By using BIM, it’s much easier to get people thinking about the maintainability of buildings, write Mike Ford, digital / BIM manager at the University of the West of England, and Dr Nick Bell, risk consultant
What does BIM have to do with building maintenance or safety? Often the answer is, not enough! As we are making the migration to the digital BIM workflow, we’re building a mountain of valuable graphics and data; the challenge is, how to squeeze all the value from this new resource? Could it be that BIM might be the solution to some of the age-old problems, like engaging with building users, operators and maintainers?
Constructing a building is no easy feat, there are lots of competing interests to consider and lots of processes to manage. It’s little wonder that sometimes we don’t have enough time to think about maintenance. The case we’d like to set out here, is that using BIM makes it much easier to get people thinking about maintainability.
We’d like to run through a very simple example of a difficult to maintain element and make an argument for why a model-based construction design and management (CDM) walkthrough may have given the opportunity to design out this issue.
Annoyingly, a light in the atrium, as shown in figure 1 above, has failed. Is that a big deal? It’s just one light at the University of the West of England (UWE) Bristol where we have 300,000m² of internal space and do around 2,000 lamping replacements a year.
As it happens, this particular fitting does cause a fair amount of upheaval. The only way to access it is using a specialist spider mobile elevated working platform (MEWP) – see figures 2 and 3 below..
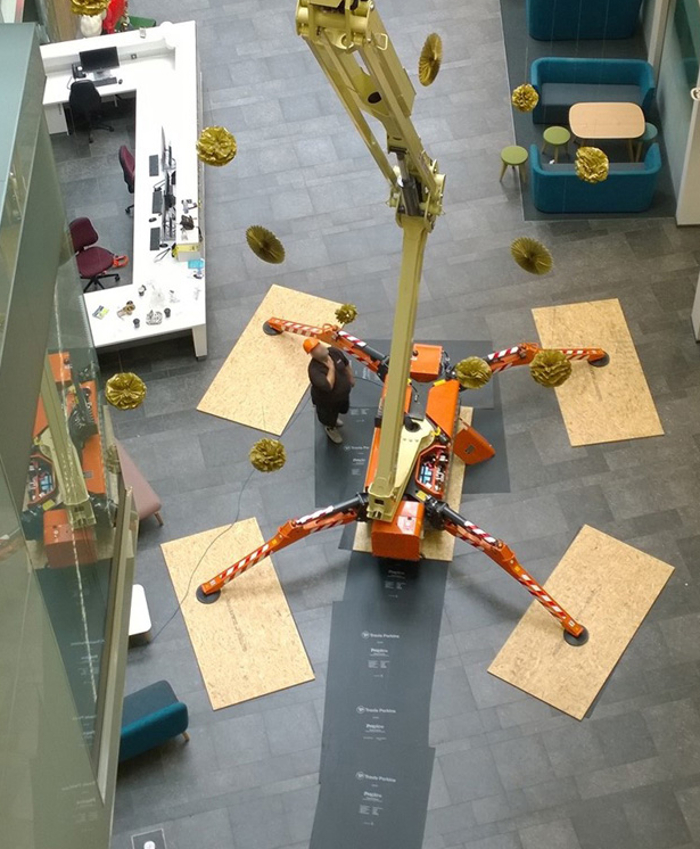
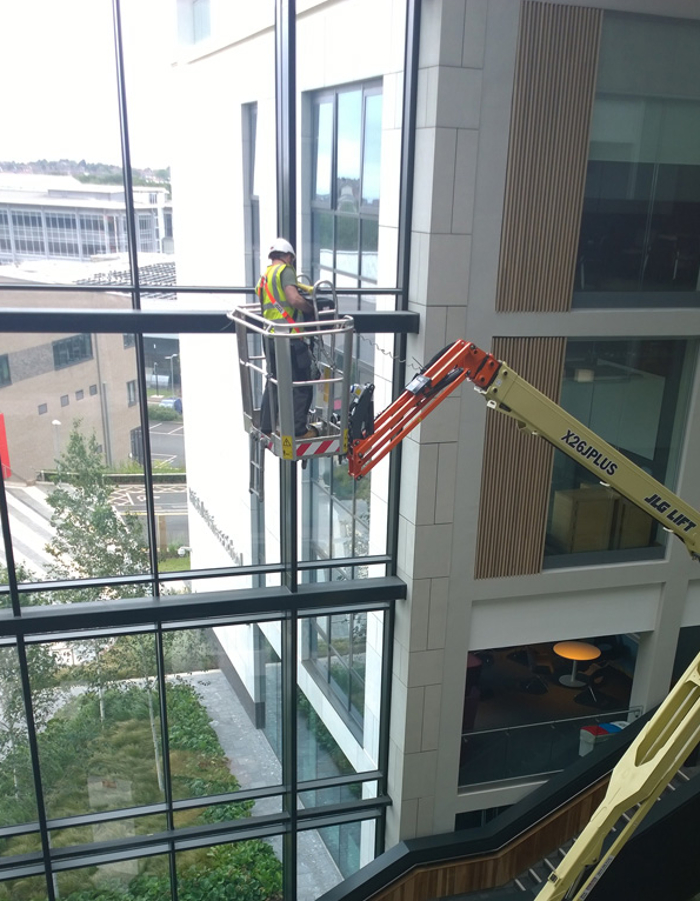
To spread the load of the MEWP and protect the tiles, wooden boards need to placed under its feet but, even then, some have still cracked.
