Understanding and communicating the form of one of the world’s most complex building designs was a tricky task. Stephen Holmes looks at how Killa Design used 3D printing to breakdown the intricacies of Dubai’s Museum of the Future
Dubai’s Museum of the Future is one of the most complex structures ever built. Its curved exterior and steel skeleton make it almost impossible for some to comprehend. Standing at 78 metres high and with barely a straight line in sight, its elliptical design has turned it into a landmark design in a city not short of adventurous architecture.
Primarily an exhibition space, which will showcase innovative and futuristic concepts, the building was designed by architects Killa Design.
Its futuristic torus-shaped structure won the design competition for the building in 2015, with its unique shape and column-free interior space attracting the attention of the judges.
Concrete in structure from its basement levels to the top, 1,024 exterior panels are supported by a steel diagrid structure — a framework of 2,400 intersecting steel members — with composite concrete floor slabs.
“Frankly, the floor plates are the only thing that are flat in the entire building,” says Shaun Killa, design partner at Killa Design. “Everything else is curvaceous, the overall form is parametrically designed.”
The creation was voted ‘Most Complex Building in Construction’ earlier this year so that explains why Killa’s team turned to 3D printing to help explain the build.
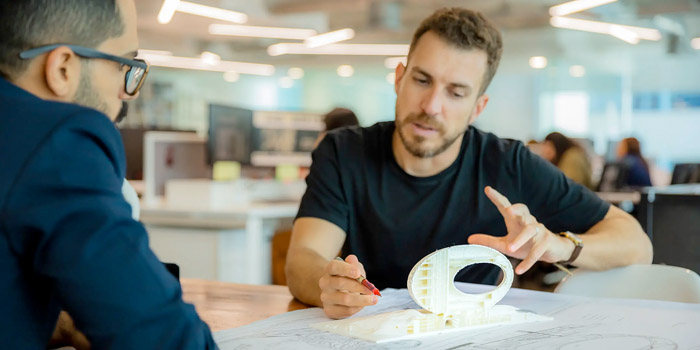
The team used a number of in-house Ultimaker S5 3D printers to create models to give contractors, manufacturers, and government review engineers a complete understanding of the building before construction began.
Killa, said: “3D printing helps us to present and explain ideas during creative brainstorming sessions, and significantly speeds up the design process.
“For challenging and organic designs, like the Museum of the Future… we find traditional methods of model-making inefficient and sometimes unworkable.”
The Ultimaker S5 is a desktop FDM 3D printer. It has a build volume of 330 x 240 x 300 mm and the benefit of dual material extruders.
With one nozzle outputting a PVA support material, it can build models with sharp overhangs and gradients, such as the Museum’s elliptical shape, with the support material simply dissolved with water once the part has finished printing, leaving the PLA or ABS plastic structure.
The S5 has also added simplicity with 24/7 automated material handling and filament humidity control, as well as efficient air filtration with its Pro variant – creating an ideal package for an office-based 3D printer.
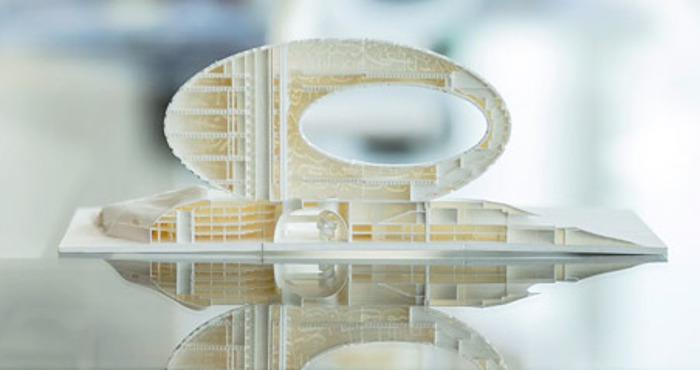
With so many complex shapes to work with, the design team needed as much help as possible.
Tommaso Calistri, architect at Killa Design, said: “You need your brain to work in a complete three-dimensional environment – as much as your brain can be good, you have some limitations, and that’s why we had to have some external tools. In that case our 3D printer was extremely helpful.”
In addition to the exterior shape, the company printed cutaway models to show the relationships between the building’s core steel structure and concrete panelled exterior.
While FDM 3D printers are not renowned for their ability to print in fine detail, the output of the Ultimaker S5 allowed for detailed cross sections showing the individual steel girders, interior and exterior cladding, and slab flooring – right down to the individual coupling methods.
3D printed segments were used to provide a clear insight into the museum’s interior space arrangement and, more surprisingly, the printed model of the museum also helped to create a cleaning strategy for its façade.
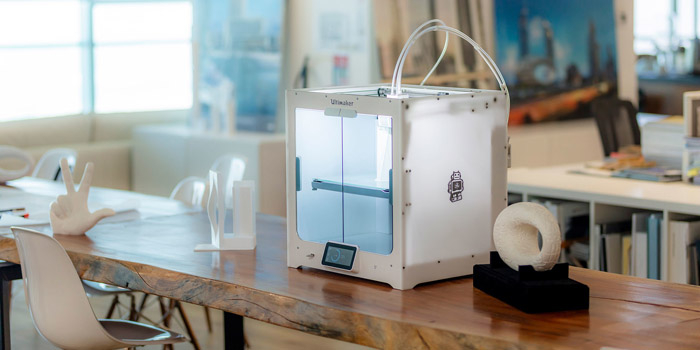
The outside of the structure is decorated with phrases written by Dubai’s ruler Sheikh Mohammed Bin Rashid Al Maktoum in giant Arabic calligraphy, with the script creating the form of the building’s windows which, with the help of 14km of LED lighting, also create a night-time spectacle.
By being able to sit down around 3D printed scale models, specialist maintenance staff were able to plan how each element would be accessed by ropes for cleaning and future repairs.
By allowing such quick access to 3D printed models for all manner of stakeholders involved in a project, Killa is adamant that in future the practice will be able to push building designs to even more ambitious levels.

“With Ultimaker we have innovated our process of design and we are confident the technology will help us to coordinate problems much clearer and faster, allowing us to create even more complex buildings in the end,” he said.
■ killadesign.com ■ ultimaker.com
If you enjoyed this article, subscribe to our email newsletter or print / PDF magazine for FREE