Pick Everard, a multi-discipline architectural and engineering practice, looked to Océ to help streamline its document issuing and distribution process. Océ delivered a solution based around its Digital Distribution Manager and a document archive managed via Océ Doc Exec Pro.
Pick Everard is a leading multi-discipline architectural and engineering practice, based in Leicester. It was founded in 1866 and remains a private practice fully owned by the Partners. Their mission statement is ‘to exceed their clients’ expectations’ and they maintain this philosophy throughout the company to deliver high quality projects on-time and on-budget. The range of services offered runs from project identification and development through to design and on-site project management.
The firm has a turnover in excess of ¼ú14 million per annum, employs 250 people and is accredited with the Investors in People award, ISO9001 and ISO14001. “Our Partners and staff are our sales force and most of our commissions are repeat business from existing clients. We are the preferred consultants for several major client organisations and design and build contractors,” stated Jeff Denner, IT Manager. “We have a good reputation for delivering high quality designs and well managed projects. Our client list includes blue-chip organisations such as Severn Trent Water, the Prison Service, the Ministry of Defence, National Grid and the retailers, Sainsbury’s and Boots.”
The workflow
Pick Everard’s CAD Technicians use AutoCAD as their main design and drawing tool but also have access to a host of other project specific software. All drawings and checkprints are printed on an Océ high volume system.
Each commission is overseen by a Partner but day to day control rests with the Project Manager. One of their roles is to manage the drawing issue process and ensure the correct drawings are issued to the appropriate recipient at the right time. All drawings are checked and signed off by the Project Manager. A drawing issue sheet was completed in Excel and together with the signed off drawings passed to the printroom operator for reproduction. Drawings were then copied on the Océ high volume system and manually recorded for accounting purposes. This took a long time to process and when the printed drawings were returned to the project team they needed to be manually collated into the relevant issue sets. “This was a very labour intensive process, frequently on a Friday afternoon and it required forward planning. Often it was all hands on deck to meet the deadlines,” observed Jeff Denner.
" Océ DDM can handle a tremendous amount of work – it is at least three times faster than our old system "
“The use of email information by was becoming more common. It was difficult to track and record drawings issued electronically as it is easy to send an email with an AutoCAD drawing attached without following the correct procedure. Most people still want paper copies and ultimately someone has to print the document in order to make use of the information. That hasn’t changed but what has is who prints the drawings. For example some of our client’s contractors have printers on-site so they receive the information electronically and print it locally,” said Jeff Denner.
Pick Everard is ISO 9001 certified and has a quality assurance (QA) procedure for issuing drawings. This involved manual recording on standard forms and occasionally drawings were issued but not recorded. A master hard copy is kept of all issues. Security is often key for example when Pick Everard works with the Prison Service their drawings have to be stamped and signed before they are sent out. Pick Everard choose to keep documents for 20 years, so once the projects are complete the as-built drawings are scanned, saved as TIFF files and stored in a document archive.
The requirement
Pick Everard identified they needed a system that would handle all their document issues automatically and complement their current setup. “Océ products are very reliable and as we had already invested in a high volume Océ printer, we wanted a system that would integrate seamlessly with the existing equipment,” said Jeff Denner. “We have over 100 CAD stations and we needed a solution that required minimal manual intervention.” Pick Everard also needed a solution that suited their ISO 9001 QA procedure including keeping a copy of all back issues for audit purposes. “We had problems with the previous manual system. If a Project Manager requested an issue was sent electronically they had to rely on the CAD Technician to follow the correct procedure,” said Jeff Denner. “We needed something that was simple to use, yet totally reliable and auditable.”
The solution
Having reviewed the options Pick Everard decided to invest in Océ Digital Distribution Manager (DDM) to manage its document issuing process. Working in parallel with Océ DDM is an electronic document archive managed via Océ Doc Exec Pro. “The standard drawing issue sheet is reproduced by the Océ DDM system so the CAD Technicians and Project Managers are familiar with the format,” noted Jeff Denner.
The CAD Technician still prints a hard copy that is signed off by the Project Manager and this is kept in the job file as the quality record. Issued drawings are automatically saved through Océ DDM in the Océ Doc Exec Pro vault for issuing later and archiving purposes. Océ DDM is set up to read the AutoCAD title block attributes, so each file is correctly indexed as it converts the DWG file to a PDF. “The AutoCAD drawing is our intellectual data so we prefer not to issue drawings in live DWG format. We issue PDFs so they cannot be altered,” said Jeff Denner.
