An explosion is underway in the use of visual data collected and used in near-real-time for construction, as Randall S. Newton reports.
Aris Market Square is a midrise tower currently under construction in Houston, Texas, an upscale residential/ commercial building adjacent to a historic downtown park.
In a high-growth city like Houston, this could be just one more tower going up, but this particular project is breaking ground for its leading-edge use of visualisation technology for construction.
General contractor Urban Oaks Builders and subcontractor Austin Commercial are working with technology firms 3DR and Autodesk to automate construction management. Using 3DR’s SiteScan and a Sony R10C camera, the contractors used an Unmanned Aerial Vehicle (UAV) – a drone – to take hundreds of photos of the building’s concrete structure, roof and exterior as it went up.
The photos were then processed using SiteScan and Autodesk ReCap to create a 3D model to prepare visualisations such as textures and wireframe views.
As a result, instead of having construction crews climb up and down scaffolding to conduct quality control checks, project managers can take updated drone photogrammetric scans and apply them to the model.
“This technology allows us to collect data in an urban environment in a way we haven’t been able to do before,” says Joe Jones, a senior project manager with Austin Commercial. “This is a gamechanger for us.”
Scan-to-BIM explosion
Aris Market Square is just one example of an explosion in the use of reality data captured and used in near-real-time for construction. It may be far removed from what most industry professionals think of as BIM, but for construction companies, building imagery scanning offers a fast return on investment and reaps dividends in saved time, increased efficiency and increased job-site safety.
Real-time scan for construction management is just one use case in the new area of scan-to-BIM technology. Terrestrial (tripod-mounted) laser scanners have been around for years, but their high prices and complicated operation have made them useful only on very large projects with plenty of room for teams to collect data from many angles.
Today’s rapid adoption of scanning is largely due to the new affordability of UAVs, as well as software advances that make photographic imagery useful as a source of site data alongside – or sometimes replacing – laser point cloud scan data.
Scan data in BIM is used in three ways: design, construction, and asset management. The reason scan-to-BIM is currently booming in construction is twofold, says Tom Greaves, chief marketing officer of DotProduct and a 13-year veteran of the AEC scan-data business in a variety of roles.
“Construction needs a good answer now,” says Greaves. “A good answer today is better than a great answer a week from now.”
The new era of drone scanning with fast data turnover answers construction ’s need for good data quickly. “If you can capture as-found and use it against the design model quickly, you have something.
”Design products like Revit, MicroStation, ArchiCAD and other architectural BIM tools are labour-intensive, notes Greaves – and labour-intensive also means time-intensive. Construction managers are familiar with the idea of throwing labour at a job to compress time, but design doesn’t work that way.“
“Our phone- and tablet-based solutions let you capture the geometry of a newly installed pump room say, in a few minutes,” says Greaves. “A few minutes later, the point cloud can be compared to the BIM either on the jobsite or in the stakeholders’ offices. The small files (<40 MB) from DotProduct scanners let project managers make swift coordination decisions without waiting for specialist survey crews or CAD modellers.”
Reality modelling
Bentley Systems has been assembling a set of scan-to-BIM tools in recent years, mostly by acquisition. Benoit Fredericque is a senior product line manager in charge of scan technology, which the company refers to collectively as ‘reality modelling’.
“We look at scan-to-BIM from the workflow point of view,” says Fredericque. First, acquire the data with scanning or photography. Second, convert it to data, and generate what Bentley calls a ‘reality mesh’, an overlay for use with both existing models and other forms of visual information. Third, move to data ‘consumption’ where the data is repurposed, translated and edited for specific tasks along the designbuild- operate continuum. Fourth, use the data for business decisions.
Along the way, the ‘reality’ level of the data matches the use case. Sometimes, all that is needed is a visualisation of how much land will be impacted by construction. Sometimes, the scan data has to become the foundation for creating design data, because it is the most costeffective and fastest way from idea to design model.
“We look at scan-to-BIM as much bigger than creating actionable geometry,” says Bentley’s David Huie, a product marketing manager and 20-year Bentley veteran. “The paradigm of scan data to geometry is not [always] the ideal use.”
For understanding brownfield environments, for communicating design intent or construction progress, or to represent 3D for operations, scan data is many times preferable to repurposing BIM data created by designers and engineers.
“Add CAD data to go to the highest degree of intelligence,” says Huie. Sometimes, this means just use scan data as a representation, and sometimes, it means extracting geometry features from scan data for use in design.
