In order to bring to life its vision for Rathbone Square, Great Portland Estates adopted BIM from the start, working with BIM Technologies to deliver a digital built asset before on-site construction even began
In the heart of Fitzrovia, a lively area of London’s West End, Rathbone Square is a mixed-use development of office space, retail outlets and 142 residential apartments, located around a new garden square – the first to be created in central London for some 100 years.
The £215 million redevelopment of this area by Great Portland Estates (GPE) began back in 2011. Recognising early on that it would need innovative technology to bring its vision to reality, GPE decided to use BIM in the project as way to minimise costs and reduce risk.
It appointed a team from BIM Technologies to act as information managers and BIM coordinators for the project, with a remit to educate and convince the supply chain of the benefits of BIM, given this was a not-so-commonly used approach at that time.
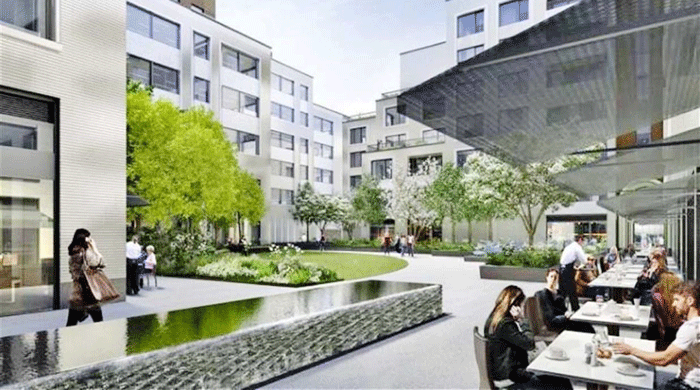
Digitising the supply chain
Digitising the construction supply chain meant that the project would be delivered in digital built asset form, prior to on-site construction. In this way, the entire supply chain would have the tools needed to successfully deliver the final physical built asset.
Clearly defined BIM requirements and roles were set and appointed via the EIR [Employer’s Information Requirements], together with detail and definition for the project models. These models then became essential drivers in decision-making at key stages of the project. That, in turn, resulted in a sustainable building with significantly reduced waste and whole lifecycle cost.
Initially, the architect, structural engineer and M&E engineer were all using a different platform. It was therefore essential to bring all of that information together in a single, federated model. Engaging with BIM at the initiation stage meant that a common data environment could be created to share project information between supply chain members. GPE also made a commitment from the outset to commissioning. So five years ahead of completion, the commissioning engineer was already involved. Again, this was almost unheard of at that time.
The company appointed Lend Lease to carry out the pre-contract service agreement. The Lend Lease team made improvements to its procurement protocols and supply chain engagement, leading to improved procurement processes using 3D and 4D BIM information during the tender process. Other benefits of this included more efficient and collaborative design and construction methods; collaborative planning using 4D BIM and P6; and enhanced soft landings.
BIM Technologies, Lend Lease and GPE also embraced a digital built asset vision on this project, supported by their ‘Digitising the Supply Chain’ initiative, which made BIM deliverables and processes mandatory parts of the design, delivery and handover processes. In this way, continuity was a commitment made by the entire team, from client to design team, through to the trades and commissioning. The BIM Technologies issue management platform Warboard was introduced to monitor coordination, giving the design development team a clear dashboard and encouraging openness. Solely for this project, BIM Technologies created a cloud-based Warboard app, giving instant access from any location to real-time project information.
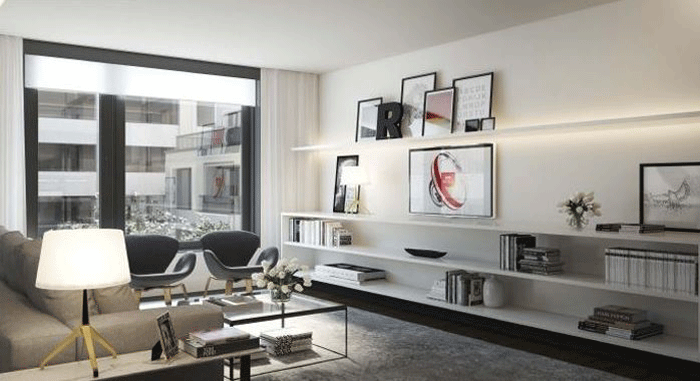
Issue management
Quality was critical for this project, which includes high-end residential properties. A digital model of the apartments allowed prototyping in advance of construction to ensure all details were correct and delivered to the required standard. This effectively enabled the team to view the apartments in a virtual environment before they were built, removing opportunities for error.
