Greg Corke reports on the maturing partnership between Bentley and Topcon that aims to streamline engineering and construction through a connected data environment in the cloud
This time last year, Bentley and Topcon introduced the idea of ‘constructioneering’. While the phrase might not be everyone’s cup of tea, no one would contest the objective – to optimise the fragmented workflow between engineering design and construction. As it stands, data in digital engineering models is often lost, inefficiently recreated, or does not flow at all.
Speaking at Bentley’s Year in Infrastructure event in Singapore last month, Topcon CEO Ray O’Connor shared some shocking figures that highlight the construction industry’s inefficiency. Since 1945, he said, productivity increases in agriculture and manufacturing have been 1,500% and 760%, respectively. Construction, on the other hand, has only managed a miserly 6%. It’s obvious that something needs to change.
Construction is one of the largest manufacturing industries in the world, and the least automated, notes Murray Lodge, senior vice president and general manager of Topcon’s construction business unit.
O’Connor admits that when he first joined the industry, he could not understand why construction was not automated like factory operations. After all, it is just like CNC machining in a machine shop, he said, except that construction machines the face of the earth.
Embracing automation
Things are starting to change. Machine control automation is currently experiencing exponential growth. Five years ago, none of the major equipment manufacturers offered machine control for guiding construction machinery. Now, they all do. Price points have also dropped. However, O’Connor acknowledges that islands of automation like these are not going to address the broader efficiency challenges facing the industry.
“If we don’t get the engineering side and the construction side calibrated together, we won’t solve the entire workflow problem,” he said. “This is not about solving just one area of the process. This is about solving the entire process – and that’s why Bentley and Topcon have partnered in order to achieve that.”
“Constructioneering is when engineering and surveying and construction are continuous processes that are not handed off from one to the other,” added Bentley Systems CEO Greg Bentley.
Merging clouds
The foundation to the Bentley/Topcon partnership is the fluid exchange of information between design office and site, and vice versa.
To facilitate this, the companies have connected their cloud platforms – Bentley ProjectWise for engineering project delivery and Topcon Magnet Enterprise for construction contractors.
Once data is shared seamlessly in the cloud, information can then get fed down to the appropriate desktop or mobile application, whether that’s in the design office or on site.
Between them, the two companies have most bases covered for technology used on a typical construction project. Topcon focuses on surveying, on-site execution and the capture of as-built assets, while Bentley concentrates on engineering design, project information management and asset maintenance. This makes for a compelling story, outlined below in one possible workflow.
1) Capture the digital content of a construction site with a Topcon UAV (drone).
2) Use the Topcon Magnet Enterprise cloud service to bring that context, processed by Bentley’s ContextCapture software, into an engineering-ready reality mesh.
3) Use the mesh as the basis for the engineering design in Bentley OpenRoads Designer or OpenRail Designer.
4) Send the design model back through ProjectWise and Magnet Enterprise and turn it into a construction model.
5) Push the construction model out to a machine control system using Topcon Positioning devices for automatic grading.
6) Use the positioning device’s record of what was actually built to feed back into the Bentley ProjectWise or AssetWise engineering and asset management environment.
Historically, most of these workflows have not been automated, others have been dumbed down to go via paper drawings and some did not really exist at all. Even contractors that have invested in a machine control system may not initially have access to a 3D model, notes Lodge, which is needed for a machine to know where it is on site, and where the blade needs to move up and down to get to finished grade. Lodge describes a familiar construction industry workflow, where a contractor takes 2D engineering plans and then creates a 3D model. But this, he says, is not only slow, but introduces potential for errors, one of many that can happen in a fragmented workflow.
One area that is often overlooked is the accurate capture of as-built data. This could include documentation of everything on site from the exact location of a pipe, including how far below the surface it is, to the position of valves. “We could give that information to the owner because, at the end, if you know where everything is exactly, not where the plans say it is, but actually really what you’ve put into the ground, you can have so much information to help you lower the cost of maintaining the project over its lifecycle,” says Lodge.
