Ogle Models and Prototypes has built up a strong client base in the automotive and consumer products sectors. The company is now applying its model making expertise to the architectural field to great effect.
As children we played with Lego, hoping to create that great masterpiece. And for those who accomplished such a feat there was a great feeling of satisfaction. These models may not be the real thing, but the sheer simplicity in even the largest construction, is mesmerising and eye catching. But as times are changing, so are the ways to create these captivating models.
Developing scale architectural models used to take weeks, if not months, hand crafting every detail. But as technology has improved, so has the efficiency of model making. It has advanced so far, that now an architectural model can be created in a matter of days. The technology that is currently used to do this is rapid prototyping. It allows a model to be produced directly from 3D CAD data.
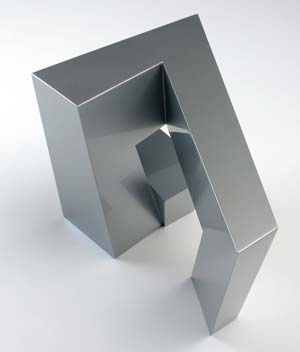
Rapid prototyping includes a group of technologies, which are used to create models in a short space of time. These technologies include Selective Laser Sintering (SLS) and Stereolithography (SLA).
Model making technology
As time becomes more of a cost, architectural businesses, like other product design companies, need models, produced quickly, but without sacrificing quality. Ogle Models and Prototypes is an experienced practitioner in this industry and technology.
Over the years, Ogle has created stunning models for companies, such as Bentley, Jaguar, Electrolux, Kraft and many others. So when Zaha Hadid and her architects needed high quality models of their architectural designs for Dubai produced, they didnÝt need to look far.
In order to create the building models required, Ogle focused on the SLA process; this is also known as 3D layering or 3D printing. It allows you to create solid, plastic, three-dimensional objects from CAD drawings in a matter of hours (depending on part sizes and finishes required).
The basic process involves creating a 3D model of the object in a CAD program, for example SolidWorks, and then exporting the model as an STL file. This is where Ogle takes over. A software program called Lightyear slices the drawing into layers as thin as 0.05mm and the model is prepared, so that the SLA machine knows how to build it and get the best of the features.
{mospagebreak}
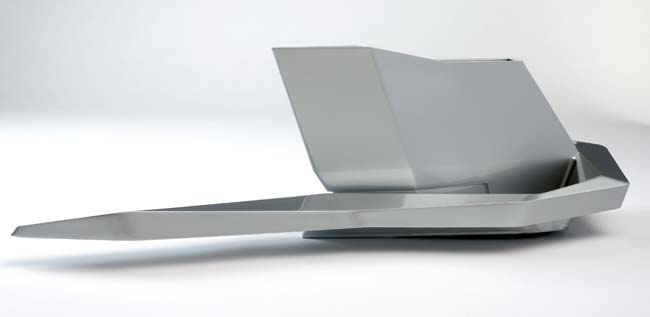
The SLAÝs laser then creates one layer at a time by exposing liquid photopolymer and hardening it. This process continues to build layers up until the model is complete.
For very complex models that require a bit more strength and where surface finish is not as important, the SLS process can be used. This uses an Argon laser to draw parts one slice at a time, onto finely powdered nylon 12, whilst melting the layers together (sintering) to form a solid component.
Because the process is fully self supporting, it allows for parts to be built within other parts, with complex geometry that simply could not be made any other way.
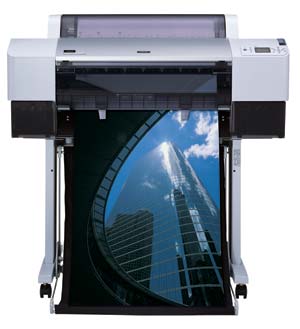
More than just technology
So what is OgleÝs role in this process? Ogle ensures that all the models are orientated in the most effective way; corners are never cut. And for the perfect finish Ogle has a purpose built paint and finishing department, which hand finishes and refines all of the models. Trained and experienced model makers will spend time rubbing away the layers that build up in the machines, to ensure models are 100% accurate. Finally, in order to retain the ultimate design precision and quality, Ogle also has a range of finishes it can use; this includes colour and texture, which can be added.
The deciding factors
Using technology over traditional model making methods is a cost effective solution. And whether you have an architectural model that requires intricate detail or smooth and slender lines the time taken to produce model masterpieces is significantly reduced. However, just because itÝs fast, it doesnÝt mean itÝs any less impressive. The cost of producing models using this technology varies, depending on the size, amount of surface finishing, different textures or painting required and the time frame in which they need to be completed. But because Ogle has all the machinery and expertise in house there is no extra expense or time incurred for outsourcing jobs. Top architectural firms, such as Zaha Hadid have identified the rewards of using Ogle and its rapid prototyping technology for its model making requirements. And as the industry moves forward, it is only a matter of time before more firms start to take advantage of this innovative technology too.