With over 10,000 attendees, Autodesk University in Las Vegas is the biggest CAD industry event of the year. With plenty of razzamatazz, dozens of speakers, training sessions, social events and a massive hands-on exhibition, there is nothing quite like it.
The annual pilgrimage to Las Vegas for Autodesk University is something I both look forward to and dread. On the good side, there are always great speakers, technology developments galore, gossip, new contacts and old friends to see. On the downside there is the never-ending twilight, the constant jingling of slot machines, the regular electric shocks from static discharge, lack of sleep and accidental and repetitive collateral liver damage.
Autodesk is in the midst of company-wide change, moving from boxed product to Suites, upgrade revenue to subscription-only and desktop applications to cloud and mobile. All this while maintaining its extensive dealer network, support distribution and growing direct sales force.
In the past, customers could decide when it was right for them to upgrade and budget accordingly but the new subscription-only model means Autodesk has to work to ensure its customers see the value in its ongoing enhancements and services. The company is moving away from its annual release cycle to providing ongoing updates throughout the subscription period.
While AutoCAD is forever popular with customers, it has long since diminished from being a central plank for the company’s future vision. Applications like Revit, Fusion, Inventor and InfraWorks get most of the limelight, as design transitions to adopt an intelligent 3D paradigm. Historically CAD was all about the documentation of design, while the latest generation of tools are for amplifying creativity, virtually prototyping, testing and improving in addition to generating documentation.
Keynotes
Jeff Kowalski, Autodesk CTO, took to the stage to give a rousing speech on what that change means for Autodesk, and how he believes that the iterative evolution found in nature is the future of design.
“All the buildings and bridges, machines, cars, products and devices all have one thing in common. They are all dead!” he said. “At Autodesk we are starting to look at technology that designs itself through the lens of nature.
“Generative design starts with your goals and runs through all the possible permutations, through successive generations until the best design is found. We think about the design process as a living process.”
Nature refines a solution to a problem through iteration, while mankind tended to start from scratch. Mr Kowalski explained his theory that we need to take into consideration all the solutions that already exist as a start point for the next design.
Autodesk is developing machine-learning algorithms to identify key concepts in millions of 3D models, classifying assemblies and components and the relationships between them. Mr Kowalski demonstrated the algorithm identifying items in an assembly, such as gears and screws. Once the context has been identified the next stage is to have a CAD system understand what these parts do; and that is exactly what Autodesk is working on.
Mr Kowalski envisages that in the future a CAD system will provide a variety of configurations to assist the design to achieve the best solution. “We have to stop telling the CAD system what to do and start telling it what we want to achieve.”
Mr Kowalski explained how, using generative design, it is possible to derive the best design in the same time it would have taken to come up with the first proposal.
In a given example, Kowalski said that for a defined criteria the computer could come up with a range of solutions with optimal geometry. The design could then select the most aesthetic and then the system would take that criteria as a constraint for the next iteration, and so on.
In the future it will be possible to design complex, aesthetic buildings without drawings, but instead setting the criteria and expressing the goals. Arup has already used some of this code for the design of tensile structures.
Mr Kowalski also looked at the issue of planned obsolescence in design. Because our designs are dead the moment they are produced, they do not react or adapt to changes in their environment but what if they could dynamically interact? There has been a huge leap in the creation of small cheap sensors and smart materials and the emergence of the ‘Internet of Things’ means objects could be aware of proximity and could potentially communicate and collaborate — but we are not there yet.
Mr Kowalski wrapped up asking attendees, “What if you were to ignore all these concepts and ideas but your competitor were to introduce a living device to compete against your dead one?”
Autodesk CEO, Carl Bass, was ebullient about the opportunities that change can bring to Autodesk and customers.
His opening line set the scene: “Not since the industrial revolution has there been such a radical rethink of the way that we make things.”
Low-cost computer power has enabled Autodesk and its customers to work with much richer data, which reflects the real world. Advances in data capture, with laser scanning and photogrammetry brings the 3D world inside the computer. It is possible to take ‘dumb’ XYZ point clouds into software, create a surface mesh and then perform analysis or edits.
This concept of reality capture is going to be big for Autodesk in the near future, with products such as Autodesk Recap for point cloud capture and registration, as well as Autodesk Memento, currently in beta, for surface creation, edit and 3D print.
A360 for cloud-based project collaboration was announced in 2013 and now has 60,000 active licenses. It is built into all Autodesk 360 products and will be in all forthcoming releases. Everyone who attended AU got a free year’s subscription, “It’s like Google Docs for designers and engineers”, explained Mr Bass.
