Autodesk invited the press to the new headquarters of its AEC Division in Boston, USA, for three days of presentations, customer site visits and technology talks on everything BIM. Martyn Day was there to report
As Autodesk is now deep into its transition to become a ‘subscription’ company, the old annual releases are now a thing of the past.
Autodesk’s AEC division is seemingly on a biannual cycle of delivering major improvements to its core products. These currently happen in March / April and September / October timeframes, with perhaps some other news items coming out in November – in time for Autodesk University in Las Vegas.
Subscription allows software developers to be much more dynamic in the delivery of content and be more open about their development objectives. With the Autodesk portfolio seemingly ever-growing to deliver on BIM, collaboration and now fabrication, Autodesk held a press event to provide a snapshot of its products and give some indication of current and future development.
Technology trends
Our introduction and first talk was by Nicolas Mangon, Vice President AEC Strategy and Marketing at Autodesk. In an overview of the industry, Mangon laid out some interesting stats, with predictions that the 3.5 billion people who live in cities today will swell to 10 billion by 2050. This means there will be a huge need to build new homes and infrastructure to manage this increase in these megacities. However, AEC makes up 6% of the global GDP and is low margin, high risk and highly fragmented.
Historically the sector has not invested heavily in technology but a move to digital constriction could save $1.2 trillion in efficiency – 10% of the total money spent globally on AEC today.
Mangon highlighted several technology trends that are set to revolutionise the industry. High definition surveys, compute power (the cloud) enabling sophisticated analysis of big data, Virtual Reality (VR) and Augmented Reality (AR) immersive environments, mobile technology, the convergence of manufacturing and AEC to digital processes and Artificial Intelligence (AI) driving generative design and machine learning. Combined, these will revolutionise the design, construction and Facilities Management (FM) of the built environment.
The future of project delivery
Vikram Dutt, Senior Director, Building Business Line at Autodesk gave the next talk concerning Autodesk’s focus on ‘Connect BIM’. Autodesk wants to use the cloud and BIM to provide an environment which creates a single place to access the right information in the right context on the right device, from design to maintenance.
Autodesk has not had a glorious history in document management, against products such as Bentley ProjectWise for instance, but when files become redundant and people are more concerned with model sharing and accessing live data, Autodesk sees it has a chance to offer an alternative.
BIM models are getting larger, models are being accessed more often and teams are becoming more geographically distributed. With 20 million AEC professionals worldwide and the next 30 years requiring a herculean effort in infrastructure delivery, the process needs to change.
Autodesk feels it is in a unique place to offer this as with Revit market share, it feels it has BIM leadership. Dutt added that Autodesk has developed the only native cloud platform for AEC, with scalability and a well-established AEC ecosystem. With an eye on industry compliance and now developing a deep cloud portfolio, Dutt proposed BIM 360 as a cloud solution for the AEC space from design, to build and operate.
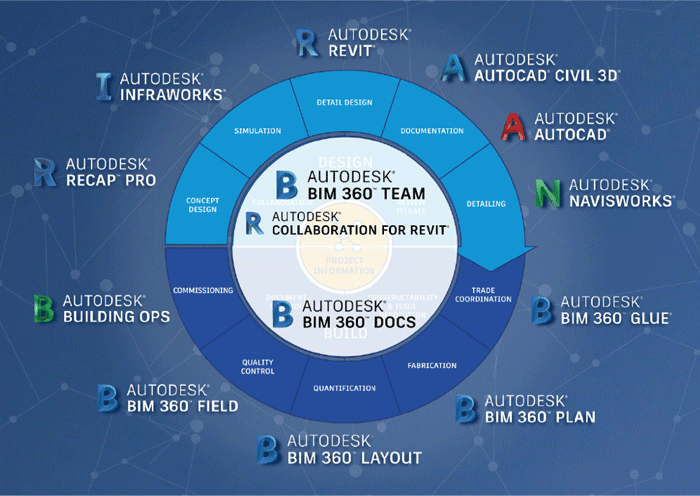
Autodesk Forge
Autodesk Forge is a significant development for Autodesk and its ecosystem of developers. It provides a cloud infrastructure for all of Autodesk’s technologies and serves them up as building blocks for third-party developers to create new solutions or develop / merge with their own. All this is made possible because BIM 360 and Forge operate in a single Common Data Environment (CDE) enabling new ways to process, distribute and see AEC information.