As-built surveys have traditionally been costly and capturing this data with drones can dramatically increase efficiency. Bentley is exploring new ways to bring down costs further. Earlier this year, it carried out an R&D project where it attached some GoPro video cameras to an excavator to dynamically capture work carried out in a trench.
The resulting videos were fed into Bentley ContextCapture, which produced an accurate reality mesh showing the size and position of pipes, along with the surrounding manholes, drains and houses.
Looking to the future, the next obvious step is to apply Artificial Intelligence (machine learning) to automatically classify objects within the mesh (see ContextCapture article here).
Of course, reality capture can also be used throughout the project. Drones can be flown daily or weekly to collect data to monitor construction progress, then the resulting mesh analysed and compared against design data to check it is within the correct tolerance.
Real-time change
It’s a familiar scenario: an issue found on site halts work until a design change can be made. Having a fully digital, optimised workflow can help minimise this downtime as data can filter through to site very quickly.
For example, changes made to the design model in Bentley OpenRoads could be sent directly into the cabin of the grader operator, via Topcon’s Magnet Field and Sitelink 3D.
The driver will be notified that there is an update to the design, which can then be downloaded so that work can begin immediately. The blade on the excavator will simply adjust, according to the new grade.
Earthwork planning
Bentley and Topcon are looking to optimise a number of different workflows between design and construction, another being the scheduling and planning of earthworks. Model information created in Bentley ConceptStation, for example, can be fed through to Topcon DynaRoad.
DynaRoad can consume that data, then do some mass haul calculations associated with the project. It can help define the number and type of trucks needed, and optimise the movement of the material in relation to the design that has been passed on.
According to Bentley Systems’ Dave Body, this process can help reduce earthwork movement costs by anywhere from 7% to 10%. And when you are talking about a large greenfield project, where the earthwork costs alone can be in the region of $200 million to $300 million, the savings can be huge.
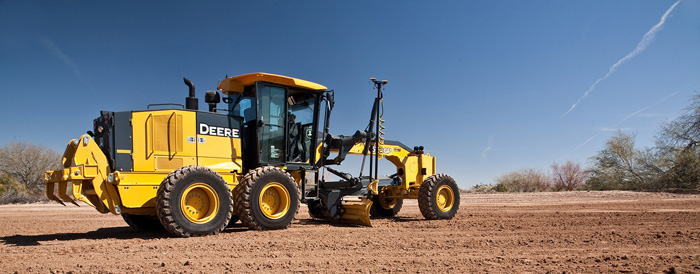
Education
Developing optimised workflows to help surveying, engineering and construction work together more seamlessly is one thing, but the effort is ultimately fruitless if the industry does not embrace them. The problem now is not the technology, admits Greg Bentley, it’s convincing a very conservative group of owners and engineers of the advantages.
“Low margins on projects mean it’s often difficult for companies to take the risk in investing in new technology,” adds John Foster, European business development manager for BIM at Topcon Europe Positioning. “Early adopters are helping to highlight the clear cost and time-saving benefits, which means more widespread adoption is now creeping into the industry.
“It’s a mindset change. All project stakeholders need to share in the risk and rewards of investing in new technologies and need to demonstrate and share the ROI stories within the industry.”
To help drive this much-needed change, Bentley and Topcon recently announced the Constructioneering Academy to provide opportunities for construction professionals to learn best practices in integrated engineering and construction.
Both companies have been proving out a number of constructioneering workflows on real construction projects over the last year. This has helped shape the ‘curriculum’, which will be implemented through existing learning centres located in Livermore, California (Topcon), Houston, Texas, and London, UK (Bentley). More academy locations will be opened in the coming months, including Pune, India; Dubai, UAE; and Beijing, China. Constructioneering Academy offerings will also be available online through universities with leading construction degree programs.
The Constructioneering Academy is not just about educating Topcon and Bentley customers. “[It] will not only teach people how to get the most out of both of our products, but will teach us about where the gaps are in order for us to solve the problem going forward and really create automation across every segment of the workflow for construction and design,” concludes O’Connor.
If you enjoyed this article, subscribe to AEC Magazine for FREE