With a design process that is becoming increasingly 3D, tools are needed to capture existing structures and sites. Laser scanning and ‘point-cloud’ data have been niche technologies but this year’s CAD releases will open up new possibilities, reports Martyn Day.
Computer Aided Design (CAD) revolutionised 2D drafting, with the majority of practices throwing their drawing boards away and benefitting from adopting a digital workflow.
However, design technology and best practice are always being redefined and enhanced to find competitive advantage. Today, ‘being 2D’ only assists documentation, the adoption of 3D is accelerating as it brings designs to life, providing the benefits of co-ordinated documentation changes, the chance to run analysis, create visualisation, provide quantities and even identify clashes before getting to site.
But with the move to a model-based process, everything has to be modelled which can be time consuming and bloat project files. So is there a quick way to capture existing infrastructure and merge it with 3D BIM models?
Survey
There are a number of ways to create 3D models of an existing building in a BIM tool, the slowest route is to perform a traditional survey and create a drawing and then a model. For modelling in context, 2D maps can be referenced and faceless 3D blocks can be used to approximate forms of adjacent buildings – and for some instances, on small projects, this approach is cost effective. But when a large ‘old’ or undocumented building needs to be modelled for renovation or retrofit this approach is slow, lacks detail and is manpower intensive. There is a smarter way.
Laser scanning and optical capture technology enables the rapid and accurate capture of the real world, from vegetation and topology to buildings and infrastructure. Laser scanners shoot a cone of laser light within a space, capturing X, Y and Z position of all the surface instances it hits. These systems work by measuring the time of flight for each laser beam, which can be fired between 10,000 and 100,000 times per second.
The resultant file made of X, Y and Z points is called a point-cloud. These points are often combined with a digital image created by an optical camera, to capture the colour and texture information of the item being scanned. Viewing a point-cloud image from afar is very much like looking at a photograph. It is only when you zoom in that you see it is made from millions of individual coloured points.
To complete a survey a number of overlapping scans need to be performed as areas in shade from one scanning position will not be detailed and lasers are only accurate over a set distance. All the survey data is brought into software, which works from a common reference point to bring together the point-cloud surveys for alignment and registration.
These point-clouds can be extremely dense, comprise billions of points and make multi-gigabyte files that can tax most hardware. Other common laser survey problems include edge definement, which lasers may not hit, highly reflective surfaces and details down narrow ‘gaps’. In these instances some preparation work may have to be done to aid the system, such as placing tape on corners. Laser scans can also not be performed in rain, as the light hits the water and ‘noise’ will be introduced into the point-cloud.
Scan to BIM
It would be absolutely fantastic to scan a building and automatically take the resultant point-cloud and get a parametric, accurate model out the other end. Unfortunately that is nowhere near possible, although people are already working on it.
While the point-clouds produced by these 3D scanners are often not used directly, it is possible to use them for visualisation and measurement. The next task is to convert these points into something more usable and ‘CAD friendly’. The options are to create polygon meshes, NURBS of tessellated surfaces or feature-based solid models. As the complexity increases, the time and the cost unfortunately also escalate, so it is really important to identify exactly what the data will be used for.
Turning point-clouds into meshed models can be useful for visualisation and allow analysis and even CNC machining. Editing meshes is not ideal and the tolerance and quality of any surface is compromised as everything is made up from straight lines. There are many mesh editors out there including Meshlab (which is free), McNeel and Associates’ Rhino and Kubit PointCloud for AutoCAD.
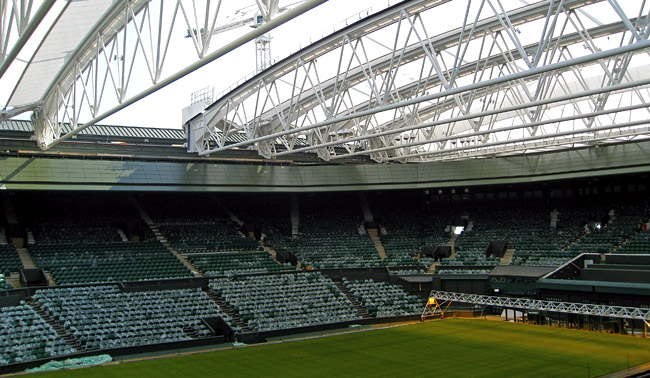
The next ‘step up’ in accuracy is full surface conversion. By converting point-clouds to NURBS or Splines, it is possible to generate quilts of continuous curved surfaces from point clouds. These can be stitched and edited with an array of standard tools, again Rhino, Kubit, Autodesk’s 3ds Max, Maya and Geomagic. Surfacing software has come a long way in the last five years and a surface model is eminently more usable today.
So far the ultimate goal for conversion has been a full solid model but this has been because the majority of companies using scanners have operated in automotive, aerospace and product design. There are no major CAD or BIM tools that produce actual solid models, which are overkill for an AEC system, but this could be used as part of conceptual design process.
Any natural shape or one built in a model can be brought in to CAD to edit, and it is possible to capture that in a point-cloud and add intelligence, such as parametrics to a converted solid model. Products such as Geomagic Fashion will find blends, fillets and features in point-clouds and allow the full power of a solid modelling tool to be used to reshape and refine a scanned object. However, the software is not cheap. Scanning to BIM is perhaps a misnomer as there is no direct software tool to provide that service. BIM is not about geometry, it is more about the information that is attached to the geometry. Point-clouds are just X, Y and Z dots and most of the tools generate CAD geometry.