Moving on to creation and fabrication, Bass said, “3D printing is the closest thing we have to the Star Trek replicator but we haven’t delivered on the promise of 3D printing yet. The machines are too slow, the materials are too limiting and expensive and the process is too unreliable.”
Autodesk’s Spark platform is an open system that makes getting parts out easier. The company is working with an array of partners to do this and has launched a $100 million fund for start-ups and researchers.
Mr Bass also highlighted the Autodesk Amber 3D printer, which is intended as a reference device and is open, with Autodesk sharing the design plans for those that want to build their own.
Further to this Autodesk is working with robotic 3D printing technology that prints in metals like stainless steel.
Mr Bass said he was excited with the potential of digital tools on building sites. Highlighting Autodesk BIM360 for project management, he said it is the fastest growing product the company has ever had.
Autodesk has worked with Topcon to include support for its point layout tools, which enables the BIM model to be queried on-site, with a laser pointing to the respective real-world space.
Mr Bass then announced a forthcoming new Subscription option called ‘Subscribe to Autodesk’, which will give customers access to all of Autodesk products for a single price. Coming in 2015, Bass promised, “You will be able to use any software, on any machine, anywhere in the world,” however no price was given.
In his parting shot, Bass announced that Autodesk was making “all of its software free to any student, any teacher, any institution, anywhere.”
AEC products
Autodesk is concentrating a lot of effort on the construction market and has started to get traction within US Departments of Transport, which are a key markets for competitor Bentley Systems.
To help combat the Trimble and Bentley alliance, Autodesk has teamed up with Topcon to try and offer feature parity for the construction phase. In many respects Autodesk’s long dedication to developing the Architecture element of AEC, left the market open for Trimble to slowly and quietly grow its presence. The battle for Building Information Modelling (BIM) in AEC is shaping up.
Autodesk A360, or BIM 360 for AEC users, is the future backbone for design teams. Teamworking has been one of Revit’s weaknesses and Autodesk plans to overcome this by using the cloud. It has already started to develop 360-based AEC tools that hook back to the 360 cloud platform – Glue, Field and Layout, extending office-based design information for use onsite or gathered and reported back. Over time this will be expanded with the addition of costing, scheduling and estimation tools.
This is clearly a transitional phase of development as Autodesk continues to fill in the missing pieces until using a cloud-based design process becomes a no-brainer.
Whilst talking with several customers at AU 2014, it was clear that there was some resentment at the lack of pace in Revit development. Despite Autodesk’s move to sell Suites over single applications, firms tend to use one of the products in the Suite way more than the others and for architects that is Revit.
Autodesk will need to get the measure of new functionality right for customers to feel that they are getting value for the fees. However this could just be early teething issues. As the cloud-based approach to using AEC tools fills out, Revit’s current bottlenecks may well fade away as file size, Revit versioning and speed get crushed through server power and omnipresence.
Memento
So-called ‘Reality Capture’ is a big focus for Autodesk. This is the ability to ‘bring in’ topography, buildings, infrastructure, objects — anything — and convert it to CAD geometry for reuse in a computer.
Surveyors and mapmakers have traditionally used expensive laser scans to provide measurement. With advances in photogrammetry and the conversion of video to 3D, the cost of doing this has drastically reduced and Autodesk proposes that we can rethink design by using accurate, captured data.
Its first offering in reality capture was a product called 123D Catch, which could take hundreds of photos of an object and build a 3D mesh. The second was Recap, a survey tool to collate laser scans and quickly generate detailed point cloud models.
Now comes Autodesk Memento, currently in beta. Memento can import point cloud data photographs or video and convert these to extremely dense meshed surfaces. Through a simple interface it is possible to manipulate these meshes, healing holes, smoothing surfaces or completely editing the shape. The software can output to a 3D printer.
It could be used to capture a building for renovation or for rapid energy modelling, rescuing an antique object such as a statue for archive, to capture complex natural forms for use in a design or for monitoring coral growth over time. Memento will have many, many applications.
Currently it is being used by the Smithsonian Institute to capture and catalogue many of its artifacts and has been used in Sweden to capture an Egyptian mummy both sarcophagus and in 3D via MRI scans. Using the software, researchers found that within the sealed mummy bindings were amulets and jewellery and without ever opening it up these pieces were isolated and manufactured.
