Greg Corke reports from Autodesk University where construction took centre stage as Autodesk re-invents itself as the end-to-end AEC company.
Over the past 18 months Autodesk has been on a shopping spree like no other in its 37-year history. With the acquisition of big-ticket software firms like PlanGrid, BuildingConnected and Assemble Systems, the company is betting big on construction and cloud-based collaboration. It now has new capabilities in mobile construction management, bid and risk management, as well as takeoff, estimating and scheduling. However, the area in which Autodesk is looking to dominate already has many players all trying to do the same thing, such as Trimble and ProCore.
As a company, Autodesk looks very different to the laser focused design software firm it used to be. It now has a comprehensive portfolio of technologies for architects, engineers, contractors and owners that touch the entire construction process from concept all the way through to operations.
Of course, when any software developer acquires so many disparate technologies, it’s always going to have a huge job on its hands to deliver an integrated solution while keeping its new customers happy. At Autodesk University in Vegas last month it took the first steps on the long road to delivering a cohesive technology stack.
The big news was the official unveiling of Autodesk Construction Cloud, which essentially brings together Assemble, BuildingConnected, PlanGrid and BIM 360 (Docs, Layout, Ops, etc.) under one umbrella. While the majority of these tools are focused on contractors, and were developed mainly for US-based processes, Jim Lynch, vice president and general manager of Autodesk Construction Solutions made the point that Construction Cloud isn’t just about construction. It actually connects the entire project workflow, he said, which is why it’s also important to architects and engineers.
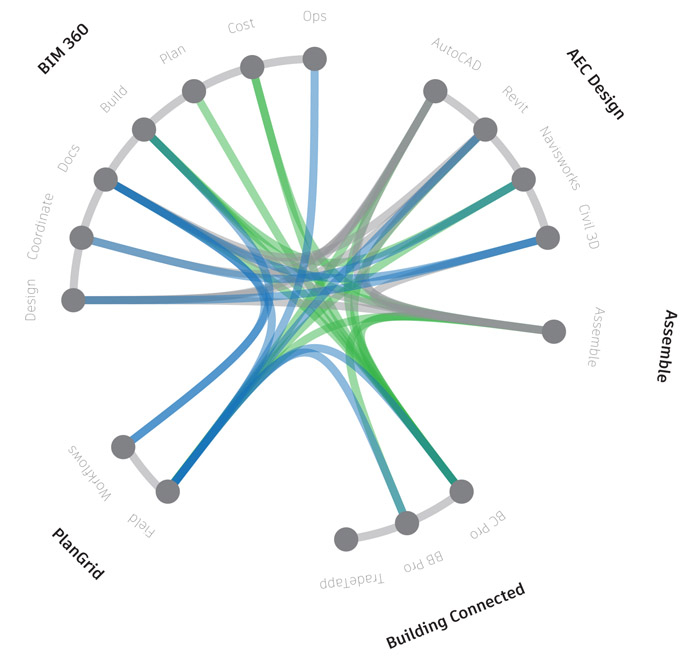
As the Autodesk mantra goes, it’s ‘design, plan, build, operate’. In practical terms, it’s about making critical data available to anyone who needs it along that path.
“You can start in your authoring tools, collaborate across the team during design, push plans and models to pre-construction for procurement, coordination, and quantity takeoff. And once you’re ready, directly push that data to your teams in the field,” said Lynch.
Of course, for this to happen, data needs to flow seamlessly, and Lynch believes connectivity is the most important part of Construction Cloud. “There are a lot of great technologies in the market in the construction technology sector that deliver meaningful productivity gains in a specific area, but it’s really when you thread these things together it creates workflows that deliver the real value.”
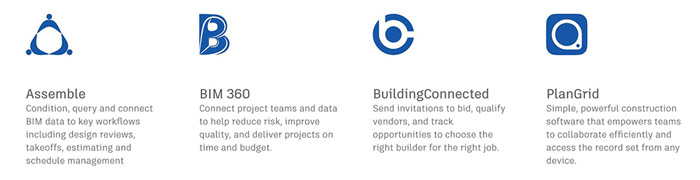
On a technical level, Autodesk has started to create connections between its key technologies. During the AEC keynote, Allison Scott, Autodesk’s director, head of construction thought leadership & customer marketing, who previously worked for Skanska, ran through some of the recent developments.
