a scan.
Conclusion
For a long time, we have been waiting for better price competition in the laser scan market. Faro was the first to bring out a highly portable scanner for around £20,000, then Leica brought out the £15,000 BLK360, but we have not seen a rush to commoditise professional point cloud capture.
While we are now starting to see LiDAR on phones and tablets, it’s a long way from the accuracy and density required for professional applications. For now, the market is adopting a hybrid approach and using the best technologies depending on need.
The SLAM market appears to be winning the productivity stakes and is carving its own niche. With Correvate’s Vercator cloud based services now being able to handle SLAM scans surely this will only accelerate that trend? AEC Magazine looks forward to seeing Correvate’s Scan-to-BIM technology later this year.