UK firm uses Formlabs Form 2 to print architectural model for spatial planning
Lush Cosmetics, known for its bath bombs and bold cosmetics, recently found a new application for its in-house family of 3D printers – 3D printing for architecture.
Instead of developing new consumer products, the UK firm used one of its many Formlabs machines to design and develop the spatial layout for a new additive manufacturing unit at its global headquarters in Poole, UK.
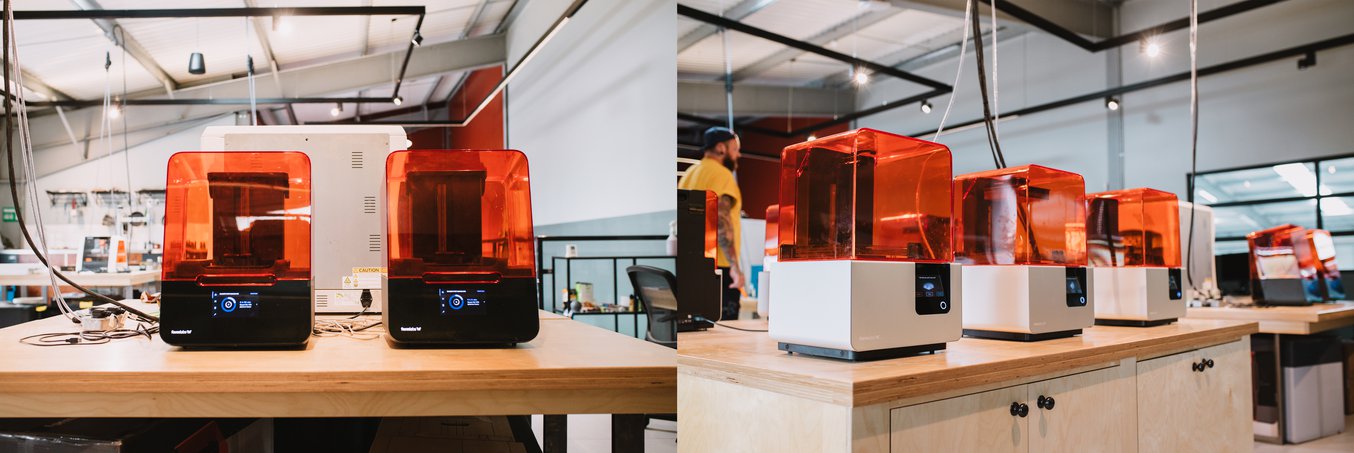
To help plan for new equipment, visualise the building and optimise the large open space, the Lush team wanted to create a to-scale architectural model of Unit 1, where most of its new products are conceptualised
At first they reached out to a design bureau which quoted £15,000 for the project, including labour, materials and shipping.
Keen to try his luck in-house, Damien Carter, Innovation Lab Manager, Lush Cosmetics, made a mockup of the space with 3D CAD software Solidworks.
He was able to print the design on a Form 2 3D Printer using a mix of Formlabs standard engineering materials: white resin for main structure, grey resin for the internal worktops and clear resin for the windows.
When he calculated the in-house project costs including labour and materials, he estimated that the model cost just under £900 to deliver – a 94% cost saving versus the external quote.
“Using Formlabs printers helped us save over £14,000 and several weeks of production time when printing a scale architectural model in-house of our new R&D facility,” he said.
“We found this to be a great tool in terms of spatial planning, meaning we can 3D print our equipment and we can tangibly look and feel how something may fit within units.”
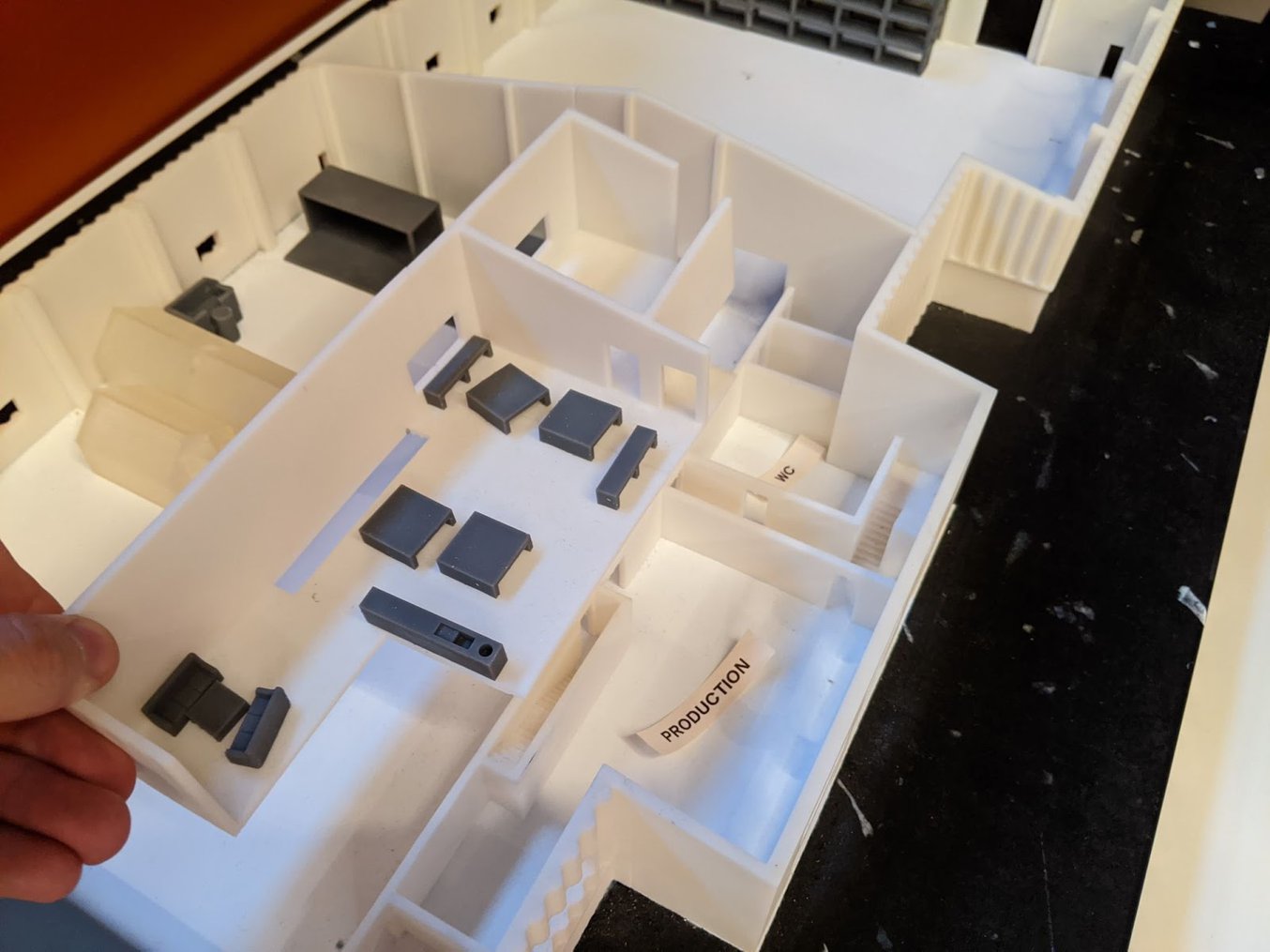