The use of cellular steel beams is on the increase in the UK construction sector. But in order to make the most of this weight saving technology, you need a design tool that engineers find easy to use says Greg Corke.
Demand for structural steel has risen steadily in the UK over the past few years and it is now estimated that over 70% of all multi-storey buildings use some form of steel framed construction. And while demand is pushing up material costs, clients are also expecting more for their money, which means structural engineers are continually looking for new construction technologies to keep that competitive edge.
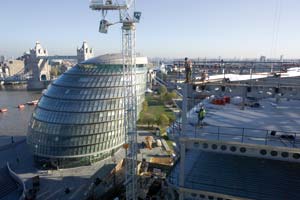
One such technology that is grabbing the attention of engineers is cellular steel beams. One in three multi storey buildings are now constructed using this system, which boasts longer spans while using less steel (particularly when used as a composite beam) and can also lead to a reduction in overall building height as services can be fed through the cells in the web of the beam.
One company that has been pioneering the adoption of this type of construction is Fabsec, which since its inception in the year 2001 now has a production capacity in excess of 50,000 tonnes per year. However, unlike most cellular beam systems which have their webs peppered with holes, the cells in FabsecÝs beams can be cut exactly where you want them prior to going on site. These can be circular, oval or rectangular and can be positioned and sized to coincide with specific building services requirements, or the web left intact so that secondary beams can be easily welded on.
Design files created in FBEAM can be utilised directly by Severfield-Rowen and William Hare subsidiary, Cellbeam for the automatic manufacture of Fabsec steel beams.
Naturally with such flexibility in cell placement, the design and optimisation of such beams is more involved than with standard sections and there needs to be an efficient design system in place to deal with this. FabsecÝs solution to this is a free software tool called FBEAM, which enables engineers to design both composite and non-composite cellular beams with ease, both in their ambient state and in fire conditions.
Beam design and optimisation
FBEAM uses a Wizard style process to guide the engineer through the design process. For simple beam design, the software offers up a number of standard templates. In the case of a custom cell composite floor beam, engineers must first enter data regarding the type of slab, the spans and arrangement of the floor. This is followed by a whole host of loading details, including imposed loads, point loads, and end moments.
Moving onto the actual beam design, FBEAM initially suggests a Ùrule of thumbÝ starting point for the section size of the beam followed by flange sizes, but these can be edited by the engineer. Providing maximum flexibility in design, top and bottom flanges can also be of different sizes, as can depth along the section to create custom tapered beams.
Next up, custom or standard cell arrangements can be generated using the built in web opening tools. These can be generated automatically along the section by spacing or Ùnumber ofÝ or produced individually according to size, location and type. Naturally, FBEAM provides full editing functionality, to accommodate a large air conditioning duct for example, but the software will automatically flag up anything that does not comply with basic design rules, such as when hole sizes are too big, or if an opening is located below a point load applied to the top of the beam.

Once the beam is designed engineers are given the option to either analyse the beam as is or to optimise it to find the perfect balance between strength and weight/cost. N.B. Cost is based on cost of steel plus cost of manufacturing processes such as amount of scrap and weld runs.
The system checks for typical design criteria, such as shear force, bending moments, web buckling, and deflection, and will warn the engineer if it fails any of these checks. For the optimisation stage, beam parameters such as depth, flange width or web thickness can be left totally free, fixed at a specific value or set within a range. The software then uses an iterative design algorithm to calculate which elements of the design are over and under utilised and adjusts them accordingly. Considering the amount of calculations the system is doing itÝs a very efficient process taking a matter of seconds, but beams can also be batch processed, so you can go off and make yourself a cup of tea if you want to optimise all the primary and secondary beams in a steel framed building in one go.