Autodesk wants to take the various scanning technologies and ‘democratise’ their application within all areas of design. This will have some challenges with issues like copyright, as it will now be even easier to have product ideas stolen but will offer to many benefits too. Imagine being able to quickly get any real world object in your CAD system and being able to edit it? My mind is truly boggling. See Memento in action here (tinyurl.com/memento3D).
Exhibition
A major component of Autodesk University is the exhibition, which occupies a cavernous hall and is filled with firms that work within the Autodesk Ecosystem, from a behemoth such as Hewlett-Packard to a small start-up that just got funded on Kickstarter.
Traditionally, when Autodesk was more AutoCAD-centric, the exhibition was filled with symbol library providers, drawing management and DWG viewer applications and made for a pretty dull afternoon. I have to say that his year the exhibition area was probably where the best things were to be found. While there were the traditional player and productivity tools, extensive space was set aside for customer displays, product demonstrations, live stage shows and hands-on booths.
Design tools and the digitisation of everything has generated an explosion of new companies and technologies that really make you think about what we can do with CAD. This year’s exhibition had many laser scanning and image capture firms showing off their wares. Topcon, fresh from the announcement of deep co-operation with Autodesk had a huge booth. Autodesk’s products now support Topcon scanners and laser pointers, furthering Autodesk’s charge into the construction space.
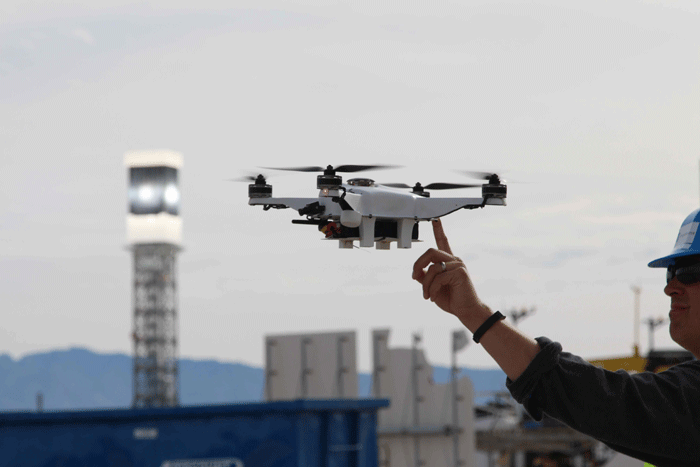
There were lots of UAVs (Unmanned Aerial Vehicle). One company in particular blew my mind, Skycatch (skycatch.com) offers a UAV drone service, which is capable of flying around building sites / landscapes / infrastructure, automatically capturing video at 1cm / pixel resolution, which can be then turned into fairly a accurate 3D point cloud model by products such as Autodesk Memento.
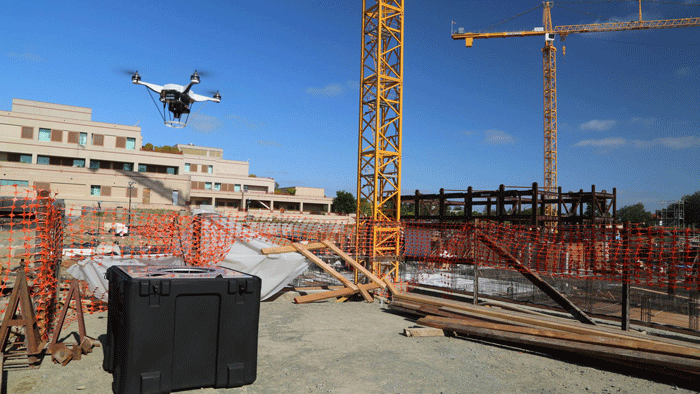
This mesh can then be compared back to the BIM model to check for differences between the as-built and the original Revit model. It’s possible to do this on a scheduled basis and could be used to assess volumetric measurements, thermal imaging, ortho mapping and 3D point cloud generation. The UAV carries the payload underneath the quadcopter body and when it needs a new HD or power, automatically flies back to its box and swaps its payload to continue. Absolutely fantastic stuff.
