What might the addition of new information types to BIM models help us achieve in terms of construction project efficiency and future building maintenance, asks Rob Charlton, CEO of AEC technology company Space Group
As more people in the industry familiarise themselves with 4D simulation and know how to use it, the more popular it becomes for Level 2 BIM projects.
The benefit of using 4D is that it adds the time dimension to an information model. That, in turn, enables us to sequence work activities graphically and simulate this in visual formats across the project lifecycle.
In the past, the connections and integration between a 3D information model and a construction schedule were minimal. Now, with the introduction of BIM and the integration of information within the BIM model, we can ‘virtually’ construct, rehearse and test a project before any ‘real’ construction work begins, with considerable potential to save on costs. And, with the added bonus of 4D, we can add scheduling to the model, further enhancing our view of an asset in all its as-built glory, way ahead of a project’s actual start date.
However, the sequencing of work activities doesn’t have to be restricted to just the sequence of construction. It can also be used for logistics and safety planning, taking into consideration site deliveries, pedestrian and vehicle movements, positioning of equipment and much more. In this way, 4D helps everyone involved in a project to understand not just the actual build, but also all other activities, on and off site. It’s also a big help in comparing schedules against progress, helping to highlight activities that are running late or ahead of schedule.
Where 4D and IoT collide
The concept of introducing timings and scheduling to a BIM model is a simple one and quite possibly the most logical step in the integration of technology in the design and construct phases of a project. So what comes next?
The Internet of Things (IoT), with its use of sensors to connect devices and facilitate the exchange of data, is an excellent example of how 4D might slot into the BIM environment. Just as the IoT ecosystem gives businesses and consumers access to data dashboards and analytics via their devices, 4D can enable a project team to map timings onto activities and view it all in one place.
By 2020, there could be more than 24 billion IoT devices on the planet, according to some analyst estimates. That equates to approximately four devices for every human being on Earth and demonstrates the accelerated speed of growth in technology. With that in mind, why should 4D be the end, when 5D could be just around the corner?
In fact, 5D is already here. All it really means is the addition of cost information to a model — another no-brainer. After all, isn’t it the next logical step, once a design is in place along with all the data behind its constituent parts and the timeline as well, that we should start to add in budget data?
However, where I think we should be heading is in the direction of real-time data for predictions, forecasting and monitoring. Typically we work with static, historical data and information. But information tends to change over time. Take, for example, the cost of steel: prices change due to currency fluctuations, supply chain issues, even factors such as natural disasters. With predictive analytics, we can start to predict steel prices based on trends and patterns.
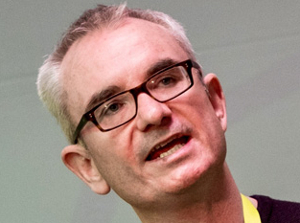
Rob Charlton is CEO of Space Group, the AEC technology company that includes Space Architects, BIM Technologies, bimstore, CAMPUS and Volula. An architect by training, he is passionate about improving the value and performance of buildings using technology.
Likewise, in Formula 1 racing, predictive analytics based on data gathered by monitoring engine heat or vibration during a race can be used to alert the pit crew if that engine is heading for a failure, prompting them to radio through to the driver to come into the pit for further investigations.
The cost of the sensors needed to collect these kinds of information has fallen dramatically over recent years, as has their physical size. It’s possible to embed sensors into a construction’s fabric to monitor the stability of structures such bridges or monitor the curing speed of concrete in a building. Smart ways of thinking — as seen in the ‘smart building’ and ‘smart city’ concepts — are only the tip of a very large iceberg as far as the AEC industry is concerned. Using real-time data can introduce many new ways of understanding assets and how they change and develop over time.
A model offers an easily accessible way of understanding the design of the asset and its information. Details that would once have been hidden in non-digital file formats are now easily interrogated graphically. This allow us to proactively anticipate events in the asset’s lifecycle and preempt maintenance and repairs, for lower long-term costs. If we then add in more data on how the asset behaves, we can start to predict patterns and learn lessons that might be applied to new construction projects, based on what did (and didn’t) work well in the past.
Data is an exceptionally powerful tool and understanding how to use it is the way forward — no matter which dimension we occupy.
If you enjoyed this article, subscribe to AEC Magazine for FREE