To help track project progress and identify build errors on a compact city project, construction firm VolkerWessels used crane mounted reality capture to get high-quality data every day
Building residential properties is never an easy task. And if the jobsite is located in a tight downtown space, the project can become even more challenging, and every mistake very costly.
In 2018, VolkerWessels, a well-established Dutch construction company, was commissioned to build a hotel for the WestCord hotel chain, located in the city centre of Groningen, the Netherlands. The building consists of 123 rooms, spread over six floors, as well as a 1,000m² catering area, located on the Grote Markt. Since Groningen is prone to earthquakes, one of the requirements for the hotel is that it is earthquake proof.
No room for errors
The site is located in the city’s busiest area, leaving no space for storing or assembling materials on-site. As a result, VolkerWessels’ team counts on prefabricated modules.
While prefabrication saves time and space on site, it requires precision scheduling and planning of deliveries.
“Once delivered, the prefabricated elements have to be installed immediately. Every minute delay can cause truck traffic and we want to avoid it,” explains Arnold Pit, BIM process manager at VolkerWessels. “The most challenging part of the project is that everything must fit at once – there is no place for deviations. We use prefabricated modules, and if there is a mistake, it would cost us a lot of effort and time to re-make the elements.”
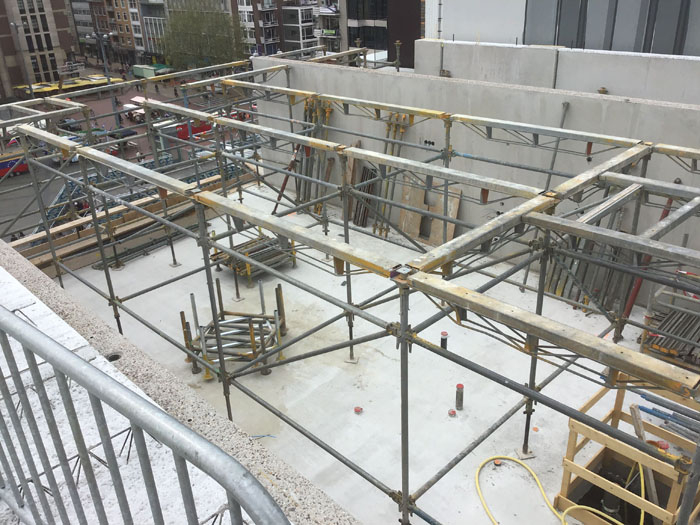
Avoiding congestion
The central location of the project imposes careful logistics planning on VolkerWessels’ team. There is a strict schedule for assembling prefabricated modules and deliveries since “every deviation would cause delay in logistics, and sequentially in the project,” says Pit.
The team has to schedule the deliveries every morning to avoid causing truck traffic from material and equipment suppliers in the afternoon. “We are tight to specific times to deliver our materials. Due to regulations, we cannot be a reason for traffic,” comments Pit. There are two other construction sites next to the VolkerWessels’ site, so delivery times have to be coordinated with them as well.
Staying on track To avoid any schedule deviations and logistics problems, the team has to be aware of the daily progress of the project. Since drones were impossible to fly downtown, Groningen, the team decided to use a Crane Camera solution from Pix4D, a technology the company had previously used on a pilot project in Eindhoven.
The solution consists of a number of connected camera systems mounted on tower crane jibs, which capture images automatically as the crane moves. Images are then wirelessly sent to the cloud where they are automatically processed and transformed into 2D maps and 3D models.
Project data delivered from the Crane Camera solution is used by several different team members and stakeholders. The superintendent checks the formwork and the floor steel to plan the daily work and the logistics. The project manager uses it for visualisation to communicate project progress to the client, importing point clouds to Trimble Connect.
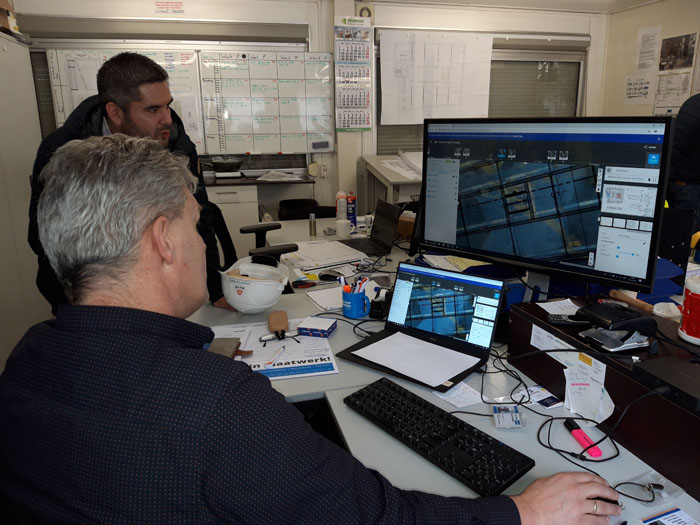
The earthquake specialist checks the installations and makes sure the building meets earthquake regulations, while the MVP subcontractor checks installations, such as ventilation and electricity.
The benefits to the project have been significant. As part of the superintendent’s daily checks of as-built vs as-designed, it was noticed that the floor formwork was not in the right place, deviating by 35cm. “I cannot imagine how we could have discovered this error so early without this tool,” said Pit.
Spotting misplaced formwork is critical as formwork affects the structural performance of concrete. “If the error was not spotted in time, the worst-case scenario would be to pour the concrete for the floors and discover that the structure is unbalanced. This could be very dangerous and result in building failure. This would have irreversible consequences,” says Pit.
“Another possibility would be to discover that there is not enough support for the elements on the floor while laying the concrete on the formwork. In this case the team would have to uninstall all these elements and re-make them. This would delay the project and lead to increased costs and extra efforts.”
With the help of the Crane Camera solution, the VolkerWessels’ team has avoided potential delays and costly rework. They also continue to keep track of the project and solve the logistic and planning challenges of the downtown hotel project.
If you enjoyed this article, subscribe to our email newsletter or print / PDF magazine for FREE