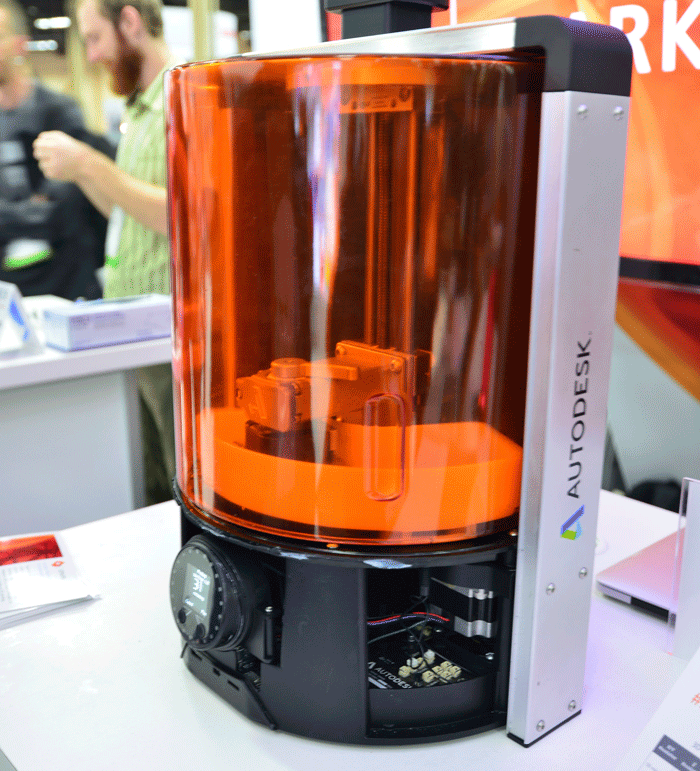
Staying with scanning, Autodesk Reality capture team had a sizeable space dedicated to demonstrating various methods of bringing the real world into the computer. The largest display piece was a mechatronics set up to automate the capture of artifacts from a museum. With millions of items to capture and scan, this framework would carefully move items along a motorised conveyor, stopping for a moving light hemisphere and multi-camera set up to capture hundreds of images. These can then be loaded to the cloud and a high resolution 3D model created using the forthcoming Memento product.
Autodesk REAL 2015
Autodesk’s Reality Capture event takes place next month in San Francisco and we will be there to report from it.
Dotproduct (dotproduct3d.com) is another interesting reality capture start up. Running on a standard small tablet, RGB scan-head (like Microsoft Kinnect’s) with a simple hand held grip, the user simply ‘paints’ over an object or space as it captures geometry. On screen the device eventually highlights green showing the 3D capture is complete. This technology could be used by architects or remote workers to capture onsite models. At around $5,000 this is one of the lowest cost professional scanners on the market.
On display were robot arms, manufacturing machines, a 3D printed car, a foldable kayak and hundreds of other customer samples, created using Autodesk tools.
IrisVR is a great little start up that was at the exhibition and we have written about them in the past. The software offers a simple drag and drop interface to accelerate the conversion of BIM models from Revit (or SketchUp), into beautiful virtual reality (VR) worlds that can be explored using the Oculus Rift. While at the show, I also heard that Autodesk had acquired the Unity (unity3d.com/unity) game engine, which is a complete ecosystem for games design and a technology that I am sure will find its way into Revit BIM tools.
It is remarkable and an exciting prospect that this kind of technology will soon be used by practices worldwide. The VR headset market is set to explode with many high-resolution, low cost products in development.
AU 2014 was the first major outing for Autodesk’s Ember SLA 3D printer and Spark software (spark.autodesk.com/ember). A dedicated stand was set up with a number of these machines cranking out 3D models. As it is still early days, and each one is pretty much handmade, there was plenty of maintenance going on, but the build quality of the output really is quite remarkable. Autodesk took orders on the stand and is looking at ramping up production beyond these early pre-production machines.
Conclusion
Autodesk is changing in all areas — from the way it sells and delivers its software, and is even looking to fundamentally change the way we use computers to design. Mr Bass and Mr Kowalski’s keynotes were visionary and inspirational, concerning much of the high-end research the firm was doing with partners and demonstrating it was running with the new revolutionary concepts that will impact the next generation of designers.
Looking around the audience, I wondered how many of the delegates were still using AutoCAD and LT to just draw and document and their main collaboration tool was an email. The prerequisite of being on the new frontier of design is to start using 3D and BIM and only then can you start to benefit from a lot of what was presented.
The fact is that Autodesk has a lot of customers that are still 2D, so this is going to be a long process of education.
As Autodesk gets increasingly more cloud-centric, new features will just automatically appear and everyone will get them at once on whatever device, with Autodesk’s commitment to provide their range of tools wherever they need to be, on whatever device is at hand.
Videos of the presentations are available for free on the AU site, together with many of the classes. Even if you can’t go to Vegas, Vegas can come to you.
■ au.autodesk.com/au-online/overview
If you enjoyed this article, subscribe to AEC Magazine for FREE