With Navisworks Publisher for Assemble, she explained how teams can now bring coordinated models from design review software Navisworks into Assemble so they can be used for estimating, scheduling or other downstream workflows. Importantly, all data is accessible onsite through the Assemble mobile app.
Autodesk is also aiming for tighter connection between the ‘plan and build handoff’ with a new BuildingConnected to PlanGrid workflow, as Scott explained, drawing from her own experiences in industry, “Models, plans, estimates and documents are often manually uploaded into project management tools – I remember this. This is a time-consuming process that can result in missing files and data errors. So now, with a simple push of a button, you can automatically send preconstruction files from BuildingConnected to PlanGrid.”
Scott explained that companies are already benefitting from this new workflow. For example, global consulting, design and construction services firm CRB can now ‘seamlessly transfer complex data from the design and planning phase into the hands of the workers on the site.’ According to Scott, the company estimates this integration will save them at least two weeks of work on every project and help them improve communication with their subcontractors.
But it’s not just cloud to cloud. PlanGrid BIM is designed to allow users to access BIM data from Revit, in either 2D or 3D, directly within PlanGrid on mobile devices, the idea being that construction teams can get quicker access to models and metadata to get a better understanding of design intent.
Autodesk has also been linking up its core tools, connecting Civil 3D to BIM 360 Design. Autodesk AI development manager Racel Williams made the point that, when combined with the existing Revit Cloud Worksharing capabilities, this will benefit firms who design airports, railway stations, and other complex projects with both vertical and horizontal structures.
Autodesk also has the added challenge that there is some overlap between its products. PlanGrid and BIM 360, for example, are both used during the build phase for project management and collaboration on site, something that Scott acknowledged in her presentation, “We’re being extremely thoughtful and understanding the capabilities that you know and love in each of these solutions, and we’re focusing on strengthening their ties,” she said, adding that the new PlanGrid Connect integration platform has deepened the connection between office and site, while still allowing users to work in either BIM 360 or PlanGrid.
“Now, you can automatically sync documents, drawings, issues, tasks, and more between BIM 360 and PlanGrid,” she said. “Information can be created and shared from BIM 360 and directly pushed to PlanGrid users in the field and PlanGrid users can now take the custom field reports they’ve created and automatically save them back to BIM 360.”
The integration between these two tools is not just for site work. It has also been extended to operations, to help better support building maintenance.
“BIM 360 Ops users can easily manage work order tickets created from PlanGrid,” said Scott. “So, as a building manager is walking a facility, they can create an issue on the as-built plans using PlanGrid on their mobile device, and a ticket is automatically created in BIM 360 Ops for tracking and resolution.”
In a heavily fragmented industry, Autodesk has a very ambitious vision for Construction Cloud. In order to deliver on this vision, it not only needs to nail the issue of data mobility through optimised workflows, but it faces a huge challenge in terms of education. With the breadth and depth of its newly acquired technologies, it will take time and investment to get the most out of the software. And, in many cases, firms will need to undergo huge cultural change to move away from long established paper-based workflows.
Autodesk also acknowledges the challenge of working with firms with proven digital processes and the importance of taking small steps, as Scott explained during the AEC press conference. “We have customers that are really using Assemble in a way that’s very effective for them. We can’t change that. But how do we extend and improve upon that? How do we extend and improve upon the way that teams are using PlanGrid? How do we extend and improve upon BuildingConnected and BIM 360, and then begin to connect the ways they talk to each other, so that we’re not disrupting the way that they work?
“We’re just making it easier for them to their day jobs, and also in some cases uncovering new ways of working, they didn’t know possible.”
Industrialised construction
In this magazine we’ve written a lot about the growing trend for offsite, modular or industrialised construction and the lack of tools fit for purpose. According to Lynch, Autodesk Construction Cloud will become the foundation for the convergence of construction and manufacturing, enabling the seamless flow of data from design, to fabrication, and ultimately out to the job site. Autodesk Inventor, the company’s primary manufacturing software tool, looks set to play a key role, with the company working on a connection with Revit.
