If digital construction is the future, we need to understand modern fabrication methods. Richard Harpham ponders if today’s design-centric BIM solutions are the right tools and, indeed, if architecture is the right discipline to take this on? It looks like the industry needs a new process
Here we go again… I think we can all identify with sitting through investor decks or keynote presentations that still start with that McKinsey flat productivity diagram, statements on how fragmented the construction industry is, the ever-shrinking pool of talent and the rise in cost of labour and materials. It seems that we still feel the need to point this out as a precursor to highlight the use of machinery, automation and robotics that we consistently sell as the solution to bring the industry forward.
For us though, it’s no longer about identifying the problems or highlighting that ‘Modern Methods of Construction’ would better the manufacturing process and will save the day. It’s not about robots and machinery, nor standardisation of elements to achieve economies of scale and mass production. It is about software and collaboration and not just BIM (Building Information Modelling). It is about focusing on the before and not just the during.
Prefabrication itself shouldn’t be the only hope, especially if you opt to brand it with Artificial Intelligence (AI), Machine Learning (ML) or ‘integrated supply chain’ next to it. It all feels a bit like 16th century medicine… whatever the ailment, a course of leaches will fix that!
When we actually lift the hood on prefabrication, it is clear we don’t get to skip all the steps other industries had to make to benefit from mass customisation and integrated delivery of products. We still need to define and execute our construction differently. That is not a technology problem. If you are struggling to write that PowerPoint to present to your executive team on how your firm can evolve to ‘industrialised construction’, you will already know that it’s not about buying software.
Let me give an example. A recent study at Stanford found that the utilisation of usable space for executing any activity across a construction project’s duration can average out at 3.2%. Let’s put that in perspective. That means for 96.8% of the time NOTHING is happening in each and every square foot of real-estate on the ‘construction factory floor’. Imagine the factory manager at Tesla telling Mr Musk that each square foot of his factory is only being utilised to make something 3 or 4% of the time. Identifying these types of opportunities, where technology has already proven to overcome issues in other industries may be a better starting point. If the whole life of the build encompasses the whole process as if it were in a single factory, then creating a building production plan that can be systematically tuned for increased productivity, may be possible.
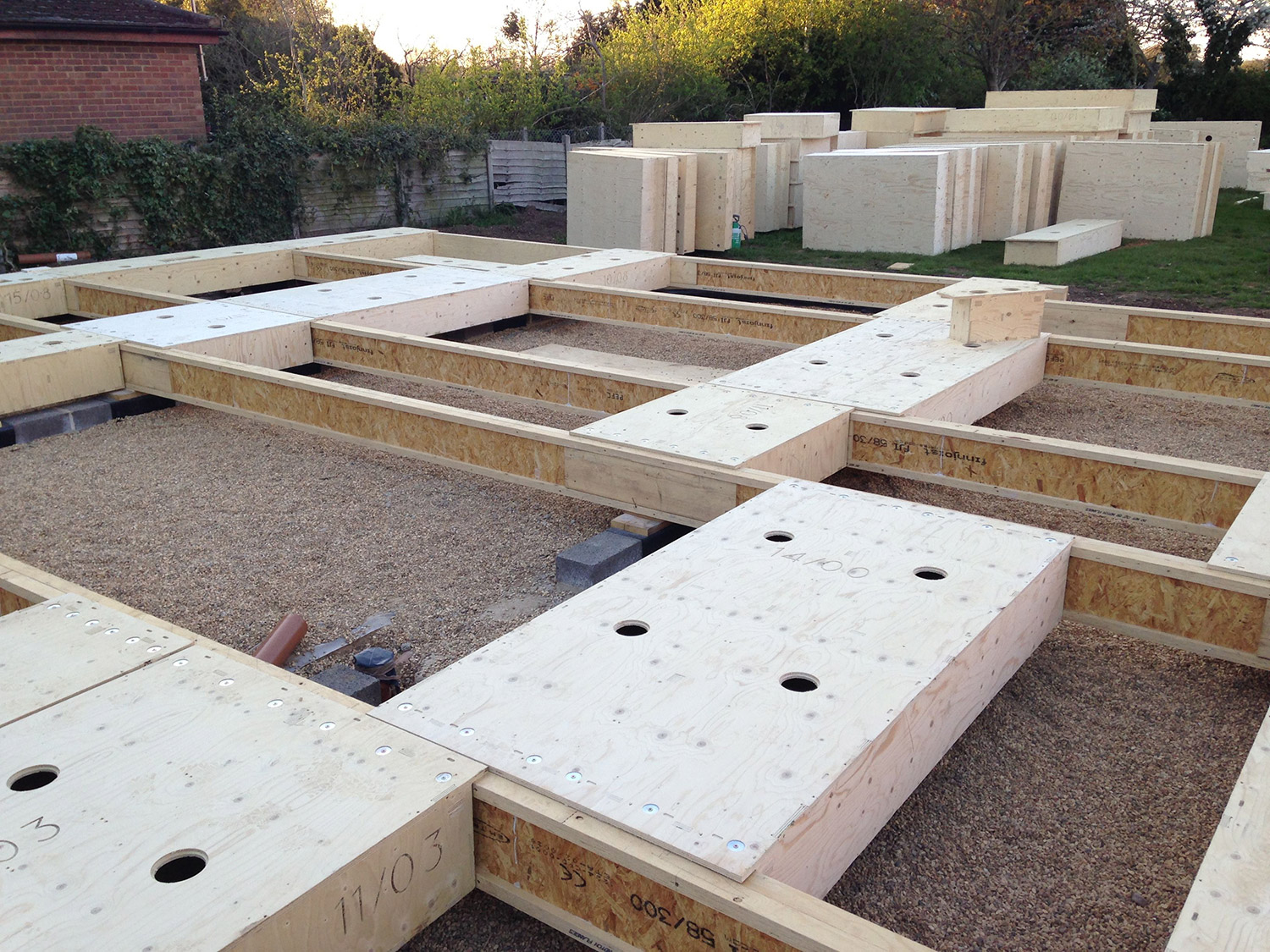
So, we are now talking about the process of how we can better build something, not just the technology that will change how we build. Even though industrial scale building prefabrication has existed for more than a century, construction companies have only now moved beyond thinking of it as a low-cost solution for repetitive structures, towards opportunities for higher quality, more predictable, mass-customised applications.