Of course, this comes at a cost. Replacing a standard light fitting (figure 4 below) costs £15 (0.6 hours of labour at £25/hour), whereas replacing the light in the atrium space costs (figure 5 below) £750 (£450 to hire the MEWP and two operators at £150 each). It’s clear that there’s a strong case for using lower level lighting to light the atrium space.
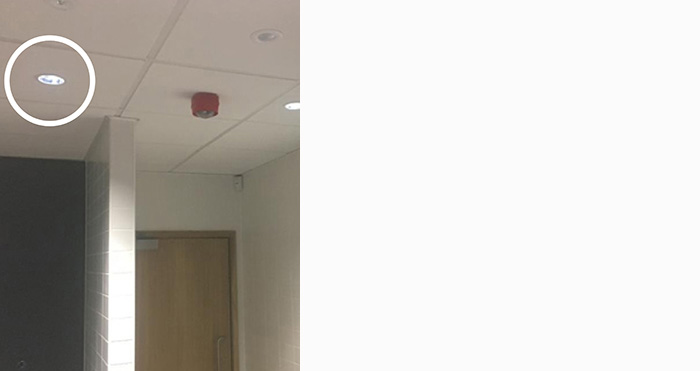
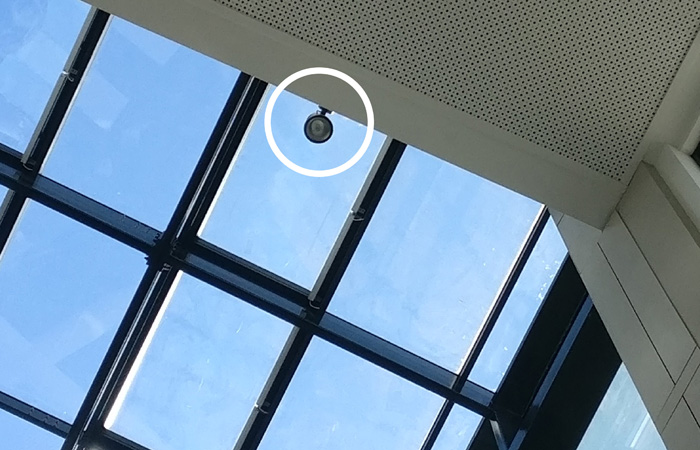
That isn’t to say that high level lighting is always the wrong solution; our argument is that best practice should always consider issues like working at height and design out risks wherever possible.
The conversation needs to be had with the person responsible for maintaining the building. If the client accepts that high level working is acceptable, then there needs to be a conversation on how to make the building easily accessible to MEWPs and how to ensure the floor and its finish is suitably robust to take the load. The problem is, how easy is it to pick up this as being an issue? If you’ve just looked through a pack of hundreds of drawings, such as the one in figure 6 below, does this stand out?
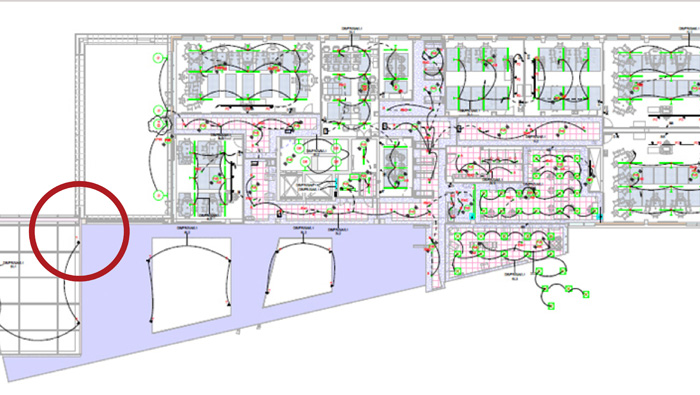
We’re all humans used to seeing the world in a certain way and in figure 7, below, you can see what a difference a third dimension makes. Additionally, with a 3D model, when we put our ‘building maintenance’ hats on, even inexperienced personnel start to ask very sensible questions about building maintainability.
