The London Mayor’s office has sponsored the development of a free application for developers to help conform to London’s spatial planning rules and assist in deciding which rapid off-site construction technology best fits their design.
For anyone living in the UK, the shortage of housing, the exceedingly high prices and the seeming inability of the Government to solve these issues have become constants in our daily lives. Their effects are actually shaping our society, should that be by pricing key workers out of cities where they are needed, or by entirely pricing out the next generation.
While there are many possible solutions, being able to build more, faster is something that could be solved by pre-construction and modularisation. However, many developers are not fully up on these emerging building technologies and may not consider them at the conception phase.
With a requirement for over 50,000 new homes a year in London alone, the Mayor’s office is acting to promote and assist developers in taking a modular and offsite approach to building. It is doing all it can to drive acceptance of the process which could double the speed of delivery of housing projects.
“We need to build far more housing in London – and particularly more council, social rented, and other genuinely affordable homes,” says James Murray, Deputy Mayor for Housing and Residential Development. “Even if we had all the investment and powers we need, traditional construction techniques will only take us so far.”
In 2017, the London Assembly Planning Committee produced a report entitled ‘Designed, sealed, delivered’ and it was a call for the creation of a standard design code for ‘precision-manufactured homes’ to combat London’s housing crisis. In response, the Greater London Authority and Transport for London funded the development of an application called Prism, which was co-funded by Greystar, Legal & General, and the housing association L&Q.
Prism was delivered by engineering and architectural firm, Bryden Wood, together with Cast Consultancy. It’s a free web-based application to assist developers better understand how housing projects could benefit from modular and pre-construction technologies using existing volumetric and panellised products. Buildings can be rapidly modelled in context, within a configurable-criteria of apartments and spaces, with checks for conformance, and then an intuitive ‘traffic light’ system indicating which modern construction methodology would be best suited to the development.
Prism is the first of its kind for modular residential design, globally, and shows that the UK is serious about adopting the new building methodology. Importantly, the buy in is not just at the developer level; it includes local and national Government as well.
Modular and pre-construction
What’s in a name? There are so many terms for offsite construction, it’s becoming hard to track. Normally each defines a specific type of process, or one associated with a specific type of material, which defines the process. The Mayor has decided on Precision Manufacture Homes, which I guess does away with the how and the material choice. It also possibly nixes the issue of negative public association with prefabricated which ranges from a ‘portaloo’ to a wartime corrugated iron structure. Given the utterly shoddy building quality of some of the new brick and block housing being built in the UK, the idea that a home is precision made may also offer some level of additional assurance.
The UK is undoubtedly embarking on a dramatic investment in offsite construction, with fabrication plants popping up all over the country and skills being imported from all over the globe through partnerships. The next step is to broaden this out to include the developer community and to increase their level of knowledge as to technically what is possible, through to delivery benefits and potential cost savings. The Prism app gives developers some basic tools to start early site evaluation with a lot of built-in knowledge as to the viability of each offsite construction methodology, given the building definition and requirement.
Prism app
Prism (prism-app.io) is based on Unity, the free, open source application, and runs in a browser, so it’s available on tablets or phones. It has a very simple interface, with just a gridded plan. At the top right of the window, there are navigation tools, while at the bottom left of the screen are the creation and analytical tools.
By hitting the create button, the first choice is to choose a location for the project, either by postcode or GPS. It’s possible to load maps, delete existing buildings and draw a site boundary. If you bring in the default map of central London, it automatically loads the demonstration area which is already populated with block models of buildings. You can also upload your own site model or background image. You then chose the site area and clear it by placing down a boundary.
The next step is to define the building and orientation, building type – linear or tower – the number of floors, the make-up of the units and to define the apartment spaces. As standard it supports anything from studios up to three-bedroom apartments, with some configuration options and dimension driven design.
The apartment areas conform to London standards and the designer can define systemisation (HRS modules, CLT modules, Steel Panels, Timber Panels, CLT Panels, Concrete Panels), corridor wall, external wall, party wall, max panel length, max load span, and whether or not there is a balcony. The model generates automatically and can be adjusted and ‘auto solved’ using combinations of unit types in an iterative process to meet the developer requirements.
The analytics panel offers a host of useful information: apartment areas for the whole project, distribution by type and the net to gross. There’s feedback on the module or panel length and width for volumetric and panel approaches, access to map layers and project alerts.
The most useful tool is the Systemisation Analysis tab which offers a traffic light system which indicates what offsite construction methodologies and material best fit the defined project’s criteria, either by volumetric or by panellisation. It checks against building height, floor-to-floor height, party wall, external wall, element size and span. Just a quick glace at this will give a developer guidance as to what process and material choice would meet the needs of the project as currently defined.
Prism could be used in an interactive way where projects could be designed in conjunction with an architect to refine the result to meet key fabrication objectives.
While Prism isn’t a ‘BIM’ tool it has just enough capability for a developer to rapidly evaluate some basic designs with the core business metrics, which can be handed on to a design team for further development. At the moment models can be exported as OBJ. It doesn’t support RVT or IFC natively; this could be improved, perhaps in a future release.