Now all we need to do is figure out how to not mess that up by insisting on using 100-year-old contract structures and 20+ year old design and collaboration technologies to deliver it!
Industrial methods
So, what should Industrialised Construction really mean? What has to happen before, during and after the production of a building to better leverage industrial methods?
It’s clear, we spend most of our time focusing on the During (manufacturing, construction methodology), but we are so often missing the Before. The design is the key and essential part to it all; if we do not do a better job of designing for constructability, then we will never achieve any of the desired outcomes.
For many, Design for Manufacture and Assembly (DfMA) has become the definition of this opportunity. In software, DfMA is a hot buzz term at the moment but from the very fact that general contractors are taking the lead in DfMA we have to assume that something is maybe fundamentally flawed here. We might argue that if it isn’t DfMA in the architect’s office, then the architect’s work isn’t a buildable design… it is design intent.
This might de-position the current design-centric BIM solutions from being at the core of the design for constructability process. If we need to understand how to construct a building during design, what technologies do we need to achieve that? And is architecture the right discipline to take that on?
Process vs design
In this magazine’s May 2019 article on digital fabrication, Martyn Day asserted that, “there are few architects who fully understand the digital fabrication limitations of building fabrication systems. Design for Manufacture and Assembly (DfMA) is a separate discipline within itself and requires a holistic view of what is possible, what’s available and the cost implications of early design decisions such as processes, material use and serviceability.”
Combining this with the impact of contract liabilities raises the question: are we seeing the inevitable removal of the role of a ‘master-builder architect’? There would appear to be many general contractors that already are operating from this assumption. But this seems in conflict with concept of design for constructability, manufacturing, assembly, carbon loading and all the other outcomes we want to deliver from building production.
At the very root of manufacturing is ‘design’, not design intent. In manufacturing, the product is not the replicable physical item, but the process and the IP. The very makeup of how it is built.
What we have discovered is that the current ‘model-centric’ approach is solely focused to provide a mere graphical representation which just isn’t enough. We need more consideration of the constructability. Less focus on drawings and more on the process and the actual design of the object and how it is built. We have spent so much effort and time focused on the 3D digital twin generation and loading the BIM content that we have missed an opportunity to own and commoditise the process. The real value is in the process, not the static object.
The legacy of the era and evolution of BIM may be that we have had too much focus on the design intent, drawing layouts and mitigating the overall responsibility for how it is actually built. Rather than tackling the problem at its roots, we have focused on the during (MMC and robotics) and after (digital twin) without identifying the value of the before (DfMA).
Design is the key to unlocking efficiency, not robots and manufacturing automation. So actually, yes, we do need architects, but the role of the architect is being redefined. The same will be true of the technologies needed.
In Phil Bernstein’s book, ‘Architecture Design Data’, he states, “The newer technologies appearing in the second digital turn are less transactional and more profound, in that we are now reaching a time where the tools are rapidly approaching the real possibility of managing the complexities of making buildings”. He also postulates,
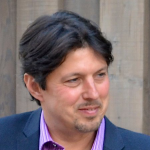
“The marketplace will press the AEC industry as a whole to leverage computation to improve the and meet the challenges of 21st century construction,” pointing to how other industries that have already climbed the productivity ladder through digital transformation.
If you take a look at the semiconductor industry, much of the industry’s progress has come from advances in manufacturing – the secret sauce of Moore’s Law. Imagine the possibilities of advanced manufacturing delivering the built environment.
However, we don’t have the liberty of spending years and large amounts of money resolving every detail like the automotive industry or the ‘Master Architect’ once did. We need data flow between stakeholders at all times. We need to do a better job of enabling the design team to make the right decisions and provide/produce the right data We need to leverage software, AI and ML to do so, but the question is… what might this look like?
About the author
Richard Harpham has experienced most of the highs and lows of bringing disruptive technology to developers, designers and contractors. As an early hire at start-up, Revit Inc., he then spent nine years at Autodesk bringing Revit and a ‘new’ concept called BIM to the US market, as well as leading global marketing for AutoCAD and all Autodesk AEC products. More recently at Katerra, he led software strategy to support transformational changes in how we design, engineer, and deliver buildings.