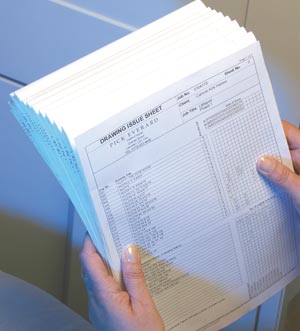
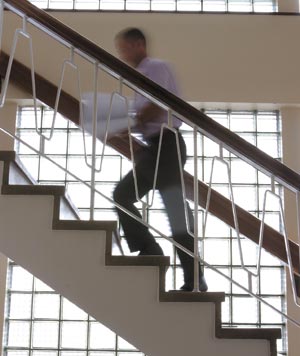
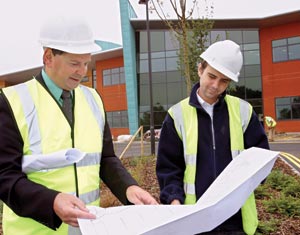
Once the PDF files are in the vault the issue can be prepared. The drawing issue sheet details, such as drawing number and drawing title, are automatically populated from the file properties of the PDF stored in the vault. The Project Manager can then view the drawings and check they are complete before they are issued. This is controlled by Océ Doc Exec Pro and has helped improve Pick Everard’s QA procedures. The firm has about 70 people using Océ DDM on a regular basis and has invested in concurrent licences. For accounting purposes an automated log of all printing is downloaded each month from Océ DDM and billed to the relevant projects.
“We have customised the issue sheet for some clients,” said Jeff Denner. “For example, for security reasons, the Prison Service signs the issue sheet and sends it back to us to confirm safe receipt, so we have customised their issue sheet to incorporate their needs. Printing via Oce DDM is much quicker and more reliable than manually feeding hard copy drawings. In addition, Océ DDM’s ability to collate the sets of drawings and keep record files creates a robust audit trail.”
Pick Everard’s use of Océ DDM has grown significantly over the past few years. In 2003 the firm distributed 117 drawing issues using Océ DDM. By 2004 this had grown to 2,843 and the 2005 estimate is approximately 4,000 drawing issues incorporating over 50,000 documents. “Without Océ DDM we would struggle to meet our deadlines and it would result in reduced productivity for our project teams,” stated Jeff Denner.
The benefit
Océ DDM automatically collates the drawing issue and prints a self-adhesive address label, so the drawings need simply be put into an envelope and the address label attached. This gives the CAD Technicians more time to concentrate on drawing work. Furthermore, Océ DDM always produces an issue sheet and stores it electronically, along with a copy of the drawings. “We know exactly what drawings we have issued and to whom. This process has given us much greater control as it is done automatically and is not subject to manual intervention,” noted Jeff Denner.
“We continue to print large quantities of drawings but in far less time. Océ DDM can handle a tremendous amount of work. The new solution is at least three times faster than our old system” said Jeff Denner. “The issue and distribution process on a typical project involving the production of 1,600 drawings would previously have taken up to three man days. Océ DDM has reduced this process to less than one day.”
Their productivity and turnaround time has improved and their costs have gone down. “Océ DDM has relieved the pressure on drawing issues. We are very pleased with the system and like to show it off to clients and other organisations. We have developed a set of FAQs that can be viewed by our staff through our intranet but generally we find it’s quick and easy to use,” remarked Jeff Denner.
Pick Everard also control the receipt and issue of third party drawings, which helps the firm comply with its QA procedures. Collaboration between Pick Everard and Océ has extended the functionality of Océ DDM. For example one of Pick Everard’s key clients, Sainsbury’s, insist all documents are uploaded to the extranet site Business Information Warehouse (BIW), so Océ developed an automatic upload feature to transmit directly to internet based portals.
“Océ are one of the most professional suppliers I have dealt with. The equipment is very reliable and even when it needs a service call the support structure is excellent. It has increased our efficiency and was certainly worth the money,” observed Jeff Denner. “Our mission is to exceed our clients’ expectations and it’s satisfying when one of our suppliers exceeds ours! I wouldn’t hesitate to recommend Océ solutions.”