Covid-19 has not stopped Boston Dynamics from working with AEC hardware and software developers like Trimble, together with advanced users like Foster + Partners. Martyn Day explores the impact the quadruped robot is having on construction
When Boston Dynamics agreed to come and talk at AEC Magazine’s NXT BLD event in 2019, the company was just about finalising the design of its quadruped robot Spot before it moved to mass production. This was a major move for Boston Dynamics as it had spent decades developing robot technology with no obvious plan to productise its innovations, funded by bodies such as the US Defense Advanced Research Projects Agency (DARPA), then Google, which helped it create Atlas, Petman, BigDog, Wildcat and Spot robotic platforms. Founded in 1992, Boston Dynamics was bringing its first robot to the mass market.
While talking with Boston Dynamics, it was clear that while they had designed Spot, it was certainly a technology in search of an application. As a quadruped robot, Spot should be able to handle construction sites, areas of danger, repetitive tasks like site survey, so the company was reaching out to firms in that space to see what they could do with the platform. Fortunately, at NXT BLD, the laser scanning companies sent over their development teams and they had even asked for the payload bay specifications to 3D print platforms for their scanners. Both Topcon and Faro were carrying out live scanning tests on the show floor!
Roll forward a year and a half and Boston Dynamics has just announced a major partnership with Trimble and Foster + Partners, with more to follow. The irony here is that the chances of seeing robots in the wild has increased dramatically, while the chances of seeing humans outside their houses has dropped dramatically. Thank you Covid.
Talking with Brian Ringley, construction technology manager at Boston Dynamics, it was interesting to hear how Spot has developed to become a construction worker.
The chassis design has been continually refined to offer better protection and weather sealing and firms like Tesla are using Spot to help with the rapid construction of its ‘Giga factories’ for batteries. The need for extended operation, beyond the 90 mins operation of the onboard battery, has led to an update coming soon, which will allow Spot to automatically head to recharge itself. At the same time, the much-seen articulating arm will be available next year, allowing new interactive applications of the robot.
With that, Boston Dynamics has been working on the controller software APIs allowing developers to interface with Spot’s sensors and even tap into its power in the payload bay. After a bunch of refinements, Spot is ready for duty.
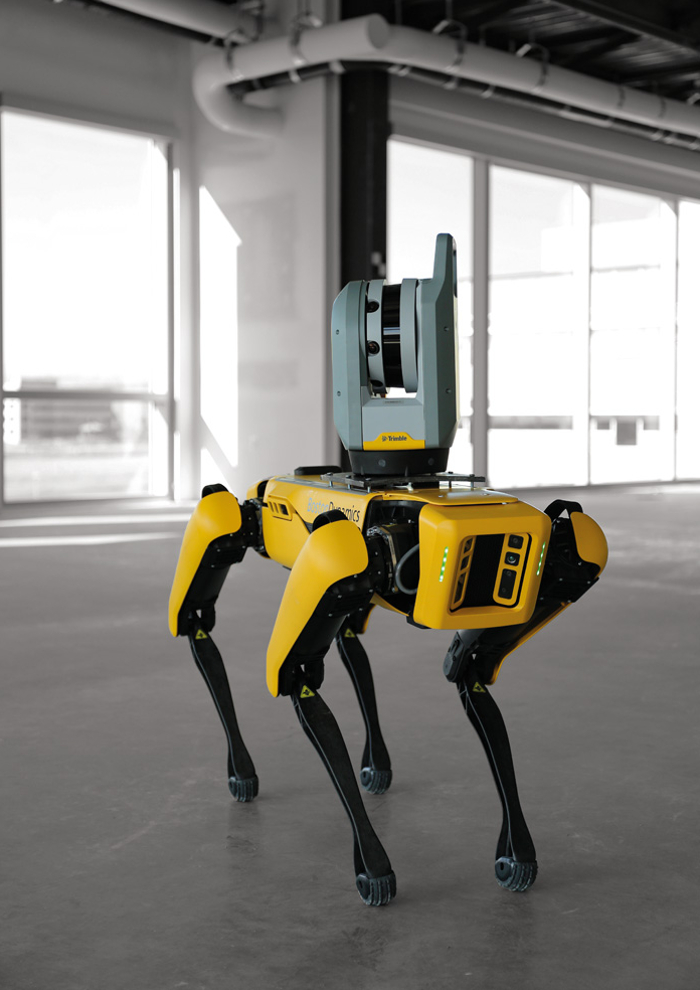
The Trimble partnership
The first major developer to announce a partnership is Trimble. The company has extensive experience in construction robotic automation featuring ultra-precise GNSS (Global Navigation Satellite System) and machine control to full automated vehicles, such as grading systems.