In areas such as process plant, objects like pipes, valves and cylinders are standard shapes and sizes, it is possible to convert the points to solids or surfaces and find and replace the dumb geometry for intelligent CAD components. Buildings and civil infrastructure just are not as standard. This is not going to stop research into delivering on the concept and there are a number of companies looking at ways of doing this. The two most common methods appear to be mixing the point-cloud with the CAD BIM model to show design or proposed changes in context, or using the scan to produce referenced 2D vector floor plans, from which the BIM model can be quickly generated.
Looking at cost
With a scanning machine priced anywhere between $35,000 and $100,000, these are not the kind of devices that many companies have in-house, but there are many global bureaus that offer a terrestrial-based service, together with aerial, car and train-based scanning.
With such expensive hardware, the software to load, manipulate and convert these huge point-clouds has traditionally cost a pretty penny, anywhere between $10,000 and $20,000 a seat, which has inhibited wide-scale usage in the field of architecture. However, scanning has found a home in richer markets such as oil, gas, mining, and in government funded areas such as civil infrastructure and geo/mapping.
The cost of entry is about to change significantly, with Bentley and Autodesk introducing point-cloud engines and capabilities into their core products.
For Bentley customers, the company is adding the renowned PoinTools Vortex engine to core MicroStation. PoinTools is widely regarded as the fastest tool for manipulating large point-clouds. While Bentley has had an arrangement with Leica and its software technology in the past, the Vortex engine will undoubtedly boost performance. Bentley has many customers in big industry that are already heavily into scanning plant, road and rail infrastructures.
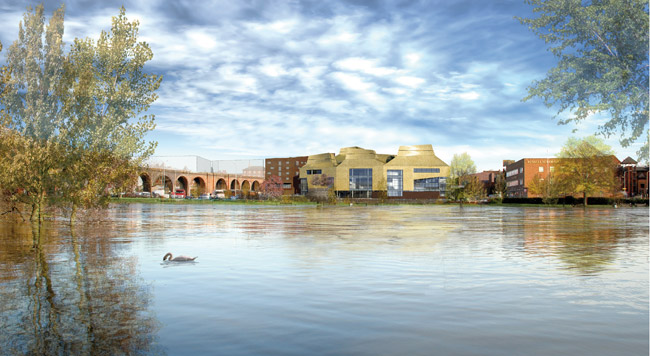
Autodesk demonstrated a new point-cloud engine at its Autodesk University gathering in Las Vegas last December. Billed as ‘forthcoming technology’, it is widely expected to be a core feature of the next release of AutoCAD, which should be available in the next couple of months. In the past, Autodesk had licensed technology from Ambercore for its AutoCAD Civil3D product but the company has decided to write its own point-cloud engine and include it in vanilla AutoCAD. This will be significant as it will add millions of possible point-cloud consumers and is surely also going to be included in the company’s BIM modelling tool, Revit.
At the show, Autodesk teamed up with scanner manufacturer Faro to laser scan the cavernous Mandalay hotel and gave us a fly through of a massive point cloud model. The demo even included conversion to AutoCAD 3D geometry. It certainly set high expectations for graphics performance in the next release, which I suspect will be called AutoCAD 2011.
This is not to forget other CAD vendors like McNeel and Associates’ Rhino, which already has a PoinTools plug in to import and manipulate point-cloud data. With such a diverse range of applications, from jewellery to architecture, customers can bring in scans of existing objects for conversion and manipulation.
Conclusion
In nearly all aspects the scanning and point cloud market is very mature, with advanced hardware and software for an expanding range of applications. The cost of the hardware is still going to remain an issue but with key vendors providing broader access and a lower cost of entry to handle the point clouds, further reductions in cost are expensive. For instance it is rumoured that one manufacturer is trying to bring out a sub $10,000 laser scanner.
CAD systems are now incredibly capable of modelling in 3D, surfaces, solids, meshes. It was only a matter of time before raster point cloud was included in these base level design systems. With Bentley and Autodesk providing extended capabilities in future products, users will have increased options in how they can create and use these 3D models, mixing proposed design with highly accurate existing point clouds. The actual conversion from point cloud to mesh or solids still has some way to go. Companies like Geomagic that have developed powerful point-cloud to intelligent solid models but have focussed on big ticket markets like automotive and aerospace. The ‘Scan to BIM’ market segment only really appeared in 2009 and a lot of research is required to turn a mass of points automatically into a Revit parametric wall, but I do believe that technology is coming.
For now the hardware and software is at least part of the way there, with best practice workflows for architecture still needing to be properly defined. It is not without its issues, with format juggling rife within existing point-cloud projects. Users also rely on multiple software applications and transforms to get the data in the right format for each step of the process. With the main CAD vendors now adding scanned information as a core capability to their design systems I fully expect to see these problems addressed in the coming releases with corresponding expanded use of 3D point-cloud in the AEC market.
PoinTools – www.pointools.com
Leica Geosystems – www.leicageosystems.com
Faro – www.faro.com
Bentley – www.bentley.com
Autodesk – usa.autodesk.com
Ambercore – www.ambercore.com
Geomagic – www.geomagic.com
Meshlab – meshlab.sourceforge.net
Rhino – www.en.na.mcneel.com