Huie says the widespread adoption of scan data is “driving us to make extra investment.” Bentley recently released an update to its ContextCapture software, which allows both laser point clouds and photos to be integrated into one data model. Bentley’s Fredericque expands on what the near future holds:
“There is a coming fusion of sensor types and sizes, and rapid adoption; it is a transformative technology. The short time it will take to create 3D models will change how people manage and process infrastructure projects.”
Straight to the geometry
Much of the use of scan data for building information focuses on the ability to reference or provide context, but there is also a big market for turning point clouds or photos into geometry for direct use inside a BIM authoring tool. Arithmetica started as a small software house to serve London’s film industry, but has found itself in the middle of BIM.
Arithmetica’s PointFuse can take point cloud data or photogrammetry from drones and generate 3D vector geometry. The software can identify natural break lines across the object’s geometry, making it possible to select, investigate and extract features like doors, walls, windows and other building elements. It allows building specialists in areas such as mechanical, electrical and plumbing to work with captured data without conversion to a 3D geometry format.
In its current form, PointFuse does not automatically classify geometry, but its developers see that as the logical evolution of the product.
“BIM isn’t really just about 3D models,” notes Will Tompkinson, a US-based consultant who helps AEC clients implement PointFuse. “BIM is a workflow for documenting what is to be on site.”
“We streamline the point cloud conversion experience,” adds Mark Senior, business development manager at Arithmetica. “People buy scanners that create great point clouds – but they don’t want point clouds, they want vectors. They want data in a format they already use.”
From extraction to verification
For several years, ClearEdge3D has published the EdgeWise portfolio of software, designed to automate the extraction of features from point cloud data. It started with intelligent identification of piping for process and power plants, then expanded the software’s capabilities to recognise other building elements. It now has a suite of products that extract a variety of features that can be added to a BIM model much faster than by manual methods.
Construction services firm 3DIS recently created a complete as-built Revit model of a newly constructed building at Kettering University in Flint, Michigan. Typically, such a job would require one day of laser scanning, a half-day registering the scans, five days of modelling in AutoCAD to draw features from the scan data, and two days of tracing in Revit.
Using EdgeWise Building, 3DIS eliminated the modelling step in AutoCAD and reduced how long it took to get to Revit data by 55%.
“What used to take days to process can now be completed in hours,” says Nick Bobbitt of 3DIS.
The newest product in the EdgeWise line is Verity, software for construction verification, which is sold in the UK by Excitech. The software verifies accuracy of as-built construction against a design model. ClearEdge3D claims commercial construction routinely spends 5% of a project’s actual cost on fixing “poorly constructed and out-of-tolerance work.” Verity is designed to shortcut the process of finding out-of-spec work early, by comparing current as-built scan data to the original design model, flagging problems requiring remediation or other attention.
“Construction verification could be seen as one of the missing links in the BIM chain,” says Michael Johnson at Plowman Craven, a leading UK survey firm that has been testing Verity. “There is an evolving need for a software tool that can automate the process of verifying construction progress and accuracy.” Verity data can be viewed in Autodesk Navisworks or Revit.
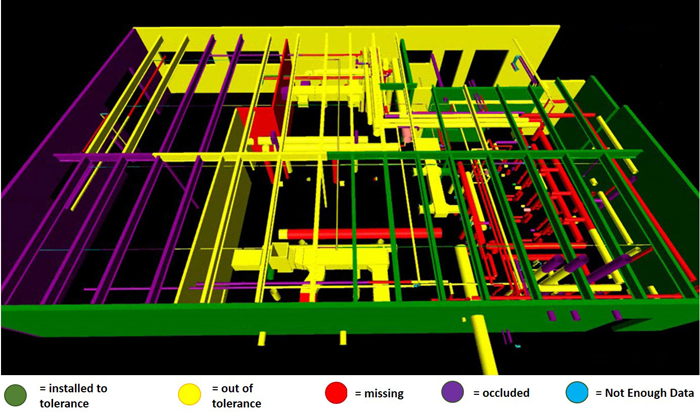
Irregular geometry in Revit
Revit has a reputation for being difficult to work with for irregular objects and unusual design flourishes. The latest edition of Scan to BIM software from ImaginIT Technologies offers a new way to deal with unusual elements. Items like built-in art objects (think gargoyles) or intricate wainscoting can be scanned at high resolution. The resulting data can be extracted and converted to a Revit library object for placement in a model.
Scan to BIM is an add-on to Autodesk Revit; it works inside the product, creating a natural familiarity to the process of bringing scan data into Revit as model elements. In addition to modelling intricate objects, the latest version of Scan to BIM automates the recognition and extraction of wall batches from a point cloud.
