Reusing the right drill-site design data has helped reduce oil field engineering costs by $2 million for ConocoPhillips Alaska Inc. (CPAI).
Located in the frozen tundra north of the Arctic Circle, AlaskaÝs North Slope oil fields produce 16 percent of the U.S. domestic oil supply and 90 percent of the StateÝs revenues. The No. 1 oil and gas producer in the State, ConocoPhillips Alaska Inc. (CPAI), invested about $1.6 billion in exploration, development, operations, and maintenance last year, including $750 million in capital projects.
To overcome the challenges of remote location, extreme climate, and complex regulatory environment on the North Slope, CPAI partners with specialist Alaskan oil-field service contractors such as VECO Alaska Inc. VECO became globally known in 1989 as prime contractor in the Exxon Valdez oil spill clean-up. Today, the contractor has more than 4,000 employees supporting the energy, resource, and process industries throughout the world, and generates annual revenues of $1 billion.
More than half of the VECO workforce is in Alaska, where engineers apply innovative technology to support CPAIÝs oil and gas production. From 2004 to 2005, VECO designed drilling sites for two new Alpine satellite oil fields – the Fiord oil field (CD3) to the north and the Nanuq oil field (CD4) to the south – which CPAI developed at a cost of more than $675 million. In 2005, CPAI challenged VECO to help reduce costs by reusing CD4 data for a new CD5 drill site at Alpine.
Reusing drill-site design and engineering data was conceptually possible, but it had not been done before within the CPAI managed environment. VECOÝs Design Technologies Group (DTG), lead by Mark Christenson, design techologies manager, worked out a process that not only saved time and money, but also preserved project knowledge about how to resolve drill-site design issues. In mid-2006, when CPAI discovered Qannik, a satellite development overlying the Alpine oil field, VECO again reused design data, making CD5 the design basis for Qannik.
Using a combination of AutoPlant and ProjectWise (in compliance with CPAIÝs managed environment), VECO manages and stores all 2D and 3D drawings, supporting designs, and project management documents in a central location with secure access. Document attributes entered via ProjectWise automatically propagate to the title blocks in AutoPlant documents, eliminating duplicate data entry and maintaining consistency between design and engineering. As documents progress through design, they are routed for review, attributes updated, and editing rights eventually restricted to select users. Individual components progress at their own pace, so projected completion dates are accurate and reliable.
ýVECO uses ProjectWise and the entire AutoPlant suite to produce cutting-edge designs,¯ said VECO project manager Steve Preston. ýRepeating these designs and reusing the data produces an estimated 20 to 30 percent cost reduction compared to Ùfrom-scratchÝ projects.¯
VECOÝs client, CPAI, monitors design progress by accessing project data through the ProjectWise Web portal. At specified milestones, VECO transmits deliverables to the client from the distribution server. ýProjectWise enables us to maintain positive control of documents without imposing undue restrictions on their accessibility,¯ Preston added.
Replicating intelligent data
Reusing drill-site data, however, is not a simple process of copying documents to a new project directory. VECO combines several Bentley technologies to produce ýintelligent data¯ that can be reused without losing linked information. For example, reusing the data requires successful linking of component tags across the Bentley applications, as well as changing tag numbers to reflect a new project.
{mospagebreak}
VECOÝs DTG supplements existing Bentley utilities with eight custom tools to streamline the process for copying project data. For each new project, these tools are used to rename batch files based on defined strings, update the internal drawing dictionary, update drawing reference paths, batch rename reference drawing file names, detach references that arenÝt required, batch update specification names for all model components, update model layer names based on new process lines, and clean up extraneous data.
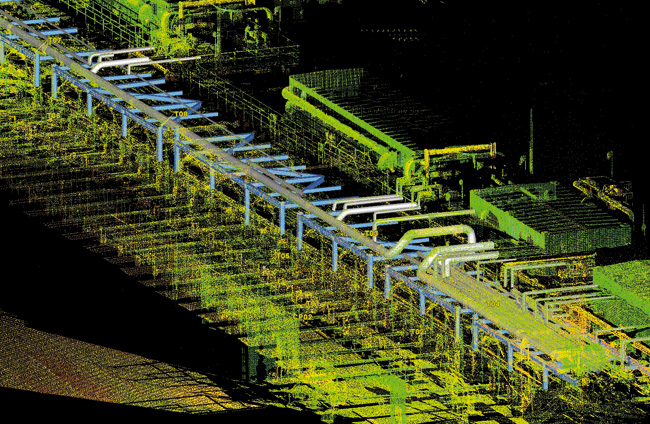
Reporting capabilities are also customized. For example, to produce instrumentation and wiring schematics, diagrams, and termination drawings, VECOÝs DTG has developed customized queries that capture real data within the drawing deliverables. When the data is reused, this eliminates hours of work associated with document production.
VECOÝs DTG also customized Bentley software to provide a way to generate a report on material requisitions and associated documents based on specific project attributes. The function spans multiple applications and enables users to export the report in nearly any format.
Over the 23-week project duration of the CD5 Project, VECOÝs DTG successfully copied and organized the drill-site designs using Bentley-supplied technology and adapted/developed supplemental tools as needed to complete the task. The result was a fully linked, ProjectWise-enabled AutoPLANT project delivered on time.
During this same time period, VECO performed retrofit design work for the Alpine oil fieldÝs CD2 pad. VECOÝs Laser Scanning Team traveled to Prudhoe Bay in August 2006 to gather as-built information using a state-of-the-art laser scanner and Bentley CloudWorx. The team captured highly accurate data for 600 linear feet of pipe rack and piping, as well as tie-in areas for future retrofitting. Scanner data imported into AutoPLANT became the basis for a 3D model of the retrofit design. A virtual walk-through not only eliminated interferences between new and existing equipment, but also avoided late-stage design objections by operations personnel.
ýUsing Bentley software enabled the team to find problems before they became major, saving both time and money,¯ Preston said. ýThe design team was able to realize improved quality of engineering information. Project productivity was also improved by the smarter use of shared information, shared documents, and reporting tools. Data integrity was improved by providing weekly reports.¯
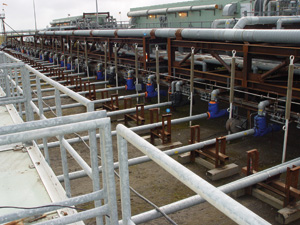
On projects totalling an estimated $250 million, VECO innovations have saved about $2 million and 23,000 man-hours. By successfully reusing existing drill-site designs for CD5 and Qannik, VECO reduced the forecast for peak staffing requirements at the execute phase to just 70 employees – about 35 fewer engineer team members than had been needed on the CD4 drill site.
ýMany of the design issues have already been resolved by the team that generated the previous drill-site design,¯ said project specialist Andy Toth. ýI look forward to further reducing costs through more effective use of the Bentley tools during execution of the CD5 and Qannik drill-site projects.¯
Oil production at these drill sites is expected to begin by late 2008. By then, CPAI will have invested nearly $500 million to develop the satellite sites at Alpine and increase oil production to 135,000 barrels per day, generating more revenue for the state of Alaska and supplying more domestic oil to meet U.S. demand.