Over 350 models were created for this project and it was essential to avoid clashes and to reduce the need for rework. That’s why the dedicated BIM team led by BIM Technologies set up camp in a single office at GPE to work together to develop the design. This space was to become the core BIM area, with large screens to help in interrogating the models and allowing Lend Lease to carry out detailed coordination with all of the trades throughout the build. By the end of stage 4, all of the models were coordinated without a single issue or clash.
To add to the complexity of the project, the site is located in a very busy area of London, with many infrastructure elements needing to be taken into consideration, including the London Underground station and Crossrail development at Tottenham Court Road and a postal train route that runs directly under Rathbone Square. This meant that the civil model and survey data needed to be federated with the building structure to ensure appropriate interfaces were used.
Looking to the future Ultimately, the driving force behind this project was the connected workforce, united through commitment, collaboration and project understanding down to the most finite detail, but totally visible through the asset model.
By integrating digital construction methods at all stages of the build, the result is a beautifully apportioned space, reckons Adam Ward, technology director at BIM Technologies. “Rathbone Square is a game changer for the construction industry. Despite its complex design structure, its facade portrays a cool simplicity that is to be admired,” he says. “It has a seamless connection with its urban environment, which will ensure its longevity as part of London’s enviable cityscape.”
Others clearly agree: social media giant Facebook, for example, has taken up residence in the office space, making Rathbone Square its London HQ.
“I am immensely proud of what GPE and our supply chain have achieved at Rathbone Square,” says James Pellatt, head of projects at GPE. “It demonstrates the sophistication of the whole project team, resulting in a highly desirable space to live and work.”
“We have delivered not only a sustainable building by significantly reducing waste and whole lifecycle cost, but also the digital built model delivered prior to the physical built asset has led to enhanced soft landings and will simplify future use,” he concludes.
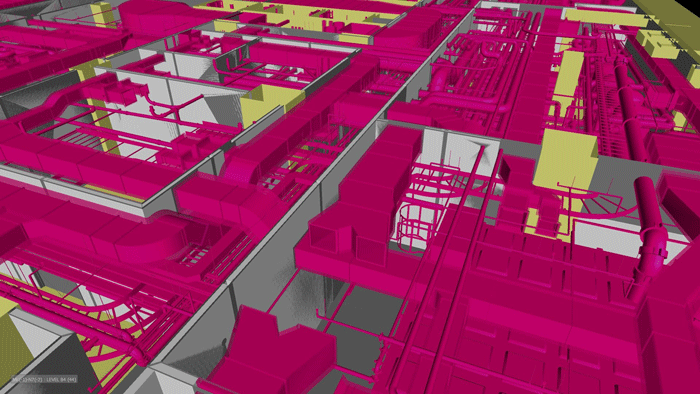
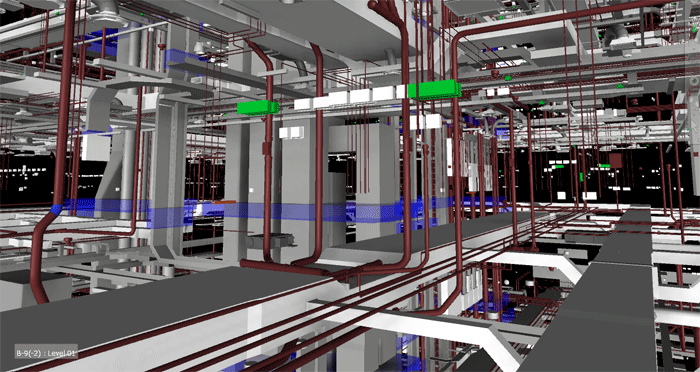
If you enjoyed this article, subscribe to AEC Magazine for FREE