There are many challenges ahead and Autodesk is working on answers to three in particular: how does a design team approach a design when they know how it will be constructed or fabricated, how do you get the level of detail required for the shop floor and how do you manage the installation or assembly? Autodesk has technologies that can handle all of these, but they’re not yet connected.
Modular Construction was one of the key themes for the opening keynote with Andrew Anagnost highlighting one of the most ambitious modular projects currently in progress, the AC Marriott New York Hotel in Manhattan. At 26 storeys when finished it will be the world’s tallest modular hotel, comprising hundreds of individual steel-framed modular rooms. Each room gets fully fitted out in a factory in Poland, including all finishes, furniture and equipment, before being taken to site and stacked much like shipping containers.
New York City construction company Skystone is leading the project. The company used Revit to develop a library of parts that can be mixed and matched to spec using ProjectFrog’s KitConnect service, which is built on Autodesk Forge.
Skystone uses KitConnect to publish component libraries to the cloud, from where they can be assembled and configured into a single central model, as Autodesk CEO Andrew Anagnost explained, “So if a component like a window is swapped out, the Bill of Materials for each module remains consistent and accurate, because the changes propagate to the Revit model, and to any other tool referencing it, like BIM 360, which Skystone is using to share 3D documentation across all phases of the project.”
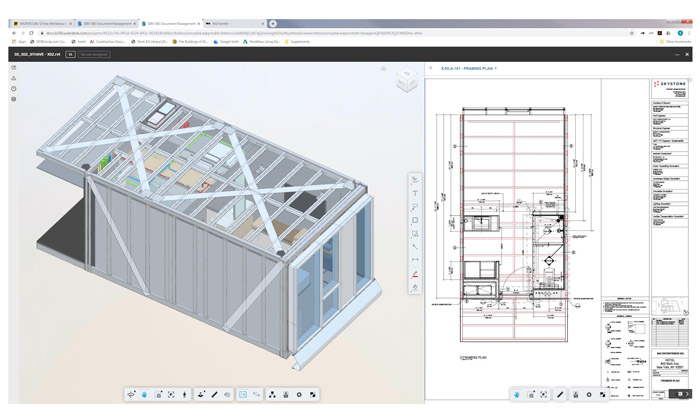
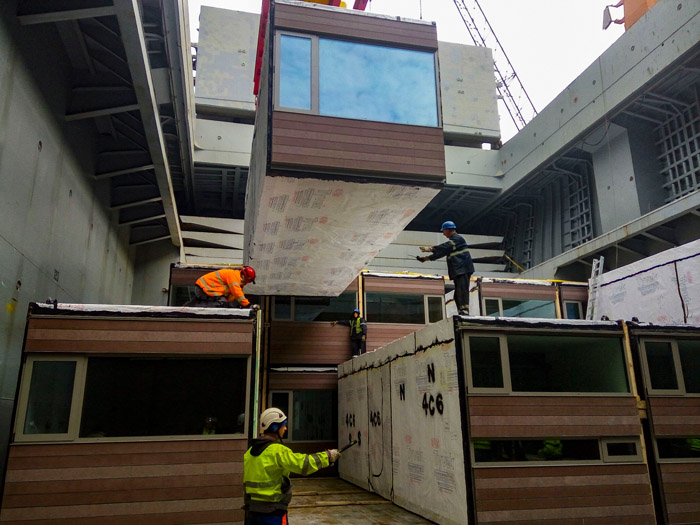
Skystone has also recently started using Assemble. At the moment it’s just to identify when materials have arrived at the facility and to mark off when modules are complete, but there are plans to use many other aspects of the software in the future.
In the factory, robots are used to weld the steel frames, but the rest is done by hand. The biggest benefit to this offsite approach is that work can be done in parallel, so the building’s concrete foundations and core can be constructed on site while the modules are being manufactured in Poland. This means a rapidly accelerated, more predicable construction process and one that creates less disruption and noise on site.
Looking to the future, because of the technology stack that Skystone is using, and the rich information held within the models, the company would be able to give a quote with detailed pricing for a similar hotel with different room configurations in three days or less.
Generative design / design automation
Few would deny that there is huge potential for generative design in architecture and engineering, especially when it comes to optimising designs for multiple, often competing criteria, like costs and performance.