In the past, developers have had to acquire expensive licences of OEM Autodesk products, or through APIs develop plug-ins for Autodesk’s desktop products. Forge is a fundamental and major change to third-party developers.
Project Quantum
With a hectic schedule, a number of issues got passed over relatively quickly. Unfortunately, one of those issues was Project Quantum which promises a whole new world of collaboration between participants in AEC workflows using the cloud. We covered this in great depth in the January / February 2017 edition.
The main new piece of information that we gathered on Project Quantum is that Autodesk expects to have at least a couple of customers talk / demonstrate their early experiments with the formative technology at Autodesk University in November.
There has been much speculation as to how far along Autodesk is with the development of Quantum. With this information, I think it’s safe to assume that Autodesk is further along than most expect.
While collaboration is the primary goal of the first tranche of Quantum technology, it is especially important to Autodesk’s commitment to try and better connect modelling with fabrication and to participate in the industrialisation of construction. The first realisation of this, is acknowledging that Revit is not best suited to drive fabrication machines directly but it’s essential that BIM interfaces with digital construction tools.
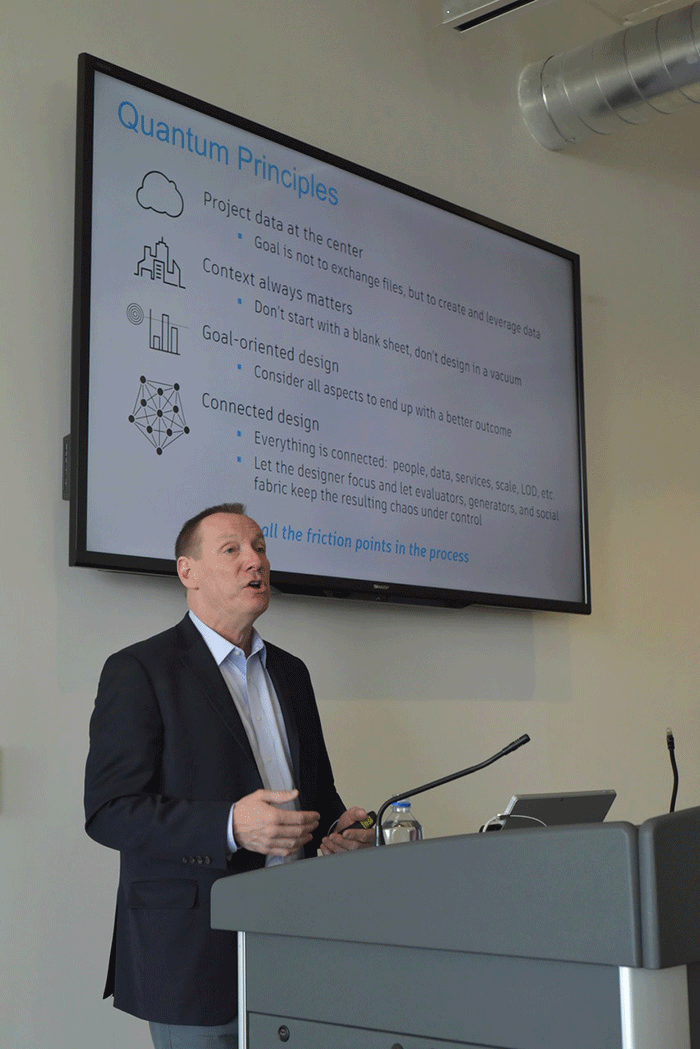
Digital Construction
Sarah Hodges, Director, Construction Business Line at Autodesk took to the stage next and concentrated her talk on a specific area of construction software, collaboration and connectivity – with BIM 360 Docs acting as the central hub, connecting to Glue, Field, the newly named BIM 360 Ops and Project IQ.
The task of managing construction data and post occupancy facilities management through the cloud offers Autodesk some fresh markets to address and, with mobile access, the BIM model really starts to leverage the Information component.
Throughout Hodges’ presentation, the new BIM 360 cloud-based User Interfaces really stood out as providing very clear views of multiple data types and worked well on the screens of mobile devices, although these also respected the fact that 95% of all data required on site is still preferred in 2D at the moment.
Infrastructure re-imagined
Theo Agelopoulos, Director, Infrastructure Strategy & Marketing Design and Build went through Autodesk’s thoughts on the market and developments within its product portfolio on Infrastructure. Refreshingly, this year InfraWorks was not the only product Autodesk seemed to want to talk about and really pushed the company’s capabilities on Reality Capture with Recap and Remake.
