The National Digital Twin is an ambitious project to bring new efficiencies to the UK’s infrastructure. Greg Corke reports on the Cambridge pilot project which aims to lay the foundations for a series of federated twins, connected by securely shared data
For infrastructure asset owners, the ‘digital twin’, a virtual replica of a physical asset that keeps in sync with its real-life counterpart, is a compelling proposition. It promises to optimise operations and maintenance and support better decision making when planning for the future.
Creating a digital twin of an individual asset is one thing, but the UK National Infrastructure Commission has a much bigger vision. In its 2017 report “Data for the Public Good” it recommends the development of a ‘National Digital Twin’. The idea is that greater sharing of data between infrastructure assets will deliver huge cost and efficiency benefits. It would use technologies like software analytics, machine learning and big data to simulate the entire UK infrastructure system.
Considering the scale and diversity of data/systems, delivering a monolithic twin for the whole of the UK would be impractical and undesirable. “You don’t want to have a ‘big brother is watching you’ situation, where somebody owns a 50TB model of the UK and they’ve got all the sewer information, the network communication information, all that stuff,” says Bruce Hutchinson, senior consultant, Bentley Systems.
The plan is to create a secure, federated twin, an ecosystem of digital twins owned by different asset owners and connected by securely shared data. These assets/systems would be represented at different levels of granularity. High quality, standardised data and seamless interoperability is of paramount importance. To help achieve this goal, asset owners, mayors and other leaders in the built environment are being guided by the Gemini Principles (tinyurl.com/gemini-twin) when developing their own digital twins.
The National Digital Twin is all about using it appropriately in different contexts, giving users access to the information that they need, but not too much or too little, says Hutchinson. “The Mayor of London is not going to care about a specific pump in a plant room, he’s going to be more interested in flood control – if the Thames goes up what streets will be affected.”
Starting small, the Centre for Digital Built Britain is supporting this national goal by funding a digital twin pilot project at the University of Cambridge, in partnership with Bentley Systems, Topcon, Geoslam and Internet of Things (IoT) software company RedBite.
The objective is to develop a dynamic ‘living’ twin of the Institute for Manufacturing (IfM) building and the West Cambridge campus, demonstrating its impact on facilities management as well as ‘wider productivity and well-being’.
“We want this twin to provide the foundation for integration with wider city scale digital twins and wider city scale data and see what we can do if we have that integrated picture of digital twins across different types of infrastructure assets such as power, water, transport and so on,” said Dr Ajith Kumar Parlikad, research lead of the project, speaking at Bentley Systems’ Future Infrastructure Symposium in London last April. “How can we actually have a positive impact through those digital twins on social and economic outcomes. How do we actually develop a twin that is federated, for example, that is open, that is interoperable, but it’s secure as well.”
The West Cambridge digital twin is different to many other digital twin pilots in that it focuses on existing buildings and infrastructure rather than on purpose-built assets. This presents a broad set of challenges around the creation of the 3D model.
“The building is around ten years old and we never had a good drawing or as-built drawing or model of the building, so one of the things we went out to do was develop a BIM model based on IFCs, – a standardised BIM model – that not only represents the structure of the building but also the components within the building as well. For example, the MEP components, the mechanical and electric components and so on,” says Parlikad.
Bentley Systems played a central role in generating the BIM model of the IfM building. This was then augmented with a highly detailed reality model of the plant room using data captured from a GeoSLAM handheld laser scanner and photogrammetry. Topcon used drone and vehicle-based scanning and photogrammetry to generate a reality model of the West Cambridge campus.
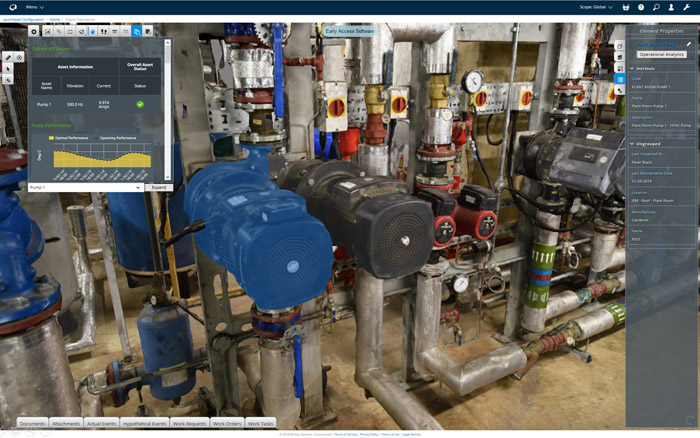
Asset tagging
The next step was to add the contextual layers within the digital twin, classifying objects within the model itself so it’s ‘aware’ of what it is. This includes the creation of an asset register, along with asset identification tags for critical equipment across the IfM. “If we don’t know what assets we have, there is no point in having a digital twin,” says Parlikad.