Autodesk has offered the technology in various forms for nearly ten years now, but it’s never gone mainstream in its customer base. One of the reasons for this is strong competition from Grasshopper, the Rhino-based visual programming tool, but also because generative design software is often not that easy to use, as Williams explained, “Many generative design tools out there can be really hard to leverage because they typically require you to know how to code or understand special terminology, or how a genetic algorithm works.”
Autodesk is now looking to change this and make generative design more accessible, and not just for those who know how to code. It’s working on a beta technology called Project Refinery, which is integrated into Revit.
During the AEC keynote, Williams gave a demonstration showing how a designer could perform a massing study to explore the allocation of retail versus office space – the key aim being to minimise cost and maximise rentable area. The software presented the options in a design grid, complete with 3D thumbnails that can be individually rotated, zoomed and panned. To dial into the details, the inputs and outputs were displayed in a Parallel Coordinates graph. Project Refinery looks like a very interesting technology and one that we will be taking a closer look at next month.
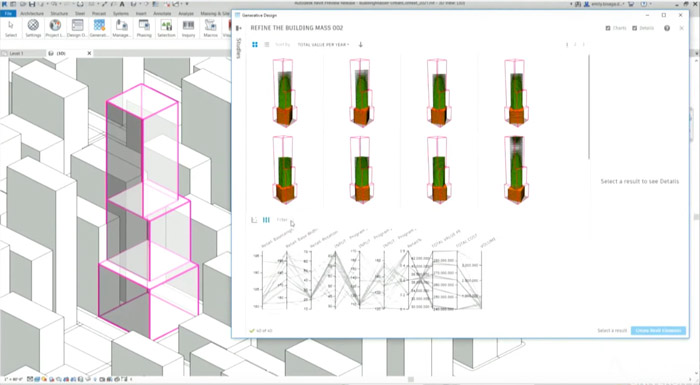
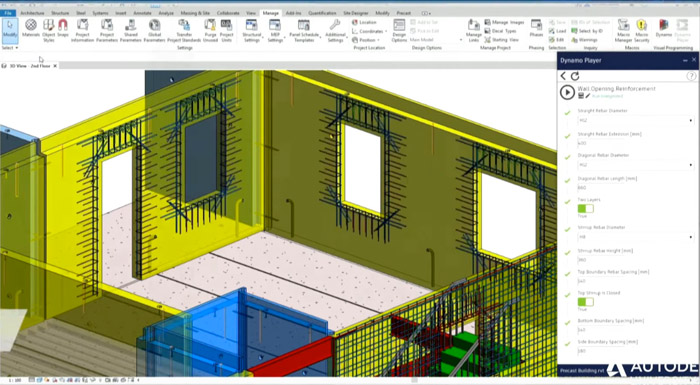
Generative design also featured in the opening keynote with Anagnost focusing on how Airbus is using the technology to optimise a new factory for installing engines. Anagnost explained that Airbus turned to generative design because of the challenging plot of land on its Hamburg campus, which was triangular and smaller than it would have liked.
On a building like this, form always follows function, so Airbus identified ten different sets of variables to optimise for, covering the social, environmental, financial and operational aspects of the design, including the flow of workers and parts throughout the factory. The study generated hundreds of options, which Airbus then narrowed down to two designs, as Anagnost explained. “Both have better flow scores than the existing standards, so either factory functions more efficiently, the engines are installed more quickly, the logistic flows are more efficient, and so are the workers because they take fewer steps each day… Both options are less costly, so now they just need to choose the one that suits them best.”
Autodesk is also working on new tools to automate tedious, time consuming tasks, something that chimes with Williams, a former architect who spent the early days of her career doing ‘boring activities’ like creating door schedules. In her own words she was basically just following standards.
Visual programming tool Dynamo has been available for Revit for some time, but Autodesk is now looking to make task automation much easier with the introduction of Dynamo Player. According to Williams, it allows anyone to run a script to automate tasks even if they don’t know how to code or use Dynamo.
Williams showed how the technology could be used to quickly generate clash free structural reinforcements for window and door openings. “A task that used to take ten minutes to do manually in Revit now only takes ten seconds using Dynamo player,” she said.
Dynamo player is also being used by Build Change, a non-profit organisation that strengthens buildings in emerging nations to help protect them from earthquakes and typhoons. Almost all houses are different, and each requires its own set of designs and drawings which, in the past, were all done manually.
