How a team of engineers realised the artistic vision for a bold new stage design featuring a fully articulated 12 metre head of a clown for Verdi’s world famous opera
The Bregenz Festival in Austria is internationally renowned for its spectacular productions held on a large floating stage on Lake Constance. The current stage design for Verdi’s opera “Rigoletto”, however, surpasses all previous ones in a special way.
The structure on the lake stage weighs a full 140 tonnes and is a marvellous combination of art and engineering.
The twelve-metre-high clown head and equally long hands are impressive in their own right. But it’s the sophisticated stage technology that sets the structure in motion and breathes life into every performance that takes the design to a whole new level.
The project is the result of meticulous planning carried out by engineering firm Lener & Schmid Ingenieure ZT GmbH. It took more than two years to bring the Rigoletto stage design to life, from initial idea to the final delivery.
Gerhard Lener, the engineer that heads up the project, is no stranger to stage design. Rigoletto is the tenth Bregenz Festival project he has been involved with in 20 years.
This, however, is his most elaborate to date: “The more movement there is in a construction like this, the more challenging it is for us,” he explains. “And this one was meant to have maximum movement. It is more of a machine than a static structure.”
A machine as a stage
Rigoletto’s head can move in a multitude of different ways. A swivel drive directs the head, which weighs tons, up, down, left or right during the performance.
A total of eight drives are used to show facial expressions to match the action on stage. Eyelids open and close, eyeballs move up and down, and the mouth can also open or close as desired. The hollow head can accommodate up to ten performers who use it as part of the stage.
We try to ‘‘ harmonise the artistic appearance, the required functionality, legal standards and technical feasibility, while implementing as much of the specifications as possible
To the left and right of the head are two hands, whose six-metre-long fingers can also be individually controlled by means of a hydraulic swivel drive, so that their movement resembles that of a human.
