Building analysis and design tools verify Russian code compliance and Leadership in Energy and Environmental Design (LEED) eligibility.
As Europe’s largest metropolitan area, Moscow has experienced booming business development and population growth that has produced record rates of traffic congestion, daily fuel consumption, and pollution. To combat this, developers are building new sustainable workspaces in suburban areas that offer workers shorter commutes and lower associated costs.
The $770 million K2 Business Park designed by Korda/Nemeth Engineering has earned internationally recognised Leadership in Energy and Environmental Design (LEED) certification for employing performance-enhancing building strategies. Located outside Moscow in the Leninsky District, the office complex features three pairs of buildings sited over massive underground parking structures. Each seven-storey building offers 17,500 square metres of rentable space plus two below-ground parking levels totalling 21,500 square metres.
The sophisticated design distributes upscale amenities throughout the ground floors, including fitness centres, banks, conference facilities and retail areas. Cafés located above the ramps to the parking garages connect each pair of buildings. The architect, NBBJ, united the six distinct structures as a single office complex by designing the exterior to look like a brick garden wall that has been parted to allow for pedestrian and vehicular traffic.
To conserve natural resources and earn LEED credits, Korda/Nemeth Engineering used several green design strategies throughout the complex. High-efficiency natural gas boilers were used to heat water with less fuel; occupancy sensors were installed to turn lights on/off to conserve electricity; and natural daylighting was used to reduce the artificial lighting. Building analysis tools were used to optimise the design of these energy-efficient features — as well as the exterior envelope, walls, roof, and glass — substantially reducing the amount of heat transfer and reducing fuel used for heating and cooling.
One critical conservation feature was heat recovery from the ventilation system. Air handling units provided 100 percent outside air for ventilation and exhaust fans. “In a traditional 100 percent outside air system, the energy used to heat or cool the ventilation air is wasted when it is exhausted from the building,” explains Korda/Nemeth Engineering structural engineer and software manager Kristin Molnar. “To recover that energy on this project, a heat recovery coil was installed in both the exhaust ductwork and the outside air intake ductwork for the air-handling units.”
The heat recovery coils and connected piping are filled with a glycol solution, and pumps circulate the solution between the coils. During the winter months, these coils transfer heat from exhaust air (which is typically 21ºC) to the incoming stream of outdoor air (which is often well below -20ºC), warming it and reducing the energy needed to bring it up to indoor temperatures. Similarly, during the summer months, heat from incoming outdoor air (35ºC on a typical day) is transferred to the exhaust air to reduce cooling costs. The year-round cost savings are substantial, more than justifying the extra costs of design and construction.
Restrictive building codes prompted the project team to innovate in other ways as well. “One obstacle we encountered was inadequate room in the technical penthouse,” says Mr Molnar. “We were not able to find room for boilers that we would normally locate there.” As an alternative, boilers were placed above the ramps to the parking levels.
To limit the amount of mechanical equipment running through rentable space, the main runs to feed the office building were located in the first parking level below ground. This resulted in a large volume of ductwork, piping, and electrical conduit that needed to be co-ordinated with the complex floor system. Routing these services was fraught with hazards, however. Placement of Heating, Ventilation and Air-conditioning (HVAC) ductwork and Mechanical, Electrical, and Plumbing (MEP) pipes and lines in the first parking level could affect fire truck access and exceed code limitations.
The designers turned to Bentley software to aid decision making, automate code compliance, and facilitate communication with the local authorities, which require the use of design software certified in the Federation of Russia. “Expertisa, the local reviewing authority, requires the use of STAAD.Pro, so we used that along with the RAM products,” explains Mr Molnar. “This allowed us to submit design documents and detailed calculations directly to Expertisa.”
The Korda/Nemeth Engineering team also used STAAD.Pro’s library of design codes to import Expertisa requirements and prevent unwitting code violations. “With STAAD.Pro, we were able to design all the concrete columns and beams using the Russian code standards.”
Bentley products saved time by enabling direct communication between RAM Concept and RAM Structural System. The team was able to do an overall structural analysis, given the imposed lateral loads, while exporting the floor plate geometry to RAM Concept for analysis of the slab system. “This meant we didn’t have to model anything twice,” Mr Molnar says. The rapid analysis also enabled the team to quickly settle on reinforced concrete two-way slab construction with drop panels, which reduced the reduced floor-to-floor heights and eased car access concerns.
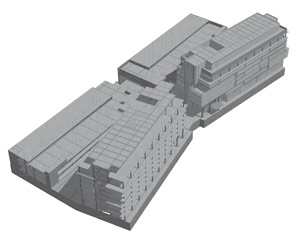
Bentley Navigator was used to co-ordinate design with several subcontractors. The MEP contractor, for example, used Autodesk products, and its models were imported without difficulty. Within Bentley Navigator, Korda/Nemeth Engineering staff analysed the models for interferences and produced visualisations for the MEP engineers. “The ability to plot to a 3D PDF allowed us to quickly generate a file that could be read by all concerned stakeholders with the free Adobe software,” says Mr Molnar. Interferences were easy to read thanks to saved views, which could be selected from drop-down menus.
“With the extensive library of structural analysis software available to us and the ability of these tools to communicate with each other, we were able to save time and money during the design process,” says Mr Molnar. “Due to the software’s ability to check for interferences between models of different formats, we were able to detect conflicts before they got built and could communicate these potential conflicts to other trades to reduce time and money spent during construction.”
Energy-efficient, LEED-certified buildings are essential in today’s resource-scarce world, but they do not get created without highly trained engineers who are able to use increasingly sophisticated design tools. Korda/Nemeth Engineering is working hard to bring along the next generation of professionals with an active domestic and international student internship and co-operative education program. To foster LEED education in particular, Korda/Nemeth Engineering created a LEED manager position responsible for promoting LEED practices, co-ordinating training, and preparing employees for LEED exams.
On the K2 Business Park, Korda/Nemeth Engineering’s expertise — complemented by the right software tools — produced a sustainable project that implemented sophisticated energy-saving strategies while also adhering to local building codes. By dramatically lowering the energy footprint of developments like the K2 Business Park, software tools like RAM and STAAD are improving the sustainability of the built environment, one building at a time.