By embracing new technology, the company has now built an automated design to construction workflow which uses Revit and Dynamo scripts to automate the retrofit design for light types of buildings. The team codes in Dynamo, creating structural engineering rules, and then Revit is used to produce a 3D design, Bill of Materials and the construction drawings. “What once took our team of three people four to five days, now takes one person three hours. That’s 97% less time,” said Elizabeth Hausler, founder and CEO, Build Change.
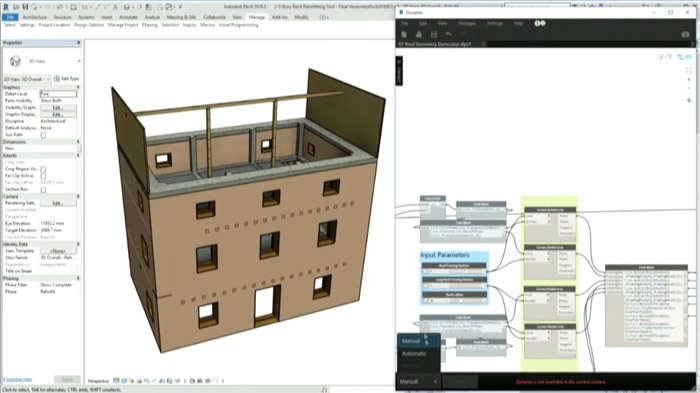
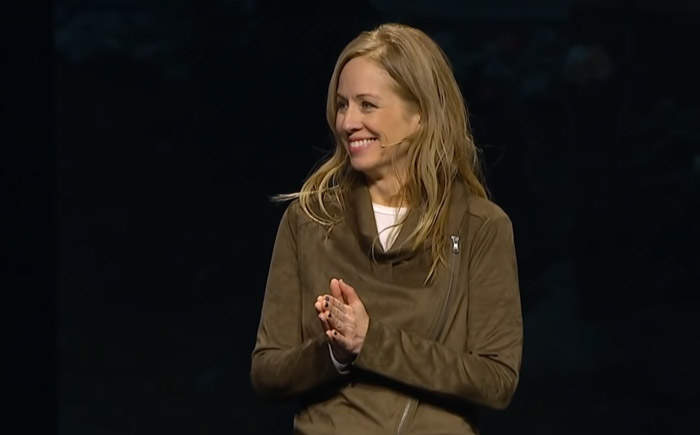
This is a hugely impressive saving and one that will completely transform the way its skilled architects and engineers are used, but Build Change is not stopping there. It’s now looking to save even more time by using Artificial Intelligence (AI) to change how homes are assessed.
Rather than sending out engineers and architects to every house, home owners can upload photos to the Build Change cloud and these are then used to quickly and automatically assess homes, as Hausler explained, “It looks at things like the continuous length of solid walls and proximity of walls to the corners, the length of wall between openings. We train the machine for image capture and all that data then tells us if it’s possible to retrofit the home.”
Build Change has the ambitious goal of strengthening 10 million homes in the next 10 years but needs three million dollars to fund the program. On stage Anagnost revealed to Hausler that Autodesk would be donating half a million dollars to help Build Change reach its goal. On a day where heavily scripted presentations were the norm, seeing the genuine surprise and emotion on the face of Hausler when Anagnost broke the news was a truly wonderful moment.
It’s not just buildings that are benefitting from Dynamo. The visual programming tool is now available for Civil 3D as well and can be used to automate a range of repetitive tasks such as the design of guardrails for road projects, signals on a rail track or disabled ramps on a site.
Williams explained how global design and consultancy firm Arcadis hired an intern to write a script to design the overhead wiring on a railway track, “When they changed the track layout, the script would automatically update the overhead wiring along with it,” she said, adding that the results were so impressive and saved them so much time that they even included wind deflection in the same script to ensure none of the poles would hit the nearby infrastructure in bad weather.
Digital twins
It’s been widely reported that 70% of the total cost of ownership for a building is during the operation phase. And with the promise of cost and energy savings, it’s no surprise that building owners and operators are increasingly looking to digital twins. According to Nicolas Mangon, VP AEC strategy and marketing, there are 30 billion Internet of Things (IoT) connected devices in buildings and this is growing.
