At Newcastle University, new student accommodation is taking shape fast, thanks to prefabricated pods manufactured off site, software-supported collaboration and a scholarly adherence to BIM Level 2 standards
Set to open in September 2018 in time for the start of the new academic year, the Park View student village will deliver 1,277 muchneeded en-suite study bedrooms for students at Newcastle University, in a complex project costing around £68 million.
The development is part of the university’s wider growth strategy to provide high-quality accommodation for incoming students, from both the UK and overseas. As the main contractor, Galliford Try made a decision from the outset to deliver Park View as a fully integrated BIM Level 2 project. It was also decided that a team from BIM Technologies would be engaged to provide information management services, with the goal of helping the project to hit targets and save on time and costs.
What’s interesting about the Park View student village is that the bulk of the development involves containerised ‘modules’, manufactured offsite.
So from the start of the project, the team from BIM Technologies focused on working closely with all stakeholders to ensure that the design, delivery and installation onsite of these modules was as smooth as possible.
The new student village comprises six individual accommodation blocks, all made up of module ‘pods’, which began arriving onsite in the spring of 2017. The modules are manufactured by the Chinese company CIMC Modular Building Systems (CIMC MBS); its factory in China was previously visited by members of the project team and key stakeholders from the university to ensure that bespoke design requirements of Park View were incorporated. The modules arrive onsite fully finished to the design spec of Space Architects.
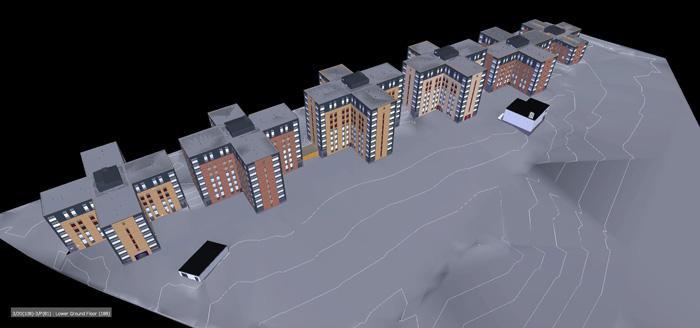
BIM Level 2 requirements
Because the project was to be delivered to BIM Level 2 standards, 3D geometrical and non-graphical data were a feature of the design phase onwards – but the team went further still, incorporating the latest developments in Virtual Reality and Augmented Reality into their workflow. These were used to communicate the design to stakeholders, giving them a feel for how the space inside these pods would work for students and providing opportunities for tweaks to the design before work got started onsite.
The team from BIM Technologies, meanwhile, had three main roles on the project: First, to create the BIM documentation including the BIM execution plan for Park View; second, to collaborate with all project team members to complete the 3D coordination, get geometry up to date and translate all data into the models; and third, to run coordination meetings and complete information exchanges.
“It was essential to set clear goals early in the project, to ensure sound understanding of the BIM requirements from all members of the project team,” says Claire Thornton, information manager at BIM Technologies. “Only by delivering on all of these objectives could we be sure that we would complete all of the client requirements at handover.”
In a further demonstration of commitment to the project and Level 2 BIM standards, Newcastle University engaged the services of the BIM Academy (Galliford Try’s client-side BIM manager) to act as BIM assurance manager, conducting audits and reporting back to the university on the progress of the project.
These audits are an extremely helpful part of the process in terms of maintaining the client’s trust, says Thornton. “The audits include all information exchanges, usually concerning data such as the geometry details, at the end of each stage of the project. We have ensured that all of the models and geometry are now fully coordinated and available to all project team members – successful collaboration has been essential on a project of this size.”