Cast and Bryden Wood
At the launch event AEC Magazine caught up with the key drivers of this initiative Mark Farmer, CEO of Cast Consultancy and Jami Cresser-Brown, architecture director of Bryden Wood.
Farmer explained how the UK is leading the charge to change the building process, “Whenever you’re changing a market, you’re innovating, and there always is this sort of sense of risk taking, and risk is not the norm in the building industry.
“We’re not quite sure of things that aren’t tried and tested but that’s the very nature of innovation. Ultimately, where this all starts is with the really positive approach that the UK seems to have taken. Even when looked at on an international basis, I’ve travelled a lot over last two years and think the UK is right up there. The level of activity on offsite construction in this country, I have not seen anywhere else in the world.”
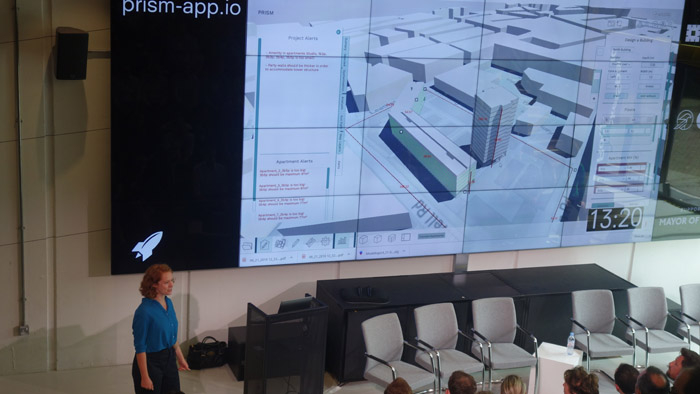
Cresser-Brown explained why the application is free and how it should be use to drive the development process, “With the app what we are really trying to do is share our knowledge that we have accrued from speaking to the manufacturing community and incorporating your kind of spatial requirements as defined by the Mayor of London. Then sharing that widely with the entire architectural community and beyond. It’s not just about architects but it’s for others as well and not hiding that behind a paywall.
“What we fundamentally don’t want is for someone to produce a design in Prism and then for there to be a load of redundancy, because the design has to be recreated in a proprietary application like Revit or whatever you normally use. It’s about the transfer of that design in a very straightforward and simple way through APIs to drive the process. It gives developers
and designers more time to focus on the quality of the environment.”
Timber barriers
In our research into modular construction and especially in the use of timber frame, it seems other key elements of the building market, namely mortgage brokers and insurance firms have yet to catch up on new construction processes. On looking up timber frame houses, we found them in the same paragraph as Japanese Knotweed, subsidence and listed buildings. Farmer said,
“On the valuation, mortgageability, financing and insurance side of the debate, I am currently leading a working group that is specifically tasked to look specifically at that. We have been in session for 18 months now and we have all the major warranty providers, because new build warranties are the trigger for the mortgage, which is also linked to building insurance.
“If the warranty market does not embrace the precision manufactured homes, then that becomes a blocker for mortgageability and insurance which then constrains the whole market. So, we can do all this great thinking and design work and manufacturing but if the end client can’t get a mortgage, it all hits the buffers. We are hoping to evolve this with BOPAS (Buildoffsite Property Assurance Scheme) to build confidence for insurers and mortgage providers.
“Putting the warranties to one side, if the insurance market is concerned about materiality and obviously, we’ve had a timber fire in the last two or three weeks in Barking concerning a balcony, so there is a spotlight on timber construction. Somehow as an industry we have to square the circle on how we’re going to embrace timber as a material that is sustainable. It actually goes to the heart of the Government’s climate change agenda. They’ve said by 2050 they want to be building with net zero carbon – and you’re not going to do that if we’re still building with cement. Somehow, we have got to change it.
“This is a very complex subject. I am looking at finance; Jami Cresser-Brown and the team at Bryden Wood are looking at design and technology opportunities to open up the front end, and lawyers need to look at the contract issue with collaborative approaches to procurement, rather than setting everyone up to have an argument from day one. All these things need adjusting to make this work.”
Conclusion According to Farmer there’s an ongoing discussion about how the team keep this initiative alive, how it’s managed, maintained and developed. This is just the beginning and because it’s open source, there is a huge opportunity to go just beyond London and to have a more multi stakeholder approach to its development.
As L&G are involved, which has a building factory almost ready to go, I could imagine a version of Prism which may focus specifically on units in the L&G catalogue, perhaps linked to the factory showing build/delivery times and costs. This could further accelerate development to delivery times.
The momentum towards adopting offsite manufacturing methodology is building up considerable speed in the UK. Now this isn’t just coming from the house builders but also developers, local Government and the national Government. The UK took assertive action to mandate BIM use on Government projects; now it’s evaluating and having a dialogue with the industry on speeding up building and looking at material usage to meet its carbon targets. However, it’s clearly not just an issue of having the factories and methodology to manufacture the buildings, with lenders, insurers and warranty holders needing to be onboarded, together with long needed changes to industry contracts.
The other component is planning, which few seem to talk about. It’s all well and good being able to rapidly develop, build and sell residential housing but if the planning system doesn’t catch up with the industry’s digitisation it will be the log jam which holds back the entire effort.
If you enjoyed this article, subscribe to our email newsletter or print / PDF magazine for FREE