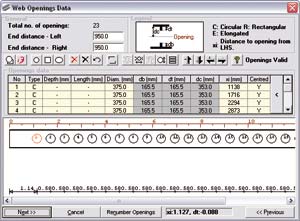
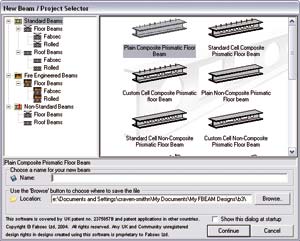
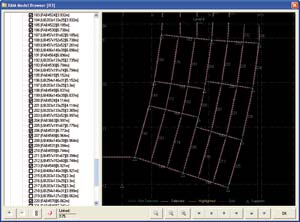
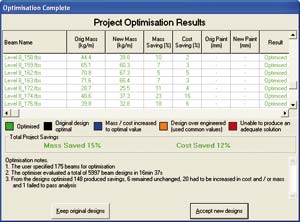
Fire engineering
In addition to designing and optimising at ambient temperatures, FBEAM can also be used to design fire engineered beams which provide up to two hours of fire resistance. Unfortunately this functionality is only available to selected customers and subject to an NDA (Non Disclosure Agreement) to protect FabsecÝs intellectual property and commercial position. LeighÝs Paints, a 25% stakeholder in Fabsec provides the design data for its Firetex FB120 intumescent paint, which can be applied off site up to 2.2mm thick and then, should it be subjected to excessive heat, swells to 50 times its applied thickness. Using FBEAMÝs Fire Engineering module users have potential for even more costs savings in the optimisation process. This is because the software looks at the effect of using different beam cross sections and coatings in conjunction with one another, rather than on an individual basis. For example, increasing the mass of steel by, say 10% (and hence increasing the fire hesitance of the steel itself) and using less paint could turn out to be cheaper than using less steel and more paint.
Project capability
New for version 2006 is a project facility which enables users to create projects to encompass all the beam designs and organise them by groups such as floor levels or roofs. A Group Edit facility now makes it easy for last minute design changes to be incorporated, such as loading modifications. This enables beam parameters (e.g. size, loading, cell arrangement) to be changed globally, where a change in one beam can be propagated down to others. In previous versions of the software this had to be done on a beam by beam basis.
Structural analysis links
Integration between different structural software is becoming more and more important across the industry and for this latest release Fabsec has followed this trend with a two way link between FBEAM and the RAM Structural System, a structural analysis solution from RAM International, the company recently acquired by Bentley Systems. Using the FBEAM plug-in inside RAM, engineers can select any standard Universal Beams which they would like to convert to Fabsec sections or alternatively the system can flag up any candidates which it thinks are likely to have any substantial mass or cost savings – in most cases these are long span sections.
RAM will then export these sections, together with their loads, so they can be designed inside FBEAM. Beams are to be found inside a project navigator which enables engineers to easily see each beam type, where it is located inside the building and its analysis state. These can then be designed, analysed and optimised in the standard way, either individually or on a group by group basis, and once complete the data can then be imported back into RAM Structural System to coordinate the structural model.
Conclusion
By transforming standard Universal Beams into Fabsec sections typical weight savings are claimed to be in the order of 20-25%, and with this in mind itÝs easy to understand why Fabsec is now producing over 50,000 tonnes of beams under license every year. However, in addition to material savings, there are many additional benefits to be had from its cellular beams. Spans of twelve to 24 metres are eminently achievable, meaning bigger uninterrupted office spaces; there are fewer structural elements to erect on site; and because the services can be fed through the beam instead of under it, developers can lower the overall building height ± which can lead to a reduction in cladding costs, additional floors within the same building envelope.
However, many of these benefits would be lost in the mix without an intuitive and cost effective way of designing these long span cellular beams and with FBEAM 2006, Fabsec looks to have just the tool to do this. FBEAM is an incredibly easy tool to use. ItÝs a simple product designed for a specific task and with its Wizard-based approach and tutorials embedded in the free CD most engineers should be able to hit the ground running.
The link to the RAM Structural System is an interesting development for a product which until this latest release existed predominantly in its own sphere. However, this development work is not finished and workflow between the two products will be refined in future releases, plus Fabsec is also talking to other structural design and analysis software vendors to broaden its reach.
In FBEAM you wonÝt find an eye catching 3D modelling environment common to many mainstream structural software products, but for most users ease of use and simplicity is more important than bells and whistles. And when considered as part of an overall structural solution, Fabsec is delivering a very attractive proposition which could help structural engineers get an edge in an increasingly competitive marketplace.
Product: FBEAM 2006 Supplier: Fabsec Price: úFREE Web: www.fabsec.com