Argyle Asia puts to the test a new ‘perimeter scan’ flight mode in the 3DR commercial drone platform, in order to capture side-on details of building facades for an as-built survey
Drones have become essential tools in many construction projects – but when it comes to conducting as-built surveys, results can sometimes fall short of expectations.
The reason for this is simple. Drones are generally very good at capturing imagery and data from above, but not always from the side. Surveying a groomed site for pre-construction, for example, is a far easier task for a drone to accomplish than trying to capture side-on views of taller, finished structures, which involves a more complex flight, at a range of different altitudes and using a variety of different gimbal angles to ensure accuracy.
With a new perimeter scan flight mode, drone software specialist 3DR claims to have cracked the problem. This perimeter scan mode is part of 3DR’s wider Site Scan commercial drone software platform and enables automated scans of vertical structures. It is already being used by 3DR customer Argyle Asia, a Southeast Asia-based firm, which specialises in real estate investment, property and infrastructure development, and design and construction delivery.
Site test
Argyle has used Perimeter Scan to perform an as-built survey on a group of mixed-used buildings in Kuala Lumpur, saving significant time on site and creating a BIM-ready deliverable into the bargain. The goal was to fast-track the collection of as-built data that could be used in design development, since the client had limited historical records and few architectural drawings relating to the site.
The site itself presented a number of challenges. It was densely populated, with large trees in close proximity to the buildings, making it difficult to capture survey points from the ground. The architectural features and alignment of the buildings would require additional survey time. Disruption to commercial and residential tenants was also a consideration, “in addition to the operational safety risks of a manual survey,” says James Hadden, director of property development and construction management services at Argyle.
Capturing the site with a drone, by contrast, looked like a great way to proceed – but the firm needed a drone that would make it possible to capture building facades without any gaps in data or major inaccuracies.
Argyle decided to use the new perimeter scan flight mode on Site Scan in order to capture the property and create a photorealistic model. Hadden set five survey control points to lock in the survey data with the orthomosaic and point cloud, and then performed the flight. “In terms of workflow, it took minutes to set up the UAV and run the survey. It was fast, reliable, efficient and the registration of the scan was great,” he says.
As mentioned, it was to vital for Argyle to capture parts of the building that might have been difficult to capture at ground level. Says Hadden: “The drone worked well with getting into the confined spaces that I didn’t think would be possible to capture. It picked up faces on the building that I thought would be obscured by the trees or the shadows.”
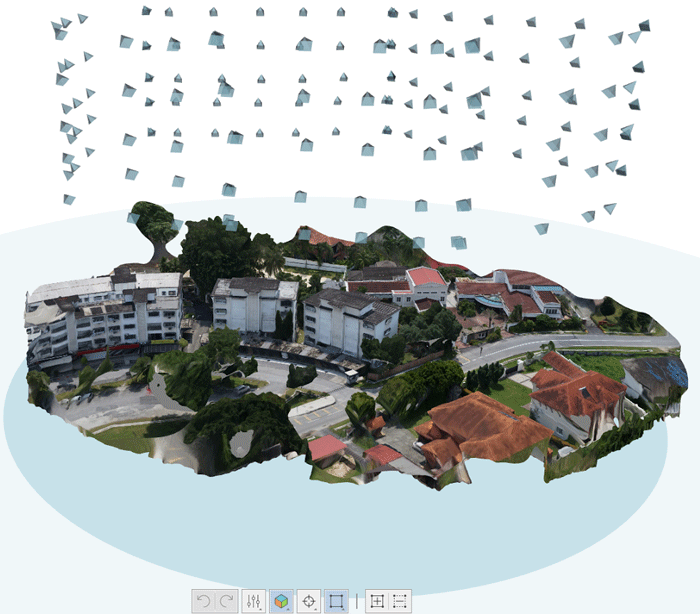
From seven weeks to ten days
From the data collected by the drone, Hadden was able to create rich 3D point cloud and meshes, use them to identify infrastructure features of the buildings, and then incorporate them into 3D models for BIM integration. Within hours of the survey’s completion, says Hadden, he was ready to register the scans and start to model and take sections.
“With the point cloud tools in Revit, I could take sections of the building, establish the profiles and start drawing perimeter walls and detailing windows,” he says.
The time saved and the need for less manpower on site to conduct a survey, he says, have been the biggest benefits of using a drone in perimeter scan mode. A traditional as-built survey for this project might have taken three to four weeks with additional manpower, he reckons. From there, another two to three weeks might be needed to interpret the survey notes and prepare the CAD as-built survey and Revit model. In total, that’s around seven weeks from conducting the survey to delivering the Revit and AutoCAD drawings.
By collecting as-built survey data by drone, Argyle is now in a position to provide these deliverables far faster. In this project, Hadden says, it took less than three days to scan the site, process the data into a geotagged orthomosaic and point cloud, and convert them into CAD-friendly files. “Then, about a week later, we finished the georeferenced CAD and Revit drawings, taking a total of ten days,” he adds.
From seven weeks to ten days is a big time saving and Hadden is already looking to achieve similar efficiencies in other projects across Asia, he says. The ability to autonomously scan vertical structures at this level of detail has a real value to him. “I look forward to continuing on even bigger, more complex projects in the future,” he says.
■ 3dr.com
If you enjoyed this article, subscribe to AEC Magazine for FREE