Parlikad is keen to point out the importance of developing a systematic methodology to define the asset information requirements and to ensure that whatever data is collected meets the organisational objectives. “Often we have a problem where we go around collecting a lot of data without knowing what it is for,” he says. “So this approach ensures that we are collecting the right data in the right way. And through the right asset hierarchy and so on, we can represent the data in the right manner.
” To date, over 200 assets have been tagged within the building. Barcodes are placed on the physical objects and the associated asset data is stored in RedBite’s asset management solution ‘itemit’.
“What these 2D barcode tags allow us to do is not only identify these assets uniquely but if you scan the tag, the app will show us an asset profile which provides all sorts of descriptions about what the asset is, but more importantly asset management data as well,” explains Parlikad. “So, you can see information about when it was last inspected, what the inspection record was, when it is due for inspection next, when the next maintenance is due and so forth. It’s a rich collection of data that you can store on those asset profiles using these tags.”
Users can also input information about the assets and Parlikad’s team has been exploring the use of natural language processing, as he explains. “For any user, given the right level of access, you can scan an asset, say the boiler, and enter in simple plain language like ‘the boiler is not working’ or ‘the fridge is not working’ and so on.”
This would then inform the asset manager, not only that there is a problem with that asset but the prioritisation of that problem.
Researchers are also developing an augmented reality (AR) application for maintenance. The idea is that users would wear a HoloLens head mounted display and see assets behind the ceiling, then tap on those assets to get their status. The plan is to take things further and allow maintenance operators to do fault diagnostics online.
Real-time performance data
One of the key aims of the project is to explore the best way to harvest and analyse data in order to understand how the asset is performing. In the IfM, this is done through the building management system, IoT sensors and devices that monitor and control the condition and operation of critical assets and the environment within.
Close to 60 environmental sensors have been deployed so far, including temperature sensors, humidity sensors, and ones that can monitor whether windows are open or closed.
“We are going to deploy C02 sensors and also occupancy monitors as well, within the building,” says Parlikad. “On top of that there are some condition monitoring sensors that allow us to capture data that is not currently captured through the building management system. So, for instance, we have these vibration sensors that are put on the pumps on the HVAC systems in our plant room.”
To create a central repository for the sensor data and building management system data, everything is being pushed to a cloud database on Amazon Web Services (AWS). This is partly because the University’s local data infrastructure is locked down, but more importantly, explains Parlikad, because the project gives an opportunity to explore how emerging cloud-based solutions can be used within the digital twin context.
Twin platforms
Two digital twin platforms are being used within the pilot. One is developed by Bentley Systems, based on its AssetWise platform, and the other is a BIM IFC-based digital twin platform that has been developed in house.
Parlikad explains the reason behind this dual platform approach, “We want to be able to show that if we have the right data and if we export and exchange the right data in the right form, the ability to exploit the data does not depend on a specific platform,” he says. “As long as the data is exchanged in a standardised way, we can explore different ways in which we visualise this data through different platforms.
“This is also an opportunity for us to explore two different pathways in terms of research – whether to go on a ‘geometric modelling BIM IFC pathway’ or a ‘realistic modelling pathway’ [using reality capture],” he adds.
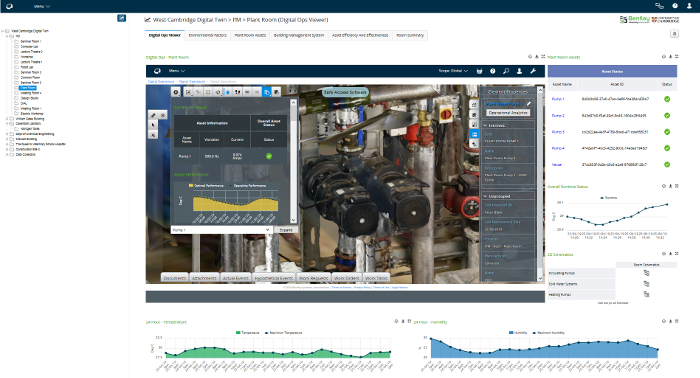
Of course, physical assets are continually changing so the project will also need to explore how the model will be updated over its lifetime. To plan for this, the site has been broken down into a number of replaceable tiles. Some are smaller than others, depending on the density of information within them.