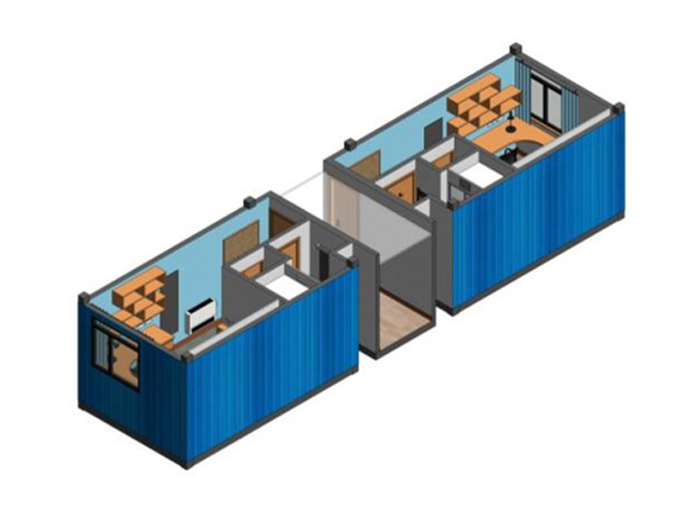
Benefits of BCF
Throughout the project, BIM Technologies used Revit software and the design management system Warboard, a cloud-based platform which manages issues in a federated model, for collaboration and communication across the project team. The use of Warboard has enabled the team to manage issues found in the model from a common source and set a course for resolution, while also tracking outstanding issues from previous reviews.
Warboard has recently undergone some fairly big improvements, according to Thornton, including a newly built interface, multiple new project management capabilities and advanced expandable clash results for customised reporting. Plus, there are the improvements in the open BIM Collaboration Format (BCF) to consider. “We can now punch the BCF format into and out of Warboard using Revit,” she says. “Essentially this means you can use Warboard to find and resolve an issue and solve it, there and then.”
The main advantage of BCF is that you can take the issue back into the authoring software; in this case, Warboard. This tends to mean that issues get dealt with immediately. By contrast, with Navisworks – typically the most popular software for viewing models and issues – you’re simply viewing the issue , rather than taking action. The BCF in Warboard also works with Solibri, providing more choice for the user.
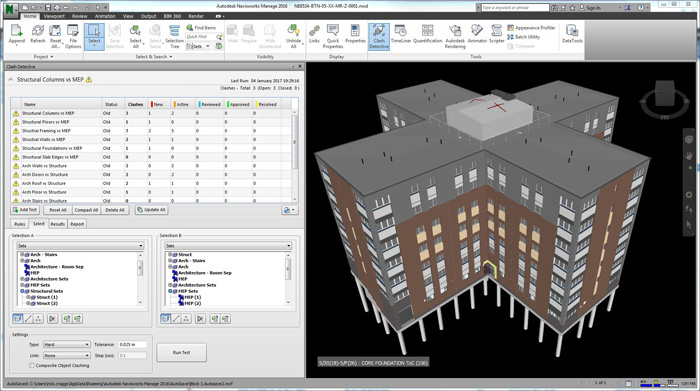
Thornton says that, in most of her projects, she uses some sort of Autodesk software, for compatibility. Those projects that don’t use Autodesk, she adds, “will likely use things like specialist structural manufacturers, where they can export an IFC from their software. Most software will export an IFC, but it has its problems, in that sometimes the data can be lost. Encouragingly though, the format is in constant development.”
Collaboration for delivery
At Park View, using Warboard allowed the entire team to have one place to go to address issues on the project, streamlining communication, rather than attempting to communicate view screenshots sent over email.
The reporting function in Warboard means users can assign clashes and issues to specific team members, and at any time, see how many clashes are assigned to a particular person. In this way, it’s clear who is responsible for rectifying and issue. “The reports we generate for our client are delivered in a simple format and the feedback we’ve had is that they appreciate the simplicity,” says Thornton. And since the pod manufacturer CIMC is based in China, this simplicity has helped the issues raised by the language barrier and the impossibility of holding regular face-to-face meetings to work things out.
As this project nears completion, those involved can assess and review the technical processes of managing the build, the data, the supply chain and onsite deliverables against the as-built model, says Thornton. “Using Warboard has made the process easier, along with the management of issue detection and resolution, and the collaboration with our client has been incredible.”
Warboard steers that collaboration, she adds, “the results of which will be clear when students are happily in their new, purpose-built accommodation.”
■ bimtechnologies.co.uk ■ warboard.co.uk
If you enjoyed this article, subscribe to AEC Magazine for FREE