Engineering design consultancy Wentworth House Partnership (WHP) used advanced structural software on a complex London re-development where a 20th Century building’s historic facade needed to be retained while the internal structure was replaced
The Knightsbridge Estate is a £150m re-development project in the heart of London’s prestigious shopping district. Designed by Fletcher Priest Architects, the 340,000 square ft project is set to restore and invigorate the premium city block. When complete, the development will deliver a mix of high-end retail, contemporary office spaces and 35 luxury apartments, all arranged around a courtyard garden, as well as a stunning rooftop restaurant, complete with panoramic views of the city.
The project is located within the Hans Town Conservation Area so the exisiting building’s impressive 20th Century façade had to be retained.
The architectural ambition of restoring the façade to its former glory presented a major challenge as the internal structures needed to be demolished to make way for the new development. There was also the added difficulty of coordinating the temporary structure around the existing street level services and London Underground assets, located beneath the site.
Due to the complex nature of the project and the numerous site constraints, the Wentworth House Partnership (WHP), an engineering design consultancy, used Tekla Structural Designer to design and detail the façade retention scheme.
“[The software] allows us to model complex geometry for façade retention, saving valuable time on site and producing a more accurate analysis when compared to using a 2D method,” explains Stuart Vaughan, director of Wentworth House Partnership. “We have also recently combined Tekla Structural Designer with Tekla Structures to enable us to produce coordinated construction information and fabrication drawings.”
Working in 3D has proven to be vastly more effective than 2D, making it easier to produce complex, layered framework designs, allowing for clash detection and reducing the amount of re-work required on site.
“The Knightsbridge Estate project presented many challenges, such as the site location and sheer size of the façade,” adds Vaughan. “For example, the structural arrangement and pavement conditions around the perimeter of the site meant that there were at least six different framing arrangements required. However, considering the size and continuity of the façade, with the whole site covering an area of 3.5 acres, the retention frames couldn’t be considered in isolation and therefore it was important that the modelling software included them all in its calculations, which Tekla Structural Designer was able to do.”
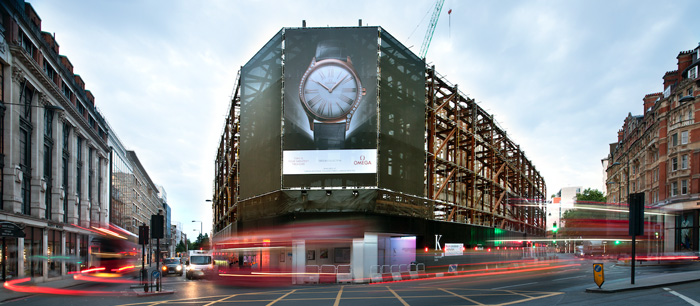
Going underground
Being in the centre of one of London’s busiest shopping districts and adjacent to London Underground assets, with Knightsbridge Underground station included within the planned re-development works, the location was an added difficulty for WHP to consider.
“Due to the height of the façade, the retention scheme had to penetrate through the pavement,” says Vaughan. “However, considering the site’s proximity to the London Underground services we were restricted in terms of workable design solutions – for example, we were unable to pile in proximity to the live London Underground assets. In addition, we also had to design the load transfer structures around the street level services, ensuring that they were considered within the model too.
“We relied on Tekla Structural Designer extensively, as it was critical that the transfer systems were designed in a way that meant the load path was viable, while at the same time avoiding the extensive live services. Tekla Structural Designer enabled us to produce a detailed analysis and design of the retention structure, taking all of these factors into account.”
Minimising movement
Another issue faced by structural engineers when designing a façade retention scheme of this scale is deflection, as too little stiffness could result in the excessive movement of frames, and consequently even structural damage to the façade itself – a serious concern when the building is located in a busy London shopping district and falls within a conservation area.
“The design for this project was deflection critical, meaning that the deflection of horizontal trusses, vertical frames and transfer systems had to all be considered,” says Vaughan. “Thankfully Tekla Structural Designer was able to model and analyse all of these conditions, enabling us to consider the 3D frame effects of the retention scheme, rather than relying on a simple 2D analysis. Working in 3D, we were also able to optimise the weight of the retention structure, reducing the amount of steelwork required and saving both time and money.”
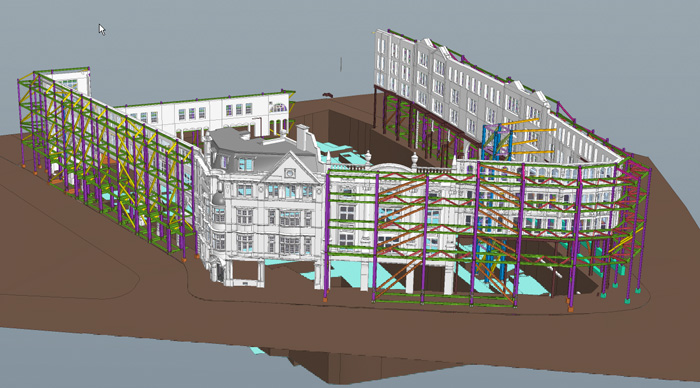
Clash detection
One of the well-documented benefits of BIM and Tekla Software is its automatic clash detection. Rather than hand-drawn 2D drawings where clashes could pass undetected until construction had begun, resulting in costly re-work and delays, 3D modelling can alert engineers to clashes at the design stage, helping mitigate errors and streamline the design process.
As well as considering clashes within the retention structure itself, the retention steelwork on the Knightsbridge Estate project also had to be precisely coordinated with the existing building façade.
“For façade retention, ensuring coordination between the existing and the temporary structure is absolutely imperative,” explains Vaughan. “However, this can prove difficult, as many of the retention scheme connections are unique and will involve the design of non-standard elements and supports. It is therefore critical that they are correctly understood by the modelling software when detailing.
“Fortunately, Tekla Structural Designer was able to analyse the steel frame and load paths while also ensuring positional coordination with the existing façade, reducing the risk of clashes or need for re-work on site.”
Furthermore, WHP was able to easily update and analyse the model whenever changes were required by the client, both during and after the design process, ensuring that the overall structural system wasn’t compromised by any such changes.
Tekla Structures was also used on the project, with information easily coordinated and transferred between the structural BIM tool and Tekla Structural Designer. This compatibility enabled WHP to prepare fabrication drawings in Tekla Structures using data generated by Tekla Structural Designer, ensuring that the steel connections used in the retention scheme would be accurately manufactured in accordance with the design and eliminated the approval cycle that would have occurred had the fabricator prepared the drawings.
“Using Tekla Structural Designer and 3D modelling helped us overcome the numerous challenges and constraints that this prestigious project presented,” concludes Vaughan. “It helped us accurately and precisely analyse highly complex and variable frame, ensuring viable load paths in a complex location whilst also minimising weight and ensuring coordination with the existing façade.”
If you enjoyed this article, subscribe to our email newsletter or print / PDF magazine for FREE