Rebar and steel modelling software from Graitec and an accurate 3D model ensured key elements of the Saadiyat bridge project met tight deadlines without a hitch.
Fundamental to the UAE’s ambitious plans for the development of a new urban community on Saadiyat Island, a previously under-utilised region off the coast of Abu Dhabi, is the new 1.5km bridge that links the island to the rest of the capital.
Fittingly, for an island set to blend culture, business and tourism, the bridge is both elegant and functional, combining undoubted style with impressive scale. Its box beam construction provides for ten road lanes and two railway lines, while its three parallel pre-stressed concrete box beam elements amount to some 60 metres in width, making it one of the widest bridges in the world. The bridge opened last year after three years in construction, with both the development and the construction owing much to the smart use of sophisticated modelling technology.
Concrete evidence
Concrete specialist GDS was brought in to provide detailing expertise after a previous contractor was unable to meet project requirements. With a tight deadline, and some particular challenges thrown up by the bridge’s geometry, GDS needed to be sure that it had the right methodology and technology in place.
Geometric accuracy is vital in designing reinforcements for complex structures, a fact not always appreciated at a project’s initial design stage, and therefore rarely reflected in the CAD applications used. “Many highway design packages may give you the basic shape but the overall breakdown of the structure for finite details will often need to be completed manually,” says Dave Vout, a bridge engineer at GDS. “In this project we recreated the entire structural geometry using AutoCAD, a necessary stage before we could even think about the make-up of the concrete sections.”
Having created the bridge geometry in a CAD environment, GDS needed a software tool that would enable the rapid generation of rebar detailing. Here, again, some commonly used tools were simply not up to the job. “Most rebar modelling systems are dedicated to the modelling of standard building structures and can be very limited when it comes to handling anything more complex,” says Mr Vout.
“Others are very specialised, perhaps only really benefiting the precast industry or geared towards providing design intent for cast-in-place rebar details. But we had a complex bridge deck to detail, construction-standard drawings to produce and we needed to integrate with downstream technology [SteelPAC] for material management. We needed a system that was flexible and capable of creating accurate geometry.”
GDS chose Advance Concrete from Graitec as the core rebar modelling tool. A key factor in the decision was how quickly the company’s engineers could get up to speed, and because Advance Concrete integrates fully with AutoCAD there was no new user interface to learn. But while ease of use was important given the tight timescales – and the new users were productive within hours – ultimately it was functionality that swung the decision.
The bridge’s design – on the face of it characterised by elegant, regular simplicity – belies the complexity of the underlying geometry. With sweeping curves throughout its length combined with a series of cambers it actually represented a rich and diverse 3D environment. Mr Vout decided that adopting Advance Concrete, which can generate intelligent rebar detailing based on any given cross section was the only way the project could be accepted.
“Advance Concrete not only generated accurate rebar geometry based on the true bridge geometry, its model-centric approach also enables ready access to the detail. This means we can use our real-world experience to make sure that the bars being specified are both geometrically and physically correct: there is no point having efficient detailing if the bars are unbendable. Happily, Advance Concrete threw up no such issues and we were able to push forward with confidence, and in the end comfortably met the nine-day deadline for producing the first drawings.”
Temporary works
Graitec software was also used in the development of the temporary works required to assemble the concrete sections that would make up Saadiyat bridge. The contractor tasked with designing the cantilever carriages required was German civil engineering specialist Züblin. Each carriage, designed to bear a 200-ton section of bridge, was a complex piece of engineering in itself, with around 3,000 individual parts and weighing in at over 60 ton. Once again, time was at a premium, not least because no fewer than 12 individual carriages would be required simultaneously when the central columns were connected to their neighbours across spans of up to 200 metres.
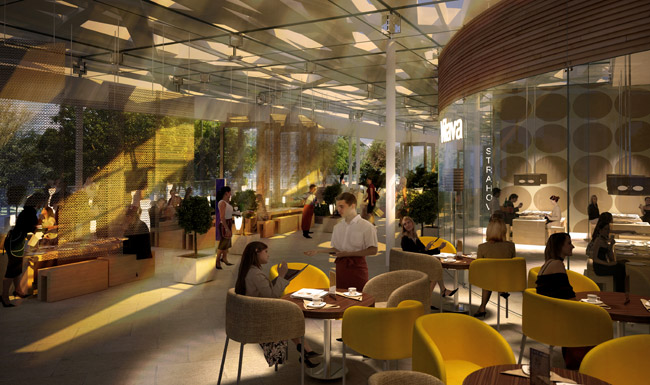
“Using Advance Steel meant we could build our master carriage directly in 3D, using intelligent steel components and taking advantage of collision checking to ensure right-first-time construction,” explains project engineer Tobias Jäger. “We could also use this 3D model to automatically generate the engineering drawings needed for the construction of the individual carriages. This proved vital in enabling us to meet the tight deadline for the simultaneous manufacture of the 12 carriages needed for the main spans.”
Advance Steel allowed Züblin to build a master carriage directly in 3D, using intelligent steel components and taking advantage of collision checking to ensure right-first-time construction. This intelligent 3D model was then used to automatically generate the engineering drawings needed for the construction of the individual carriages. This proved vital in enabling Züblin to meet the tight deadline for the simultaneous manufacture of the 12 carriages needed for the main spans.
“The Saadiyat bridge is an excellent example of an emerging trend in civil engineering projects, where different designers and engineers – even different contractors – can all base their work on the same core 3D geometry,” says Carl Spalding, Graitec’s UK Business Manager. “The key to the success of this is an accurate core model and tools specifically designed to make best use of this geometry at every stage. In this case it is great to see the specialist capabilities of Advance Steel and Advance Concrete being put to use to help two contractors meet some extremely challenging deadlines.”