Agelopoulos stated that Autodesk doesn’t want to be a GIS firm (and so partners with the likes of ESRI and others for that component) but it does want to sit at the intersection of BIM and GIS.
Autodesk customers are starting to really use drones, laser scanners, even LiDAR for much more than surveying and are building aggregated models for advanced uses such as measuring material removed from site, security, and design optioneering.
Infraworks was demonstrated in advanced bridge design and water services design, all looking very slick and turning civil engineering into the best version of SimCity there’s ever been.
The cloud was the big story repeated throughout the day; cloud simulation and collaboration with BIM 360 Glue were shown and even Civil 3D being able to upload and publish to the cloud.
UK vs US
The next session included talks from Phil Bernstein, Independent Strategy and Technology Consultant (former Autodesk AEC VP) and Mark Bew, Chairman at BIM Task Group in the UK.
Bernstein is interested in what factors drive the adoption of technology. In the UK and the US, Revit has done well and BIM is becoming the normal way of working, but he identified that this success was for different reasons.
In the US, where Government mandates are not particularly liked, BIM succeeded as it’s a highly competitive market. Nobody forced BIM on any firm, the tool was taken up to ‘bludgeon the competition’. The net result is a market where no two firms use BIM in the same way.
Meanwhile, the UK has taken a policy-based approach with an alliance of the supply chain with mutually agreed objectives and prescribed common practices.
While this is perhaps a rose-tinted view of the challenges and acceptance of BIM standards, the general difference in approach is certainly well observed. Americans will fly by the seat of their pants. In the UK, we are more likely to buy ours from Marks and Spencer, as they just work.
Bernstein finished off with a prediction that he feels that, as the construction market is high commoditised with low margins and even final costs can’t be guaranteed, the market may change to seek engagement for more guaranteed outcomes, over lowest cost, as a larger policy objective.
Mark Bew, Chairman at BIM Task Group from the UK did a sterling job of taking the audience through the Government’s drive to improve the UK’s construction industry’s woeful productivity issues, which employs 3 million people and generates £100 billion a year, of which 40% of the projects are public works.
As the single biggest client, the Government kicked off a strategy in 2011/12 to push a data-driven process to improve program delivery and drive costs down. CrossRail is the first end-to-end project delivered in that manner but is only one of 15 worldwide projects around the world that is using the UK-derived standard.
Bew stated that Level 3 focus has now started, with an estimated implementation in 2025, with £15 million in backing from the Government (Level 2 had £5 million) but solving the Level 3 problem is much bigger than £15 million and so he is in the process of planning how to get more funds.
Level 3 is all about transactional BIM with much more sophisticated models. It’s the move from files to objects, single buildings to communities of buildings with infrastructure (could be termed smart cities), and of course, data security is a major issue.
Bew thinks we have lost the skill of generating decent briefings, and through better understanding of feedback from real world information in space usage, human interaction wants to focus on creating detailed digital briefings for Level 3 projects.
Revit and Connect BIM
It has been 17 years since the launch of Revit. Autodesk has owned it for 15 years of its life and so has done all the heavy lifting. Oddly enough Revit was originally a subscription-based product before Autodesk bought it. In 2005, we had the first version of Structures and 2006 came MEP. By 2013 they had all been rolled back into one product.
There wasn’t a lot of time allocated to in-depth features but Autodesk highlighted the updates to the new multi-storey stairs command in Revit. Storeys can be different heights and unique edits can be made with auto-updates to the railings. The railings can also be used as fences.
Navisworks models can now be taken into Revit and users get the same performance, allowing Navisworks to draw inside Revit. As a test, they took the whole city of Moscow inside for a dynamic fly-through.
Formit and Revit now play better together, so early concept designs don’t lose information when they move downstream.
Autodesk Insight is a cloud-based energy and daylight performance tool which can be used through the design process, from Formit concept models, all the way to final sign off. It has a really nice simple graphical interface and it’s easy to understand the results.
Autodesk Revit Live is Autodesk’s first iteration of delivering Revit models to VR. In the past, you had to use multiple packages to do it; now it can be uploaded to the cloud for automatic preparation and pre-flight.
The main problem here is that any changes require the whole file to be re-uploaded and re-processed. I suspect this will be improved quickly as ‘Revit to VR’ applications from third-party developers, such as Enscape, can already handle small delta changes without having to shunt big Revit models around. (see our Revit to VR article).