For new buildings, an as-built BIM model might be the obvious choice, but Bentley believes reality capture has a very important role to play. Hutchinson cites a Bentley R&D project that allows a service company to easily capture assets when digging a hole in the road. A GoPro camera is attached to an excavator boom via a custom rig and the videos are then fed into Bentley ContextCapture to produce a mesh showing the exposed pipes, as well as the surrounding manholes and drains.
There are important lessons to be learned about data visualisation but, as Parlikad explains, it’s of no use if you can’t exploit the data to drive decisions. With Bentley’s platform, data from the environmental sensors is pushed into AssetWise every minute, along with data from the building management system. This is then fed into AssetWise Operational Analytics with a view to giving insights into the data and the ability to predict asset failures or operational events.
Through a web portal, users can access operational data via a series of custom dashboards with key performance indicators (KPIs). Depending on the permissions or role of the end user, data can be presented in different ways to convey different operational and reliability stories. Everything is fully customisable.
Through a hierarchical tree, users can explore all rooms and assets within the building, but the system also offers a model first view, where users can navigate, much like in a video game. “You can interact with the assets in the room, you can click on them and get a picture in picture idea of what’s happening with that asset at any one time,” says Hutchinson, adding that you can also click to see what’s happened in the past and then predict what will happen in the future. This could be predicting the failure of the boilers within the plant room or monitoring the vibrations coming out of the pump to detect any anomalies.
Safety operating envelopes can also be created to monitor assets during operation. If an asset is working fine, for example, then a green tick could be displayed on a custom table in the dashboard. But if it goes out of pre-defined limits then an alert could be sent by email or text. To date, the project is restricted to analysis and reporting; it hasn’t gone so far as to create control systems that can interact with the assets directly.
The West Cambridge pilot has now been collecting sensor data every minute for over a year, which Hutchinson says gives a good dataset for predictive maintenance.
“What we need to work on is the idea of machine learning and algorithms that Cambridge University are looking at, so if we were to click onto an object, what is its predicted failure rate, is the bolt loose, is it vibrating too much, is it too hot?” he says.
Scaling up
So far, the West Cambridge project has focused predominantly on the IfM building but it is now starting to extend its reach. Working with Smart Cambridge, researchers have been exploring how a city level digital twin could deliver benefits to citizens and to the council.
By looking at traffic data, for example, that the city has been collecting through sensors and through automatic number-plate recognition (ANPR) cameras, the city-level digital twin can be used to predict the impact of different scenarios. This could be how a new housing development might affect the traffic across the different parts of the city, or how the increased use of electric vehicles might impact the energy demand because people will be charging their vehicles at home or at work.
The future
Over the next two years, there are plans to add sensors for things like traffic monitoring, air quality, parking and vision-based condition monitoring of the road surface. There’ll also be an increased focus on data modelling, further research into IFCs, how GIS data and BIM data can be combined and how reality models can be made more object oriented.
There are also many questions that need to be answered, as Parlikad explains, “How do we reduce the cost of maintenance through predictive maintenance, remote diagnostics and so on, how do we reduce the cost of operations by reducing energy consumption and developing performance management apps that allows us to compare the performance of boilers across the different buildings in the campus?”
The pilot will also seek to explore how digital twins can improve citizen level outcomes across cities through things like traffic modelling or air quality modelling using C02 sensors.
But most importantly, the project needs to move away from simply looking at assets and into large scale systems and national level digital twins.
The success of the National Digital Twin project hinges on its ability to bring together multiple, secure, plug and play digital twins seamlessly in one interdependent, dynamic system. “How easy is it for one organisation to say, yes we have developed a digital twin of our asset, [but] can we plug our twin into the city twin at all?” says Parlikad. “I don’t think we can do it now so we have to explore how we can.”
If you enjoyed this article, subscribe to our email newsletter or print / PDF magazine for FREE