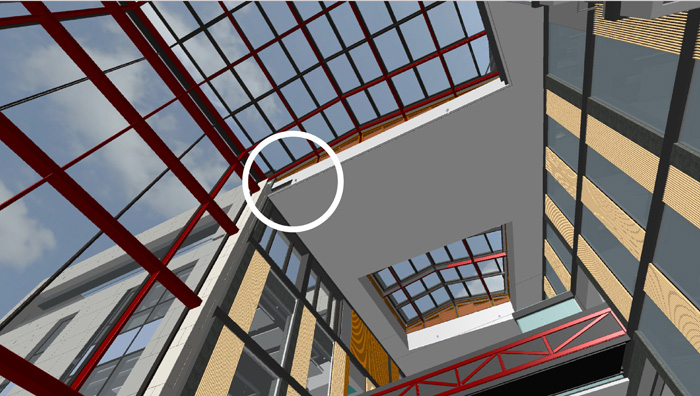
Collaborative thinking
A virtual CDM walkthrough of a building should take place during RIBA stage 4 (Technical Design). The sooner you find problems with the building design that can be designed out, the cheaper it will be to change the building design. However, the earlier you hold a model walk-through, the less developed the model is. You certainly want to carry out this process before construction begins, perhaps BSRIA BG6 2018 stage 4ii (coordinated generic design) is the best time, as items are correctly located but not yet fully specified.
Who should attend? You could run a workshop with just the maintenance team, but I think it’s better to have representatives from the design team, the project manager and the main contractor present (if appointed). The design team will be able to offer immediate insight into the design intent, perhaps there has already been a lot of thought on a certain issue and the design has already been optimised for maintainability.
The main contractor can use this as an opportunity to comment on buildability and may be able to draw on their experience to offer suggestions for how to solve maintainability issues.
The maintenance team will know how to maintain a building and which issues have caused them headaches in the past. It is the project manager’s responsibility to find the best possible middle ground between beautiful high-quality spaces and spaces that are practical, cheap, safe and easy to maintain.
This has, of course, just been one example of an issue and method for resolution/consideration. We chose this example mainly because it was very easy to illustrate. Other typical issues that have been discussed are: removing roof plant at end of life, safe cleaning of glass balustrades,safe roof access, high level window cleaning, plant room configurations, etc.
All things considered, this process means that the client ends up with a better building, design changes can be made, there is less criticism at handover and the maintenance team are already aware of difficult to maintain areas.
Managing risk
If you have come across PAS1192-6 “Specification for collaborative sharing and use of structured Health and Safety information using BIM” you may have experienced the concept for highlighting specific risks in the model using three-dimensional warning symbols – see figure 8 below.
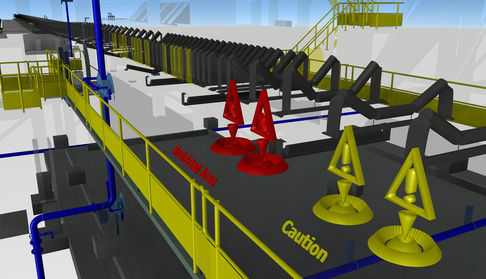
This is a very important concept within BIM. In the past we’ve communicated risk using hazard symbols on 2D plans and risk assessments. It used to be the case that risk assessments were too often being ignored, but at least everyone had to look at the drawings in order to construct the building.
On our building sites at the University, we’ve now enabled our supply chain to use 3D models on site. This is seen to be a very positive step forwards and it leads to far better BIM deliveries for us as a client, not to mention better communication and less errors on site. However, this also means that fewer people are looking at the 2D drawings. According to our site managers, 2D drawing use has dropped to around 20% where 3D models are available using tablets.
As an industry we need to rapidly change the way we record risks. BIM brings much more functionality to the table than we’ve been used to in the past. A 3D hazard symbol can also appear as a 2D symbol on the floor plans, as well as the sections, elevations and details.
This way, no matter where you’re looking for construction information, the risks are there.
The best thing about BIM in our biased view, is the information contained within the modelled elements. This is a real win, for managing risks. All of these 3D symbols can hold all of the relevant risk information, including mitigations and links to other documents, such as method statements.
Now the risk assessment table is generated from the 3D model, changing the model updates the risk assessment and updating the risk assessment updates the model. A single source of information for risks! Now using the 3D model on site is ensuring that everyone has access to relevant risk information; it’s graphical and relevant to the area they are working in. It is also far easier than it has ever been to get to the relevant information; they just need to tap on the hazard symbol on their tablet.
3D hazards are good for the client as well, especially if the contractor has applied 4D sequencing to the project risks. Using this method, risks should be able to pop in and out of existence at the right points in time. For example, the risk of being impaled on reinforcement bars doesn’t exist when the foundations are being dug or after the concrete has been poured. As the project progresses the risks change. Why is that good for the client? Well, any risks remaining at handover are residual risks that the client needs to manage. In an ideal world we would see the building, model and risks all handed over to the client and all maintained, updated and added to over the building’s life.
■ uwe.ac.uk/estates ■ nickbellrisk.com
If you enjoyed this article, subscribe to our email newsletter or print / PDF magazine for FREE