Reality capture began with costly terrestrial laser scanners, then advancements in photogrammetry-to-mesh significantly lowered the barrier to entry. Now, Matterport is bridging the gap by combining both technologies to deliver a scanner priced under $6,000, writes Martyn Day
Laser scanners were first commercially available in the mid 1990s and they have been used across nearly all AEC disciplines: civil engineering, surveying, architecture, heritage and quality control. The technology has moved from tripods to backpacks, handheld to mounted on robot dogs. However, the one thing that has remained stubbornly fixed is the high cost.
In 2012, Brian Mathews who previously ran Autodesk Labs, was made Autodesk VP of Reality Capture, as Autodesk anticipated the ‘democratisation of reality capture’. The closest that revolution came to being was in 2016 when Leica and Autodesk jointly launched the ultra-portable Leica BLK360 coupled with Autodesk Recap scanning software on the iPad.
At $15k the Leica BLK360 was half the price of most other scanners and looked set to be the breakthrough product that would bring prices down. Faro soon followed with a highly portable but more accurate scanner at around $20k but since then the appetite to drive costs lower has evaporated. If anything, most new scanning products have returned to previous price points and the Leica BLK360 will now set you back around $20k. In 2016, Mathews told AEC Magazine that to really open-up the market, scanners would need to drop below $10k. That moment never really materialised, until now.
Matterport was established in 2011 and brought out its first bespoke camera in 2012. Over time the technology improved to deliver 3D environments of interior scans, combining HDR photogrammetry with structured light sensors for depth information.
Find this article plus many more in the Nov / Dec 2024 Edition of AEC Magazine
👉 Subscribe FREE here 👈
Structured light sensors use a projector and cameras to capture an object’s 3D shape by analysing the deformation of a projected infrared light pattern. The most well-known application of this technology was from Microsoft with the Xbox One Kinect Sensor, an add-on for its gaming console.
Structured light sensor technology is significantly different to LiDAR, which uses time of flight of laser light to establish a cloud of 3D points.
Matterport became very popular in high-end real estate / estate agents and the company currently has 38 billion square feet of digital property currently under management in its platform.
Matterport technology has been used in architecture and construction to some degree, but not as a replacement for surveying.
The company shifted its business model to a subscription-based approach, added support for 360 cameras, and appeared to focus primarily on retail and real estate sectors.
The subscription pivot really only made sense to repeat volume users and not for occasional use. AEC is very much project focussed and that seemed to be a mismatch.
The last two years have seen two significant changes at Matterport.
The first was the release of the sub $6k Matterport Pro3, a LiDAR scanner and camera, which can cover 10-100m distances with a precision of around +/- 20mm (at 10m).
The second is the company’s acquisition by the CoStar Group in April 2024 for approximately $1.6 billion. CoStar appears to have cottoned onto the Digital Twin wave and Matterport’s use of AI. The company has backing and resources to double down on its real estate market, as well as entertain addressing a pro market with advanced AI and ever more sophisticated scanners.
Leica BLK 360 G1 vs Matterport Pro3
At $6,000, the Matterport Pro3 costs $15,000 less than the latest Leica BLK360, so it’s not surprising that it can’t match the specifications of Leica’s compact laser scanner. See specs below.
• Matterport Pro3 – 100,000 points per second, spherical capture 20 seconds, +/- 20mm @10m.
• Leica BLK360 G1 – 680,000 points per second, spherical capture in 20 seconds, 4mm @ 10m.
Capture times are roughly the same, but the Leica BLK360 G1 has almost seven times the depth of density of points, and up to five times greater accuracy. Both machines capture very high-resolution spherical imagery and software can combine laser with photogrammetry.
However, the price can’t be ignored and as an opening LiDAR scanner the Matterport Pro3 is a good option. Of course, the entry-level specs may limit its suitability for applications that require higher levels of accuracy.
Understanding the market
To find out more AEC Magazine talked with Stephanie Lin, VP and GM – Operate at Matterport.
Lin is ‘one of us’. She started as a licensed architect in the state of New York and specialised in super tall skyscrapers. She worked for one year at SOM San Francisco, with the eminent Neil Katz and then did seven years at KPF in New York, London and Shanghai.
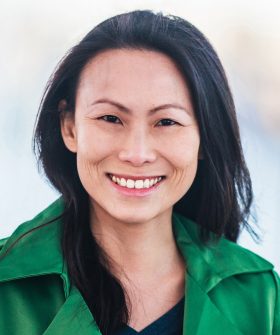
Post skyscrapers, Lin went in-house for eight years, to work with retail, specifically Michael Kors and Tory Burch. Lin understands the needs of retail and the pro level features that those in AEC design would love to have from low-cost laser scanning.
She explains Matterport’s offering, “With traditional laser scanning, you’re not just buying the hardware, you also have to train the operator in-house to use specialist software.
“Matterport does the registration and the stitching in the back end with our AI, which we’ve been using for 13 years now, so you can imagine, it’s quite well trained at this point.
“We’re trying to identify the friction points of going from design to the tedious task of documenting a space and then the equally tedious task of building up the Revit model.
“We kind of do full end-to-end for that beginning portion, which is get the quick scan, get the point clouds. You can even get a BIM file or a CAD file from us — remove the tedious day to day stuff and have your team go do everything else.”
Lin is convinced that the proprietary Matterport sauce is a major differentiator. That’s the technology that overlays point cloud, mesh and high-resolution images in the back end when processing a file, as she explains, “We’re really addressing the full building lifecycle, because that’s actually where the expensive part is. It’s not digging the hole in the ground, it’s making that space,” she says.
We’re trying to identify the friction points of going from design to the tedious task of documenting a space and then the equally tedious task of building up the Revit model
“We are now very focused on two solutions for the industry, and that’s design / construction management, and then facilities management,” she adds. “We are used time and time again, especially in the documentation stage, for milestone captures and definitely for handover packages. But we need to own it, and we need to put it out that way. And so this is our big focus for the company.”
In terms of technology, Lin explains how Matterport now has automatic dimensions, the ability to merge complex spaces and to copy notes and annotations from one model to the next. “These are workflow challenges that have hindered people from adopting using Matterport technology on a more regular basis,” she says.
Matterport also has a team of service professional scanners, ‘the Uber on demand’ of scanning. If you want a scan, or don’t want to make the camera investment, it’s possible to have someone go and scan with the Matterport Pro3.
Matterport covers 77 countries or more. That means, you could be based in New York, and get something scanned in Cape Town by tomorrow.
Conclusion
Matterport has taken on the mantle of the democratisation of reality capture. It has a usable device at a price point that is certainly in the right ballpark for mass adoption of LiDAR and photogrammetry.
Matterport seems very committed to going ‘Pro’, offering capabilities to AEC design firms and targeting the long tail of digital twin adoption. However, this will require ongoing evolution of the scanner suite, with more connectors to pro design tools and defined workflows.