Build Space
One of the key areas in Autodesk’s new offices is the Build Space, a factory floor with a suite of massive fabrication tools and robots for customers to come and experiment on designs using cutting edge digital fabrication and materials.
There is also a space for industry-related incubators to operate in-house and use the machines, while sharing their experiences and challenges with Autodesk to help improve software product development.
The area is run by Rick Rundell, Technology and Innovation Strategist, Start-up Mentor and Senior Director at Autodesk and the facility has really delivered on connecting Autodesk with local academia and innovative developers and has become an in-demand space where digital and physical design technologies can meet and be tested.
We visited the space last year and it was still early days; now there are a number of interesting projects being run in the space, from innovative mould making for large scale forms, using robots to 3D print / extrude and stretch tetrahedron-based lattice forms to 3D printing components for historical facades which are being refurbished in the city.
Leica BLK + Autodesk ReCap
There is been a lot of hype around Autodesk’s co-developments with Leica for its new portable laser scanning system the BLK 360. First shown at Autodesk University 2016, the BLK 360 is possibly the sexiest laser scanner ever made, if there should be such a thing.
The device is incredibly small and will fit into a bag and is the first ultraportable laser scanner ideally suited to scanning the interiors of buildings. Autodesk and Leica have worked together to create a relatively low-cost combination of portable scanner with Recap running on Apple’s 12” iPad Pro. The combination enables firms to arrive at location and quickly carry out multiple scans while collecting the data and checking scans on the iPad Pro. This helps firms ensure the laser scan data is complete with no holes in the model before anyone leaves the site.
To see the BLK 360 and Recap work together we visited wework in downtown Boston, a company which hires office floors or whole buildings in major cities around the world and converts them into shared co-working and hot desk environments. This impressive company uses Revit, standardised fit-out with laser scans to rapidly assess buildable space and return on their investment prior to signing any lease. The company regularly sends out employees with large laser scanners to capture potential new sites with one employee saying they made over 200 site visits last year to scan and collect 3D data. The new Leica BLK 360 and iPad combination will save considerable luggage space and effort, and they’ve been very happy with their trials so far. The accuracy of the Leica is to within 4-6 mm, which is good enough for modelling. While it was hoped that the machines would be available by now, they are still under pre-order on the Leica website, so there is still some work to do. We can’t wait to get hold of one of these to test.
wework is a great example of how BIM can be used to provide tactical advantage over competitors. BIM isn’t a technology, it’s a process and the company has continued to refine its process to enable rapid modelling of potential new sites. This not only identifies the buildings with the best business potential but also brings forward the ordering of components, accelerating fit and finish.
This rapid turnaround has enabled the firm to grow quickly in and beyond the major centres of business. The company aims to build communities of workers in their very funky spaces and I was especially won over by their supplying of free beer!
Skanska 121 Seaport
Near Boston’s North End, the Seaport region has become a very busy construction site for many office buildings and condos. Since the city courts relocated to the area there has been an explosion of investment and interest in creating a masterplan to turn this previously neglected harbour area to mixed use.
The net result of this is 2.8 million ft.² of residential, 1.2 million ft.² of office space, the same again for retail, together with 860,000 ft.² of additional hotel space and a quarter million ft.² for civic and cultural spaces.
One of the companies heavily involved in redevelopment of the area is Skanska and we visited its headquarters to hear about some of the projects the company was involved in – as well as a little about their BIM process.
A case in point was 121 Seaport, the 17 storey 400,000 ft.² office building, a platinum LEED design which features outdoor spaces such as rooftop terraces, a pedestrian-only 50,000 ft.² retail promenade, a fitness centre and access to the Boston Underground. To talk about the process, Skanska had assembled a team which worked on all aspects of the design. The owner and commissioning firm was Skanska itself and, unsurprisingly, it used Skanska to build the office block, with architecture firm CBT doing the design work. #
The building site was itself an issue as in the top corner it overran the Boston subway, which meant that it was impossible to drive deep piles in parts of the site. CBT decided that the form of an ellipse would help in overcoming some of the site’s limitations, but in the process it discovered that the form factor also benefited, spreading wind loads on the structure. It also became a sales point in a very rectilinear part of the Boston skyline.
The teams talked about how they collaborated and used BIM tools such as Revit, Navisworks and VR to drive the process and expedite completion.
Skanska’s expertise in 4D has enabled and accelerated construction time which drives an expedited opportunity to rent the office space.