We talked with Martin Holmgren, the company’s general manager for buildings field solutions. He explained what Trimble brings to the party, “What makes Trimble unique and I think the preferred partner for Boston Dynamics is that in the construction world we already have a very heavy investment and focus on autonomy. And whether it’s an excavator, or a 70 pound Spot robot, for us it’s another automated vehicle in the mix.
“In a Trimble world we have the full 3D model of what should be built, as well as information coming out of say, a laser scanner or other sensor tool, that can rapidly augment the understanding for a robot of what’s around it — how to best navigate it, but also things like how it should position itself to optimise the value of this scan. So there’s a lot of AI and kind of next level intelligence that we can bring to the workforce and we intend to bring Spot both to the civil construction sites, the earthmoving sites, but also to indoor environments. With Spot’s size and its agility, it’s is a really good fit for us both in and outdoors.”
After hours
Automated anything on a construction site comes with health and safety risks which, at the moment, limit the mixing of people and heavy automated devices, but there will come a time when that will be the norm. I asked Holmgren if Spot changes that concern, or if it was going to be a limiting factor in its deployment? He replied, “If you had a laser scanner on Spot’s back, when everyone’s left for the day, there’s no human obstructions. You could have Spot walk every floor of your building, during the off hours of the construction side, collect a complete set of point clouds that are ready to go, available in the computer of the project manager when he arrives at the site in the morning.
“It actually doesn’t require anyone to be there. Digital design, digitise the construction site, that’s where we add value.”
The earth moves
Looking at outdoor examples, Holmgren outlined one concerning the digital terrain model, which needs to be monitored each day, or every three or five days, so they can know how much material has been moved and how much material needs to be moved to achieve the features of a specific site. “This ties back to cash flow for these companies, because the subcontractor wants to be paid quickly as possible. So, there’s tension in the construction process between determining the right time for an investment and for payments.
“On smaller construction sites, you may need to achieve a certain terrain model using a total station and Spot with a Prism or GNSS, we can use it for layout, essentially meaning we could even place stakes in the ground with Spot’s arm.”
Power in reserve
Trimble’s equipment already comes with onboard batteries that outlast Spot’s 90 minute duration so it doesn’t need to tap into the robot’s power supply, maximising it’s longevity. Trimble is looking at perhaps tapping into Spot to get a charge boost when it goes back to the recharge station.
I asked Holmgren about reliability, as this is Boston Dynamics’ first prosumer product and construction sites are exposed and a potentially unfriendly place for precision electronics and servos. “We have, of course worked with Boston Dynamics for quite a while now we’ve seen the evolution. While Spot looks identical to what you saw in 2019, performance and capabilities have evolved tremendously.
“The reliability is not at the same level as you would expect from mainstream construction technology but I would say they’re getting there. Trimble is very, very careful with putting our brand and our reputation behind a product. We have units in North America, New Zealand, India, testing them in different climates, different temperatures. Like any brand new technology you bring onto a construction site, whether that’s robotics or something else, it will be improving over time, but we have determined that we’re comfortable bringing this to market and that the benefits by far outweigh the challenges.