Digital twins as a technology is being pushed hard by many AEC software developers, especially Autodesk competitor Bentley Systems. Autodesk hasn’t really jumped on the digital twin bandwagon yet, but as the AEC industry grapples with definitions, it had a strong and clear message for AU. According to Mangon, you get your digital twin by combining BIM plus IoT plus Artificial Intelligence (AI) and it can then help building owners and operators better manage and understand the performance of the built environment.
In the AEC keynote, Mangon focused on a hospital project which was fitted with smart doors, complete with sensors that can monitor smoke, temperature, humidity, particles, air pressure and more. In one possible scenario the door didn’t shut, or was blocked, so triggered an alert in facilities management software BIM 360 Ops, producing a ticket for a technician, who is then sent to the exact location using an indoor map based on the Revit model.
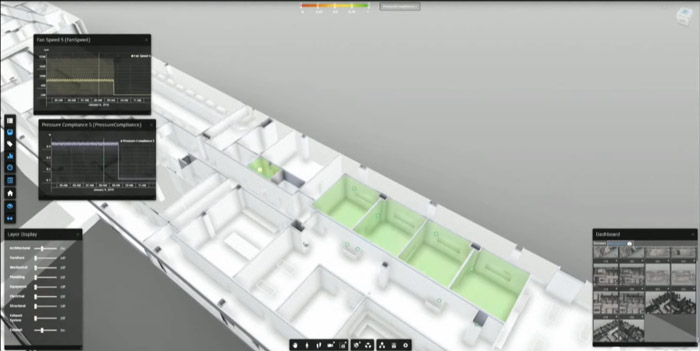
As the technician is reviewing the ticket, AI indicates that there’s an overdue maintenance on one of the exhaust fans that might result in a possible contamination. Dashboards can then be pulled up to show how the fan has been performing over time and if other fans are meeting requirements. Armed with this information the owner can take a proactive approach to maintenance in this and other hospitals.
The model-centric software used in this demonstration was not a product, rather a technology based on Autodesk Forge that can visualise and aggregate all kinds of IoT data. It was later revealed to be Project Dasher, which actually dates back to 2016, but should come to market in 2020.
Mangon stressed the importance of using AI in Digital Twins to look at large amounts of data from other sources including occupant data, social media, weather conditions, HR systems and many more. “[Digital twins] will provide owners and operators with insight like never before. Our buildings will be more efficient, they will produce less C02 and they will be more resilient for the future,” he said.
Where GIS meets BIM
It’s been two years since Autodesk announced its partnership with Esri to build a bridge between GIS and BIM. The aim is for users of Esri software to be able to access, update and use BIM data in a spatial context throughout the lifecycle of an asset. Conversely, architects and engineers will get better access to GIS data from within Autodesk’s design and construction tools.
“The more we talk, the more we realise that our customers are demanding that engineering and design workflows aren’t just in isolation, they have to have context, environmental context, social context,” said Esri CEO Jack Dangermond.
To date, the two companies have connected up ArcGIS (Esri’s mapping and analytics platform) to InfraWorks, Map 3D and Civil 3D, so infrastructure projects designed in those Autodesk products can be published directly back to ArcGIS. But the real prize is through the cloud and work is underway to connect ArcGIS data to models in BIM 360. But it’s not just about bringing in contextual GIS data, it’s also about being able to access Esri services.
In the AEC press conference, Mangon explained how some of the major AEC companies are using both Autodesk and Esri software but admitted that Autodesk and Esri could engage with these firms better. “As we go and talk to customers, sometimes we go separately, and we need to build that connective tissue, reinforcing the partnership,” he said.
From BIM to real time 3D
Autodesk’s partnership with Unity was the big news from AU 2018. One year later and we now see the first real fruits of this relationship with the launch of Unity Reflect. The real-time 3D tool, which can create live links to multiple Revit models and also bring across the BIM metadata, is available now for an annual subscription of $690. Support for Navisworks, ArchiCAD, Rhino and SketchUp is also in the pipeline.
Autodesk confirmed that there will be a future integration with Autodesk BIM 360 that will allow users to flag design issues in VR and have them show up automatically in BIM 360’s issue registry so they can be resolved later on. It’s this kind of round-trip workflow that’s lacking in most AEC-focused VR tools at the moment, even though BIM 360 integration is everywhere.