MEP and Fabrication
The Boston Seaport area is not only a regeneration project for offices and houses but also for fabrication and industry. We visited ‘Building 16’ to meet one of the largest local mechanical construction firms, Cannistraro, headed by CEO, John Cannistraro, which had acquired the lease on the historic building originally constructed in 1940 by the U.S. Navy.
Cannistraro is in the process of consolidating four fabrication units into one, with this giant 157,000 ft.² building on the waterfront bringing everything under one roof and close to where a lot of the building work is taking place.
The first part of the process though, is to rehabilitate the building and bring it back from decades of neglect. Built by the US Army Corps of Engineers, it’s impressively over engineered.
Cannistraro began utilising BIM in its earliest forms in the early 2000s, and expanded its use each year. The use of BIM for off site prefabrication became prevalent across the organisation and on all projects by 2008. The company became known in the industry as an early adopter and advocate for the use of BIM, early collaboration and alternative delivery methods such as design assist and IPD.
Today Cannistraro employs over 30 coordinators and designers in its BIM group as well as an in-house VDC (Virtual Design & Construction) group for file / model management, maintaining BIM standards, as well as quality assurance.
Cannistraro currently uses Autodesk fabrication CAD MEP, as well as Navisworks and BIM 360 Glue, and is increasing its training and usage of Revit. The company also owns various tools that supplement its BIM-enabled fabrication efforts including Trimble total stations, 3D laser scanners, a HoloLens headset and manufacturing / scheduling tools including FabPro and Touchplan.
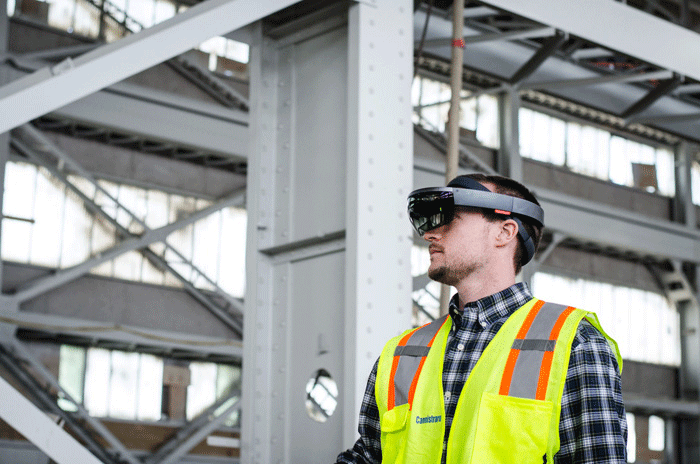
While we were in Building 16, Jim Lynch, Autodesk’s Vice President, BIM Product Line Group, gave a presentation on Autodesk’s commitment to connecting BIM to digital fabrication. In the manufacturing space this has already been a great success but that revolution has yet to come in AEC.
By making a move to creating accurate models, the downstream benefits have yet to be realised. Autodesk has technology in both AEC and in manufacturing and is committed to sharing that expertise between verticals. The obvious meeting point for that is in MEP fabrication, modular construction – any job that requires complex shapes, material cutting or shaping.
Through Project Quantum the data will be made available in whichever application is applicable to the task, with the data seamlessly moving between trades providing the level of detail required at each development stage.
Perkins + Will
The final session was given by Dr John Haymaker, Director of Research at architecture and design firm Perkins + Will (P+W) who evaluates new technologies and heads up its incubator program, along with 9 research labs around the world.
Haymaker feels that we are at a watershed moment for architecture and data is changing everything. It’s not just helping P+W better refine and design towards objectives like cost and schedules, but also water and energy consumption. It’s becoming performance-based design and the risk is being shifted to contract and delivery.
Haymaker said, “We have to decide if a building is the best it can be along many different performance metrics. We are reaching the human cognition, we are at our limit of how many objects we can consider – alternatives, systems, materials. We need computational assistance. We aren’t using computational design to replace any of our 2,000 designers, we want to enable cyborg super designers and design teams! ”
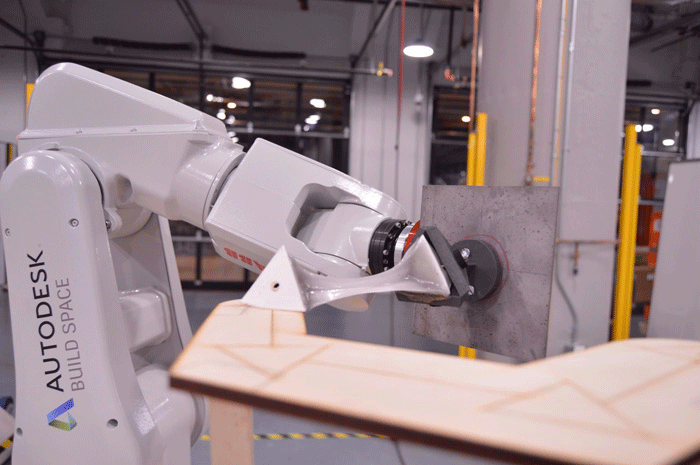
P+W has built up in-house research labs with experts in process, efficiency, material performance, urban water issues, design resilience, mobility (transport), society, and human experience.