Midwestern Consulting is a US-based civil engineering consulting firm special-sing in large building construction projects. As its customers migrated from AutoCAD to Revit, they noticed a simultaneous increase in the number of times laser cloud scan data was being modelled first in AutoCAD, then again in Revit.
Midwest started using ImaginIT’s Scan to BIM to help its clients reduce the time to turn scan data into intelligent model data. On one preliminary consulting project for a large government building, Midwestern documented a 40% reduction in cost to turn as-built data into an intelligent building model. Most of the savings lay in the reduction of designer time by importing intelligent Revit assets from scan data.
Scan-to-BIM as a service
Not every AEC firm wants to become an expert in gathering site data for BIM. Fortunately, there is a strong service community staying current on the technology. Severn Partnership is one of many UK firms with years of survey experience that has moved into using laser scanners and drones for gathering data and delivering BIM-ready data for clients.
Working with the Royal Institute of Chartered Surveyors (RICS), Severn recently completed a scan of RICS’ headquarters. The Institute wanted first-hand experience in procurement, use and management of BIM data starting with the asbuilt. The historic RICS headquarters are in London’s Parliament Square, opposite Big Ben and the Houses of Parliament, comprising several different buildings that have evolved over centuries, making for a challenging assignment.
A survey team was on-site for two weeks. Some rooms were simple; others, including the Library, were filled with bespoke structural features. The Severn team turned the scan data into Revit model data with a high level of detail (LOD) factor, befitting the complexity and non-uniform nature of the RICS headquarters.
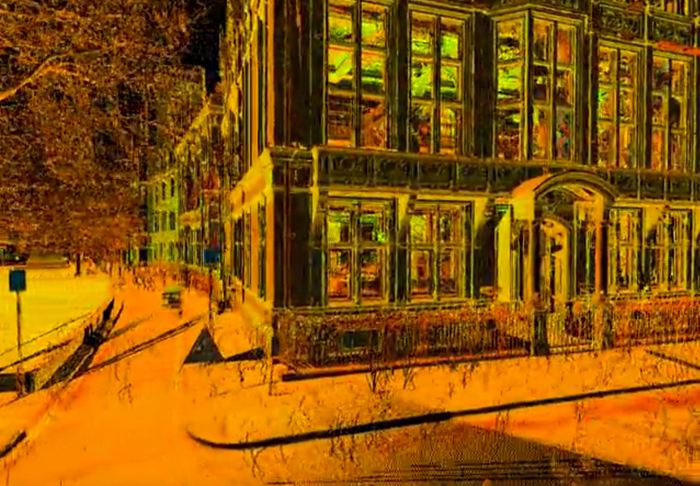
Point clouds to the cloud
Point cloud files are massive; it is common for them to be measured in terabytes. Processing such behemoths can tie up the average workstation for days. A US-based start-up Skur intends to bypass desktop processing of point cloud data for BIM by taking it to the cloud.
Skur is using a proprietary process and the vast parallel processing capabilities of the cloud as a way to streamline the use of scan data for rapid visualisation of large-scale environments. The goal is to make data immediately available for design review and project progress reports. Skur claims its software “can tell you not only that an object is off, but by how much and in what direction.”
The process has three steps. First, a client uploads a 3D .dwg files as a basis for comparing the design and the scan. Then the Lidar data is processed to remove unnecessary ‘debris’ that does not impact a progress study. Finally, the two are compared and analysed by the software, which outputs a variances report.
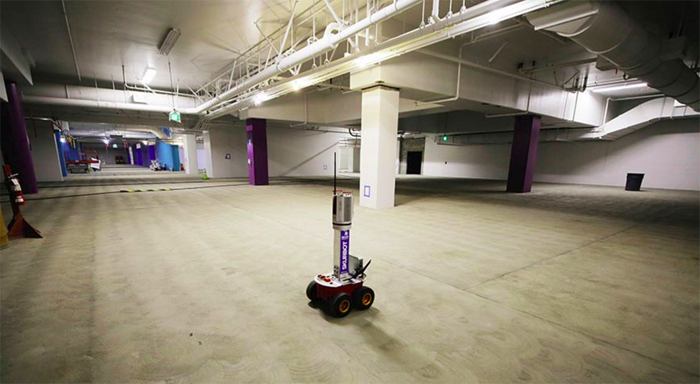
In conclusion, there are many ways that AEC firms can start to tap into scan-to- BIM, but the benefits remain largely the same regardless of which one is taken: fast ROI, saved time, increased efficiency and better health and safety conditions for those working on-site.
Randall S. Newton is Principal Analyst at Consilia Vektor. He has been writing about AEC technology since 1987.
If you enjoyed this article, subscribe to AEC Magazine for FREE