In his left hand, Rigoletto holds a real balloon with a diameter of 14 metres, which is filled with more than 1,300 cubic metres of helium and – when weather and wind conditions allow – rises into the night sky during the performance.
Realising the vision
The idea for the imposing stage set came from the stage designers, who turned to Lener & Schmid to help deliver on their vision.
Away from the Bregenz Festival, the engineers work for public-sector clients or specialist companies with a deep technical understanding.
Working with artists is therefore always something special, which is the great attraction, but also requires a close exchange and a lot of mutual understanding. “We try to harmonise the artistic appearance, the required functionality, legal standards and technical feasibility, while implementing as much of the specifications as possible,” says Lener.
To help make the project a reality, the engineers relied on advanced structural software SCIA Engineer. The first step was to model the geometric representation and then analyse the movement of the rotating head.
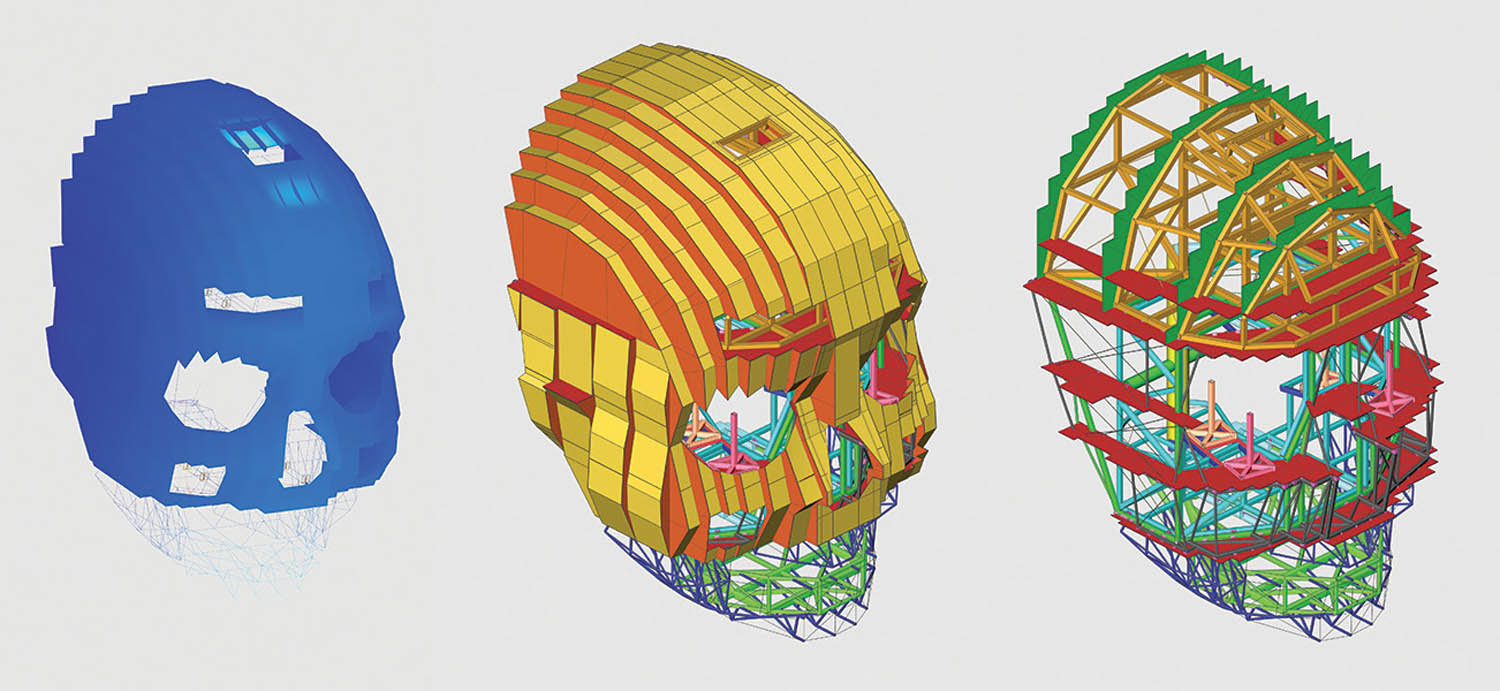
One of the major challenges the experts had to face was the distribution of the loads. This is because the lake stage is built on a fixed concrete core with a maximum load of 1,000 kg per square metre. “We had to think carefully about how to distribute that. Because with Rigoletto that became extremely tight,” explains Lener.
It quickly became clear that it wouldn’t work without lightweight and composite construction. “When you look at this stage set, you realise that it consists of many construction parts and materials. It starts with steel, goes through wood to fibreglass,” he says.
To save weight, the engineers relied on both a wood-steel and a fibreglass-steel composite construction. The formwork thus also became a load-bearing component. “This is where we benefited greatly from SCIA Engineer, as this software covers all these materials,” he explains.
Safety first
The project is somewhat unique in that it is not only a structure, but also the workplace of several actors and singers who perform in front of, on top of, and even inside the head. Therefore, it was important to consider strict safety requirements to protect the actors.