“Of course, we offer Trimble support and we’re comfortable with all of European Union, US, Canada, Australia, Japan, Singapore, as starting markets and we will have local service centres at each of these locations, with a level of service capability to provide continuity of operation for users.”
Pricing for Spot through Trimble has yet to be set but they are looking at both outright purchase and monthly hire.
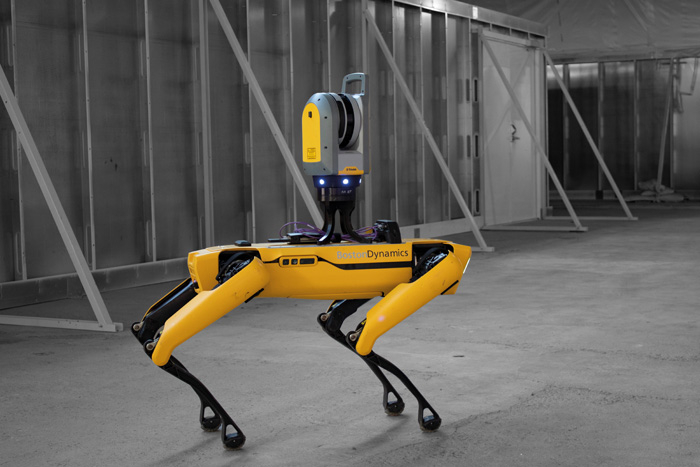
Foster + Partners
As part of Boston Dynamics’ Early Adopter Program, Foster + Partners Applied Research + Development group (ARD), has been exploring the use of Spot on construction sites, by laser scanning on a regular basis to easily compare the ‘as-designed’ models against the ‘as-built’.
The team used its Battersea Roof Gardens mixed use project (the third phase of the Battersea Power Station development, as a testbed). Spot followed a designated path on a weekly basis, scanning as it went, which generated a sequence of highly comparable, consistent models.
Martha Tsigkari, partner, Foster + Partners explained, “The ability of Spot to repeatedly and effortlessly complete routine scans, in an ever-changing environment was invaluable, not only in terms of the consistency but also the large amount of high-quality data collected.
“Through this process we developed a sequence of scans that may help us track the project progress against timeframes as well as facilitate regular comparisons against the BIM model.
“Our scans can ensure that very quick and accurate changes to the newly designed system could be made to accommodate the differences captured by the scans – all in a matter of days. This could result in savings both in terms of time and money.”
Foster + Partners has also used Spot to construct a digital twin of its own campus in London. The team built up a fourdimensional model, showing how the space changes over time. Adam Davis, partner, Foster + Partners, said, “Combining temporal and spatial information with data from sensors that read environmental conditions and occupancy, we can construct an intricate model of how people, furnishings and environmental conditions interact. This, in turn, helps us to operate our premises more efficiently and to anticipate how new designs will perform.”
Conclusion
While Spot may be a novelty as it’s the first roaming robot in construction, the reality is that it brings real business cases with it and will expand and drive further digitisation of the profession. It will drive Digital Twins and deployment of 4D and will also help in spotting errors on site quickly.
While talking with Holmgren, we discussed the development of swarming technology and the interaction of robots on site. It’s too easy to just wonder at Spot as a singular device but imagine a construction site as a network of machines, each carrying out their task, all feeding back to a centralised system, as they sculpt, position and place everything in the right place, in the optimum sequence, pausing only to recharge.
There will be robots surveying the site to watch over the work of other robots and add additional layers of geometric feedback and data to the cloud, where AI can auto recognise building components, ensuring the next ones arrive on site just in time. Construction sites of the near future are going to be very different places, if we ever manage to leave home again.
SPOT will cost $74,500 for a base model and obviously increases with payload and selfcharging stations, articulated arm.
■ bostondynamics.com ■ construction.trimble.com/spot
If you enjoyed this article, subscribe to our email newsletter or print / PDF magazine for FREE