While the CAD firms have been talking about BIM, there have been few projects that deliver on the vision. Autodesk has managed to pull off a major customer coup with Revit playing an important role in the design of New York’s Freedom Tower.
Everyone remembers where they were when they heard or saw the terror that happened in New York, Philadelphia and Washington on Tuesday, 9/11, 2001. For me, I was sat at work in London, when a friend from North America rang to say a plane had flown into one of the Twin Towers. Like millions, in utter disbelief I logged onto any news site that hadn’t been inundated with traffic to find out what had happened. From that point, a continuous stream of the most unbelievable and terrible events just kept on coming, suddenly nowhere felt safe.
Through television, the aftermath of the horrific day’s events and the huge loss of life became physically embodied at ground zero, in the rubble of the Twin Towers and the dust-covered streets of lower Manhattan. These iconic buildings were completed in 1972 and 1973 and were briefly the tallest buildings on the planet with their 110 stories dominating the New York skyline. The towers were probably the best known examples of tube buildings, with a main core, strengthened by closely spaced columns and beams in the outer walls. At 1,368/1,362 ft and built on landfill, the foundations had to be extended more than 70ft below the ground, to reach the solid bedrock. While the towers were actually designed to withstand a direct hit from an aircraft, the amount of fuel onboard the 9/11 planes created intense fires (estimated at 2,300 degrees Fahrenheit) which weakened the metal infrastructure, collapsing the upper floors, which then created too much load for the lower floors to handle, causing catastrophic failure of both towers.
The decision to rebuild was political, commercial and a matter of national interest and pride. With so much interest and competing ideas, whatever got chosen was bound to have its detractors and critics. Should it be higher? should they be rebuilt exactly? Others wanted a memorial park only. The Lower Manhattan Development Corporation initiated a competition inviting nine star architects to submit designs. The winner of the site plan was Daniel Libeskind, surely the commission of a lifetime, although the task proved controversial with the developer Larry Silverstein (the lease holder) appointing David Childs of Skidmore, Ownings and Merril (SOM) as lead architect for the Freedom Tower and in subsequent revisions much of Libeskind’s original plan has been altered, dumbed down or removed. This happens in many major public works but perhaps in this case, not quite as publically.
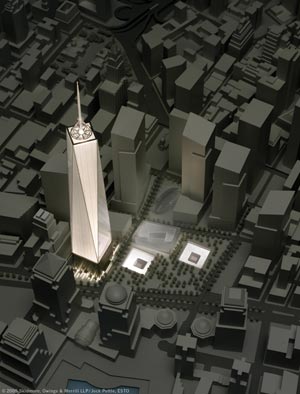
Added to those team pressures, since 9/11 town planners and authorities have become aware of the dangers that prominent buildings are now under. As the design for the Freedom Tower progressed, major changes were required to respond to the New York Police Department’s security fears; this happened after a year of work had already taken place on the design and was above and beyond any documented building codes.
Freedom Tower Design
The Freedom Tower will reach 1,776 feet, (significant as the year of American Independence) and while the glass form is striking and new, it’s reminiscent of other classic New York skyscrapers, like the Empire State and the Chrysler Building, in its symmetry. The design also incorporates a reference to the torch of the Statue of Liberty. And as mentioned before, the newly revised Freedom Tower design has been modified to include even more safety features than the original, including extra strong fire proofing, blast-resistant materials, biological and chemical filters in the air system, redundant exits and a core wall that’s three feet thick. That said, the new Freedom Tower design retains key elements of the original, including 2.6 million-square feet of office space, and an observation deck.
The Freedom Tower is located on the northwest corner of the 16 acre World Trade Center site. The revised Freedom Tower features a cubic base (rather than a parallelogram as originally conceived), and has been set back further from one street identified as being a place where a possible threat could be launched. The tower’s footprint measures 200 feet by 200 feet, which is the same size as the footprints of the original Twin Towers and replaces more than one quarter of all the office space that was lost on 9/11.
As the tower rises from its cubic base, its square edges chamfer back, transforming the square into eight tall isosceles triangles in elevation. At its middle, the tower forms a perfect octagon in plan and then culminates in an observation deck and glass parapet (elevation 1,362 feet and 1,368 feet – the heights of the original Twin Towers) whose plan is a square, rotated 45 degrees from the base. On top there’s a mast containing a television antenna for the Metropolitan Television Alliance (MTVA), designed by a collaboration of architects, artists, lighting designers and engineers. This is secured by a system of cables, which rise from a circular support ring, similar to the Statue of Liberty’s torch, taking the structure to 1,776 feet. The mast will emit light, and is being called the ‘Beacon of Freedom’.