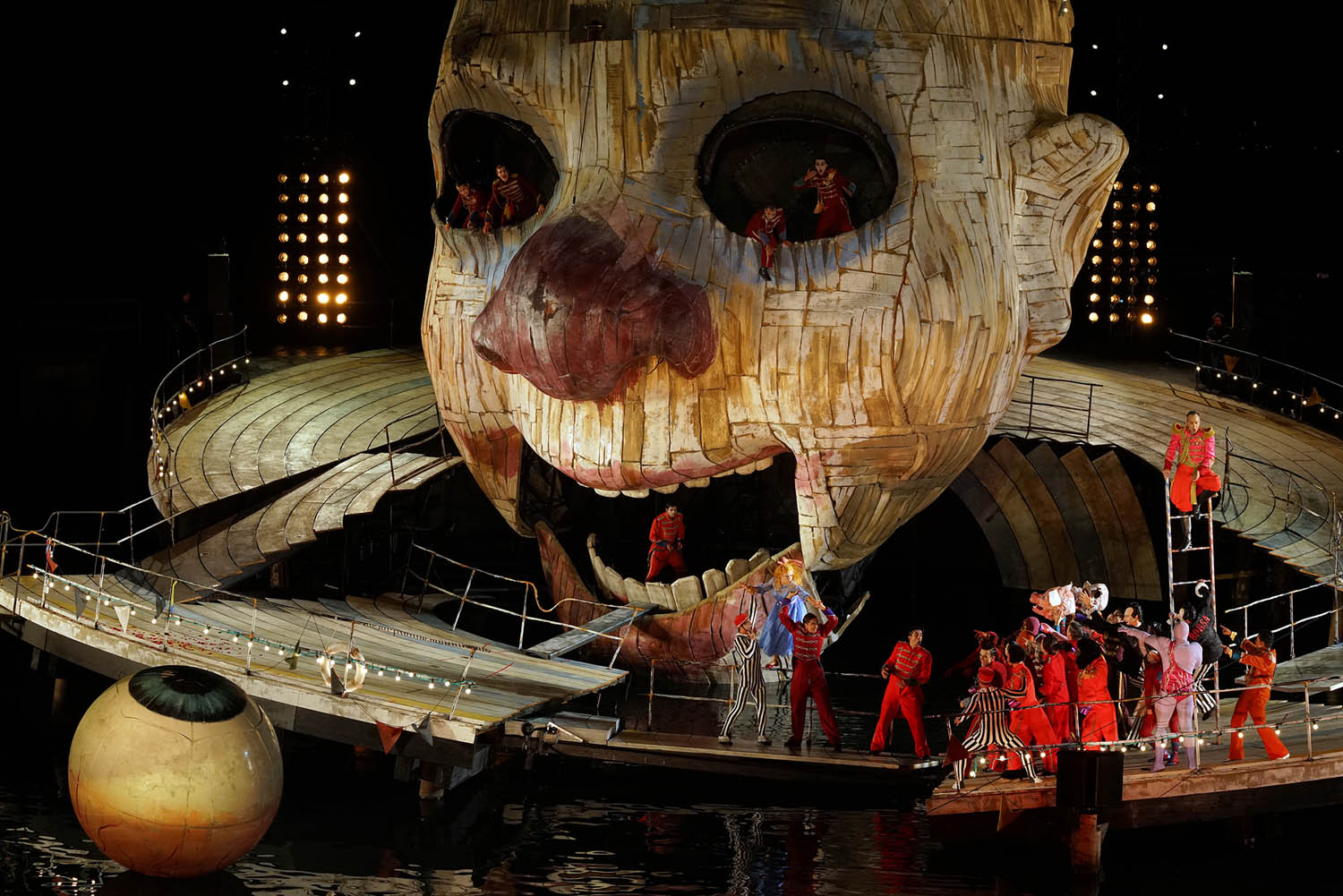
In some cases, stunts are also performed in which people fall off the stage. All of this has to be taken into account in the design, including the forces that such movements exert on the structure.
For the engineers, this meant a verifiable structural analysis needed to be submitted. The dimensioning is done according to the Eurocodes – i.e. corresponding European standards and dimensioning rules.
For this, Lehner & Schmid had to provide precise models and verifications. “Keeping to the form of all the verifications was enormously time-consuming,” explains Lener. “Without software support, it would not have been possible to carry out the corresponding variants.”
“This is the huge advantage of the SCIA Engineer software. It contains all EN standards and verifications. During the calculation run with SCIA Engineer, the solution of the system of equations, the determination of the deformations and internal forces was achieved within a few minutes,” he adds.
This enabled Lener & Schmid to carry out the structural design and calculation quickly, and also to deliver the necessary verifications in a timely manner.
A masterly performance
Thanks to the precise planning in advance, hardly any reworking was required, and the complex structure was accepted and fully operational on time for the start of the Bregenz Festival 2019.
During this year’s festival season, the Rigoletto stage set was in action until 22 August 2021. Now it is being dismantled and the materials recycled. Because Lener & Schmid are already planning the next stage design – Puccini’s “Madame Butterfly” in summer 2022.