London-based Marks Barfield architects is using Gehry Technologies Digital Project (DP) technology to enhance tourist attractions in this iconic world city.
Located on the bank of the Thames as it flows through one of the worldÝs leading tourist cities, the London Eye is an iconic and world-renowned structure.
The Eye was designed and recently sold by Marks Barfield architects. The London-based firm is well-known for its iconic designs. It was instrumental in the newly-opened Treetop Walkway at Kew Botanical Gardens and is currently working on an 170 m vertical pier on the Brighton seafront, where the popular and historic West Pier was previously located. A circular chamber will raise 170 people at a time to thrill at the spectacular views that i360, as it has been named, offers.
The company combines design creativity and engineering in ways that attract millions of visitors to the UK every year. Chris Smiles, associate at Marks Barfield, explains: ýOur practice develops unique propositions that combine multiple and interconnected functions of design, engineering, commercial and structural considerations including ground engineering, aerodynamics and deflection along with support analysis and complex mechanisms.¯
The firm uses Gehry Technologies Digital Project (DP) technology, supplied by UK VAR, Desktop Engineering. Chris Smiles says: ýWe have been using Digital Project for two years and found that its parametric functionality allows us to rationalise designs taking all of these considerations into account. This is crucial because our designs have a primary reliance on mechanical and structural analysis and because of this, a great number of changes inevitably occur before a final solution is achieved.¯
Group ticket
Marks Barfield has seven employees trained to use DP and has benefited from support in this and other routes to best practice from Desktop Engineering (DTE) which, with its multi-industry customer base is able to deliver the most appropriate methods from aerospace and automotive engineering to the AEC sector.
DTE managing director Geoff Haines says: ýDP was developed from Dassault Syst?mes Catia technology by Gehry Technologies to deliver advanced design-to-manufacture technology to architects and structural engineers. It is enjoying considerable success among leading practices including Arup, Zaha Hadid, SOM, Allies and Morrison, where parametric 3D-based model technology secures a better outcome from better designs.¯
Having produced a finished design DP is used to communicate to fabricators, contractors and detailers using formats best-suited to their work practices. Designer, Yan Gao spoke about this aspect of the process: ýThe ability to communicate to our supply chain is crucial to ensure that our design intentions are realised in the final structure and that inputs from consultants are efficiently rationalised and communicated in the design.¯
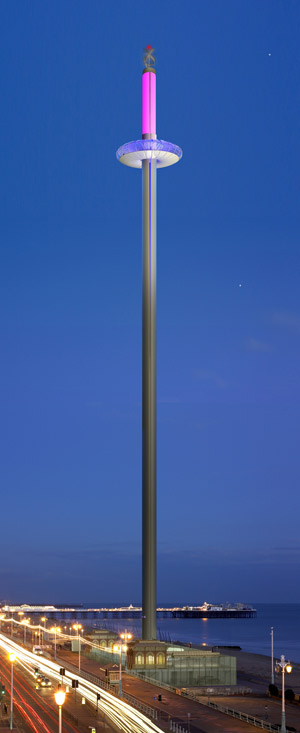
Chris Smiles adds: ýAccurate and timely communication of design iterations and their impact on the final form allows us to make better decisions that are based on more complete and precise information. This provides more design options and greater flexibility. DP effectively keeps you in the picture.¯
Branch and root review
One example of the efficient use of DP is found in the development of the Kew Gardens Tree Top Walkway where the use of inverse kinematics enabled the optimum location of pylons and the chain of bridge sections that link them together into a 200 m tree top tour.
There were many constraints in the project not least having to avoid damaging the roots of nearby trees, which had been previously mapped using radar. The parametric capabilities of DP allowed the design elements to act in a symbiotic relationship. This enabled the designers to move one element and have others react to the change logically and within the design constraints that the overall scheme demanded.
DP methodology also allowed the walkwayÝs bill of materials to be reduced through standardisation of components and this in turn reduced project completion time to just nine months.
Yan Gao says: ýOur experience of DP is that it increases design productivity by 30 percent to 40 percent, allowing us to meet tight deadlines and bring in contractors much earlier than otherwise possible.
ýThat enables concurrent working practice by allowing contractors to start their work sooner.
ýThis brought particular dividends in the design and fabrication of the complex trifurcated pylon design, which could not have been easily resolved using traditional methods since it required input from several parties and resulted in many design iterations. Without DP this would have demanded a much greater resource and increased the total project cost.¯
Another example of the benefits that have been derived from this technology is found in the Rhizotron ¾ a subterranean space that allows visitors to see tree roots. Its inclined concrete surfaces could not be communicated using traditional techniques. With DP and its 3D imagery the buildingÝs fluid lines could be understood and built without compromising the design.
Marks Barfield is making full use of DP to design and build more attractions on a grand scale; i360 being next. As a practice that has strongly focussed on sustainable design DP helps by enabling a better use of resources with less waste, facilitating designs that reflect and communicate this vision.
Desktop Engineering: www.DTE.co.uk
Dassault Syst?mes: www.3ds.com
Marks Barfield: www.marksbarfield.co.uk