The Freedom Tower has a robust and redundant steel moment frame, consisting of beams and columns connected by a combination of welds and bolts, and resists lateral loads through bending of the steel frame elements. Paired with concrete-core shear walls, the moment frame lends rigidity and redundancy to the overall building structure, while providing column-free interior spans.
Energy efficiency and environmental sustainability play a large role in the design. The Freedom Tower will include state-of-the-art energy conservation technology to reduce energy demand; better interior “daylighting” and views of the outside for occupants due to ultra-clear glass technology that also saves energy; improved indoor air quality due to outside-air ventilation and use of building materials without toxic materials such as volatile organic compounds (VOCs); water conservation due to reuse of rainwater for building cooling and irrigation.
Construction of footings for the Freedom Tower is expected to begin in the first quarter of 2006. It is projected that steel for the building will be visible above grade in 2007, with a topping out in 2009. The building is projected to be ready for occupancy in 2010, where, according to a report by the Lower Manhattan Development Corporation, the rebuilding the World Trade Center will generate something like $15 billion in total economic output in New York City and an average of 8,000 jobs each year for thirteen years.
SOM and CAD technology
Founded in 1936, Skidmore, Owings and Merrill (SOM) is one of the America’s leading architecture, urban design, engineering, and interiors firms. SOM has completed more than 10,000 architecture, engineering, interior architecture, and planning projects in more than 50 countries around the world, specialising in the design of high-rise buildings. It was responsible for the design and structural engineering of America’s tallest building to date – the 109-storey Sears Tower in Chicago.
Since the late 80s, SOM has been deeply involved in using advanced technology in its practice, even developing its own design software system, called AES. The firm has been a long time believer in the use of the virtual 3D model, integrating all building components including building systems and structural engineering. The company moved to AutoCAD from its in-house system and has been one of the leading users of Revit in the USA. It appears that Revit Building has allowed the firm to realise its concept that an integrated modelling system would bring major benefits.
” SOM believes in 3D and thinks that the current inefficiencies in the construction business can and should be improved on. Revit is certainly playing its part in this process, with plans to use Revit on many other projects currently in development. “
Armed with Revit Building, SOM decided to use its new modelling tool alongside AutoCAD to design only the building’s complex subgrade levels. The challenge here was to design around the plethora of existing underground (subway) tunnels, utilities and services. This opportunity gave the team at SOM a chance to cut their teeth on Revit and devise best practices and working methodologies. The more the team used Revit the greater their confidence grew and the team gradually expanded the use of Revit to the tower’s lower and main core. This done, Revit was pushed again to define the enclosure, cable net, mechanical, electrical and plumbing systems. The managers at SOM, while impressed with the tool, also had fears as to where Revit should stop being used and when more traditional, proven technologies should be deployed. At this point Autodesk and SOM hammered out a deal, where Autodesk would support SOM to utilse Revit as the main design tool on the project. Autodesk would assist in development of the technology for the project and step in at the documentation stage should help be required.
The benefit and the problem with BIM tools are that they automatically generate the 2D sections, plans and elevations from the 3D model. While you may be happy with the 3D model you have created, getting the drawings out in a format that you want, with everything grouped on the right layer, isn’t necessarily that straightforward. Fortunately, SOM has a few architects and managers that have test-driven previous versions of Revit on older projects to work out the benefits and the drawbacks. With the backing of Autodesk and considerable in-house knowledge, Revit is now being used for the design and construction documentation on the newly redesigned tower.
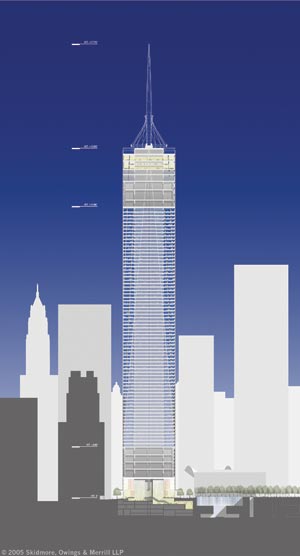
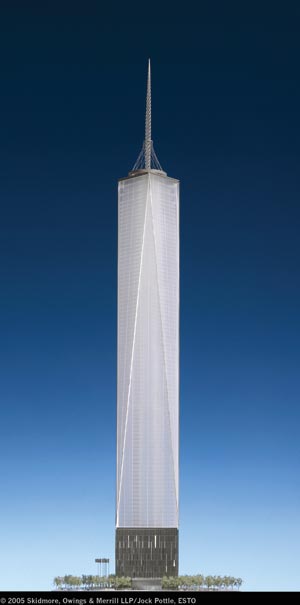
With the concept of the central data model, the design and documentation benefit of Revit would be considerable but nowhere near the maximum benefit of creating a multi-discipline model, including all elements, referenced to the main design. Here, Autodesk has been assisting in getting the project’s M/E/P engineer to develop generic building systems to add to the model. The project’s Structural Engineer used a combination of Revit Building and AutoCAD to model the Tower’s foundations, buttress slabs, core walls and columns. These would have been dumb elements as Revit had no intelligent structural members at the time. Since the project started though Autodesk has introduced Revit Structure, which is now being implemented, improving the richness of the overall data model.
