Amsterdam-based architectural firm 3D Blueprint is using Building Information Modelling to build better and at lower cost through effective co-operation.
The journey into ones self or your body is a dream that is shared by many people, and previously could only be experienced in the cinema. But that changed this Spring with the opening of the Corpus Museum in Oegstgeest, The Netherlands. Visitors can take an active journey through the human body from head to toe and find out Ùin situÝ how we work. This is made possible thanks to a 35 metre-high figure of wood and steel that flanks the narrow side of the glass museum structure. Designed by PBV Architecten, construction of the building was a particular challenge, which the commissioned designers from 3D Blueprint Architects & Engineers overcame with flying colours. Thanks to Building Information Modelling (BIM) and Allplan BIM from Nemetschek Allplan, the Amsterdam-based architects were able to complete the building on time and even remained below the planned budget.
Building Information Modelling relates to the consistent use of a virtual building model across all phases and disciplines of design, construction and management. Thus, BIM makes it possible to design construction projects that are less costly, contain fewer errors and are more efficient in meeting deadlines than is the case with conventional planning methods. This is exactly what Joep Esser and Wubbo Hazewinkel had in mind when they founded their company six years ago, and they have used BIM and Allplan BIM from the very start: ý3D BlueprintÝs goal is to build better and at lower cost through effective co-operation,¯ explains Joep Esser, managing director of the company.
The architects and engineers have developed their own working method for this, which they call the ýRegiplan method¯.
In Allplan BIMÝs virtual building model, all project-relevant information is entered centrally and made available to all those involved across the complete planning and construction phase. The Nemetschek Allplan solution offers exactly the right range of features, as employee Persijn Bongers explains: ýThe software is so sophisticated and powerful that even the most unusual components can be saved as intelligent objects ± an important prerequisite, if you want to work exclusively with BIM.¯
Cost cutting
The designers draw up the project requirements with the building client in advance in a Ùbuilding programÝ, which formulates a clearly defined and feasible goal. An initial (basic) three-dimensional building model is created for this in Allplan BIM, which allows reliable statements to be made on quantities and costs on the basis of the assigned material properties. Economic factors can be taken into consideration from the start and tracked over the entire project period: ýFor decision-making, the coupling of planning and calculation of costs enables us to identify the lower-cost option and therefore counteract incorrect developments at an early stage,¯ explains Mr Esser. ýAs a result, we are able to reduce the costs of a building project by 10±15 percent, for example, or to deliver a higher-quality building without increasing the construction costs.¯
The Amsterdam designers have already executed a number of projects successfully in this way, including most recently a new building for the Dutch Railroad Museum in Utrecht. The company now employs 50 people and has long been co-ordinating international projects. 3D Blueprint has made a name for itself as a specialist in integrated project planning, and was involved in this capacity in the Corpus Museum project. The company was, more or less, called in to save the day: because execution and design planning had been carried out completely removed from each other in 2D, a number of planning errors had already crept in after just a short time due to the complex shape of the building. As a result, costs had spiralled out of control. In order to bring things back on track in time, the building client, Heddes Bouw, handed over the entire project co-ordination, as well as tendering, project approval and project management to 3D Blueprint.
The planners soon got the project under control thanks to integrated project processing. All project information ± that is, all geometric and technical data of all the companies involved ± was merged and co-ordinated in a central Allplan BIM building model. In the first step, 3D Blueprint created the building and the human figure as a 3D model, and generated floor plans, views and sections from this.
A comparison of these plans with the steel construction data, which was imported to Allplan first in 2D and later as a 3D DWG file, brought a whole series of design errors to light. For example, there were points where the diagonal crosses of the reinforcing bonds ran exactly in front of doors, or the required heights for openings could not be adhered to because of the steel girders in front of them. By bringing together the various disciplines in one single data model, these problems could be identified long before the ground-breaking ceremony and corrected in good time.
This also applied for the building technology: once it had been ascertained that there was sufficient space for the required installations, all the installation plans were imported to Allplan BIM and checked on the basis of the execution plans. This was mostly done in 2D, but also in 3D at particularly complicated points, in order to identify potential collisions between steel structures, finishes and building installation immediately on the model and correct these where necessary. The building client and planners were therefore spared any unpleasant surprises on the construction site.
Made to Measure
In addition, information from the 3D model could be used to manufacture the corresponding steel elements with a precision fit and the elements could then be installed at the construction site without any additional work. The steel company took the construction data and added further production-relevant factors to the 3D model. This 3D model for the steel construction was then re-integrated in Allplan BIM via IFC and was then available as the planning basis for the wood structure, which together with the overlying metal elements, formed the external ÙskinÝ of the figure.
In the end, a virtual building model was created in which all the key factors ¾ relating to design, function, structure and production technology ¾ were incorporated and optimised. It is an excellent example of Building Information Modelling with Allplan BIM and was a determining factor in ensuring that the museum could be opened on schedule by Queen Beatrix of The Netherlands, who had long had the date noted in her calendar.
www.3dblueprint.net
www.nemetschek.co.uk
Interview: Joep Esser, managing director, 3D Blueprint
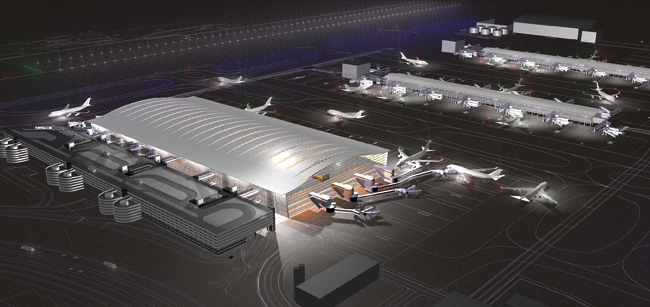
AEC: What is the ideal construction process?
JE: In our opinion, it is important that project requirements are specified with precision and that the construction team subsequently implements these requirements. This means that all parties involved work together without interruptions in the flow of information. To achieve this goal, we count on Building Information Modelling, and on the Regiplan method developed by us. During this process, the building model in Allplan BIM functions as a central hub for all project information and technologies.
AEC: What are the benefits you derive from using NemetschekÝs Allplan BIM?
JE: We consider Allplan BIM a very high-performance software that is quite mature as well. For example, this affects working with intelligent objects ¾ a requirement for BIM. In addition, the software provides a multitude of options for defining attributions for construction elements and offers extensive data exchange options ¾ both are crucially important for working with a central building model.
AEC: Does Building Information Modelling help you keep costs under control?
JE: Of course ¾ from the very start of a project. In our initial draft, we already connect individual components of the 3D model with costs. This lets us find the appropriate architectural style while staying within financial requirements and specifications. As the project advances, coupling the building model with pricing helps us make well-informed decisions and counteract undesirable economic developments.
AEC: Does Building Information Modelling require a specific work method?
JE: We are convinced that a structured process is a prerequisite for effective project management with BIM. We do this with the Regiplan method that we developed ourselves. BIM then makes it possible for the architects to stay on top of all aspects of the project and take on the role of general contractor ¾ very much like the original job description for architects.