Unity has big plans for the software, including new workflows for on-site Quality Assurance & Control and support for higher quality visuals through its High-Definition Rendering Pipeline.
It also has several use case workflows under consideration, including a two-way live link, drone scanning, smart cities (IoT) and construction sequencing.
It’s refreshing to see a company share its roadmap and potential future plans so openly, but one can’t help but wonder if Unity will start to tread on the toes of the company that gave it the keys to Revit and a level of integration enjoyed by no other.
To learn more about Unity in AEC and Unity Reflect, read AEC Magazine’s in-depth article.
Hyperloop One
When it comes to customer stories, few can compete with the engineering wonder that is Virgin Hyperloop One. During the AEC keynote, CTO Josh Gievel gave an insight into the futuristic transport technology that shoots electromagnetically levitated passenger and cargo pods through a depressurised tube.
By eliminating the impact of air-drag and friction, less energy is used making it cheaper to operate. And, of course, pods can travel at exceptionally high speeds. The ultimate aim is to reach 670mph, as fast as an aeroplane and three times as fast as a high-speed train. To date, 240mph has been achieved on a 500m test track that was built in Las Vegas in a mere six months, but the company plans to take it to commercial operation in just a few years.
Of course, technology is playing a key role in making this a reality and the design team is using a raft of tools to design both the linear infrastructure and the vehicle design simultaneously. These include Civil 3D, InfraWorks, Revit and Inventor. Virgin Hyperloop One is also adopting BIM 360.
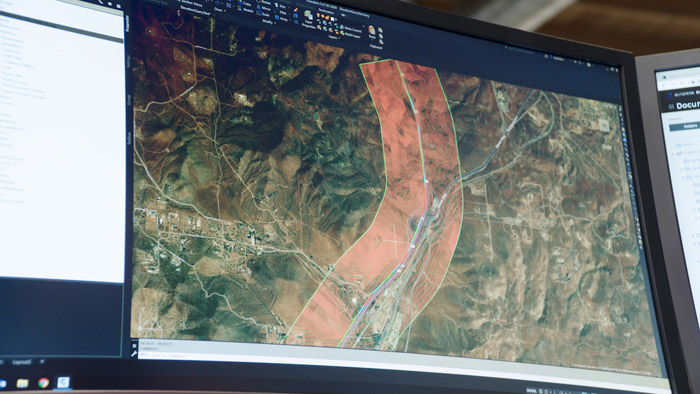
Conclusion
With its recent big-ticket acquisitions and launch of Construction Cloud, Autodesk is arming itself for the next big battleground in AEC. It has huge ambitions for construction but now faces the challenge of making Construction Cloud bigger than the sum of its parts, while fending off competition from the likes of ProCore and Trimble. Autodesk’s trump card might be its connection with its design authoring tools, but with the move towards digital fabrication it will also face competition from firms with more knowledge of direct manufacture within AEC, such as Dassault Systèmes Solidworks and Catia. (You can read more about this topic in this AEC Magazine article).
The huge investment and pursuit of cloud services has come at some cost to the development of its more mature products, especially in the discipline of architecture. Those with Revit would have noticed the depth of yearly additions suffer. Also, the next generation BIM and collaborative technology Project Plasma (formerly Quantum) has been stretched out as more of a multi-year project.
However, Autodesk has a renewed focus on design automation and generative design. Making it more accessible with Project Refinery and Dynamo Player could help realise the potential of what has been slow burners in terms of technology adoption. Digital twins, currently one of the buzzwords in AEC and a big focal point for Bentley Systems, is also on the agenda, and it will be interesting to see what Autodesk delivers in 2020.
But Autodesk has also set some boundaries. With its close relationship with Unity and the plethora of VR collaboration tools that now plug into BIM 360, it seems more than happy to let third parties handle the gamification and expansion of BIM into real time visualisation, virtual reality and mixed reality, while it manages the data from the cloud.
As Autodesk continues to branch out from design, the next few years are going to be critical as it tries to reposition itself as a company that takes every bit of architecture, engineering and construction as seriously as the others.
If you enjoyed this article, subscribe to AEC Magazine for FREE