The single data model and shared data resource improves co-ordination between all disciplines and the firm holds regular integrated discipline meetings, using the Revit 3D model and a large plasma screen. This enhances co-ordination and gives higher quality assurance. The company also notes that there has been a reduction in revision times and RFIs. The project’s Construction Manager will be exporting data from Revit to Excel for quantity take-offs but will be run in conjunction with traditional methods and used as a safety check for now.
Revit hasn’t completely replaced AutoCAD. SOM has a long history of using the software and has developed many of its own programs and automations to improve productivity. Using AutoLISP, SOM has created tools for modelling, analysis and documentation that enable team members to experiment with design ideas and get rapid feedback. Some AutoCAD models were analysed visually, while others were analysed with routines that, for example, cast shadows to create post-processed images used to compute area and time in shadow.
Since 1999, SOM has also been an Autodesk Buzzsaw subscriber and with the Freedom Tower, Buzzsaw is the primary tool for keeping the project’s members up to date by sharing and distributing all the reports and design docs. Autodesk is using the experience it’s gaining from working on the project to build forms into Buzzsaw and to expand into project management with Buzzsaw Professional.
While the single model is good for design and documentation, it still doesn’t mean that the model created in these systems, such as Revit Building, are ideal for generating visualisations. The concept of the single model for everything is still some way off. SOM uses 3D Studio Max and a render farm in conjunction with AutoCAD to quickly generate complex geometry in Max and render the impressive images you see in this article.
SOM uses a lot of Autodesk software and while products like Revit have yet to integrate to the family of products particularly smoothly, it’s clear to see that the company is mixing and matching the best tool for the best job. If 2D analysis is required then use AutoCAD, if a decent rendering is needed, then use Max. Meanwhile, the Revit model is updated and holds the definition of the Freedom Tower and as Autodesk expands its features, SOM is deploying the add-ons or expansion possibilities within the project network.
This tells me what I already knew, that Revit isn’t fully cooked yet, but then there isn’t any BIM solution that can actually do it all. The best approach is to use each product, old and new, for its strengths and hopefully you will have enough overlap to cover all bases. SOM believes in 3D and thinks that the current inefficiencies in the construction business can and should be improved on. Revit is certainly playing its part in this process, with plans to use Revit on many other projects currently in development. When the Freedom Tower is eventually built, it will definitely be a testament to early adopters of BIM.
Conclusion
With SOM using Revit Building so visibly on one of the world’s most talked about buildings, Autodesk really couldn’t have got a higher profile leading adopter to champion the Building Information Model story. The fact that SOM didn’t intend to use Revit Building on anything above ground but its employees led the charge also gives Revit a huge endorsement. However the project could not have been done in Revit Building as it was. Autodesk has had to work very hard to feed back requirements to the Revit development team to ensure that the capabilities were incorporated for the project. The story here is that Autodesk not only got a great PR opportunity but it got a customer that drove the development of the product to make it battle hardened on a very large dataset. To this point, Revit Building and indeed all BIM products, appeared to have speed issues when working on large data sets.
On the other hand, Autodesk gave SOM assurances that it would assist in doing any work necessary, should Revit Building fail to be up to the task, so SOM was not operating without a safety net. It still makes the decision to run with Revit Building a ‘gutsy’ one but the risk was mitigated by Autodesk. This makes me think about all those firms out there that are thinking of using Revit or rely on their dealers for support within a project. Smaller firms are not likely to get Autodesk backing them should they get into technical difficulty and dealers, as of yet, have little experience of Revit within sizeable projects, which concerns me. It’s really important to find a reseller that has actually had experience of Revit being used at the coal-face and not just as a fancy front end for client presentation, which it does well but is not its intended purpose.
There is no doubt that, slowly but surely, Revit is now gaining credibility within larger firms, as well as small practices. It still may take more than a decade to get the industry to see the benefits of 3D but we are now seeing the early adopters applying BIM tools to benefit real projects. The Freedom Tower project and SOM’s deployment and future use are clearly leading this charge.
www.som.com
www.autodesk.co.uk/revit