The many competing issues which face designers fascinate Haymaker. Performance-based design needs to trade off these competing issues to maximise the best outcome that meets the most important criteria. The traditional route is to come up with various resultant designs which are then analysed for how best they trade off against the competing criteria.
Today’s methods are just not good enough at defining what all the alternatives are, or how well we measure them up.
Haymaker thinks in terms of Design Spaces, which he started while at Georgia Tech. He defines them as being BIM models plus the environment around them and multiple BIM models that might fulfil the brief, as well as the stakeholders and decision makers and the objectives, preferences for trade-offs, the constraints.
After formulating the outlying parameters, it is easier to derive computational algorithms which can then create thousands of alternative designs within the defined trade off.
P+W is also experimenting with new fabrication technologies, such as composites, 3D printing and robots, using CNC milling to make moulds for complex geometrical panels. The idea is to show contractors the design intent to provide guidance. Thermoplastics are another area of interest where, after heat is applied, robots can pull and stretch the material to produce precise deformations – meshed panels with structural characteristics.
On the subject of materials, Haymaker talked about ‘Tall Wood’ structures and a project that’s intended for Chicago. It’s led to experimentation with modular designs, material sourcing and onsite fabrication. P+W has spent some time in Autodesk’s Build Space to create test modular components for the building.
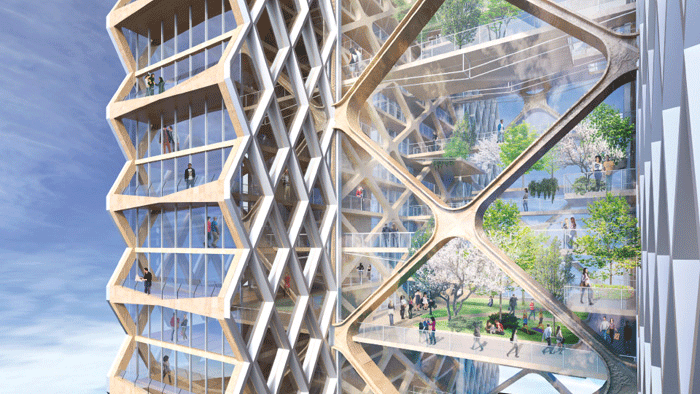
Conclusion
With so many talks and site visits, the Boston event really was an incredibly intense three days. The message was consistent and strong: while Autodesk is improving its desktop tools, all destinations for that data will be on Autodesk’s cloud and that is where a huge effort is being placed.
Third-party developers are being encouraged to develop for Autodesk’s cloud and for customers to get the promised benefits of a common data environment – collaboration and powerful simulation / mobile access and lots of compute power – having data on a desktop is not going to cut it.
However, for customers that are not happy with a subscription-only option or having to rely too much on a single vendor, this could be less than brilliant news – as Autodesk won’t just own your design weapon of choice but will own your company’s design process.
The question will be if the benefits provided outweigh the concerns. I have to admit that Autodesk’s vision of BIM-cloud-utopia does sound compelling and it has seemingly identified the key problems. The devil will be in the details and one wonders how generous an eco-system will be in adapting to different processes of customers. Then there’s also the fear of future price hikes and no way out.
While a lot of BIM is about software development and usage it’s clear that, with advances in mobile computing, the cloud and big data, software and hardware are becoming better integrated and seamless.
For such a long time we have been concerned with moving from 2D drawings to making models and enjoying the advantage of co-ordinated output of drawings when edits are made. This truly pales into insignificance when one considers the revolution of a move to true, end-to-end digital construction and fabrication – design construction firms are driving this development forward at considerable pace.
Out of all the software developers, Autodesk is perhaps best placed to deliver on that digital / physical connection, being the only significant AEC developer with feet in both the construction and the manufacturing sectors.
If you enjoyed this article, subscribe to AEC Magazine for FREE